Top 10 welded tubing in China introduce,list main products and website if have
Here are the top 10 welded tubing manufacturers in China, including their main products and websites:
1. Sino East Steel Enterprise Co., Ltd.
– Main Products: Welded steel pipes, galvanized steel pipes, stainless steel pipes, seamless steel pipes.
– Website: [sesteelpipe.com](http://www.sesteelpipe.com)
2. Landee Pipe
– Main Products: LSAW, SSAW, ERW welded steel pipes, seamless pipes, OCTG tubing.
– Website: [landeepipe.com](http://www.landeepipe.com)
3. Tianjin United Steel Pipe Co., Ltd. (TUSPIPE)
– Main Products: ERW pipes, carbon steel pipes, high-frequency welded pipes.
– Website: [tuspipe.com](http://www.tuspipe.com)
4. Dongshang Stainless
– Main Products: Stainless steel tubes and pipes, boiler tubes, heat exchanger tubes, mechanical tubing.
– Website: [dsstainlesssteel.com](http://www.dsstainlesssteel.com)
5. KAYSUNS
– Main Products: Stainless steel pipes, duplex stainless steel pipes, nickel alloy tubes, pipe fittings.
– Website: [kaysuns.com](http://www.kaysuns.com)
6. Hunan Great Steel Pipe Co., Ltd.
– Main Products: ERW steel pipes, LSAW steel pipes, spiral welded pipes, seamless steel pipes.
– Website: [hnssd.com](http://www.hnssd.com)
7. Yuantai Derun Pipe Manufacturing Group Co., Ltd.
– Main Products: ERW steel pipes, galvanized pipes, square and rectangular tubes.
– Website: [yuantaiderun.com](http://www.yuantaiderun.com)
8. Hebei Zhonghai Steel Pipe Manufacturing Corporation
– Main Products: ERW steel pipes, LSAW steel pipes, SSAW steel pipes, seamless steel pipes.
– Website: [zhonghaipipe.com](http://www.zhonghaipipe.com)
9. Zhejiang Kingland Pipeline and Technologies Co., Ltd.
– Main Products: ERW pipes, spiral welded pipes, oil and gas pipelines.
– Website: [kinglandpipe.com](http://www.kinglandpipe.com)
10. Cangzhou Steel Pipe Group (CSPG)
– Main Products: SSAW pipes, LSAW pipes, ERW pipes, seamless pipes.
– Website: [cangzhougroup.com](http://www.cangzhougroup.com)
These companies are prominent in the welded tubing market in China, providing a wide range of products used in various industries such as construction, oil and gas, and manufacturing.
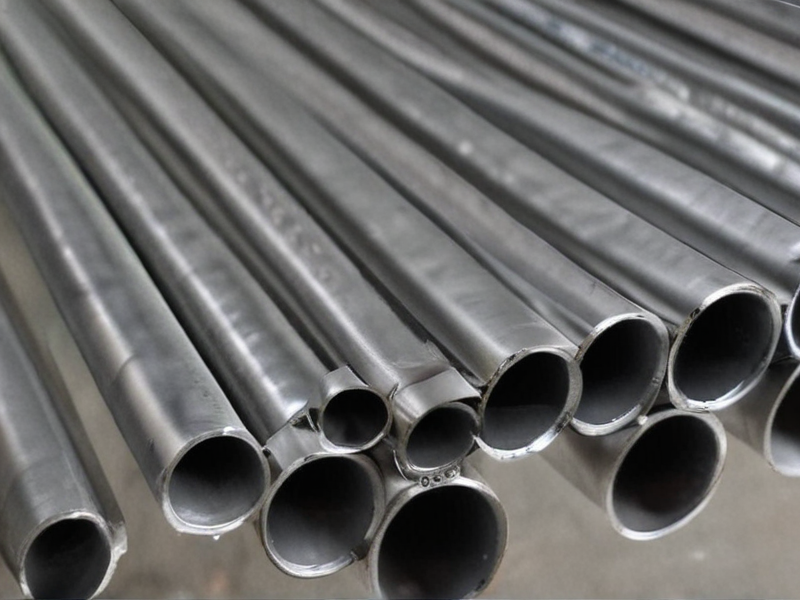
Types of welded tubing
Welded tubing is created by forming a flat strip of metal into a tube shape and then welding the seam. Here are the primary types:
1. Electric Resistance Welded (ERW) Tubing:
– Production: Made from cold-rolled or hot-rolled steel.
– Uses: Widely used in the automotive, furniture, and construction industries due to its cost-effectiveness and high dimensional accuracy.
2. High-Frequency Induction Welding (HFIW) Tubing:
– Production: Similar to ERW but uses a high-frequency electrical current to heat the edges of the strip before welding.
– Uses: Suitable for high-stress applications like oil and gas pipelines due to its robust weld quality.
3. Double Submerged Arc Welded (DSAW) Tubing:
– Production: Made by welding both the inside and outside of the seam, providing extra strength.
– Uses: Common in high-pressure environments, such as oil rigs and industrial pipelines.
4. Seamless Tubing:
– Production: Technically not welded but often discussed alongside welded types. Made by extruding a solid billet of metal.
– Uses: Preferred for high-pressure applications due to the absence of a seam, which eliminates potential weak points.
