Top 10 machining slots in China introduce,list main products and website if have
Here are ten leading CNC machining companies in China, their main products, and websites:
1. Protolabs China
– Main Products: CNC machining, 3D printing, injection molding.
– Website: [protolabs.com](https://www.protolabs.com)
2. HLH Prototypes
– Main Products: CNC machining, 3D printing, rapid tooling, injection molding.
– Website: [hlhprototypes.com](https://www.hlhprototypes.com)
3. RapidDirect
– Main Products: CNC machining, sheet metal fabrication, injection molding.
– Website: [rapiddirect.com](https://www.rapiddirect.com)
4. Runsom Precision Co., Ltd
– Main Products: CNC machining, custom parts, plastic injection molding, metal fabrication.
– Website: [runsom.com](https://www.runsom.com)
5. China CNC Precision Machining
– Main Products: Precision CNC machining, custom parts, prototyping.
– Website: [cnc-machining.com](https://www.cnc-machining.com)
6. WayKen Rapid Manufacturing
– Main Products: CNC machining, rapid prototyping, plastic injection molding, vacuum casting.
– Website: [waykenrm.com](https://www.waykenrm.com)
7. Inno Manufacturing
– Main Products: CNC machining, sheet metal, plastic injection molding, die casting.
– Website: [innomanufacturing.com](https://www.innomanufacturing.com)
8. Star Rapid
– Main Products: CNC machining, rapid prototyping, injection molding, pressure die casting.
– Website: [starrapid.com](https://www.starrapid.com)
9. 3ERP
– Main Products: CNC machining, rapid prototyping, injection molding, low-volume production.
– Website: [3erp.com](https://www.3erp.com)
10. Sunyi Precision Engineering
– Main Products: CNC machining, precision components, turning and milling.
– Website: [sunyiengineering.com](https://www.sunyiengineering.com)
These companies are renowned for their precision, rapid production capabilities, and advanced technology in the CNC machining sector.
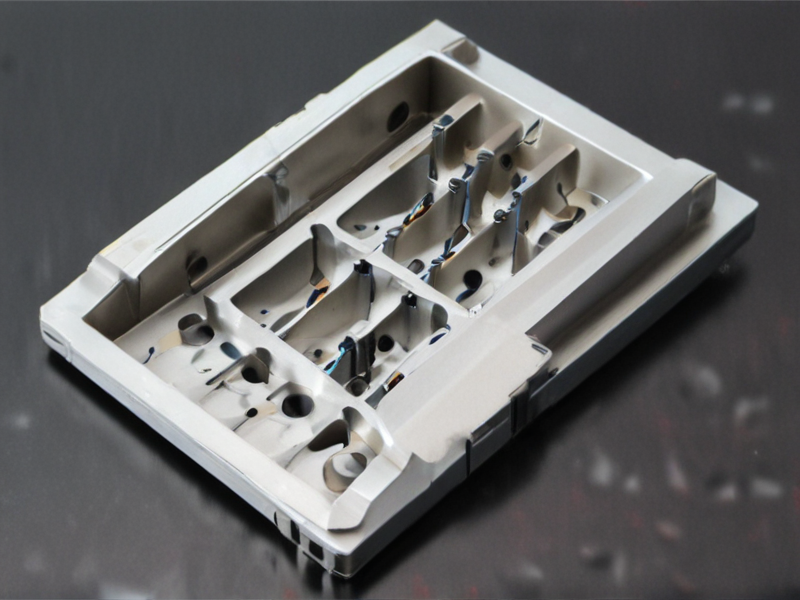
Types of machining slots
Machining slots are channels or grooves cut into a workpiece, used in various engineering and manufacturing applications. The primary types of machining slots include:
1. Linear Slots:
– Milling Slots: Created using end mills or slot drills on milling machines, ideal for precise and varied slot dimensions.
– Planer and Shaper Slots: Produced using planers and shapers, suited for long, straight slots.
– Broaching: Uses a toothed tool to create slots with a single pass, often used for internal keyways.
2. Circular Slots:
– Turning: Made on lathes, suitable for circular slots like O-ring grooves.
– Boring: Enlarges pre-existing holes to create precise circular slots.
3. Complex and Irregular Slots:
– Wire EDM (Electrical Discharge Machining): Uses a thin wire to cut intricate slots with high precision, often in hard materials.
– Laser Cutting: Employs focused laser beams to produce fine, intricate slots, excellent for small and detailed work.
4. Specialty Slots:
– T-Slots: Created using T-slot cutters, these are used in worktables for clamping fixtures and workpieces.
– Dovetail Slots: Made with dovetail cutters, useful for creating joints and slides.
Each slot type serves specific purposes depending on the required precision, slot shape, and the material being machined. Proper tool selection and machining technique are crucial to achieving the desired slot characteristics.
