Top 10 isolation valve in China introduce,list main products and website if have
Here are the top 10 isolation valve manufacturers in China, along with their main products and websites:
1. Chuanyi Automation Co., Ltd.
– Products: Gate valves, globe valves, ball valves, butterfly valves.
– Website: [Chuanyi Automation](http://www.cnasz.com)
2. Neway Valve (Suzhou) Co., Ltd.
– Products: Gate valves, globe valves, check valves, ball valves, butterfly valves, control valves, safety valves.
– Website: [Neway Valve](http://www.newayvalve.com)
3. Jiangsu Suyan Valve Machinery Co., Ltd.
– Products: Gate valves, ball valves, fully welded ball valves.
– Website: [Suyan Valve](http://www.suyangroup.com)
4. Xintai Valve Group Co., Ltd.
– Products: Gate valves, globe valves, check valves, ball valves, butterfly valves.
– Website: [Xintai Valve](http://www.xintaivalves.com)
5. Shanghai Valve Factory Co., Ltd.
– Products: Gate valves, ball valves, butterfly valves.
– Website: [Shanghai Valve](http://www.shvalve.com)
6. CNNC Sufa Technology Industry Co., Ltd.
– Products: Nuclear valves, control valves, safety valves.
– Website: [CNNC Sufa](http://www.sufa.cn)
7. Huangshan Industrial Pump & Valve Co., Ltd.
– Products: Globe valves, check valves, diaphragm valves.
– Website: [Huangshan Valve](http://www.hspv.com)
8. China Valve Technology Co., Ltd.
– Products: Ball valves, butterfly valves, plug valves.
– Website: [China Valve Technology](http://www.chinavalve.com)
9. Zhejiang Zhedong Valve Co., Ltd.
– Products: Gate valves, globe valves, ball valves, butterfly valves.
– Website: [Zhedong Valve](http://www.zhedongvalve.com)
10. NTGD Valve Co., Ltd.
– Products: Ball valves, gate valves, globe valves, check valves, butterfly valves.
– Website: [NTGD Valve](http://www.ntgdvalve.com)
These companies are recognized for their quality, innovation, and wide range of industrial valve solutions, serving various industries including oil and gas, chemical, power generation, and more.
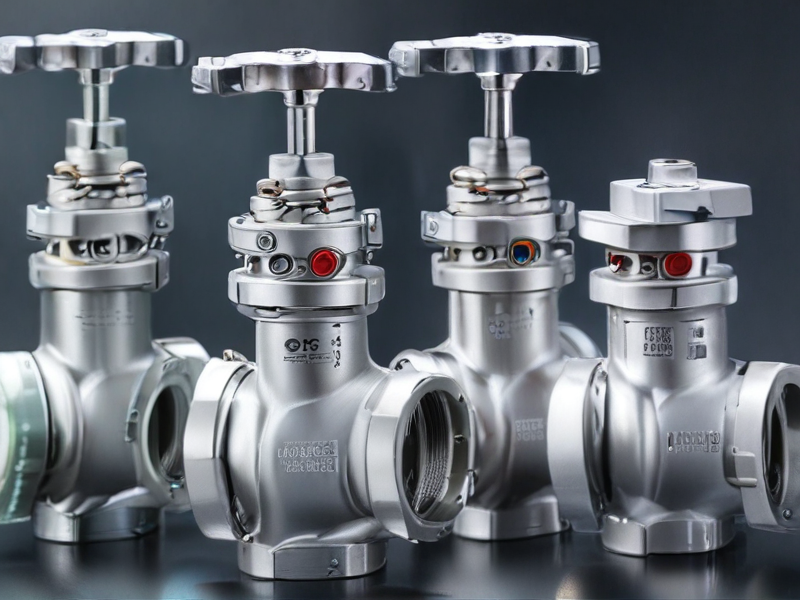
Types of isolation valve
Isolation valves are essential components in fluid control systems, used to stop or regulate the flow of fluids. Here are the main types of isolation valves:
1. Gate Valves: These valves operate by lifting a gate out of the fluid path, providing a straight-through flow with minimal pressure drop when fully open. They are typically used for on/off control in systems where infrequent operation is required.
2. Ball Valves: Featuring a spherical disc, ball valves control flow through a hollow, perforated ball that pivots to open or close the valve. They offer quick operation, tight sealing, and are ideal for applications requiring shut-off and control.
3. Butterfly Valves: Consisting of a rotating disc, butterfly valves regulate or isolate flow by turning the disc, which is mounted on a rod. They are suitable for large volume flow control, providing a compact and lightweight solution with fast operation.
4. Globe Valves: Designed with a movable plug or disc, globe valves regulate flow by changing the position of the disc relative to a stationary ring seat. They offer precise flow control and are used in applications requiring frequent adjustment.
5. Check Valves: These valves allow flow in one direction only, automatically preventing backflow. They are used in systems where maintaining directional flow is critical.
