Top 10 rubber gasket materials in China introduce,list main products and website if have
Here are the top 10 rubber gasket material manufacturers in China, including their main products and websites:
1. Miles Rubber and Plastic Technology Co., Ltd.
– Main Products: Silicon rubber seals and gaskets, high-temperature rubber O-ring seals, rubber bellows, custom seals.
– Website: [Miles Rubber](http://www.milesrubber.com)
2. Tongxiang Spring, Rubber, and Plastic Tech Co., Ltd.
– Main Products: Rubber gaskets, silicon rubber parts, rubber bellows, rubber O-rings.
– Website: [Tongxiang Spring](http://www.springrubber.com)
3. Yiho Polytek Co., Ltd.
– Main Products: Rubber gaskets and seals, auto rubber parts, silicone keypads, medical rubber parts.
– Website: [Yiho Polytek](http://www.yihopolytek.com)
4. Hengheng Sealing Technology Co., Ltd.
– Main Products: Rubber gaskets and seals, metal gaskets, high-pressure rubber seals, food-grade rubber gaskets.
– Website: [Hengheng Sealing](http://www.henghengseal.com)
5. Unilutek Industry Co., Ltd.
– Main Products: Rubber molded gaskets, PVC strip door curtains, hydraulic and oil seals.
– Website: [Unilutek Industry](http://www.unilutek.com)
6. Jin Hongtai Rubber Co., Ltd.
– Main Products: Rubber gaskets and seals, SEG silicone strips, rubber seal strips.
– Website: [Jin Hongtai Rubber](http://www.jinhongtai.com)
7. Jiangyin No. 3 Rubber Manufacturer Co., Ltd.
– Main Products: Oil seals, mechanical seals, rubberized rings.
– Website: [Jiangyin No. 3 Rubber](http://www.jiangyinrubber.com)
8. Hangzhou Bright Rubber Plastic Product Co., Ltd.
– Main Products: Oil seals, mechanical seal rings, rubber gaskets.
– Website: [Hangzhou Bright Rubber](http://www.bright-rubber.com)
9. Ningbo Bandak Sealing Material Co., Ltd.
– Main Products: Expanded PTFE, industrial gaskets, braided packing.
– Website: [Bandak Sealing](http://www.bandaksealing.com)
10. Qingdao Source Seal Technology Co., Ltd.
– Main Products: Oil seals, O-rings, sealing parts.
– Website: [Source Seal](http://www.sourceseal.com)
These manufacturers are renowned for their quality products and have extensive export capabilities, ensuring they can meet global standards and demands.
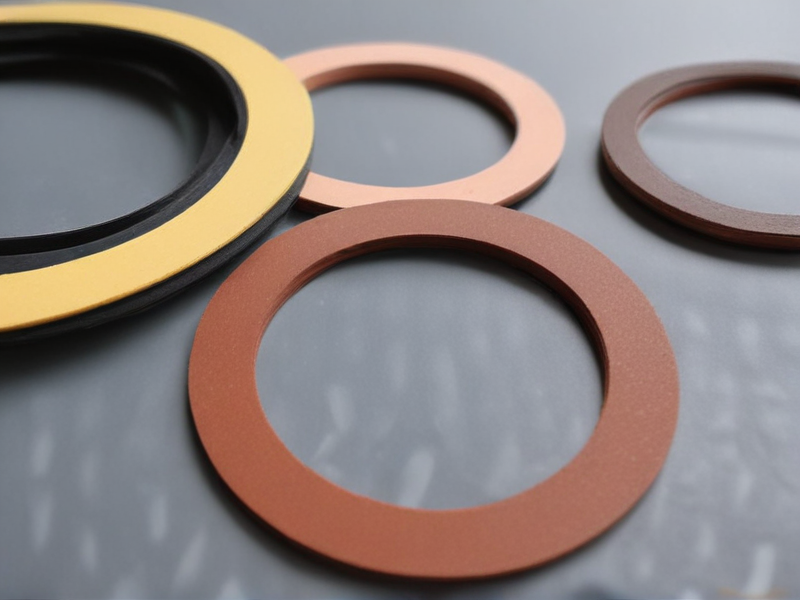
Types of rubber gasket materials
Rubber gaskets are essential for creating seals to prevent leaks in various industrial applications. Different types of rubber gasket materials offer specific properties suitable for different environments and conditions. Here are the primary types:
1. Natural Rubber (NR): Known for its excellent elasticity and tensile strength, natural rubber gaskets are ideal for applications requiring good resistance to abrasion and tear. However, they have limited resistance to ozone, oils, and chemicals.
2. Neoprene (CR): Neoprene gaskets offer good chemical stability and are resistant to oils, greases, and solvents. They also provide moderate resistance to ozone and weathering, making them suitable for outdoor applications.
3. Nitrile (NBR): Nitrile rubber is well-known for its excellent resistance to oils, fuels, and other petroleum-based products. It is widely used in automotive and aerospace industries but has poor resistance to ozone and weathering.
4. EPDM (Ethylene Propylene Diene Monomer): EPDM gaskets are ideal for outdoor applications due to their superior resistance to ozone, UV rays, and weathering. They also perform well with water, steam, and some chemicals, but are not suitable for petroleum-based oils and solvents.
