Top 10 flanged valve in China introduce,list main products and website if have
Here are the top 10 flanged valve manufacturers in China, along with their main products and websites:
1. Yuanda Valve Group Co., Ltd.
– Main Products: Middle and low-pressure valves
– Website: [Yuanda Valve Group](http://www.ydvalve.com/)
2. Neway Valve (Suzhou) Co., Ltd.
– Main Products: Gate valves, globe valves, check valves, ball valves, butterfly valves, control valves, API6A valves, subsea valves, safety valves, and nuclear power valves.
– Website: [Neway Valve](http://www.newayvalve.com/)
3. Chongqing Chuanyi Automation Co., Ltd.
– Main Products: Industrial automation control systems and instruments, including control valves.
– Website: [Chuanyi Automation](http://www.cqcy.com/)
4. Suyan Valve Machinery Co., Ltd.
– Main Products: Gate valves, ball valves, fully welded ball valves, and high, medium, and low-pressure valves.
– Website: [Suyan Valve](http://www.suyangroup.com/)
5. Jiangsu Shentong Valve Co., Ltd.
– Main Products: Gate valves, globe valves, check valves, ball valves, and butterfly valves.
– Website: [Shentong Valve](http://en.stfm.cn/)
6. ZFA Valve
– Main Products: Butterfly valves, gate valves, and check valves.
– Website: [ZFA Valve](https://zfavalves.com/)
7. Xiamen Dervos Valves Industry Co., Ltd.
– Main Products: Industrial valves including gate, globe, check, and ball valves.
– Website: [Dervos Valves](http://www.dvsvalve.com/)
8. Sanhua Valve
– Main Products: HVAC&R controls and components.
– Website: [Sanhua Valve](http://www.sanhuagroup.com/)
9. Langao Valve
– Main Products: Industrial valves including various types of gate, globe, check, and ball valves.
– Website: [Langao Valve](http://www.langaovalve.com/)
10. China Valves Technology (Changsha) Co., Ltd.
– Main Products: Industrial valves including gate, globe, check, and ball valves.
– Website: [China Valves](http://www.cvalve.com/)
These companies represent a significant portion of China’s valve manufacturing industry, providing high-quality flanged valves for various industrial applications.
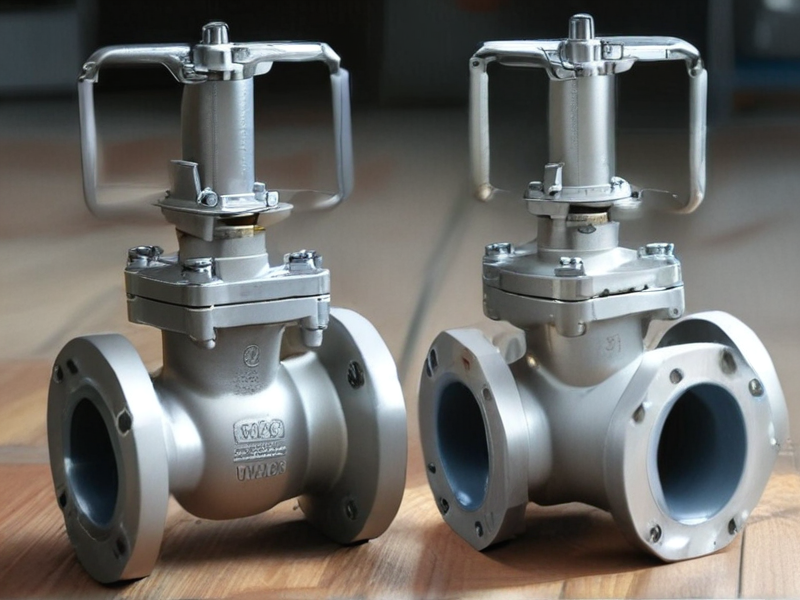
Types of flanged valve
Flanged valves are essential components in piping systems, used to control the flow of fluids. They feature flanges on the ends for easy connection to pipes. Here are the main types of flanged valves:
1. Gate Valve:
– Function: Used for on/off control with minimal pressure drop.
– Design: Features a gate or wedge that moves up and down to open or close the flow path.
2. Globe Valve:
– Function: Used for regulating flow.
– Design: Contains a movable disk and a stationary ring seat. Flow changes direction within the valve, providing good throttling capabilities.
3. Ball Valve:
– Function: Provides quick on/off control with low pressure drop.
– Design: Utilizes a spherical ball with a hole through the middle. When the hole aligns with the flow path, fluid passes through.
4. Butterfly Valve:
– Function: Suitable for flow regulation and quick shut-off.
– Design: Consists of a rotating disk within the flow path. A quarter-turn of the handle or actuator opens or closes the valve.
5. Check Valve:
– Function: Prevents backflow.
– Design: Allows flow in one direction only. Types include swing check (with a hinged flap) and lift check (with a movable disk).
6. Plug Valve:
– Function: Used for on/off control and flow diversion.
– Design: Features a cylindrical or conical plug with a passage to permit flow when aligned with the ports.
7. Diaphragm Valve:
– Function: Ideal for handling corrosive fluids and slurries.
– Design: Uses a diaphragm to open or close the valve. Suitable for clean or sterile applications.
8. Needle Valve:
– Function: Allows precise flow control.
– Design: Has a small, tapered needle-like plunger that fits into a conical seat.
Each type of flanged valve is chosen based on the specific requirements of the application, including flow control, pressure, and fluid characteristics.