5. Laser Beam Welding (LBW) Tubing:
– Production: Uses a focused laser beam for precise and high-quality welds.
– Uses: Ideal for applications requiring fine tolerances and high strength, such as aerospace and medical devices.
Each type of welded tubing offers unique benefits, making them suitable for specific industrial applications based on factors like pressure, cost, and required strength.
Pros and Cons of Using welded tubing
Pros of Using Welded Tubing:
1. Cost-Effective: Welded tubing is generally less expensive than seamless tubing due to the less complex manufacturing process.
2. Availability: It’s widely available in various sizes and materials, making it easier to source for diverse applications.
3. Customization: Easier to manufacture in custom shapes and sizes compared to seamless tubes, allowing for more design flexibility.
4. Strength and Durability: Advances in welding technology have improved the strength and reliability of welded tubing, making it suitable for many structural applications.
5. Lead Time: Typically, welded tubing has shorter lead times compared to seamless tubing, which can be beneficial for time-sensitive projects.
6. Surface Finish: Welded tubing often has a smoother surface finish, which can be beneficial for aesthetic applications or when a smooth surface is required.
Cons of Using Welded Tubing:
1. Potential for Weakness: The welded seam can be a point of weakness, particularly under high pressure or stress conditions, making it less suitable for certain critical applications.
2. Corrosion Resistance: The welded seam can be more susceptible to corrosion, especially in harsh environments, unless properly treated or protected.
3. Internal Residual Stress: Welding can introduce residual stresses in the material, which may affect its performance in certain applications.
4. Inspection and Quality Control: Requires rigorous inspection and quality control to ensure the integrity of the weld, which can add to the overall cost and complexity.
5. Limited to Lower Pressure Applications: Generally not recommended for high-pressure applications where seamless tubing would be preferred due to its uniform strength.
6. Fatigue Resistance: The welded seam may reduce the fatigue resistance of the tubing, making it less ideal for applications involving cyclic loading or dynamic stresses.
Overall, the choice between welded and seamless tubing depends on specific application requirements, considering factors like cost, strength, and environmental conditions.
welded tubing Reference Specifications (varies for different product)
Welded tubing specifications are crucial for ensuring the proper performance and safety of the final product. Here are some key specifications that vary depending on the product type:
Material
– Stainless Steel: Common grades include 304, 316, and 321.
– Carbon Steel: Often specified as A513 or A500.
– Alloys: Depending on requirements, materials such as Inconel or Hastelloy may be used.
Dimensions
– Outer Diameter (OD): Typically ranges from 1/8 inch to 12 inches.
– Wall Thickness: Varies from 0.010 inches to 0.5 inches or more.
– Length: Standard lengths are 20 feet, but custom lengths can be produced.
Manufacturing Standards
– ASTM Standards: Common standards include ASTM A249 (welded austenitic steel boiler, superheater, heat-exchanger, and condenser tubes), ASTM A269 (seamless and welded austenitic stainless steel tubing for general service), and ASTM A554 (welded stainless steel mechanical tubing).
– ASME Standards: Often adhere to ASME Boiler and Pressure Vessel Code for critical applications.
Tolerances
– Dimensional Tolerance: Typically ±0.005 inches on OD and ±10% on wall thickness.
– Straightness: Generally 0.010 inches per foot of tubing length.
Mechanical Properties
– Tensile Strength: Varies by material but commonly ranges from 70,000 to 95,000 psi for stainless steel.
– Yield Strength: Ranges from 30,000 to 50,000 psi.
– Hardness: Measured in Rockwell B or C scale, depending on material.
Surface Finish
– Mill Finish: Standard finish directly from the manufacturing process.
– Polished Finish: Specified when aesthetic or hygienic qualities are required, with common finishes being #4, #6, or #8 mirror polish.
Testing and Quality Assurance
– Non-Destructive Testing (NDT): Methods include eddy current testing, ultrasonic testing, and hydrostatic testing.
– Destructive Testing: Includes tensile testing, flattening tests, and flare tests to ensure material integrity.
Certification
– Material Test Reports (MTRs): Provide detailed information about the chemical composition and mechanical properties.
– Compliance Certificates: Ensure adherence to specific standards like ASTM, ASME, or specific customer requirements.
By adhering to these specifications, welded tubing can meet the diverse requirements of industries such as automotive, aerospace, construction, and medical devices.