5. Silicone Rubber: Silicone gaskets can withstand extreme temperatures, ranging from -60°C to 230°C (-76°F to 446°F). They are also resistant to ozone, UV, and weathering, making them suitable for food processing, medical devices, and high-temperature applications.
6. Viton (FKM): Viton gaskets are highly resistant to heat, oils, fuels, and chemicals, making them suitable for high-performance applications in automotive, aerospace, and chemical processing industries.
7. SBR (Styrene-Butadiene Rubber): SBR gaskets offer good abrasion resistance and are commonly used in water and low-temperature applications. However, they have limited resistance to oils and chemicals.
Each type of rubber gasket material has unique properties that make it suitable for specific applications, depending on the environmental conditions and the substances it will come into contact with.
Pros and Cons of Using rubber gasket materials
Rubber gaskets are commonly used in various industries due to their flexibility, sealing capabilities, and durability. Here are the pros and cons of using rubber gasket materials:
Pros:
1. Excellent Sealing:
– Rubber gaskets provide superior sealing capabilities, preventing leaks of gases or liquids, which is critical in many industrial applications.
2. Flexibility and Compressibility:
– They offer high flexibility and compressibility, allowing them to conform to irregular surfaces and maintain a tight seal under varying pressure and temperature conditions.
3. Wide Range of Materials:
– Available in various types such as nitrile, EPDM, silicone, and Viton, rubber gaskets can be chosen based on specific chemical and environmental resistances.
4. Temperature Resistance:
– Certain rubber materials like silicone and Viton can withstand high temperatures, making them suitable for applications involving extreme heat.
5. Chemical Resistance:
– Rubber gaskets can be formulated to resist a wide range of chemicals, oils, and solvents, enhancing their suitability for diverse applications.
6. Durability and Longevity:
– When chosen appropriately for the environment, rubber gaskets can last long without significant degradation, providing cost-effective sealing solutions.
Cons:
1. Limited Temperature Range for Some Types:
– Not all rubber materials can withstand extreme temperatures. For example, natural rubber degrades quickly at high temperatures.
2. Susceptibility to Swelling:
– Certain rubber gaskets can swell when exposed to specific chemicals or oils, leading to failure in sealing.
3. Permeability:
– Some rubber materials are permeable to gases, which can be a drawback in applications requiring airtight seals.
4. Aging and Degradation:
– Over time, rubber gaskets can deteriorate due to exposure to UV light, ozone, and other environmental factors, which can reduce their effectiveness.
5. Cost Variability:
– High-performance rubber materials like Viton can be expensive compared to other gasket materials, impacting the overall cost of the application.
In summary, while rubber gaskets offer excellent sealing, flexibility, and durability, their performance can be limited by temperature, chemical exposure, and environmental factors. Selecting the appropriate rubber material based on the specific application requirements is crucial for maximizing their benefits and minimizing drawbacks.
rubber gasket materials Reference Specifications (varies for different product)
Rubber gaskets are used to seal gaps between two surfaces, preventing leakage of fluids or gases. The selection of materials for rubber gaskets depends on the application requirements, including temperature, pressure, chemical exposure, and mechanical stress. Below are some commonly used rubber gasket materials and their reference specifications:
1. Nitrile Rubber (NBR)
– Temperature Range: -40°C to 120°C (-40°F to 248°F)
– Hardness (Shore A): 40-90
– Standards: ASTM D2000, SAE J200
– Applications: Oil and fuel systems, automotive, marine
– Properties: Excellent resistance to petroleum-based oils and fuels, good mechanical properties
2. Ethylene Propylene Diene Monomer (EPDM)
– Temperature Range: -50°C to 150°C (-58°F to 302°F)
– Hardness (Shore A): 40-90
– Standards: ASTM D2000, SAE J200
– Applications: Weather seals, brake systems, HVAC
– Properties: Excellent resistance to weather, ozone, and aging; good chemical resistance
3. Silicone Rubber
– Temperature Range: -60°C to 200°C (-76°F to 392°F)
– Hardness (Shore A): 20-80
– Standards: ASTM D1418, FDA compliance for food-grade applications
– Applications: Food and beverage, medical devices, high-temperature seals
– Properties: High temperature stability, flexibility, and non-reactive with many chemicals
4. Viton® (Fluoroelastomer)
– Temperature Range: -20°C to 200°C (-4°F to 392°F)
– Hardness (Shore A): 55-95
– Standards: ASTM D2000, SAE J200
– Applications: Chemical processing, aerospace, automotive
– Properties: Excellent chemical resistance, high-temperature stability, and durability
5. Neoprene (Chloroprene Rubber)
– Temperature Range: -40°C to 120°C (-40°F to 248°F)
– Hardness (Shore A): 40-90
– Standards: ASTM D2000, SAE J200
– Applications: Refrigeration, automotive, industrial
– Properties: Good chemical stability, flexibility, and resistance to weather and ozone
6. Natural Rubber (NR)
– Temperature Range: -50°C to 70°C (-58°F to 158°F)
– Hardness (Shore A): 30-90
– Standards: ASTM D2000, ISO 1629
– Applications: Automotive, industrial machinery, vibration damping
– Properties: Excellent tensile strength, flexibility, and abrasion resistance
Selecting the appropriate rubber gasket material involves evaluating these specifications against the application’s operational environment to ensure optimal performance and longevity.