6. Plug Valves: Operating with a cylindrical or tapered plug, plug valves control flow through a quarter-turn motion. They provide a simple, reliable mechanism for shut-off and are used in systems requiring minimal leakage.
7. Diaphragm Valves: Using a flexible diaphragm to open, close, or regulate flow, these valves are ideal for handling corrosive or abrasive fluids. They offer tight sealing and are commonly used in the pharmaceutical and food industries.
8. Needle Valves: Featuring a small, tapered needle-like plunger, needle valves provide precise control of flow rates. They are typically used in applications requiring fine adjustments and low flow rates.
Each type of isolation valve is suited for specific applications based on factors like flow control precision, pressure requirements, and fluid characteristics.
Pros and Cons of Using isolation valve
Pros of Using Isolation Valves:
1. System Control and Maintenance:
Isolation valves allow sections of a system to be shut off for maintenance, repair, or replacement without affecting the entire system, ensuring smoother operations and minimizing downtime.
2. Safety:
These valves enhance safety by isolating hazardous areas or fluids, preventing accidents during maintenance or emergency situations.
3. Operational Efficiency:
By isolating specific sections, operators can perform tasks more efficiently, knowing that other parts of the system remain operational and unaffected.
4. Leak Prevention:
Properly installed isolation valves help in preventing leaks, which is crucial in systems handling dangerous or costly fluids and gases.
5. Cost Savings:
Reducing the need for complete system shutdowns saves time and operational costs. Additionally, preventing leaks and accidents saves costs related to damages and regulatory fines.
Cons of Using Isolation Valves:
1. Initial Cost:
The installation of isolation valves can be expensive, particularly in large or complex systems, due to the cost of the valves themselves and the labor required for installation.
2. Maintenance:
While they help in system maintenance, the valves themselves require regular inspection and maintenance to ensure they function correctly, adding to the overall maintenance burden.
3. Potential for Failure:
Like any mechanical component, isolation valves can fail, potentially leading to leaks, system disruptions, or safety hazards if not properly maintained or if they malfunction.
4. Complexity:
Adding isolation valves increases the complexity of the piping or fluid system. Operators and maintenance personnel need to be well-trained to manage these components effectively.
5. Flow Disruption:
Improperly used or malfunctioning isolation valves can cause flow disruption, pressure drops, or blockages within the system, impacting overall performance.
In summary, isolation valves are vital for system control, safety, and operational efficiency, but they come with costs related to installation, maintenance, and potential operational complexities.
isolation valve Reference Specifications (varies for different product)
Isolation Valve Reference Specifications
#### General Specifications:
1. Type: Gate, Globe, Ball, Butterfly, or Plug valves.
2. Material: Carbon Steel, Stainless Steel, Alloy Steel, Brass, Bronze, or PVC.
3. Size Range: 1/2″ to 48″ (DN15 to DN1200).
4. Pressure Rating: ANSI Class 150 to 2500, PN10 to PN420.
5. Temperature Range: -196°C to 600°C (-320°F to 1112°F).
#### Construction:
1. Body: Cast or forged.
2. Ends: Flanged, Butt-weld, Socket-weld, or Threaded.
3. Stem: Rising or non-rising, with backseat for additional sealing.
4. Bonnet: Bolted, welded, or pressure-sealed.
5. Seals: Metal-to-metal or soft-seated.
#### Operation:
1. Manual: Handwheel, lever, or gear.
2. Automated: Pneumatic, electric, or hydraulic actuators.
3. Fail-safe options: Fail-open or fail-closed.
#### Standards Compliance:
1. Design: ASME B16.34, API 600, API 6D, or ISO 17292.
2. Testing: API 598, ISO 5208.
3. End Connections: ASME B16.5, ASME B16.25, ASME B16.11.
#### Performance:
1. Leakage Class: ANSI/FCI 70-2 Class VI (for soft seats) or Class IV/V (for metal seats).
2. Flow Coefficient (Cv): Varies with size and type.
3. Cycling Capability: High cycle or standard cycle based on application.
#### Additional Features:
1. Fire-Safe Design: API 607 or ISO 10497.
2. Anti-static Device: To prevent sparking in explosive environments.
3. Blow-out Proof Stem: Ensures safety during operation.
4. Locking Mechanism: For securing valve position.
#### Special Considerations:
1. Corrosive Service: Special alloys or linings (e.g., Hastelloy, PTFE).
2. Cryogenic Service: Extended bonnets and low-temperature materials.
3. High Temperature Service: Graphite packing and metal seats.
4. Sanitary Applications: Polished internals and FDA-approved materials.
These specifications provide a comprehensive overview of the various aspects to consider when selecting and using isolation valves in different industrial applications. Adjustments may be needed based on specific service conditions and regulatory requirements.