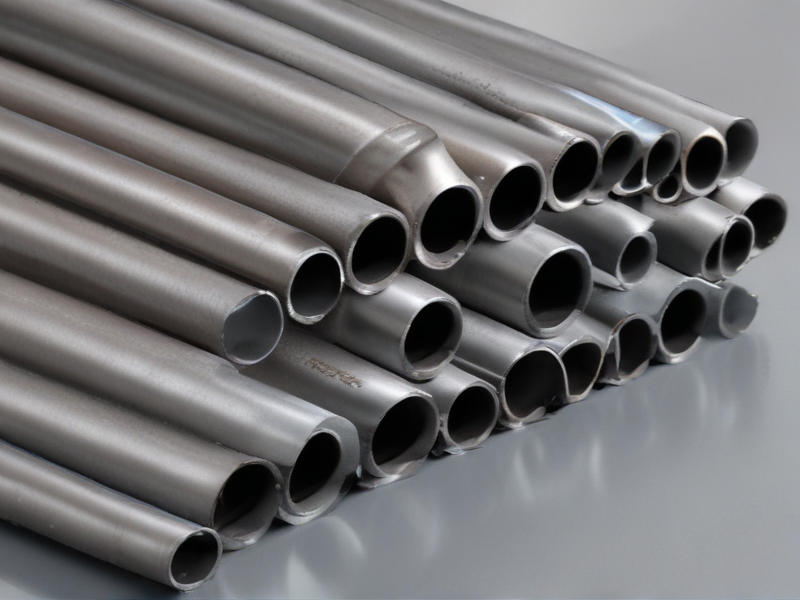
Applications of welded tubing
Welded tubing, created by welding together the edges of flat-rolled strips or plates, finds applications across numerous industries due to its cost-effectiveness, strength, and versatility.
1. Automotive Industry: Welded tubing is crucial in automotive manufacturing for exhaust systems, drive shafts, and vehicle frames. Its lightweight yet durable nature helps improve fuel efficiency and structural integrity.
2. Construction and Infrastructure: In construction, welded tubes are used for scaffolding, structural support in buildings, and handrails. They offer a combination of strength and flexibility, essential for maintaining safety and stability in construction projects.
3. Oil and Gas: Welded tubing is widely utilized in the oil and gas sector for pipelines, offshore platforms, and drilling rigs. Its resistance to corrosion and high-pressure capabilities make it ideal for transporting oil, gas, and other fluids.
4. HVAC and Plumbing: In heating, ventilation, air conditioning (HVAC), and plumbing systems, welded tubes are used for air ducts, water pipes, and gas lines. Their ability to withstand high temperatures and pressures ensures reliable performance in these applications.
5. Manufacturing and Machinery: In manufacturing, welded tubing serves as components in machinery, conveyor systems, and industrial equipment. Its precision and uniformity support the efficient operation of various mechanical systems.
6. Aerospace and Defense: Aerospace applications require materials that offer high strength-to-weight ratios and resistance to extreme conditions. Welded tubing meets these demands in components like hydraulic systems, fuel lines, and structural elements in aircraft and spacecraft.
7. Furniture and Appliances: Welded tubes are also used in making furniture and household appliances. They provide a sturdy yet lightweight framework for products such as chairs, tables, and appliances, combining aesthetic appeal with functional strength.
These applications highlight the versatility and reliability of welded tubing across different sectors, making it a crucial material in modern engineering and manufacturing.
Material of welded tubing
Welded tubing is manufactured from a wide variety of materials, each chosen based on specific application requirements, including mechanical properties, corrosion resistance, and thermal stability. Here are some common materials used for welded tubing:
1. Stainless Steel:
– 304/304L: Widely used for its corrosion resistance and strength. It is suitable for most general-purpose applications.
– 316/316L: Offers higher corrosion resistance than 304, especially in marine and chloride environments.
– 321: Stabilized with titanium, making it ideal for high-temperature applications.
2. Carbon Steel:
– ASTM A513: Commonly used in structural and mechanical applications due to its good machinability and strength.
– ASTM A500: Suitable for structural applications, offering good weldability and mechanical properties.
3. Alloy Steel:
– 4130: Known for its strength and toughness, often used in aerospace and motorsport applications.
– 4140: Similar to 4130 but with higher carbon content, offering enhanced strength and wear resistance.
4. Nickel Alloys:
– Inconel 600: Excellent resistance to high temperatures and oxidation, used in extreme environments.
– Monel 400: Resists corrosion by seawater and various acids, suitable for marine and chemical processing applications.
5. Aluminum:
– 6061-T6: High strength, good corrosion resistance, and excellent weldability, commonly used in aerospace, automotive, and structural applications.
– 5052: Known for its high fatigue strength and excellent corrosion resistance, used in marine and fuel tank applications.
6. Titanium:
– Grade 2: Excellent corrosion resistance and strength-to-weight ratio, used in aerospace, chemical processing, and medical applications.
– Grade 5 (Ti-6Al-4V): Higher strength than Grade 2, suitable for high-performance applications.
Each material offers distinct advantages, making the selection process crucial based on the specific requirements of the end application, including mechanical loads, environmental conditions, and regulatory standards.
Quality Testing Methods for welded tubing and how to control the quality
Quality testing methods for welded tubing include both non-destructive and destructive techniques. Key methods are:
1. Visual Inspection: The simplest form of quality control, where the tubing is visually checked for surface defects, weld bead uniformity, and overall appearance.
2. Ultrasonic Testing (UT): Uses high-frequency sound waves to detect internal flaws and inconsistencies in the weld. It is highly effective for identifying voids, cracks, and incomplete fusion.
3. Radiographic Testing (RT): Employs X-rays or gamma rays to produce an image of the internal structure, highlighting defects such as cracks, porosity, and inclusions.
4. Eddy Current Testing (ECT): Uses electromagnetic fields to detect surface and near-surface defects. It is particularly useful for identifying cracks, seams, and other discontinuities.
5. Hydrostatic Testing: Involves filling the tubing with water and applying pressure to ensure it can withstand the specified pressure without leaking or bursting.