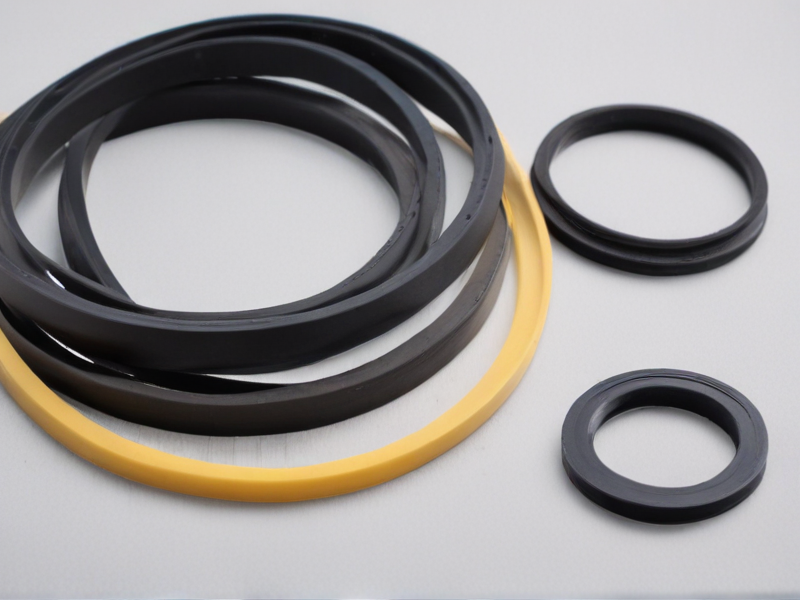
Applications of rubber gasket materials
Rubber gasket materials are crucial in various industries due to their sealing properties, flexibility, and durability. Here are some key applications:
1. Automotive Industry:
– Engine Components: Rubber gaskets seal engine parts, preventing oil and coolant leaks, enhancing engine performance and longevity.
– Exhaust Systems: They are used in exhaust systems to prevent gas leaks and withstand high temperatures and vibrations.
2. Aerospace Industry:
– Fuel Systems: Rubber gaskets are essential in sealing fuel systems, ensuring no leakage and maintaining system integrity under extreme pressures and temperatures.
– Cabin Seals: They provide airtight seals in cabins, crucial for maintaining pressure and comfort.
3. Oil and Gas Industry:
– Pipeline Sealing: Rubber gaskets are used to seal pipelines, preventing leaks of oil, gas, and other chemicals, ensuring safety and efficiency.
– Valves and Flanges: They provide tight seals in valves and flanges, critical for controlling fluid flow and preventing leaks.
4. Food and Beverage Industry:
– Processing Equipment: Rubber gaskets ensure sanitary seals in food processing equipment, preventing contamination and maintaining hygiene.
– Bottle Seals: Used in bottle caps and closures to keep beverages fresh and uncontaminated.
5. Medical Devices:
– Sterile Equipment: Rubber gaskets provide seals in medical devices, ensuring sterility and preventing leaks of fluids and gases.
– Diagnostic Equipment: They are used in diagnostic equipment to provide airtight and liquid-tight seals.
6. Industrial Machinery:
– Pumps and Compressors: Rubber gaskets seal components in pumps and compressors, ensuring efficient operation and preventing leaks.
– Hydraulic Systems: They maintain fluid seals in hydraulic systems, essential for effective pressure management and system performance.
7. Electrical and Electronics:
– Enclosures: Rubber gaskets seal electronic enclosures, protecting sensitive components from dust, moisture, and other environmental factors.
– Connectors: They provide seals in electrical connectors, ensuring stable connections and preventing short circuits.
Overall, rubber gasket materials are versatile and essential for ensuring the safety, efficiency, and reliability of various systems across numerous industries.
Material of rubber gasket materials
Rubber gaskets are crucial components used in various industries to provide a seal between two surfaces, preventing leaks of liquids or gases. The materials used for rubber gaskets vary based on the specific requirements of the application, such as temperature resistance, chemical compatibility, and mechanical properties. Here are some common rubber gasket materials:
1. Nitrile Butadiene Rubber (NBR): Known for its excellent resistance to oils, fuels, and other chemicals, NBR is widely used in automotive and industrial applications. It offers good mechanical properties and is suitable for temperatures ranging from -40°C to 120°C.
2. Ethylene Propylene Diene Monomer (EPDM): EPDM is highly resistant to weathering, ozone, and UV exposure, making it ideal for outdoor applications. It also resists water, steam, and some chemicals, and functions well in temperatures from -50°C to 150°C.
3. Silicone Rubber: Silicone gaskets can withstand extreme temperatures, from -60°C to 250°C, making them suitable for high-temperature applications. They are also resistant to ozone, UV light, and some chemicals, and are commonly used in the food and medical industries due to their non-toxic properties.
4. Fluoroelastomer (FKM): FKM, such as Viton, is known for its excellent chemical resistance, especially to fuels, oils, and solvents. It performs well in high-temperature environments, up to 250°C, and is often used in automotive, aerospace, and chemical processing industries.