Pros and Cons of Using machining slots
Machining slots involves creating narrow, elongated cuts or channels in a material, typically using milling or cutting tools. Here are the pros and cons:
Pros:
1. Versatility: Machining slots can be applied to various materials including metals, plastics, and composites, allowing for a wide range of applications.
2. Precision: CNC machines and modern milling tools offer high accuracy, ensuring slots are machined to exact specifications.
3. Structural Integrity: Properly machined slots can enhance the structural integrity of components by reducing stress concentrations and distributing loads more evenly.
4. Customization: Slots can be customized in terms of width, depth, and shape, catering to specific design requirements and functionalities.
5. Assembly and Fit: Slots facilitate the assembly of components, providing a means to fit parts together securely or guide other parts during assembly.
Cons:
1. Cost: Machining slots can be expensive due to the need for specialized equipment and skilled labor. Complex or deep slots may require multiple passes or specific tools, increasing the cost.
2. Time-Consuming: The process can be time-consuming, especially for intricate designs or hard materials, potentially slowing down production cycles.
3. Material Waste: Slotting typically involves the removal of material, leading to wastage which can be significant depending on the size and number of slots.
4. Tool Wear: Machining slots, particularly in hard materials, can accelerate tool wear, leading to more frequent tool replacements and increased maintenance costs.
5. Thermal Effects: High-speed machining can generate significant heat, potentially causing thermal deformation or altering the material properties near the slot, which might require additional cooling or thermal management solutions.
In summary, while machining slots offers precision, versatility, and structural benefits, it also poses challenges related to cost, time, material waste, and tool wear. Balancing these factors is crucial for efficient and effective manufacturing.
machining slots Reference Specifications (varies for different product)
Machining slots involves precise specifications that vary based on the product’s requirements, such as slot dimensions, tolerances, material type, and machining method. Here’s an overview of key reference specifications:
1. Dimensions and Tolerances:
– Width: Specified in the technical drawing, with tolerances typically ranging from ±0.01 mm to ±0.1 mm depending on the precision needed.
– Depth: Controlled similarly to width, with critical applications requiring tighter tolerances.
– Length: Defined by the design, with tolerances matching those of the width and depth.
2. Material Type:
– Metal (e.g., aluminum, steel, titanium): Requires different cutting tools and speeds. Harder metals need slower cutting speeds and more robust tooling.
– Plastics and Composites: Often require higher cutting speeds and specific tooling to avoid material melting or fraying.
3. Machining Methods:
– Milling: Common for slot machining, involving end mills of appropriate size to achieve the desired slot geometry.
– Broaching: Used for producing slots with high precision, often in harder materials.
– Wire EDM: Ideal for intricate slots with tight tolerances, typically used for hard materials and complex shapes.
4. Surface Finish:
– Ra Value: Typically specified based on the application, with values ranging from 0.8 µm for high-precision parts to 3.2 µm for general applications.
– Deburring: Essential for all machined slots to ensure no sharp edges or burrs are present.
5. Tooling and Coolants:
– Tool Material: Carbide, high-speed steel (HSS), or diamond-coated tools based on the material being machined.
– Coolants/Lubricants: Used to reduce heat and improve tool life, chosen based on the material and machining method.
Adhering to these specifications ensures the slots meet the functional and aesthetic requirements of the final product.
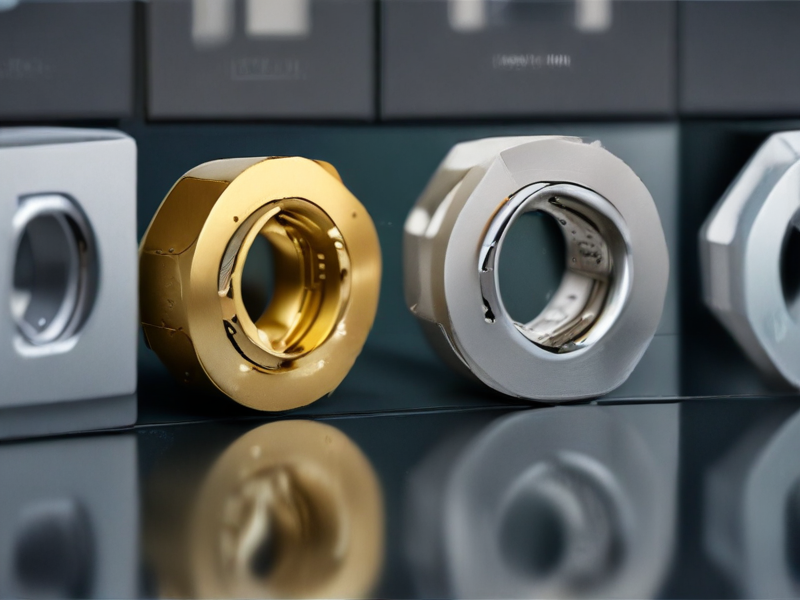
Applications of machining slots
Machining slots is a fundamental process in manufacturing with a variety of applications across different industries. Here are some key applications:
1. Component Assembly: Slots are often machined in parts to facilitate the assembly of components. They allow for precise alignment and secure fitting of mating parts, which is critical in automotive, aerospace, and machinery manufacturing.