6. Magnetic Particle Inspection (MPI): For ferromagnetic materials, this method uses magnetic fields to detect surface and near-surface defects by the accumulation of magnetic particles at discontinuities.
7. Dye Penetrant Inspection (DPI): Applies a liquid dye to the surface, which penetrates defects. Excess dye is removed, and a developer is applied to draw out the dye from defects, making them visible.
8. Tensile Testing: Measures the material’s strength and ductility by applying tension until it breaks. It is a destructive test and provides valuable information about the mechanical properties of the weld.
Quality control involves several key steps:
– Establishing Standards: Implement industry standards and specifications that the welded tubing must meet.
– Process Control: Monitor and control welding parameters (temperature, speed, pressure) during production to ensure consistent quality.
– Regular Inspections: Conduct routine inspections using the above methods at different stages of production.
– Documentation and Traceability: Maintain detailed records of inspections and tests for traceability and accountability.
– Training: Ensure personnel are well-trained in both the operation of testing equipment and the interpretation of results.
By integrating these methods and controls, manufacturers can ensure the production of high-quality welded tubing.
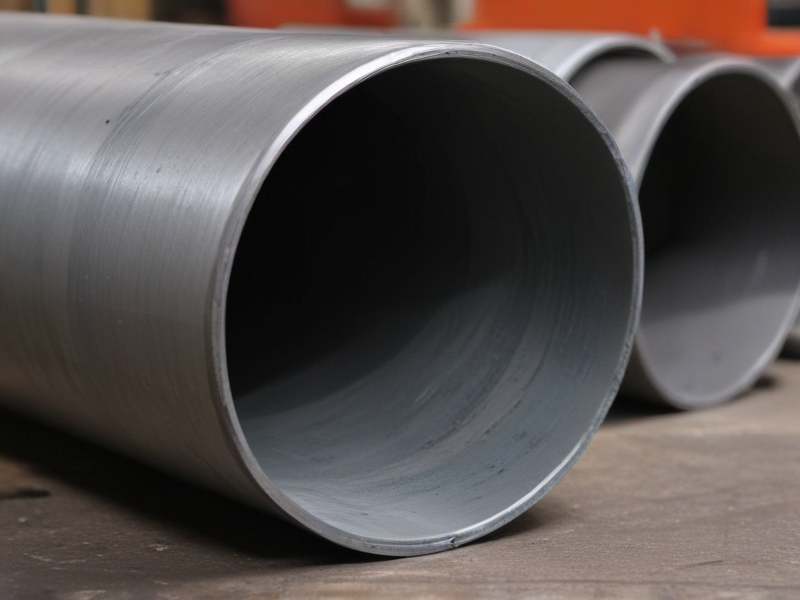
The Work Process and how to use welded tubing
Work Process for Using Welded Tubing
#### 1. Selection:
– Material: Choose the right alloy based on application needs (e.g., stainless steel, carbon steel).
– Size and Shape: Select appropriate diameter, wall thickness, and length.
#### 2. Cutting:
– Tools: Use saws, torches, or laser cutters.
– Precision: Ensure cuts are clean and precise to fit specifications.
#### 3. Preparation:
– Cleaning: Remove any contaminants or oxidation.
– Fitting: Align and fit tubing sections together accurately.
#### 4. Welding:
– Method: Choose welding techniques like TIG, MIG, or resistance welding.
– Execution: Weld along the seam, ensuring uniform penetration and minimal distortion.
#### 5. Inspection:
– Visual: Check for weld defects such as cracks or incomplete fusion.
– Non-Destructive Testing: Use methods like X-ray or ultrasonic testing for internal flaws.
#### 6. Finishing:
– Deburring: Remove sharp edges and burrs.
– Coating: Apply protective coatings if required (e.g., galvanizing, painting).
#### 7. Assembly:
– Joining: Weld or mechanically join tubing with other components.
– Alignment: Ensure the assembly is aligned correctly and secured.
#### 8. Testing:
– Pressure Testing: Check for leaks or weaknesses.
– Functionality: Verify performance according to specifications.
Applications
Welded tubing is used in various sectors including automotive, construction, and industrial machinery for conveying fluids, structural support, and fabrication purposes.
Key Tips:
– Safety: Follow all safety protocols during cutting and welding.
– Quality Control: Maintain rigorous inspection standards to ensure reliability and performance.
welded tubing Importing questions including Cost,Supplier,Sample,Certification and Market
When importing welded tubing, several key considerations need to be addressed to ensure a smooth and cost-effective process:
1. Cost:
– Unit Price: Compare prices from multiple suppliers. Prices can vary based on material, dimensions, and quantity.
– Shipping Costs: Factor in shipping, handling, and potential customs duties.
– Total Cost: Include taxes, import duties, and potential additional fees for handling or storage.
2. Supplier:
– Reputation: Research suppliers’ backgrounds, customer reviews, and industry reputation.
– Location: Proximity to your location can influence shipping costs and delivery times.
– Capabilities: Ensure the supplier can meet your specifications and volume requirements.
3. Sample:
– Requesting Samples: Obtain samples to verify quality and specifications before placing large orders.
– Sample Cost: Some suppliers may charge for samples or offer them for free depending on the relationship or order potential.