5. Neoprene (CR): Neoprene offers good resistance to oils, chemicals, and weathering. It is versatile, with moderate mechanical properties and temperature resistance ranging from -40°C to 120°C. Neoprene is used in a variety of applications, including automotive and refrigeration.
6. Natural Rubber (NR): Natural rubber provides excellent elasticity and abrasion resistance. It is suitable for applications requiring high tensile strength and flexibility, though it has limited chemical and temperature resistance, typically up to 70°C.
Each material has unique properties that make it suitable for specific applications. The choice of gasket material depends on the operating environment, including exposure to chemicals, temperature ranges, and mechanical stresses.
Quality Testing Methods for rubber gasket materials and how to control the quality
Quality Testing Methods for Rubber Gasket Materials:
1. Tensile Strength: Measures the force required to break the rubber, indicating durability. Tested using a tensile testing machine where the material is stretched until it breaks.
2. Hardness: Determines the material’s resistance to indentation, often using a durometer. Ensures the gasket can withstand pressure without deforming.
3. Compression Set: Evaluates the material’s ability to return to its original thickness after prolonged compression. Essential for gaskets to maintain a seal.
4. Elongation at Break: Assesses the rubber’s ability to stretch before breaking. Higher elongation means better flexibility.
5. Aging Tests: Simulate long-term exposure to heat, ozone, or chemicals to predict how the gasket will perform over time. Typically conducted in accelerated aging chambers.
6. Abrasion Resistance: Measures the gasket’s resistance to wear from friction. Conducted using a rotary drum or an abrasion tester.
7. Fluid Resistance: Tests how the rubber reacts to different fluids it might contact in service, ensuring it doesn’t degrade or swell excessively.
8. Thermal Conductivity: Assesses the rubber’s ability to conduct heat, which is crucial for gaskets in high-temperature environments.
Quality Control Measures:
1. Standardization: Use standard test methods (e.g., ASTM, ISO) to ensure consistent results.
2. Batch Testing: Test samples from each production batch to verify they meet specifications.
3. Traceability: Maintain detailed records of material batches, production parameters, and test results for traceability.
4. Inspection: Regularly inspect finished gaskets for defects such as cracks, voids, or inconsistencies.
5. Supplier Certification: Source materials from certified suppliers and periodically audit them for compliance with quality standards.
6. Process Control: Implement strict process controls in manufacturing to ensure consistency, including maintaining proper curing times and temperatures.
These methods and controls help ensure the reliability and performance of rubber gaskets in their intended applications.
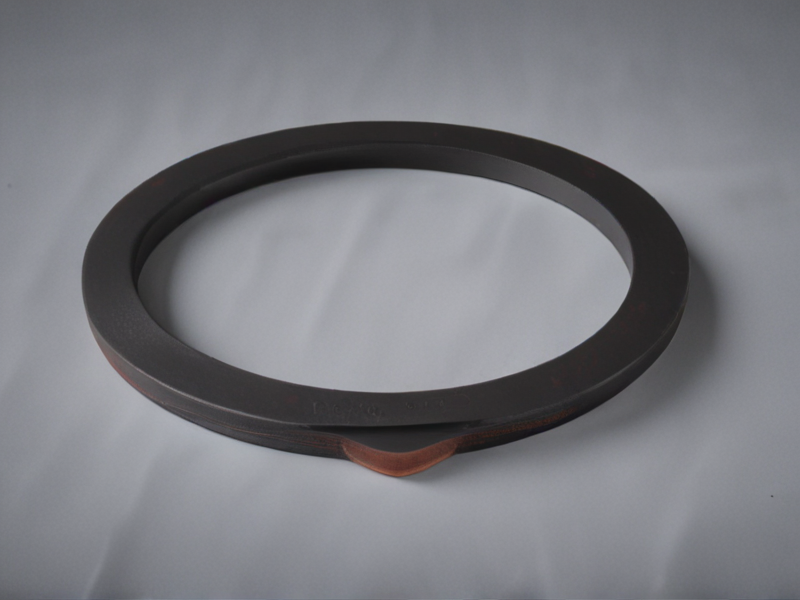
The Work Process and how to use rubber gasket materials
Work Process of Using Rubber Gasket Materials
1. Material Selection:
– Identify Requirements: Determine the operational conditions such as temperature, pressure, and chemical exposure.
– Choose the Right Material: Select a rubber material like EPDM, Nitrile, or Silicone based on the identified requirements.
2. Measurement and Cutting:
– Measure Precisely: Accurately measure the dimensions of the flange or surface where the gasket will be installed.
– Cut to Size: Use a precision cutter or die to cut the gasket material to the required shape and size, ensuring clean and accurate edges.
3. Surface Preparation:
– Clean the Surfaces: Ensure both the gasket and the mating surfaces are clean, dry, and free of any debris, oil, or old gasket material to ensure a good seal.
– Inspect for Damage: Check the mating surfaces for any damage or irregularities that might prevent proper sealing.
4. Installation:
– Align Properly: Position the gasket carefully, ensuring it aligns correctly with the bolt holes and other features of the mating surfaces.
– Tighten Evenly: Gradually tighten bolts or fasteners in a cross-pattern sequence to distribute pressure evenly across the gasket, avoiding over-tightening which can cause deformation.