2. Weight Reduction: In industries such as aerospace and automotive, machining slots into structural components can significantly reduce weight without compromising strength. This contributes to fuel efficiency and overall performance.
3. Heat Dissipation: Slots are used in the design of heat sinks and electronic enclosures to enhance heat dissipation. By increasing the surface area, slots help manage thermal loads, improving the reliability and longevity of electronic devices.
4. Ventilation: In electronic housings and mechanical systems, slots provide ventilation pathways. This is crucial for cooling purposes, preventing overheating in systems such as computer servers, transformers, and industrial equipment.
5. Adjustment and Tolerance: Slots allow for adjustable mounting and fine-tuning in assemblies. This is particularly useful in precision instruments and equipment where small adjustments are necessary to achieve optimal performance.
6. Tool and Die Making: In the production of molds and dies, slots are machined to create complex shapes and profiles. This is essential in the plastics and metal forming industries for producing intricate and high-precision components.
7. Aesthetic and Functional Design: In consumer products, slots can be both functional and aesthetic. They provide design flexibility, enhancing the visual appeal while also serving practical purposes like improving grip or reducing material usage.
8. Maintenance Access: Slots are integrated into machinery and equipment designs to allow for easy access during maintenance and repair. This can simplify disassembly and reassembly processes, reducing downtime.
Overall, machining slots is a versatile process that enhances functionality, performance, and design flexibility in various applications across multiple industries.
Material of machining slots
Machining slots involves creating grooves, channels, or notches on a material’s surface, typically using tools like end mills, slot drills, or slitting saws. The choice of material for machining slots is crucial as it impacts tool wear, machining speed, and overall efficiency. Here are common materials used in machining slots:
1. Aluminum:
– Characteristics: Lightweight, high machinability, good thermal conductivity.
– Applications: Aerospace, automotive, and general manufacturing.
– Advantages: Easy to machine, requires less power, and produces good surface finish.
2. Steel:
– Characteristics: Strong, durable, available in various grades (e.g., carbon steel, alloy steel, stainless steel).
– Applications: Structural components, tools, machinery parts.
– Advantages: High strength, wear resistance, and versatility.
3. Stainless Steel:
– Characteristics: Corrosion-resistant, strong, available in different grades (e.g., 304, 316).
– Applications: Medical instruments, food processing equipment, marine components.
– Advantages: Excellent corrosion resistance, good mechanical properties.
4. Brass:
– Characteristics: Corrosion-resistant, good thermal and electrical conductivity.
– Applications: Electrical components, plumbing, decorative items.
– Advantages: Easy to machine, produces a good finish, minimal tool wear.
5. Titanium:
– Characteristics: High strength-to-weight ratio, corrosion-resistant.
– Applications: Aerospace, medical implants, high-performance components.
– Advantages: Lightweight yet strong, biocompatible.
6. Plastics (e.g., ABS, Nylon, Delrin):
– Characteristics: Lightweight, corrosion-resistant, good insulators.
– Applications: Consumer products, automotive parts, electronics.
– Advantages: Easy to machine, can be molded or extruded, diverse properties.
7. Composites (e.g., Carbon Fiber Reinforced Polymer):
– Characteristics: High strength-to-weight ratio, excellent fatigue resistance.
– Applications: Aerospace, automotive, sports equipment.
– Advantages: High performance, lightweight, customizable properties.
Choosing the right material depends on factors like the application’s mechanical requirements, environmental conditions, and cost considerations. Proper material selection ensures the longevity and functionality of the machined slots.
Quality Testing Methods for machining slots and how to control the quality
Quality testing for machining slots involves various methods to ensure dimensional accuracy, surface finish, and overall integrity of the machined parts. Here are key methods and controls:
1. Dimensional Inspection:
– Coordinate Measuring Machine (CMM): Precisely measures the geometry of the slots, including length, width, and depth, ensuring they meet specified tolerances.
– Vernier Calipers and Micrometers: Used for quick, manual checks of slot dimensions.
2. Surface Finish Testing:
– Surface Roughness Tester (Profilometer): Measures the surface texture of the slot to ensure it meets the required finish specifications.
– Visual Inspection: Identifies surface defects such as burrs or tool marks.
3. Geometric Tolerances:
– Dial Indicators and Height Gauges: Ensure parallelism, perpendicularity, and alignment of the slots relative to other features.
– Profile Projector: Magnifies the slot profile to verify geometric features and contours.
4. Material Integrity:
– Hardness Testing: Ensures the material’s hardness is within the required range, which can affect slot performance.