– Evaluation: Test samples rigorously to ensure they meet your standards and requirements.
4. Certification:
– Quality Standards: Ensure the tubing meets necessary standards (e.g., ISO, ASTM).
– Documentation: Verify certificates of compliance, quality control reports, and any required safety certifications.
– Regulatory Compliance: Ensure the products meet the regulatory requirements of your country.
5. Market:
– Demand Analysis: Assess market demand and potential competition for welded tubing in your target region.
– Pricing Strategy: Determine competitive pricing strategies based on market analysis.
– Distribution Channels: Identify the best distribution channels for your product, whether direct to consumer, through distributors, or other means.
By considering these aspects, you can effectively navigate the complexities of importing welded tubing and make informed decisions that align with your business goals.
How to find and select check reliable welded tubing manufacturers in China
Finding and selecting reliable welded tubing manufacturers in China involves several steps to ensure quality and dependability:
1. Online Directories and Marketplaces: Start with reputable B2B platforms like Alibaba, Made-in-China, or Global Sources. These platforms offer a vast list of manufacturers and detailed company profiles.
2. Verify Certifications: Ensure manufacturers have necessary certifications such as ISO 9001, CE, or ASTM. Certifications indicate adherence to international quality standards.
3. Request Samples: Ask for samples to inspect the quality of the tubing. Assess the welding quality, material composition, and finish.
4. Check Company Reputation: Look for reviews and ratings on B2B platforms. Use third-party review sites or business directories to gauge the company’s reputation.
5. Factory Visits: If possible, visit the factories to inspect their production capabilities, quality control processes, and working conditions.
6. Communication and Support: Evaluate the responsiveness and professionalism of their sales and support teams. Reliable manufacturers provide clear and prompt communication.
7. Compare Pricing and Lead Times: Obtain quotes from multiple manufacturers. Compare prices, but be wary of significantly lower prices which might indicate lower quality. Check lead times and delivery capabilities to ensure they meet your requirements.
8. Check Export Experience: Manufacturers with extensive export experience are often more reliable. They understand international standards and logistics better.
9. References and Case Studies: Ask for references or case studies from previous clients, particularly from your industry. Contact these references to get firsthand feedback.
10. Third-party Inspections: Consider hiring third-party inspection services to verify the quality and compliance of the products before shipment.
By following these steps, you can identify and select a reliable welded tubing manufacturer in China, ensuring quality and dependable supply.
Background Research for welded tubing manufacturers Companies in China, use qcc.com archive.org importyeti.com
Background Research on Welded Tubing Manufacturers in China
China hosts numerous manufacturers specializing in welded tubing, serving a variety of industries. Here’s an overview of some prominent companies identified through sources like qcc.com, archive.org, and importyeti.com.
1. 浙江金洲管道科技股份有限公司 (Zhejiang Kingland Pipeline and Technologies Co., Ltd.):
– Overview: Established in 1999, this company is a leading manufacturer of welded steel pipes in China. They cater to industries including oil and gas, water supply, and construction.
– Location: Based in Zhuji, Zhejiang province.
– Website: [qcc.com](https://www.qcc.com/firm/ef4f963b1c580e23956e41c79f5a36f9.html).
2. 江苏永钢集团有限公司 (Jiangsu Yonggang Group Co., Ltd.):
– Overview: Known for their comprehensive steel products, including welded tubes, they have a significant presence in the domestic and international markets.
– Location: Headquartered in Zhangjiagang, Jiangsu province.
– Website: [qcc.com](https://www.qcc.com/firm/0da0fcbf8825234826909c3b682f06f7.html).
3. 天津友发钢管集团股份有限公司 (Tianjin Youfa Steel Pipe Group Co., Ltd.):
– Overview: One of the largest welded steel pipe manufacturers in China, producing a wide range of products including galvanized and non-galvanized steel pipes.
– Location: Based in Tianjin.
– Website: [qcc.com](https://www.qcc.com/firm/eab0b0e933a09f09a1eb137fb96f2b67.html).
4. 宝钢集团 (Baosteel Group):
– Overview: A giant in the Chinese steel industry, Baosteel manufactures high-quality welded tubes among other steel products, with a significant global footprint.
– Location: Headquarters in Shanghai.
– Website: [qcc.com](https://www.qcc.com/firm/838005ea7260c9d47e7f295470893599.html).
5. 鞍钢集团 (Ansteel Group):
– Overview: Another major player, Ansteel is known for its comprehensive range of steel products including welded pipes, catering to various industrial sectors.
– Location: Based in Anshan, Liaoning province.
– Website: [qcc.com](https://www.qcc.com/firm/84ecaf75f40f4f029d9d5883ceab526e.html).
These companies represent a cross-section of the welded tubing manufacturing industry in China, known for their extensive product lines, large production capacities, and significant contributions to both domestic and international markets.
For more detailed information, including specific product offerings and corporate histories, you can refer to their profiles on qcc.com and other business directories.