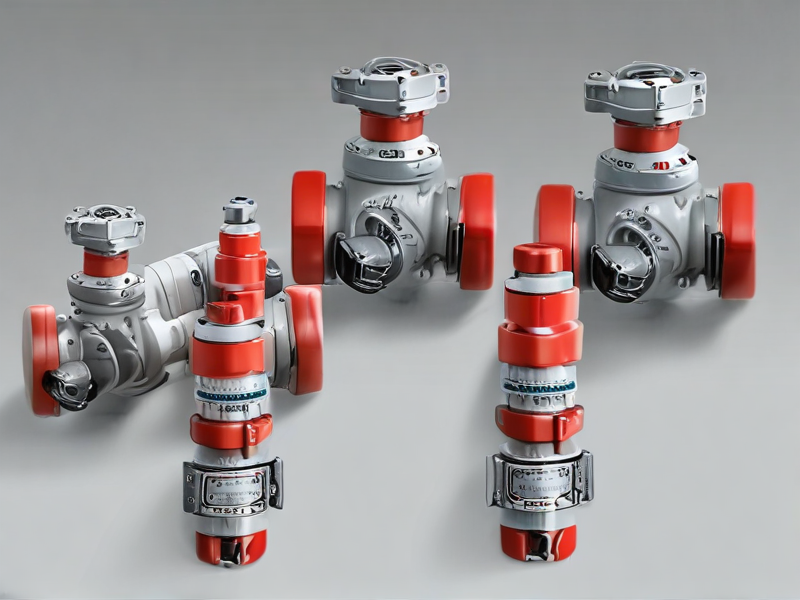
Applications of isolation valve
Isolation valves are critical components in fluid handling systems, serving various functions across multiple industries. Here are some key applications:
1. Maintenance and Safety: Isolation valves are used to block the flow of fluids, allowing for safe maintenance and repairs. This prevents leaks, reduces the risk of accidents, and ensures the safety of personnel working on or near the equipment.
2. System Control: In industrial processes, isolation valves help control and direct the flow of liquids and gases. They can isolate sections of a pipeline to manage process operations, aiding in efficient system control and flexibility.
3. Emergency Shutdown: Isolation valves are crucial in emergency situations to quickly stop the flow of hazardous fluids, minimizing potential damage and preventing environmental contamination.
4. Leak Prevention: They provide a tight seal to prevent leaks, essential in applications involving toxic, corrosive, or flammable fluids. This is particularly important in the chemical, oil, and gas industries.
5. Testing and Inspection: Isolation valves allow specific sections of a system to be isolated for pressure testing, inspection, and quality control without affecting the entire system.
6. Process Isolation: In complex processing plants, such as refineries and power plants, isolation valves are used to isolate processes or equipment, facilitating process changes and maintenance without shutting down the entire plant.
7. Hydraulic and Pneumatic Systems: In hydraulic and pneumatic applications, isolation valves help control the flow and pressure, ensuring the system operates efficiently and safely.
8. Water Supply Systems: In municipal and building water supply systems, isolation valves are used to isolate sections for repair, maintenance, and emergency response, ensuring the continuity of service.
Overall, isolation valves are essential for ensuring the safe, efficient, and reliable operation of fluid handling systems across various industries.
Material of isolation valve
Isolation valves are critical components in various industrial systems, used to stop the flow of fluid or gas. The material selection for isolation valves depends on the application, fluid type, pressure, temperature, and environmental conditions. Here are some commonly used materials:
1. Carbon Steel:
– Applications: Suitable for general-purpose applications in oil, gas, water, and steam services.
– Properties: High strength and durability but limited corrosion resistance.
2. Stainless Steel:
– Applications: Used in corrosive environments, including chemical processing, food and beverage, and pharmaceutical industries.
– Properties: Excellent corrosion resistance and good mechanical properties at a wide range of temperatures.
3. Brass:
– Applications: Common in water, air, and some low-pressure gas applications.
– Properties: Good corrosion resistance and machinability, but not suitable for highly corrosive environments or high-pressure systems.
4. Bronze:
– Applications: Often used in water and marine environments.
– Properties: Good corrosion resistance, especially in seawater, and good mechanical strength.
5. Ductile Iron:
– Applications: Frequently used in water and wastewater systems.
– Properties: High strength and toughness, with better corrosion resistance than cast iron.
6. PVC (Polyvinyl Chloride):
– Applications: Suitable for low-pressure applications, especially in water and some chemical services.
– Properties: Lightweight, corrosion-resistant, and easy to install but not suitable for high temperatures or pressures.
7. Alloy Steels:
– Applications: Used in high-temperature and high-pressure applications, such as power generation and petrochemical industries.
– Properties: Enhanced mechanical properties and better corrosion resistance at elevated temperatures.
8. Titanium:
– Applications: Ideal for highly corrosive environments, including chemical processing and seawater applications.
– Properties: Outstanding corrosion resistance and high strength-to-weight ratio, but expensive.
Selecting the right material for an isolation valve involves considering the specific requirements of the application to ensure reliability, safety, and cost-effectiveness.
Quality Testing Methods for isolation valve and how to control the quality
Quality Testing Methods for Isolation Valves
1. Hydrostatic Testing: This involves filling the valve with water and pressurizing it to check for leaks, ensuring the valve body and seals are intact.