5. Testing and Adjustment:
– Initial Testing: Conduct a pressure test to ensure there are no leaks. If leaks are detected, slightly adjust the tightness of the bolts.
– Final Inspection: After a short period of operation, re-inspect the gasket to ensure it maintains its seal.
6. Maintenance:
– Regular Checks: Periodically inspect the gasket during routine maintenance to ensure it remains in good condition.
– Replacement: Replace the gasket if signs of wear, such as cracks or compression set, are observed to prevent potential leaks or failures.
Using rubber gasket materials efficiently requires careful material selection, precise cutting, proper surface preparation, and correct installation techniques to ensure a reliable and durable seal. Regular maintenance further ensures the longevity and effectiveness of the gasket.
rubber gasket materials Importing questions including Cost,Supplier,Sample,Certification and Market
Importing rubber gasket materials involves several key considerations:
1. Cost: The cost of rubber gasket materials varies based on the type (e.g., silicone, neoprene, EPDM), quality, and quantity ordered. Typically, the cost per unit decreases with larger orders. Additional costs include shipping, tariffs, and customs duties. It’s crucial to request detailed quotes from multiple suppliers to compare prices effectively.
2. Supplier: Finding reliable suppliers is critical. Start by searching for manufacturers and distributors with a good reputation. Websites like Alibaba, Global Sources, and ThomasNet can help identify potential suppliers. Check for reviews, ask for references, and verify their business credentials.
3. Sample: Before placing a large order, request samples from potential suppliers to assess the material’s quality, durability, and performance. This step ensures the product meets your specifications and standards.
4. Certification: Ensure the materials meet necessary industry standards and certifications, such as ISO 9001 for quality management, RoHS for hazardous substances, and specific certifications for food-grade or medical-grade gaskets if applicable. This guarantees compliance with international regulations and ensures product safety and reliability.
5. Market: Understand the market demand and applications for rubber gaskets in your target region. Analyze trends, competitor offerings, and customer needs to determine the most suitable types of gaskets to import. This knowledge will help in selecting the right materials and planning your marketing strategy.
When importing rubber gasket materials, thorough research and careful planning are essential to ensure cost-effectiveness, quality, and compliance with standards. Building strong relationships with reliable suppliers and understanding market dynamics will support successful import operations.
How to find and select check reliable rubber gasket materials manufacturers in China
Finding and selecting reliable rubber gasket materials manufacturers in China involves several steps:
1. Research and Identify Potential Manufacturers:
– Online Directories: Use platforms like Alibaba, Made-in-China, and Global Sources to find manufacturers.
– Industry Exhibitions: Look for participants in trade fairs such as the China International Rubber Industry Exhibition.
2. Evaluate Manufacturer Profiles:
– Company Information: Check for detailed company profiles, including history, product range, certifications, and production capacity.
– Certifications: Look for ISO certifications and compliance with international standards.
3. Assess Product Quality:
– Samples: Request samples to evaluate the quality of materials.
– Technical Specifications: Ensure the products meet your technical requirements and industry standards.
4. Check References and Reviews:
– Customer Feedback: Look for reviews and testimonials from other buyers.
– References: Ask the manufacturer for references to contact past clients.
5. Conduct Factory Audits:
– Site Visits: If possible, visit the factory to assess production facilities, quality control processes, and working conditions.
– Third-Party Audits: Use third-party inspection companies to conduct audits and verify compliance with your standards.
6. Evaluate Communication and Responsiveness:
– Customer Service: Assess their communication skills, responsiveness, and ability to understand your requirements.
– Language Skills: Ensure they can communicate effectively in your preferred language.
7. Review Terms and Conditions:
– Pricing and Payment Terms: Compare quotes and understand payment terms.
– Delivery and Logistics: Ensure they have reliable shipping and logistics arrangements.
By following these steps, you can identify and select a reliable rubber gasket materials manufacturer in China.
Background Research for rubber gasket materials manufacturers Companies in China, use qcc.com archive.org importyeti.com
Several prominent companies in China specialize in manufacturing rubber gasket materials. Noteworthy among them are:
1. ContiTech China – A subsidiary of the German company ContiTech AG, ContiTech China operates multiple facilities and provides a wide range of rubber products, including gaskets. They are well-regarded for their advanced manufacturing capabilities and high-quality materials used in various industries such as automotive and industrial applications.
2. Zhongshan Xiong Bing Rubber Co., Ltd. – Located in Guangdong Province, this company has been in the rubber industry since 2001. They focus on producing various rubber products, including gaskets. Known for their robust production capacity, they cater to both domestic and international markets.
3. China National Chemical Rubber Corporation – This large state-owned enterprise, part of ChemChina, is a major player in the rubber products sector. They manufacture a broad range of rubber goods, including high-performance gaskets, and have a significant presence both domestically and internationally.
4. Hangzhou Techwell Rubber Products Co., Ltd. – Based in Zhejiang Province, Techwell specializes in the production of rubber gaskets and sealing materials. They emphasize innovation and quality control, serving a global clientele with products that meet international standards.