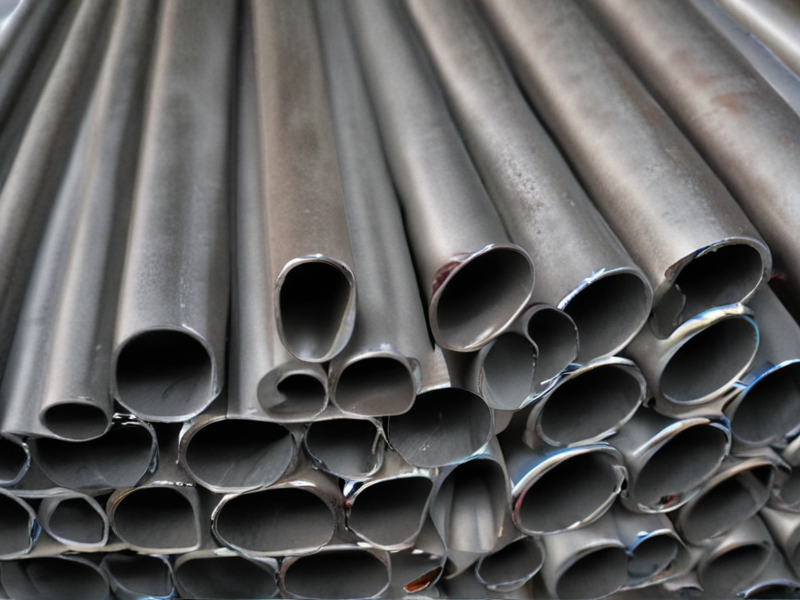
Price Cost Research for welded tubing manufacturers Companies in China, use temu.com and 1688.com
For welded tubing manufacturers in China, here are some insights based on research from Temu.com and 1688.com:
Temu.com
On Temu.com, you can find various suppliers of welded tubing, though specific prices are not readily available on the search results. It is recommended to contact suppliers directly through the platform for detailed quotations and pricing based on your specific requirements.
1688.com
1688.com, a subsidiary of Alibaba, lists numerous manufacturers and suppliers offering welded tubing. Here are some examples:
1. 雄县宇通塑料制品有限公司:
– Product: PVC steel wire hose, transparent, high-temperature resistant, thickened.
– Price: Approximately ¥8.46 per meter.
– Delivery: 48-72 hours.
2. 潍坊市美拓思塑料制品有限公司:
– Product: CPVC power pipe, custom-made for high-pressure cable protection.
– Price: Around ¥12.00 per piece.
– Delivery: Within 72 hours.
3. 河北献博管道科技有限公司:
– Product: High-pressure oxygen acetylene hose.
– Price: ¥1.71 per meter.
– Delivery: 48 hours.
4. 东莞市穗滢新型材料科技有限公司:
– Product: PE50 oxygenation pipe for aquaculture and irrigation.
– Price: ¥0.55 per meter.
– Delivery: 24 hours.
5. 山东圣泽管业有限公司:
– Product: PE water supply pipe, small diameter irrigation pipe.
– Price: ¥8.58 per meter.
– Delivery: 48 hours.
Recommendations
For detailed inquiries and bulk orders, it’s advisable to directly contact the manufacturers via these platforms. Prices can vary based on order quantity, customization, and delivery terms. Both Temu.com and 1688.com provide robust platforms to compare different suppliers and negotiate better deals.
For further details, visiting the specific product pages and reaching out to the suppliers would be beneficial.
Shipping Cost for welded tubing import from China
Importing welded tubing from China involves several cost components that impact the total shipping cost. These include:
1. Freight Costs: This is the primary cost and varies by the mode of transport (air or sea). Sea freight is typically more economical for bulky items like welded tubing. Costs are influenced by factors such as distance, shipping route, and the weight and volume of the shipment. As of mid-2024, sea freight for welded tubing ranges from $2,000 to $4,000 per 20-foot container.
2. Customs Duties and Taxes: Duties on welded tubing vary depending on the country of import. In the US, for instance, the tariff for imported steel tubing is around 25% of the product value, plus any additional anti-dumping duties that may apply.
3. Port Charges and Handling Fees: These include terminal handling charges, wharfage, and documentation fees, which can add $200 to $500 per container.
4. Insurance: Cargo insurance protects against potential damage or loss during transit. Premiums are typically between 0.5% to 2% of the shipment’s value.
5. Inland Transportation: Costs for transporting goods from the port to the final destination vary based on distance and transportation method. Trucking within the US might add $500 to $1,000 to the total cost.
6. Additional Fees: These may include customs broker fees, inspection fees, and warehousing, which can add another $200 to $500.
In summary, the total shipping cost for importing welded tubing from China can range from $3,000 to $6,500 per 20-foot container, depending on specific variables such as shipment size, destination, and applicable duties and fees.