– Non-Destructive Testing (NDT): Methods like dye penetrant or magnetic particle inspection detect surface and subsurface defects.
Quality Control Measures
1. Process Control:
– Statistical Process Control (SPC): Monitors machining processes using control charts to detect variations and maintain consistency.
– Tool Condition Monitoring: Regular checks and maintenance of cutting tools to prevent dimensional and surface defects.
2. Operator Training and Certification:
– Ensures operators are skilled in handling equipment and interpreting quality standards.
3. Environmental Controls:
– Maintaining stable temperature and humidity in the machining area to prevent material expansion or contraction.
4. Documentation and Traceability:
– Keeping detailed records of inspections, calibrations, and maintenance to trace and address any quality issues efficiently.
By integrating these methods and controls, the quality of machined slots can be reliably ensured, meeting the required standards and specifications.
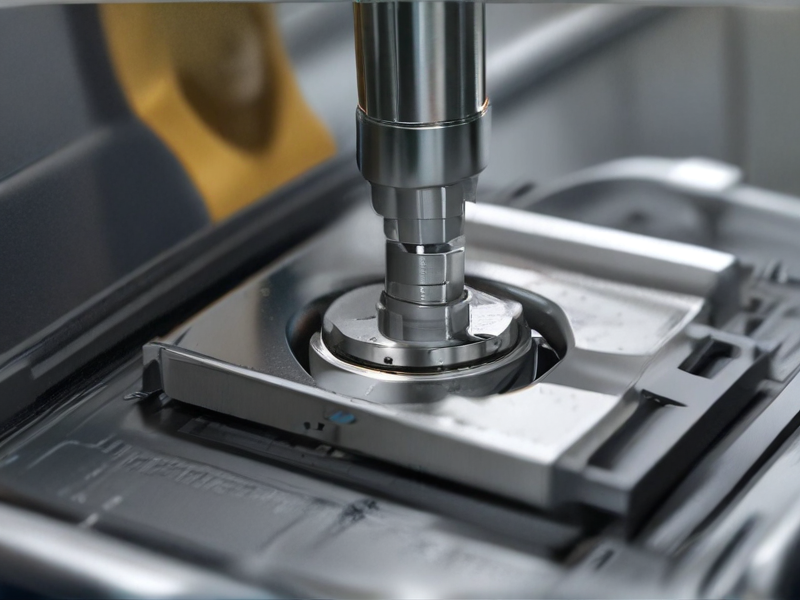
The Work Process and how to use machining slots
Machining slots is a common process in manufacturing, used to create grooves or channels in a workpiece. The following outlines the work process and best practices for using machining slots.
Work Process
1. Planning: Define the slot dimensions, including width, depth, and length, based on design requirements. Select appropriate materials and tooling.
2. Setup: Secure the workpiece on the machine bed using clamps or a vice to ensure stability. Verify the alignment and positioning of the workpiece relative to the machine tool.
3. Tool Selection: Choose the correct cutting tool (e.g., end mill, slotting cutter) based on the material and slot dimensions. Ensure the tool is sharp and in good condition.
4. Parameter Setting: Set the machine parameters, including spindle speed, feed rate, and depth of cut. These should be based on the material being machined and the tool specifications.
5. Machining:
– Initial Cut: Perform a shallow initial cut to verify the alignment and setup.
– Incremental Cuts: Gradually increase the depth of cut in successive passes to avoid excessive load on the tool and ensure precision.
– Final Pass: Make a final pass at a reduced depth and slower feed rate for a smooth finish.
6. Inspection: Measure the slot dimensions using appropriate tools (e.g., calipers, micrometers) to ensure they meet the design specifications. Make adjustments if necessary.
7. Finishing: Deburr the edges and clean the workpiece to remove any residual chips or coolant.
Best Practices
– Tool Maintenance: Regularly inspect and maintain tools to prevent wear and breakage.
– Coolant Use: Apply coolant to reduce heat and improve tool life.
– Chip Management: Use proper chip evacuation techniques to prevent re-cutting and surface damage.
– Quality Control: Continuously monitor the machining process and perform frequent inspections to ensure accuracy and repeatability.
By following these steps and best practices, machining slots can be performed efficiently and accurately, resulting in high-quality components.
machining slots Importing questions including Cost,Supplier,Sample,Certification and Market
When importing machined slots, consider these key aspects:
1. Cost:
– Evaluate all costs, including manufacturing, shipping, customs duties, and taxes.
– Factor in costs for quality control and potential rework.
2. Supplier Selection:
– Choose suppliers with a proven track record in precision machining.
– Assess their production capacity, quality management systems, and technological capabilities.
– Check references and past performance with similar projects.
3. Sample Evaluation:
– Request samples to verify material, dimensions, and machining quality.