2. Pneumatic Testing: Similar to hydrostatic testing, but uses air or inert gas, making it suitable for valves in gas applications.
3. Seat Leak Test: This test checks the sealing capability of the valve seat. The valve is closed, and pressure is applied to see if any leakage occurs past the seat.
4. Shell Test: Conducted to verify the strength of the valve body, this test involves pressurizing the valve to a specified limit and checking for any deformations or weaknesses.
5. Functional Testing: Ensures the valve operates correctly. This includes cycling the valve open and closed, checking actuation times, and verifying the response to control signals.
6. Visual Inspection: Involves a thorough examination for defects, proper assembly, and adherence to specifications. It includes checking for casting flaws, surface finish, and overall construction.
7. Nondestructive Testing (NDT): Methods like radiography, ultrasonic, and dye penetrant testing are used to detect internal or surface defects without damaging the valve.
Quality Control Measures
1. Standard Operating Procedures (SOPs): Implement detailed SOPs for each testing method to ensure consistency and accuracy.
2. Training and Certification: Ensure all personnel conducting tests are properly trained and certified.
3. Calibration of Equipment: Regularly calibrate testing equipment to maintain accuracy and reliability.
4. Documentation: Maintain comprehensive records of all tests performed, including results and any corrective actions taken.
5. Third-Party Audits: Periodic audits by external parties can validate the effectiveness of quality control processes.
6. Compliance with Standards: Adhere to relevant industry standards and regulations, such as ASME, API, and ISO, to ensure valves meet required quality benchmarks.
7. Continuous Improvement: Implement a feedback loop to continually assess and improve testing and quality control processes.
By integrating these testing methods and quality control measures, manufacturers can ensure that isolation valves perform reliably in their intended applications.
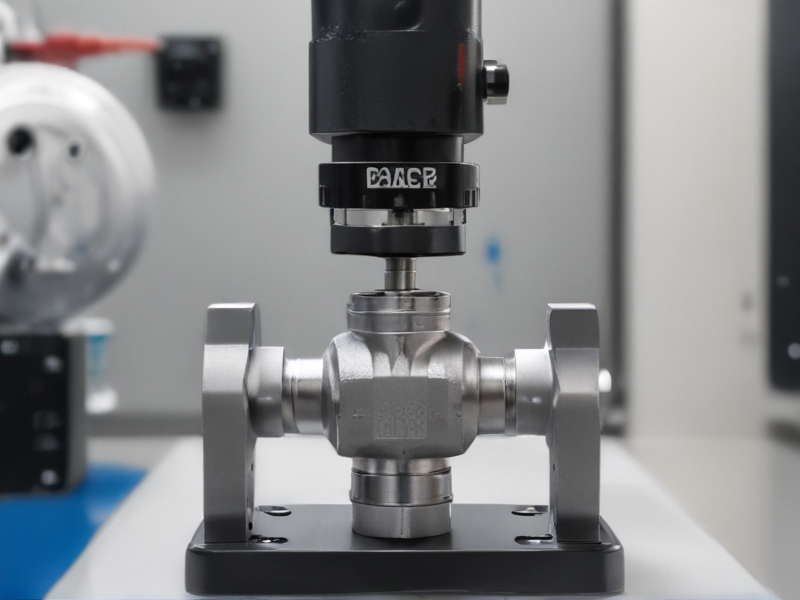
The Work Process and how to use isolation valve
Work Process for Using an Isolation Valve
1. Preparation:
– Identify the Valve: Ensure you have correctly identified the isolation valve in the system.
– Review Procedures: Familiarize yourself with the specific operational procedures and safety guidelines related to the valve.
2. Safety Precautions:
– PPE (Personal Protective Equipment): Wear appropriate PPE such as gloves, safety goggles, and protective clothing.
– System Shutdown: If necessary, shut down the system or the section where the valve is located to ensure safe operation.
– Pressure Release: Ensure that any pressure within the system is safely released to avoid accidents.
3. Operating the Valve:
– Check Valve Position: Verify whether the valve is in the open or closed position before beginning operation.
– Turn the Valve: Use the appropriate tool (typically a valve key or handle) to turn the valve. Turn clockwise to close and counterclockwise to open.
– Verify Operation: Confirm that the valve has reached the desired position (fully open or fully closed) by observing the flow or using indicators on the valve.
4. Post-Operation:
– Inspect for Leaks: After operation, inspect the valve and surrounding area for any signs of leaks.
– Secure the Valve: Ensure the valve is securely in place and cannot be accidentally moved.
– Document the Operation: Record the operation details, including the time, date, and personnel involved.
5. Return to Service:
– Repressurize System: Gradually bring the system back to operating pressure if it was shut down.
– Monitor: Monitor the system for any irregularities or leaks to ensure the valve is functioning correctly.
Important Tips
– Regular Maintenance: Periodically inspect and maintain isolation valves to ensure they are in good working condition.