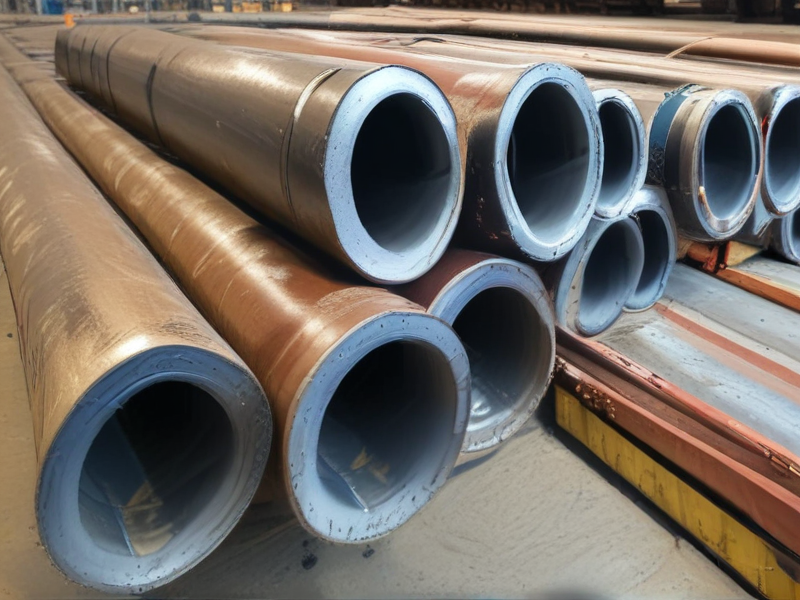
Compare China and Other welded tubing Markets: Products Quality and Price,Visible and Hidden Costs
Comparison of Welded Tubing Markets: China vs. Others
#### Product Quality
– China: Chinese welded tubing is generally considered to have lower quality compared to Western standards. Issues include inconsistent wall thickness, inferior raw materials, and weaker weld seams. However, quality can vary significantly between manufacturers.
– Others (e.g., USA, Germany, Japan): These markets typically offer higher quality tubing, adhering to stringent industry standards. They use better raw materials and advanced welding technologies, ensuring durability and uniformity.
#### Price
– China: Chinese tubing is significantly cheaper, often 20-30% less than Western counterparts. This price advantage is due to lower labor costs, economies of scale, and less stringent environmental regulations.
– Others: Tubing from Western countries is more expensive, reflecting higher production costs, stricter regulations, and the emphasis on quality.
#### Visible Costs
– China: Lower initial purchase price is the main visible cost advantage.
– Others: Higher upfront costs due to better quality and compliance with international standards.
#### Hidden Costs
– China:
– Quality Control: Higher likelihood of defects leading to increased rejection rates.
– Logistics: Longer shipping times and potential delays.
– Regulatory Compliance: Potential issues with meeting international standards.
– Durability: Shorter lifespan and more frequent replacements.
– Others:
– Maintenance: Lower maintenance costs due to higher durability.
– Regulatory Compliance: Fewer issues in meeting international standards.
– Reputation: Better perception and reliability, which can lead to long-term savings and customer trust.
#### Conclusion
While Chinese welded tubing offers a significant cost advantage, the hidden costs associated with quality control, logistics, and durability can offset the initial savings. In contrast, tubing from Western markets, though more expensive upfront, typically offers better quality, compliance, and lower long-term costs. Buyers must weigh these factors based on their specific needs and usage scenarios.
Custom Private Labeling and Branding Opportunities with Chinese welded tubing Manufacturers
Custom private labeling and branding with Chinese welded tubing manufacturers offer significant opportunities for businesses looking to enhance their product offerings and market presence. China, being a global manufacturing hub, provides cost-effective production capabilities combined with advanced technology and quality standards.
Benefits of Custom Private Labeling and Branding
1. Cost Efficiency: Chinese manufacturers offer competitive pricing due to lower labor costs and economies of scale, allowing businesses to increase their profit margins.
2. High Quality: Many Chinese manufacturers adhere to international standards, ensuring high-quality welded tubing that meets industry-specific requirements.
3. Customization Options: Chinese manufacturers provide extensive customization options, including size, material, coating, and finishes. This allows businesses to tailor products to specific market needs and preferences.
4. Branding Flexibility: Companies can leverage private labeling to build their brand identity. Manufacturers offer customizable packaging, logos, and labeling, enabling businesses to maintain consistent branding across all products.
Key Considerations
1. Supplier Selection: It is crucial to choose reputable manufacturers with a proven track record. Research and due diligence, including factory visits and certifications verification, are essential.
2. Quality Control: Implement rigorous quality control processes to ensure products meet desired standards. This can include third-party inspections and testing.
3. Communication: Clear and effective communication is vital. Working with manufacturers who have English-speaking staff can facilitate smoother interactions and reduce misunderstandings.
4. Lead Times and Logistics: Understanding lead times and having a reliable logistics plan are critical to ensure timely delivery. This includes accounting for production times, shipping durations, and potential customs delays.
By leveraging Chinese welded tubing manufacturers for custom private labeling and branding, businesses can offer high-quality, tailored products that resonate with their target market, ultimately enhancing brand reputation and market share.
Tips for Procurement and Considerations when Purchasing welded tubing
Tips for Procurement and Considerations when Purchasing Welded Tubing
1. Material Selection:
– Determine Requirements: Assess the specific mechanical, chemical, and physical requirements for the application.
– Standard Specifications: Ensure the material meets relevant standards (e.g., ASTM, ASME) for quality and performance.
2. Tube Specifications:
– Dimensions: Verify the required diameter, wall thickness, and length to match the application needs.
– Tolerances: Check permissible variations in dimensions to ensure compatibility with other components.
3. Quality and Testing:
– Inspection Certifications: Request mill test certificates to verify chemical composition and mechanical properties.