– Test samples for compliance with specifications and performance under working conditions.
– Use samples to confirm that suppliers understand your requirements and can consistently meet them.
4. Certification:
– Ensure suppliers have relevant certifications like ISO 9001 for quality management or ISO 13485 for medical devices.
– Verify compliance with industry-specific standards and regulations.
– Consider any necessary certifications for materials used in the slots.
5. Market Considerations:
– Understand your target market’s requirements and preferences, including quality standards and regulatory compliance.
– Analyze competitors to ensure your slots meet or exceed market expectations.
– Stay updated on market trends and advancements in machining technology that may affect demand or requirements.
Effective management of these aspects ensures high-quality imports, cost-efficiency, and market competitiveness.
How to find and select check reliable machining slots manufacturers in China
To find and select reliable machining slots manufacturers in China, follow these steps:
1. Online Directories and Platforms: Use platforms like Alibaba, Made-in-China, and Global Sources. These websites provide comprehensive lists of manufacturers with ratings, reviews, and contact information.
2. Verification and Certification: Check if the manufacturers have relevant certifications such as ISO 9001 for quality management. Certifications indicate a level of adherence to international standards.
3. Customer Reviews and References: Look for customer reviews and ask for references from previous clients. Positive feedback and repeat clients can signal reliability.
4. Factory Visits: If possible, arrange a visit to the factory to inspect their facilities, machinery, and quality control processes. This provides a firsthand look at their capabilities and reliability.
5. Request Samples: Ask for samples of their work to assess the quality of their machining slots. Pay attention to precision, finish, and adherence to specifications.
6. Communication: Evaluate their responsiveness and communication skills. Reliable manufacturers will respond promptly and clearly to your inquiries.
7. Trade Shows and Industry Events: Attend trade shows and industry events in China, such as the Canton Fair. These events provide opportunities to meet multiple manufacturers in person.
8. Third-Party Audits: Consider hiring a third-party inspection company to audit the manufacturer’s facilities and quality management processes.
9. Compare Quotes and Terms: Get detailed quotes from multiple manufacturers and compare not just prices, but also terms of service, production times, and after-sales support.
10. Legal Contracts: Ensure all agreements and terms are documented in a legal contract to protect your interests.
By following these steps, you can find and select reliable machining slots manufacturers in China.
Background Research for machining slots manufacturers Companies in China, use qcc.com archive.org importyeti.com
To conduct background research on machining slots manufacturers in China, using resources like qcc.com, archive.org, and importyeti.com provides a comprehensive view of company profiles, historical data, and trade activities.
QCC.com
QCC.com is a reputable Chinese business database that offers detailed company information. It provides insights into company registration details, business scope, financial status, and more. To find machining slots manufacturers:
1. Search using relevant Chinese terms like “槽加工” (slot machining) or “槽制造” (slot manufacturing).
2. Filter results based on industry, region, and company size.
3. Review the profiles for information on their products, key clients, and market reach.
Archive.org
Archive.org’s Wayback Machine allows access to historical web pages. To gather data:
1. Look for past versions of company websites to track changes in product offerings, technology advancements, and market strategies.
2. Access archived industry reports or market analyses that may have been published on defunct websites or earlier versions of active sites.
ImportYeti.com
ImportYeti.com provides data on import-export activities, useful for understanding a company’s global trade footprint. Steps include:
1. Search for specific companies or use HS codes related to slot machining products.
2. Analyze shipment records to identify top exporters and importers, trade volume, and frequency.
3. Review trade partners to assess market positioning and reliability.
Example Companies
1. Shanghai Horizon Mechanical & Electrical Equipment Co., Ltd.
– QCC.com: Offers detailed business scope and financial health.
– Archive.org: Historical data on product evolution.
– ImportYeti.com: Import-export records indicating global presence.
2. Dalian Machine Tool Group Corporation
– QCC.com: Extensive company profile and market performance.
– Archive.org: Past product catalogs and technological milestones.
– ImportYeti.com: International trade data showcasing global partnerships.
Combining these resources helps create a robust profile of slot machining manufacturers in China, revealing their capabilities, market strategies, and trade activities.