5. Jiangyin Haida Rubber and Plastic Co., Ltd. – Operating from Jiangsu Province, Haida focuses on various rubber and plastic products, including gaskets. They have a strong reputation for reliability and precision in their manufacturing processes, catering to industries such as automotive, machinery, and electronics.
These companies demonstrate the diversity and strength of China’s rubber gasket manufacturing industry, providing high-quality products to various sectors worldwide. For more detailed information, you can explore their profiles on platforms like QCC.com.
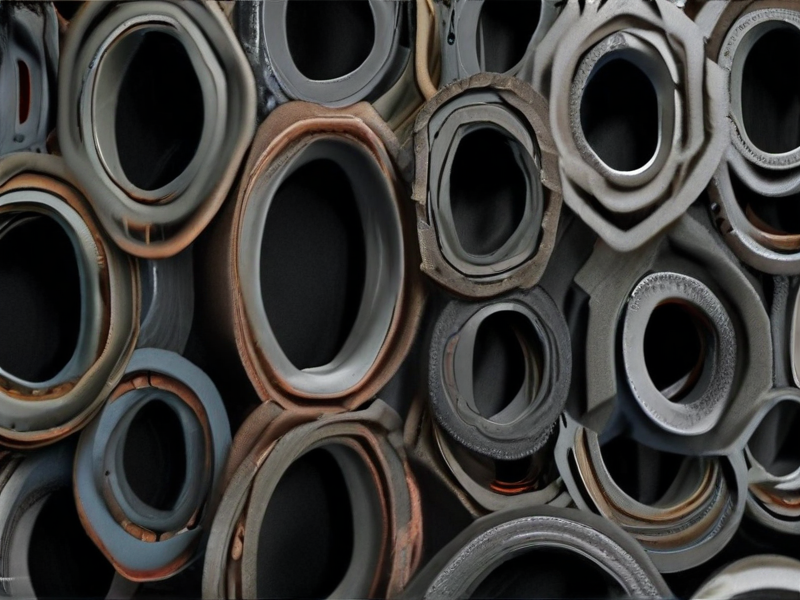
Price Cost Research for rubber gasket materials manufacturers Companies in China, use temu.com and 1688.com
For researching prices and manufacturers of rubber gasket materials in China, both Temu.com and 1688.com provide a range of options:
1. Temu.com: This platform primarily showcases various manufacturers and their offerings for rubber gaskets, including detailed product specifications and prices. Products include different types of rubber gaskets suited for various industrial applications.
2. 1688.com: This site offers a broader range of manufacturers and products, often with detailed listings and competitive pricing. Examples include:
– Ningbo-based O-ring seals: Prices start around ¥0.95 per piece.
– PTFE mold products: Ranging from ¥10 to ¥300 depending on specifications and customization levels.
Key manufacturers include:
– Shanghai Zhixin Mold Technology: Specializes in PTFE molds.
– Yangzhong City Xingfuda Rubber & Plastic Co., Ltd.: Known for high-volume sales and a range of PTFE products.
For detailed pricing and more specific inquiries, it’s beneficial to visit the product pages directly on 1688.com and Temu.com to compare options and contact suppliers for quotes.
Shipping Cost for rubber gasket materials import from China
Shipping costs for importing rubber gasket materials from China depend on several factors, including the mode of transport, shipment volume, weight, distance, and current market conditions. Here are key considerations:
Modes of Transport
1. Air Freight: Faster but more expensive, suitable for urgent or high-value shipments.
2. Sea Freight: Cost-effective for large, heavy shipments but slower, typically taking weeks.
3. Rail and Road Freight: Intermediate option, often used for landlocked regions.
Cost Factors
1. Volume and Weight: Larger and heavier shipments cost more. Shipping companies often use volumetric weight for pricing.
2. Distance: Costs increase with the distance from the shipping port in China to the destination port.
3. Shipping Incoterms: Terms like FOB (Free on Board) or CIF (Cost, Insurance, and Freight) affect which costs (e.g., transportation, insurance) are borne by the buyer or seller.
4. Current Market Rates: Freight rates fluctuate based on demand, fuel prices, and geopolitical factors.
Example Costs
– Air Freight: Generally ranges from $5 to $10 per kilogram for large volumes, but can be higher for smaller, urgent shipments.
– Sea Freight: A 20-foot container from China to the US might cost between $1,000 and $4,000, depending on the port of destination, while a 40-foot container might range from $2,000 to $8,000.
– Additional Fees: Customs duties, insurance, handling, and delivery charges at the destination port.
Recommendations
1. Choose Sea Freight for Large Shipments: More economical for bulk materials.
2. Negotiate Rates: Work with a freight forwarder to get competitive rates.
3. Plan Ahead: Avoid urgent shipments to reduce costs.
Understanding these factors and planning accordingly can help manage and reduce shipping costs effectively.