– Non-Destructive Testing (NDT): Ensure the tubing undergoes appropriate NDT methods (e.g., ultrasonic, X-ray) to detect internal defects.
4. Supplier Evaluation:
– Reputation and Experience: Choose suppliers with a proven track record in providing high-quality welded tubing.
– Compliance and Standards: Verify that the supplier adheres to international quality standards and industry-specific certifications.
5. Cost Considerations:
– Total Cost of Ownership: Consider not just the purchase price but also factors like shipping, handling, and potential downtime costs.
– Bulk Purchasing: Evaluate the benefits of bulk purchasing for cost savings, but balance this against storage capabilities and potential material degradation.
6. Lead Times and Availability:
– Inventory Levels: Check supplier’s stock levels to ensure timely availability and reduce lead times.
– Lead Time: Understand the lead time for manufacturing and delivery, and plan procurement schedules accordingly.
7. Customization Needs:
– Special Requirements: If custom sizes or specific alloys are required, ensure the supplier has the capability to meet these needs.
– Value-Added Services: Look for suppliers offering additional services such as cutting, finishing, or coating.
8. Environmental and Safety Regulations:
– Compliance: Ensure the tubing complies with relevant environmental and safety regulations.
– Sustainability: Consider the environmental impact of the materials and the supplier’s sustainability practices.
By carefully considering these factors, you can ensure the procurement of welded tubing that meets quality standards, application requirements, and budget constraints.
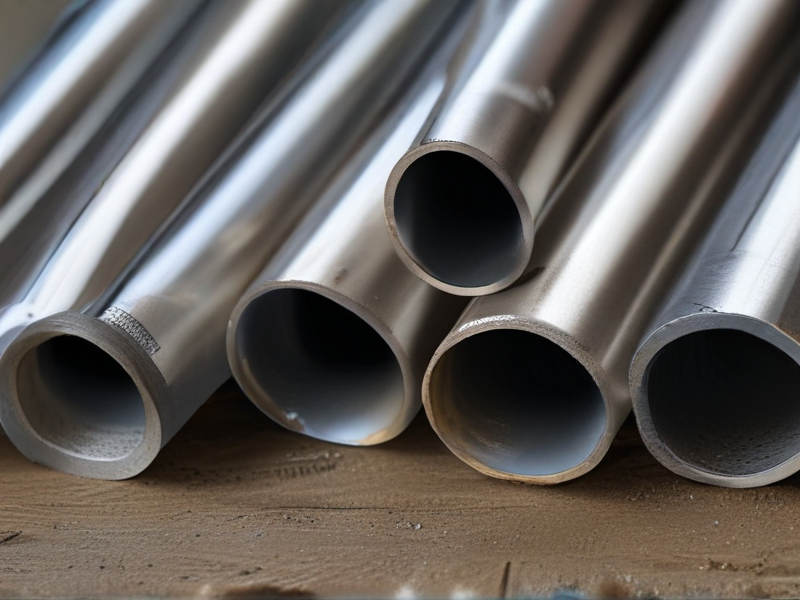
FAQs on Sourcing and Manufacturing welded tubing in China
FAQs on Sourcing and Manufacturing Welded Tubing in China
1. Why source welded tubing from China?
China offers competitive pricing, extensive manufacturing capabilities, and a wide range of materials and specifications. Chinese manufacturers often have advanced technology and experience in producing high-quality welded tubing.
2. What materials are commonly used in welded tubing from China?
Common materials include stainless steel, carbon steel, aluminum, and various alloys. Each material is selected based on the application’s specific requirements, such as corrosion resistance, strength, and conductivity.
3. How do I find reliable suppliers in China?
Use platforms like Alibaba, Global Sources, and Made-in-China to identify potential suppliers. Verify their credentials through customer reviews, factory visits, and third-party audits. Request samples to assess quality.
4. What standards and certifications should I look for?
Look for ISO 9001, ISO 14001, and industry-specific certifications like ASTM, ASME, or EN standards. These ensure the manufacturer adheres to international quality and environmental management standards.
5. What is the typical lead time for manufacturing and delivery?
Lead times vary depending on order size, complexity, and the supplier’s production schedule. Typically, expect 4-8 weeks for manufacturing and an additional 2-4 weeks for shipping.
6. Can I customize the tubing specifications?
Yes, most Chinese manufacturers offer customization options, including dimensions, material grades, surface finishes, and special coatings. Provide detailed specifications and drawings for accurate quotes and production.
7. How can I ensure quality control?
Implement stringent quality control measures, including pre-production samples, in-process inspections, and final product inspections. Consider hiring third-party inspection services for unbiased quality checks.
8. What are the payment terms typically offered?
Common payment terms include 30% deposit upfront and 70% balance before shipment (T/T). Letters of Credit (L/C) are also widely accepted, providing additional security for large transactions.
9. Are there any import duties or tariffs?
Import duties and tariffs depend on your country’s trade policies with China. Check with your local customs office or a customs broker for accurate information on applicable charges.
10. How can I manage shipping and logistics?
Collaborate with experienced freight forwarders who can handle customs clearance, documentation, and transportation. Opt for CIF (Cost, Insurance, and Freight) or FOB (Free on Board) shipping terms to clarify responsibilities.