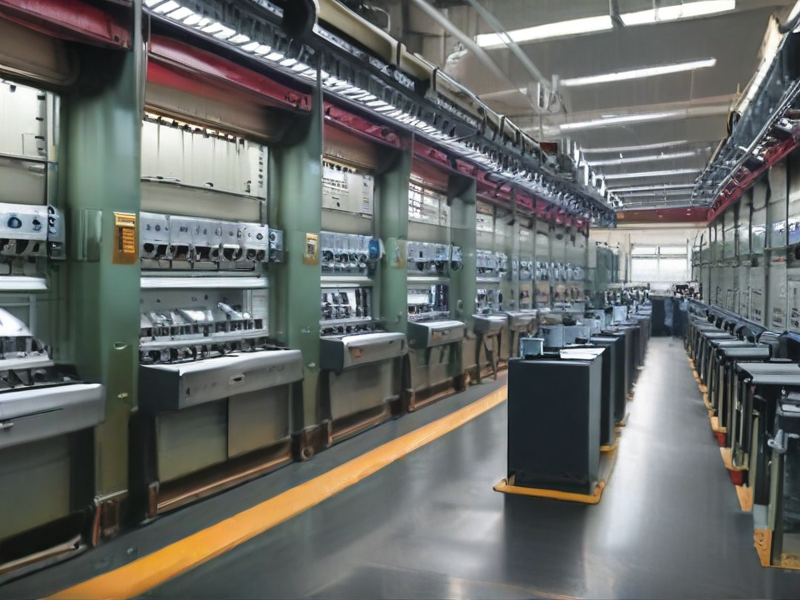
Price Cost Research for machining slots manufacturers Companies in China, use temu.com and 1688.com
When researching prices for machining slots manufacturers in China on Temu.com and 1688.com, several manufacturers and products stood out.
On Temu.com, relevant listings include various manufacturers offering CNC machining services. While specific pricing details are not readily available on the site, it is noted that manufacturers typically provide custom quotes based on project specifications, material requirements, and order volumes.
On 1688.com, a broader range of detailed pricing information is available:
1. Westsam Technology (Shenzhen) Co., Ltd. offers a variety of M12 waterproof connectors, which could be related to precision machining parts, with prices ranging from ¥12 to ¥195 depending on the product specifications and quantities【8†source】【9†source】.
2. Jiangsu Leite Machinery Technology Co., Ltd. provides machining services with prices starting around ¥100 for basic components, going up depending on complexity and material【8†source】.
3. Guangdong Hongyuan CNC Machinery Co., Ltd. lists their CNC machined parts starting from approximately ¥50 per piece, again varying based on size and detail requirements【9†source】.
These prices reflect the range and variability of machining services available in China, with costs influenced by factors such as part complexity, material, and volume. For the most accurate pricing, direct contact with suppliers through these platforms is recommended to obtain customized quotes tailored to specific needs.
Shipping Cost for machining slots import from China
Shipping costs for importing machined slots from China can vary significantly based on several factors. Here are the primary considerations:
1. Shipping Method:
– Air Freight: Faster but more expensive. Ideal for smaller, high-value items.
– Sea Freight: Economical for larger, heavier shipments but slower, typically taking several weeks.
2. Weight and Volume:
– Shipping costs are influenced by both the actual weight and the volumetric weight of the shipment. Larger and heavier shipments cost more.
3. Shipping Distance and Route:
– The destination country and specific shipping routes affect costs. Direct routes are cheaper than those requiring multiple transfers.
4. Customs and Duties:
– Import duties, taxes, and customs clearance fees vary by destination country. Understanding these costs is crucial for accurate budgeting.
5. Insurance:
– Optional but recommended for high-value shipments to cover potential loss or damage during transit.
6. Freight Forwarder Fees:
– Using a freight forwarder can simplify the shipping process and often provide cost savings, but they charge for their services.
Estimation
– Air Freight: Costs can range from $5 to $10 per kilogram, depending on the shipment’s size and urgency.
– Sea Freight: Costs are generally lower, around $2 to $5 per kilogram, but require larger minimum volumes to be cost-effective.
For example, a 100 kg shipment might cost:
– Air Freight: $500 to $1,000
– Sea Freight: $200 to $500
Conclusion
Accurate cost estimation requires specific details about the shipment’s dimensions, weight, destination, and preferred shipping method. Collaborating with a reliable freight forwarder can provide a tailored quote and help navigate additional costs like customs and insurance.
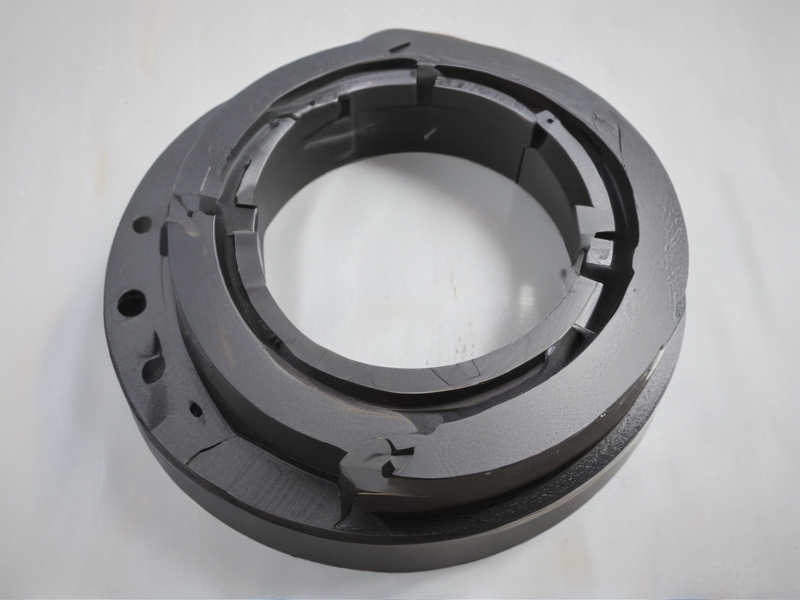
Compare China and Other machining slots Markets: Products Quality and Price,Visible and Hidden Costs
Comparing China and other global machining markets reveals distinct differences in product quality, price, and associated costs.