– Training: Ensure all personnel are adequately trained in operating isolation valves and understand the safety protocols.
By following these steps, you can safely and effectively use isolation valves in various industrial applications.
isolation valve Importing questions including Cost,Supplier,Sample,Certification and Market
When importing isolation valves, it’s essential to address several key factors to ensure a successful procurement process. Here’s a concise guide covering cost, suppliers, samples, certifications, and market considerations:
Cost
1. Initial Cost: Evaluate the unit cost of valves from different suppliers.
2. Total Cost of Ownership: Consider shipping, customs duties, installation, and maintenance costs.
3. Bulk Discounts: Inquire about discounts for large orders.
Supplier
1. Reputation: Research the supplier’s market reputation and history of reliability.
2. Lead Time: Assess the supplier’s delivery timelines to ensure they align with your project needs.
3. Support Services: Check if the supplier offers technical support, installation guidance, and after-sales service.
Sample
1. Request Samples: Before placing a large order, request samples to evaluate the quality and performance.
2. Testing: Conduct rigorous testing on samples to ensure they meet your specifications and operational requirements.
3. Return Policy: Understand the supplier’s policy on sample returns or exchanges if they do not meet expectations.
Certification
1. Compliance: Ensure the valves comply with international and local standards (e.g., ISO, API, CE).
2. Quality Assurance: Verify if the supplier holds relevant certifications like ISO 9001 for quality management systems.
3. Industry Standards: Check for certifications specific to your industry, such as ASME for industrial valves.
Market Considerations
1. Demand and Supply: Analyze the market demand and supply dynamics to negotiate better prices.
2. Regulations: Stay updated on import regulations and standards in your country to avoid legal complications.
3. Competitors: Understand the market share and strategies of competitors using similar valves to position your offerings effectively.
By addressing these aspects, you can make informed decisions, ensuring cost-effectiveness, compliance, and reliability in your isolation valve imports.
How to find and select check reliable isolation valve manufacturers in China
To find and select reliable isolation valve manufacturers in China, follow these steps:
1. Research and List Potential Manufacturers: Use trade directories such as Alibaba, Made-in-China, and Global Sources. Look for manufacturers with high ratings, multiple years of experience, and comprehensive product catalogs.
2. Verify Credentials: Check for certifications like ISO 9001, CE, and API. These standards indicate adherence to international quality norms.
3. Assess Product Quality: Request product samples and detailed specifications. Evaluate materials, design, and compliance with industry standards.
4. Customer Reviews and References: Look for customer reviews and ratings on trade platforms. Contact previous clients for feedback on product performance, reliability, and after-sales service.
5. Factory Visits and Audits: If possible, visit the manufacturing facilities. Verify the production processes, quality control measures, and overall manufacturing environment.
6. Communication and Responsiveness: Evaluate the manufacturer’s responsiveness to inquiries. Clear and prompt communication is crucial for a smooth business relationship.
7. Pricing and Payment Terms: Compare pricing structures, including hidden costs like shipping and customs. Ensure the payment terms are fair and protect your interests.
8. Supply Chain and Logistics: Assess the manufacturer’s capacity to meet your order volumes and delivery timelines. Reliable logistics support ensures timely supply.
9. After-Sales Support: Confirm the availability of after-sales support, including warranty, maintenance, and repair services.
By following these steps, you can identify reliable isolation valve manufacturers in China who meet your quality, pricing, and logistical needs.
Background Research for isolation valve manufacturers Companies in China, use qcc.com archive.org importyeti.com
Several prominent isolation valve manufacturers operate in China. Among them are:
1. SuZhou KEDE Valve Co., Ltd: Located in Jiangsu province, Suzhou KEDE Valve specializes in manufacturing various valves, including isolation valves, used in chemical, petroleum, and natural gas industries. The company emphasizes innovation and quality, with extensive research and development efforts.
2. Zhejiang Sanhua Intelligent Controls Co., Ltd: Based in Zhejiang, this company is well-known for its comprehensive range of HVAC controls and components, including high-quality isolation valves. Sanhua focuses on both domestic and international markets, maintaining a strong reputation for technological advancements and quality products.
3. Wuhan Xingyu Machinery Co., Ltd: This Wuhan-based company manufactures a wide range of industrial valves, including isolation valves. They serve industries such as water treatment, oil and gas, and power generation, emphasizing durability and reliability in their product lines.
4. Hebei Kaixuan Sealing Co., Ltd: Located in Hebei province, Kaixuan Sealing offers a broad spectrum of sealing solutions and industrial valves, including isolation valves. The company prides itself on its strict quality control processes and adherence to international standards.
These companies are recognized for their strong manufacturing capabilities, technological innovation, and adherence to stringent quality standards, making them key players in the isolation valve market in China.