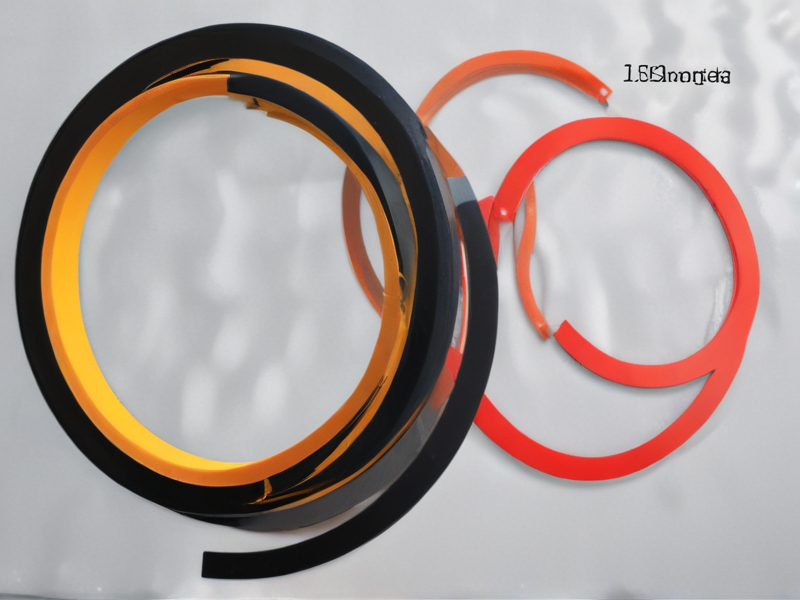
Compare China and Other rubber gasket materials Markets: Products Quality and Price,Visible and Hidden Costs
When comparing rubber gasket materials markets between China and other countries, several factors come into play: product quality, price, visible costs, and hidden costs.
Product Quality
Chinese rubber gaskets often emphasize cost-effectiveness. Quality varies widely, with high-end manufacturers providing competitive products, while lower-end suppliers may offer inferior quality. Other markets, especially in Europe and North America, typically maintain stringent quality controls and standards, ensuring more consistent and higher-quality products.
Price
Chinese gaskets are generally more affordable due to lower labor and production costs. This makes them attractive for cost-sensitive applications. In contrast, gaskets from Europe or North America tend to be more expensive, reflecting higher labor costs and adherence to strict quality standards.
Visible Costs
Visible costs include the purchase price and shipping fees. Chinese products usually have lower purchase prices but might incur higher shipping costs depending on the destination. Conversely, gaskets from local or regional suppliers in Europe and North America might have higher upfront costs but lower shipping expenses for local buyers.
Hidden Costs
Hidden costs encompass aspects like reliability, maintenance, and potential downtime. Lower-quality gaskets from some Chinese suppliers may lead to higher maintenance costs and more frequent replacements, increasing overall lifecycle costs. Conversely, higher-quality gaskets from Europe or North America might entail higher initial costs but offer better durability and performance, reducing long-term expenses.
Conclusion
Choosing between Chinese and other rubber gasket materials depends on specific needs. If initial cost savings are crucial and quality can be managed through careful supplier selection, Chinese gaskets are advantageous. However, for applications where long-term reliability and lower hidden costs are essential, gaskets from Europe or North America may provide better value despite higher upfront prices.
Custom Private Labeling and Branding Opportunities with Chinese rubber gasket materials Manufacturers
Custom private labeling and branding with Chinese rubber gasket materials manufacturers offer numerous opportunities for businesses looking to enhance their product offerings. Here are some key aspects to consider:
1. Diverse Material Options: Chinese manufacturers provide a wide range of rubber materials, including EPDM, silicone, nitrile, and more. This variety allows businesses to choose materials that best fit their product specifications and market demands.
2. Customization: These manufacturers often offer extensive customization options. You can specify dimensions, shapes, and properties tailored to your products. This level of customization ensures that the gaskets meet the exact requirements of your applications.
3. Branding: Private labeling enables businesses to brand the gaskets with their own logos and packaging designs. This enhances brand visibility and consistency across your product range, reinforcing brand identity in the market.
4. Quality Assurance: Many Chinese manufacturers are certified to international standards such as ISO and RoHS. This ensures that the products meet high-quality benchmarks, which is crucial for maintaining customer trust and satisfaction.
5. Cost Efficiency: China is known for its cost-effective manufacturing processes. By sourcing from Chinese manufacturers, businesses can benefit from competitive pricing without compromising on quality. This is particularly advantageous for bulk orders, leading to better profit margins.
6. Supply Chain Management: Partnering with Chinese manufacturers can streamline your supply chain. Many manufacturers offer integrated services, including production, quality control, and logistics, ensuring timely delivery and reducing the complexities associated with international shipping.
7. Technical Support and Expertise: Many Chinese manufacturers have experienced R&D teams that can provide technical support and advice on product development. This collaboration can lead to innovative solutions and improvements in your product offerings.
By leveraging these opportunities, businesses can effectively enhance their product portfolios, ensure high-quality standards, and maintain competitive pricing, all while strengthening their brand presence in the market.
Tips for Procurement and Considerations when Purchasing rubber gasket materials
When procuring rubber gasket materials, consider these essential tips and factors to ensure optimal performance and cost-effectiveness:
Tips for Procurement
1. Understand Requirements: Clearly define the operational conditions, such as temperature, pressure, and chemical exposure. This helps in selecting the right material.
2. Material Selection: Choose materials based on their properties. Common materials include:
– EPDM: Excellent for weather, ozone, and UV resistance. Suitable for outdoor applications.
– Nitrile (Buna-N): Good for oil and fuel resistance. Ideal for automotive and industrial applications.