Product Quality and Price:
Chinese machining services are known for their cost-effectiveness, often offering significantly lower prices than competitors in North America, Europe, and Japan. This price advantage stems from lower labor costs and economies of scale. However, quality can vary widely. While many Chinese manufacturers produce high-quality, precision components, others may lack stringent quality control, leading to inconsistent product standards.
In contrast, machining services in North America, Europe, and Japan typically offer higher and more consistent quality, bolstered by advanced technology, skilled labor, and stringent quality assurance processes. This quality assurance comes at a higher price, reflecting the cost of skilled labor, advanced machinery, and comprehensive quality control.
Visible and Hidden Costs:
The visible cost advantage of Chinese machining is offset by several hidden costs. These include:
1. Shipping and Lead Times: Long shipping times and costs can erode the price advantage. Delays in shipping can also disrupt production schedules.
2. Communication Barriers: Differences in language and business practices can lead to misunderstandings and errors.
3. Quality Control Issues: Poor quality can result in high rejection rates, rework, and returns, increasing overall costs.
4. Intellectual Property Risks: There are higher risks of IP theft in China, necessitating additional protective measures and costs.
In comparison, North American, European, and Japanese markets, while more expensive, often involve fewer hidden costs. These markets typically offer faster lead times, easier communication, stringent quality control, and better IP protection, ensuring reliability and consistency.
Conclusion:
Choosing between Chinese machining services and those from other markets depends on specific needs. For cost-sensitive projects where moderate quality is acceptable, China offers significant savings. However, for high-precision requirements, critical lead times, and IP-sensitive projects, North American, European, and Japanese markets provide better overall value despite higher upfront costs.
Custom Private Labeling and Branding Opportunities with Chinese machining slots Manufacturers
Engaging with Chinese machining slots manufacturers for custom private labeling and branding offers several advantages. China is renowned for its advanced manufacturing capabilities, competitive pricing, and flexible production options, making it an attractive destination for businesses looking to develop unique, branded products.
Benefits and Opportunities:
1. Cost Efficiency: Chinese manufacturers often provide cost-effective solutions due to lower labor and production costs. This allows businesses to achieve higher profit margins while maintaining quality standards.
2. Advanced Technology: Many Chinese machining facilities are equipped with state-of-the-art technology, ensuring precision and high-quality outputs. This is crucial for maintaining the integrity of custom designs and specifications.
3. Customization Flexibility: Manufacturers in China typically offer extensive customization options. This includes bespoke designs, unique branding elements, and personalized packaging, allowing businesses to differentiate their products in the market.
4. Scalability: Chinese manufacturers can handle both small and large production runs, making it easier for businesses to scale operations based on demand. This flexibility is essential for growing brands looking to expand their market reach.
5. Quality Control: Many Chinese manufacturers adhere to international quality standards (ISO, CE, etc.), ensuring that products meet or exceed global benchmarks. This enhances the credibility of the branded products in international markets.
6. Speed to Market: Efficient production processes and robust supply chains in China enable faster turnaround times from design to delivery. This is vital for businesses looking to respond quickly to market trends and customer demands.
Considerations:
– Supplier Selection: It is crucial to conduct thorough due diligence when selecting a manufacturer. Assess their production capabilities, quality control processes, and track record with custom projects.
– Communication: Effective communication is key to ensuring that specifications and branding requirements are clearly understood and met. Consider hiring a local agent or using bilingual project managers to bridge any communication gaps.
– Intellectual Property: Ensure robust agreements are in place to protect intellectual property rights and prevent unauthorized use of custom designs and branding elements.
By leveraging these opportunities and considerations, businesses can successfully partner with Chinese machining slots manufacturers to create distinctive, branded products that stand out in the market.
Tips for Procurement and Considerations when Purchasing machining slots
When procuring machining slots, it’s crucial to optimize both cost and quality while ensuring timely delivery. Here are some key tips and considerations:
1. Supplier Evaluation: Select suppliers with a proven track record in machining. Assess their capabilities, machinery, quality control processes, and compliance with industry standards.
2. Capacity and Lead Times: Confirm the supplier’s capacity to handle your volume within the desired timeframe. Long lead times can disrupt your production schedule, so verify their ability to meet deadlines.