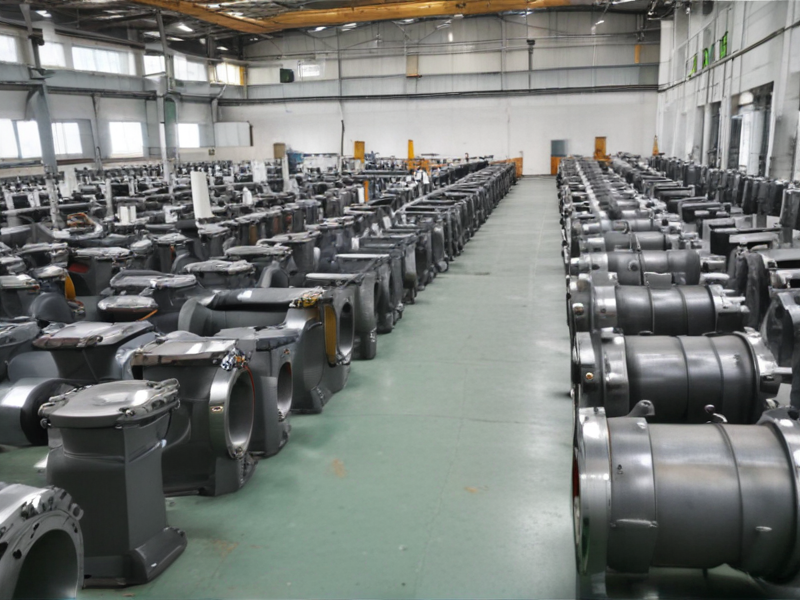
Price Cost Research for isolation valve manufacturers Companies in China, use temu.com and 1688.com
When researching isolation valve manufacturers in China through Temu.com and 1688.com, you can find a variety of options with competitive prices.
On 1688.com, several manufacturers offer different types of isolation valves. For instance, pneumatic solenoid valves are available from multiple suppliers such as Dongguan Bridge Pneumatic Components Factory, offering prices starting from ¥19.95 per unit. Companies like Jin Yi Electromagnetic Valve Factory provide pneumatic directional control valves at around ¥29.25 each. Safety valves, such as those from Tianjin Tangzheng Valve Co., start at ¥263.0 per unit.
For more specialized options, butterfly valves (DN100) are available from manufacturers like Bundor Valve Technology Co., starting at ¥125.0 per piece, and Tianjin Yongjian Valve Co., offering manual wafer butterfly valves for around ¥32.0 each. These prices reflect bulk purchasing options, often with flexible terms for shipping and payment.
Temu.com also lists several isolation valve products, but the detailed pricing and specific product options may vary and require direct inquiry with suppliers for precise quotes and bulk order negotiations.
Both platforms provide a range of valve types and materials, including stainless steel and brass, catering to different industrial needs. For accurate and specific pricing, direct contact with manufacturers is recommended to account for customization and shipping considerations.
Shipping Cost for isolation valve import from China
When importing isolation valves from China, the shipping cost depends on several factors: weight and dimensions of the shipment, shipping method, and destination. Here’s a concise breakdown of the main elements affecting the cost:
Shipping Methods
1. Air Freight: Fast but expensive, suitable for small, high-value shipments.
2. Sea Freight: Economical for large volumes, but slower.
3. Courier Services: Ideal for small packages, often includes customs clearance.
Factors Influencing Cost
1. Weight and Volume: Larger and heavier shipments cost more.
2. Destination: Distance and access to major ports/airports affect pricing.
3. Incoterms: Defines who pays for which part of the shipping process (e.g., FOB, CIF, DDP).
Cost Estimates
– Air Freight: $5-$10 per kg for international shipping.
– Sea Freight: Around $1,000-$3,000 per 20-foot container, depending on the route and current market rates.
– Courier Services: $10-$20 per kg for door-to-door service.
Additional Costs
– Customs Duties and Taxes: Varies by country; typically 5%-15% of the shipment value.
– Insurance: Optional but recommended, around 0.3%-0.5% of the shipment value.
– Handling Fees: Port or airport handling, documentation fees, and other miscellaneous charges.
Example Calculation
For a 500 kg shipment of isolation valves:
– Air Freight: Approximately $2,500 – $5,000.
– Sea Freight: Around $1,500 for a shared container (LCL).
– Customs Duties: If the shipment value is $10,000, duties could range from $500 to $1,500.
Tips
– Consolidate Shipments: To reduce cost per unit.
– Negotiate Rates: With multiple freight forwarders.
– Consider Lead Times: Air for urgency, sea for cost-saving.
Engage a reliable freight forwarder to get precise quotes tailored to your specific needs.