– Silicone: Great for high-temperature resistance but not suitable for high-pressure applications.
– Viton: High chemical resistance and temperature stability. Used in chemical and aerospace industries.
3. Compliance and Standards: Ensure materials comply with relevant standards (e.g., ASTM, ISO) and industry regulations.
4. Supplier Evaluation: Assess suppliers for quality, reliability, and compliance with specifications. Consider factors like lead times, flexibility, and after-sales support.
5. Cost-Benefit Analysis: Balance quality and cost. Higher initial costs for premium materials can lead to longer-term savings through durability and reduced maintenance.
6. Testing and Validation: Perform testing under actual operating conditions to validate performance before full-scale procurement.
7. Logistics and Storage: Ensure proper storage conditions to maintain material integrity. Avoid exposure to extreme temperatures and direct sunlight.
Considerations when Purchasing
1. Environmental Conditions: Consider exposure to chemicals, oils, UV light, and extreme temperatures. Select materials that withstand these conditions.
2. Mechanical Properties: Evaluate properties like tensile strength, elongation, and hardness to match application demands.
3. Aging and Degradation: Assess the material’s resistance to aging, ozone, and weathering to ensure long-term performance.
4. Compatibility: Ensure the gasket material is compatible with the fluids and surfaces it will contact.
5. Thickness and Size: Choose the appropriate thickness and dimensions to ensure a proper seal without excessive compression.
6. Lifecycle and Maintenance: Consider the expected lifespan and ease of maintenance. High-quality materials might reduce the frequency of replacements and downtime.
By considering these factors, you can make informed decisions that ensure the longevity and effectiveness of your rubber gaskets.
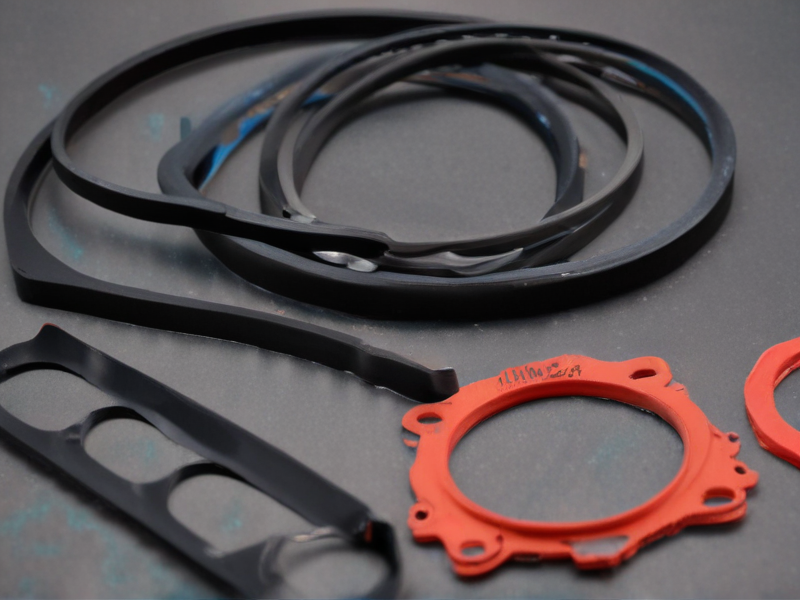
FAQs on Sourcing and Manufacturing rubber gasket materials in China
FAQs on Sourcing and Manufacturing Rubber Gasket Materials in China
1. Why source rubber gasket materials from China?
China offers competitive pricing, a vast range of materials, and extensive manufacturing capabilities. Many suppliers have significant experience in producing high-quality rubber gaskets for various industries.
2. What types of rubber gasket materials are available?
Common materials include Nitrile (NBR), EPDM, Silicone, Neoprene (CR), Viton (FKM), and Natural Rubber. Each type has unique properties suitable for different applications.
3. How do I find reliable suppliers?
Utilize online platforms like Alibaba, Global Sources, and Made-in-China. Verify suppliers by checking certifications, visiting their facilities, and requesting samples. Engage with trade organizations and attend trade shows.
4. What certifications should suppliers have?
Look for ISO 9001 for quality management, ISO 14001 for environmental management, and specific industry certifications like TS 16949 for automotive parts.
5. What are the key quality considerations?
Ensure the material meets your specifications for hardness, tensile strength, elongation, and temperature resistance. Request material data sheets and test reports.
6. Can suppliers assist with custom designs?
Many Chinese manufacturers offer custom design and tooling services. Provide detailed drawings and specifications to get accurate quotations and prototypes.
7. What are typical lead times?
Lead times vary depending on order complexity and volume but generally range from 2 to 6 weeks. Custom orders may take longer.
8. How is pricing determined?
Pricing depends on material type, order volume, complexity, and additional services like tooling or custom packaging. Request multiple quotes for comparison.
9. What are the common payment terms?
Payment terms often include a 30% deposit with the balance paid before shipment. Payment methods include T/T (Telegraphic Transfer), L/C (Letter of Credit), and sometimes PayPal for smaller orders.
10. What should I know about shipping and logistics?
Factor in shipping costs and times. Utilize freight forwarders for efficient logistics and ensure proper packaging to protect goods during transit.