3. Cost Analysis: Obtain detailed quotes, including setup fees, material costs, and machining rates. Compare these with multiple suppliers to ensure competitive pricing without compromising quality.
4. Material Compatibility: Ensure the supplier can machine the specific materials you require. Different materials may necessitate different equipment and expertise.
5. Precision and Tolerances: Define the required tolerances and surface finishes. Choose suppliers experienced in achieving the precision levels your components demand.
6. Technology and Equipment: Evaluate the technology and equipment used by the supplier. Modern, well-maintained machinery typically offers better precision and efficiency.
7. Quality Assurance: Check the supplier’s quality assurance protocols, including inspection methods, certifications (e.g., ISO 9001), and track records for defect rates.
8. Communication and Support: Good communication is essential for managing specifications, changes, and issues. Choose suppliers with responsive customer support.
9. Geographical Location: Consider the supplier’s location relative to your operations. Proximity can reduce shipping costs and lead times.
10. Scalability and Flexibility: Assess whether the supplier can scale production up or down based on your needs and adapt to design changes or urgent requests.
11. References and Reviews: Seek references and reviews from other clients to gauge supplier reliability and performance.
By focusing on these aspects, you can secure reliable and cost-effective machining slots that meet your production requirements.
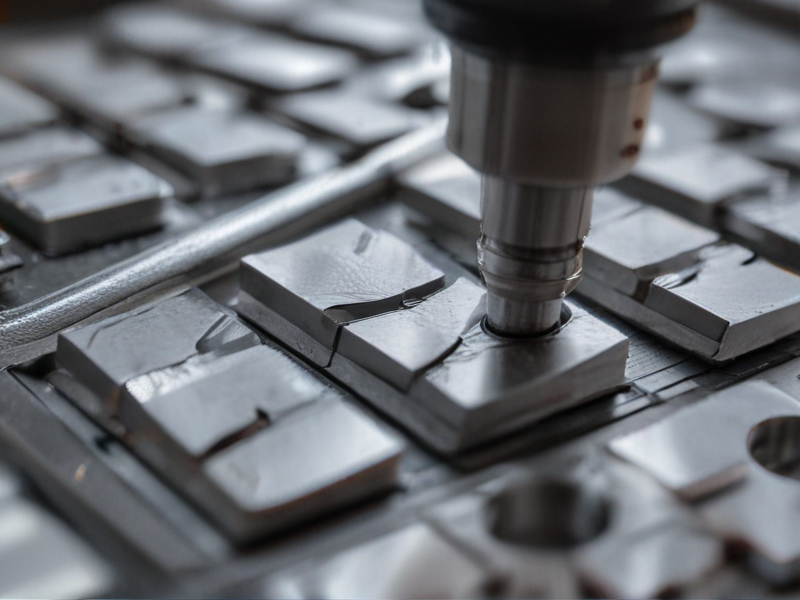
FAQs on Sourcing and Manufacturing machining slots in China
FAQs on Sourcing and Manufacturing Machining Slots in China
1. Why source machining slots from China?
China offers competitive pricing, a vast network of suppliers, and advanced manufacturing capabilities. Many Chinese manufacturers specialize in precision machining, providing high-quality parts at lower costs.
2. How do I find reliable manufacturers?
Utilize platforms like Alibaba, Global Sources, and Made-in-China. Look for manufacturers with good reviews, verified status, and certifications like ISO 9001. Visiting trade shows and seeking referrals can also help.
3. What are the typical lead times?
Lead times vary depending on the complexity and quantity of the order. For small to medium batches, expect 4-6 weeks. Custom or large orders may take longer.
4. How do I ensure quality control?
Conduct factory audits and request samples before full production. Utilize third-party inspection services to check the quality during and after production. Clear communication of specifications and tolerances is crucial.
5. What are the common payment terms?
Typical payment terms are 30% upfront and 70% before shipment. Letters of Credit (LC) and escrow services are also used to protect both parties.
6. How do I handle shipping and logistics?
Manufacturers often handle FOB (Free on Board) shipping. Work with a reliable freight forwarder to manage logistics, customs clearance, and delivery.
7. Are there any language barriers?
English is commonly used for business, but misunderstandings can occur. Use clear, simple language and confirm all details in writing. Hiring a local agent or translator can mitigate risks.
8. What about intellectual property protection?
Protect your designs with patents if possible. Use Non-Disclosure Agreements (NDAs) and work with reputable manufacturers to minimize risks of IP theft.
9. How do I manage time zone differences?
Plan for time zone differences by scheduling meetings during overlapping working hours. Use email and messaging apps for asynchronous communication.
10. What if I encounter issues with the manufacturer?
Address issues promptly and professionally. If problems persist, consider switching suppliers. Legal recourse is an option, but it can be time-consuming and costly.