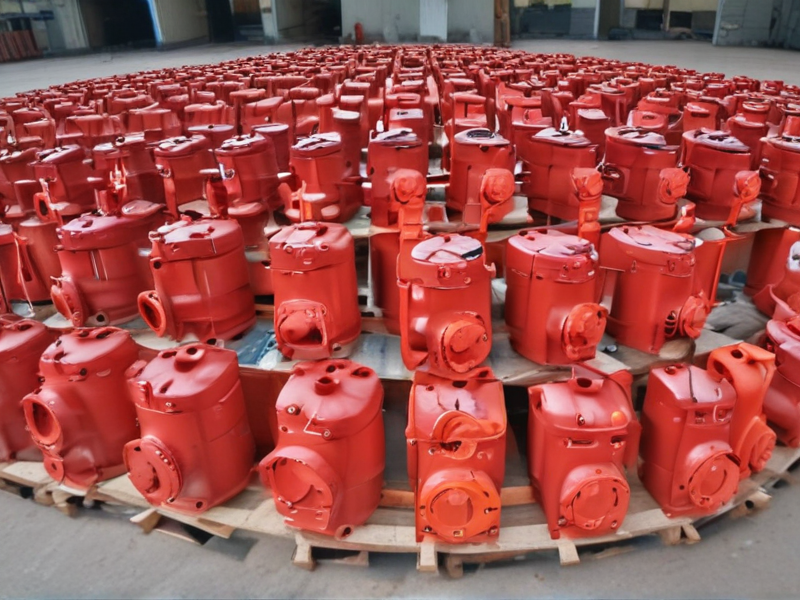
Compare China and Other isolation valve Markets: Products Quality and Price,Visible and Hidden Costs
When comparing the isolation valve markets of China and other global regions, several key aspects emerge: product quality, price, and costs.
Product Quality:
Chinese isolation valves often face scrutiny regarding quality control. While many manufacturers in China produce valves that meet international standards, inconsistency remains a concern. In contrast, valves from Europe, the U.S., and Japan are generally perceived as more reliable due to stringent manufacturing standards and rigorous testing protocols.
Price:
Chinese valves are typically cheaper due to lower labor costs, economies of scale, and government subsidies. This cost advantage can make them attractive for budget-sensitive projects. On the other hand, valves from other regions, particularly Europe and the U.S., are priced higher, reflecting higher production costs and premium branding.
Visible and Hidden Costs:
Visible costs include the initial purchase price, shipping, and duties. Chinese valves often have lower upfront costs. However, hidden costs can be significant. These include potential quality issues leading to higher maintenance, replacement costs, and downtime due to valve failure. Valves from Europe, the U.S., and Japan, while more expensive upfront, often incur lower hidden costs due to their durability and reliability.
In summary, while Chinese isolation valves offer a cost advantage, this can be offset by potential hidden costs and quality concerns. Valves from other global markets, though pricier, generally offer higher reliability and lower long-term costs. Buyers must weigh immediate budget constraints against potential long-term expenditures and operational reliability when making procurement decisions.
Custom Private Labeling and Branding Opportunities with Chinese isolation valve Manufacturers
Chinese isolation valve manufacturers offer extensive custom private labeling and branding opportunities, making them attractive partners for businesses seeking to differentiate their products in competitive markets. Here are key opportunities:
1. Customization Flexibility:
Chinese manufacturers typically provide extensive customization options. This includes tailoring the valve design, materials, sizes, and specifications to meet unique requirements. Customization ensures that the valves meet specific application needs, enhancing their functionality and appeal.
2. Private Labeling:
Businesses can opt for private labeling services, allowing them to market valves under their brand name. This process includes customized packaging, labeling, and even bespoke branding elements like logos and color schemes. Private labeling helps businesses build their brand identity and foster customer loyalty.
3. Cost Efficiency:
Manufacturing costs in China are generally lower due to economies of scale, lower labor costs, and efficient production processes. This cost advantage enables businesses to offer competitive pricing or achieve higher profit margins, even with customized and branded products.
4. Advanced Manufacturing Capabilities:
Many Chinese manufacturers invest in advanced technologies and equipment, ensuring high-quality production standards. This technological edge ensures that the valves meet international quality and safety standards, which is crucial for brand reputation.
5. Quick Turnaround Times:
Chinese manufacturers often have streamlined production processes and supply chains, allowing for faster turnaround times. This agility is beneficial for businesses needing to respond quickly to market demands and trends.
6. Comprehensive Support Services:
These manufacturers often provide comprehensive support, including design assistance, prototyping, and technical advice. This support is invaluable in developing and launching new products effectively.
By leveraging these opportunities, businesses can enhance their product offerings, establish a strong brand presence, and compete more effectively in global markets.
Tips for Procurement and Considerations when Purchasing isolation valve
When procuring isolation valves, consider the following tips and factors to ensure optimal performance, reliability, and cost-effectiveness:
1. Understand the Application: Determine the specific requirements such as the type of fluid (gas, liquid, corrosive, etc.), temperature, pressure, and flow characteristics. This helps in selecting the right valve material and type.
2. Valve Type Selection: Choose between gate, globe, ball, butterfly, or plug valves based on the application’s control needs and the nature of the fluid.
3. Material Compatibility: Ensure the valve material is compatible with the fluid to prevent corrosion, wear, and chemical reactions. Common materials include stainless steel, brass, bronze, and specialized alloys.
4. Pressure and Temperature Ratings: Verify that the valve can withstand the maximum pressure and temperature of the system. This ensures safety and longevity.
5. Valve Size: Correct sizing is crucial. An oversized or undersized valve can lead to operational inefficiencies and increased wear.
6. End Connections: Choose appropriate end connections (flanged, threaded, welded) based on the piping system and installation requirements.
7. Standards and Certifications: Ensure the valve complies with industry standards (e.g., ASME, API, ISO) and any specific certifications required for your application.
8. Maintenance and Operation: Consider the ease of maintenance, availability of spare parts, and operational simplicity. Valves that are easy to service and operate can reduce downtime and maintenance costs.
9. Manufacturer Reputation: Select valves from reputable manufacturers known for quality and reliability. Check for reviews, references, and industry reputation.
10. Cost vs. Quality: While cost is a significant factor, do not compromise on quality. A cheaper valve may lead to higher long-term costs due to frequent replacements and potential system failures.
11. Warranty and Support: Ensure the valve comes with a robust warranty and that the manufacturer offers strong customer support for troubleshooting and parts replacement.
By considering these factors, you can ensure the procurement of reliable isolation valves that meet your system’s specific needs and operational requirements.
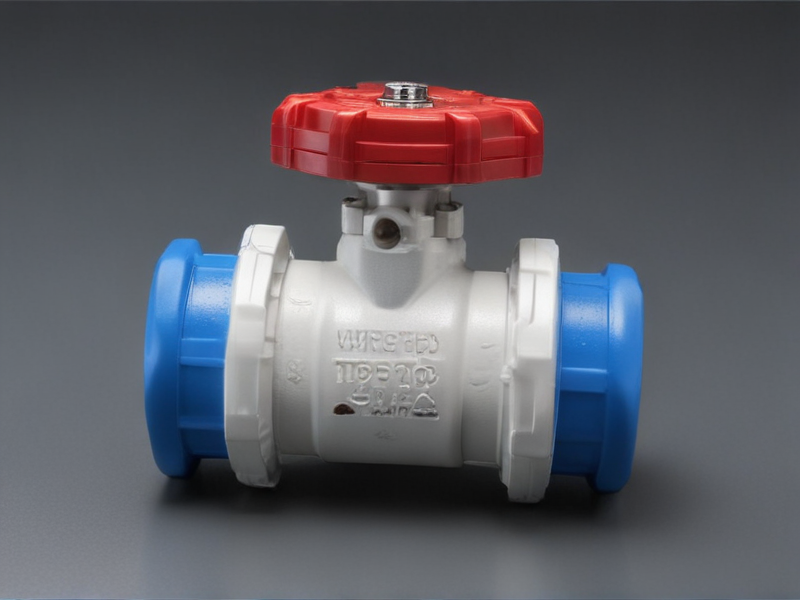
FAQs on Sourcing and Manufacturing isolation valve in China
FAQs on Sourcing and Manufacturing Isolation Valves in China
1. Why source isolation valves from China?
China is a global manufacturing hub, offering competitive pricing, a wide range of suppliers, and advanced manufacturing capabilities. This makes it cost-effective without compromising quality.
2. What types of isolation valves are manufactured in China?
China produces various types of isolation valves, including gate valves, ball valves, butterfly valves, and globe valves. These valves are available in different materials such as stainless steel, carbon steel, and alloys.
3. How can I ensure the quality of valves from Chinese manufacturers?
To ensure quality, select ISO-certified manufacturers, request product samples, conduct factory audits, and hire third-party inspection services. It’s also beneficial to review previous customer feedback and compliance with international standards like API, ANSI, and DIN.
4. What is the typical lead time for manufacturing isolation valves in China?
The lead time varies depending on the order size, complexity, and factory workload. Typically, it ranges from 4 to 12 weeks. Custom orders may take longer.
5. Are there any language barriers when dealing with Chinese suppliers?
While many Chinese manufacturers have English-speaking staff, some communication challenges may arise. Clear and concise communication, written agreements, and professional translation services can mitigate this.
6. What are the shipping options and costs?
Shipping can be done via sea freight (most economical for large orders), air freight (faster but more expensive), or express services for smaller, urgent shipments. Costs depend on the shipment size, weight, and destination.
7. How do I handle payments and ensure secure transactions?
Common payment methods include T/T (Telegraphic Transfer), L/C (Letter of Credit), and PayPal for smaller orders. To ensure security, use escrow services or make payments in stages, tied to production milestones.
8. What are the import duties and regulations?
Import duties vary by country and product classification. Familiarize yourself with your country’s import regulations, HS codes, and ensure compliance with all relevant standards and certifications.
9. Can I visit the manufacturer’s factory?
Yes, visiting the factory can provide insights into their operations and build trust. Many manufacturers welcome potential clients to their facilities.
10. What should I include in the contract with the manufacturer?
Contracts should detail product specifications, pricing, payment terms, lead times, quality standards, inspection criteria, and penalties for non-compliance. Having a clear, comprehensive contract helps protect both parties’ interests.