Pros and Cons of Using flanged valve
Flanged valves are a common type of valve connection used in various industrial applications. Here are the key pros and cons of using flanged valves:
Pros:
1. Ease of Installation and Maintenance:
– Simple Assembly: Flanged connections allow for easy installation and removal, facilitating maintenance and inspection.
– Reusability: Flanges can be reused, which is economical and convenient.
2. Strong and Reliable Connection:
– Secure Fit: Flanged connections provide a robust and secure seal, which is crucial for preventing leaks in high-pressure systems.
– High Durability: Flanged valves are highly durable and can withstand substantial pressure and temperature variations.
3. Versatility:
– Wide Range of Sizes and Materials: Available in various sizes and materials, making them suitable for a wide range of applications.
– Compatibility: Easily compatible with different types of piping and equipment.
4. Pressure and Temperature Resistance:
– High Performance: Suitable for high-pressure and high-temperature environments, making them ideal for industrial settings such as chemical plants and oil refineries.
Cons:
1. Cost:
– Higher Initial Cost: Generally more expensive than other types of valve connections due to the material and precision required for the flanges.
– Installation Cost: The installation process can be labor-intensive, leading to higher initial setup costs.
2. Size and Weight:
– Bulkiness: Flanged valves are typically bulkier and heavier compared to other valve types, which can be a disadvantage in space-constrained applications.
– Handling and Transportation: The size and weight can make handling, transportation, and installation more challenging and expensive.
3. Potential for Leakage:
– Gasket Dependency: The seal between flanges relies on gaskets, which can degrade over time, leading to potential leakage if not properly maintained.
4. Complexity:
– Alignment Issues: Precise alignment is necessary during installation to ensure a proper seal, which can complicate the installation process.
In summary, flanged valves offer strong, reliable connections suitable for high-pressure and high-temperature applications, but they come with higher costs, increased size and weight, and potential complexity in installation and maintenance.
flanged valve Reference Specifications (varies for different product)
A flanged valve is a critical component in various industrial applications, designed to control the flow of liquids or gases. The specifications for flanged valves can vary significantly depending on the product and its intended use. Here are key reference specifications commonly considered:
1. Valve Type: Gate, globe, ball, butterfly, or check valves, each suited for specific applications.
2. Material: Typically made from cast iron, ductile iron, carbon steel, stainless steel, or specialized alloys to resist corrosion, high temperatures, or specific chemicals.
3. Size Range: Available in sizes from 1/2 inch to 24 inches or larger, accommodating different flow capacities.
4. Pressure Rating: Valves are rated according to their pressure handling capabilities, typically ranging from 150 PSI to 2500 PSI (ANSI Class 150 to Class 2500).
5. Temperature Range: Depending on the material and design, valves can operate in temperatures from -100°F to 1200°F (-73°C to 649°C).
6. End Connections: Flanged ends, usually conforming to standards such as ANSI, DIN, or JIS, ensure compatibility with piping systems.
7. Operation: Manual (handwheel or lever), pneumatic, hydraulic, or electric actuators for remote operation.
8. Standards Compliance: Valves must comply with industry standards such as API, ANSI, ASME, ASTM, or ISO to ensure quality and reliability.
9. Flow Characteristics: Defined by the valve design, influencing flow control and pressure drop across the valve.
10. Seating and Sealing: Materials and design ensuring tight shut-off and minimal leakage. Common materials include PTFE, elastomers, or metal-to-metal seats.
11. Maintenance Features: Includes considerations for ease of maintenance, such as replaceable seats and seals, and design for minimal downtime.
12. Special Features: Options like anti-blowout stems, fire-safe designs, or corrosion-resistant coatings depending on specific application requirements.
These specifications ensure that flanged valves are appropriately selected and used for their intended application, providing safe, efficient, and reliable flow control in various industrial settings.
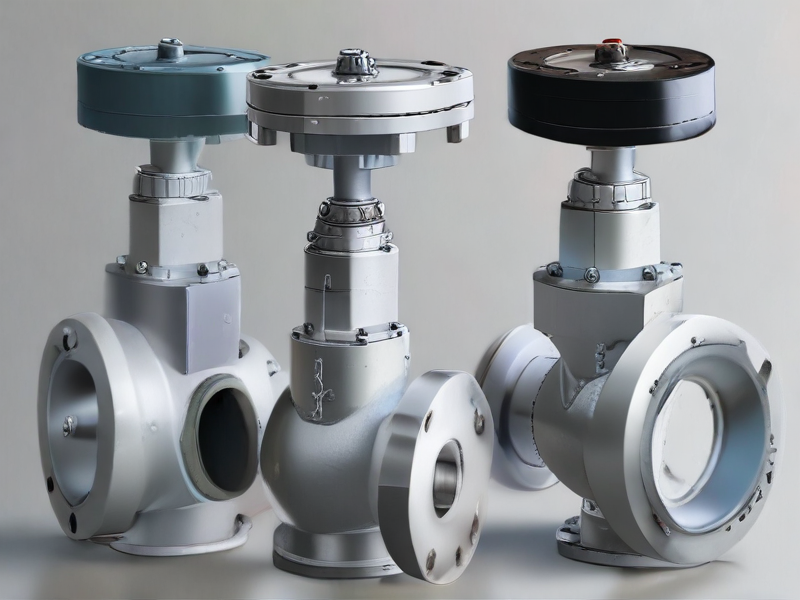
Applications of flanged valve
Flanged valves are essential components in various industrial and commercial applications due to their robust design, ease of installation, and maintenance. Here are some key applications:
1. Oil and Gas Industry: Flanged valves are widely used in the oil and gas sector for controlling the flow of crude oil, natural gas, and refined products. They are employed in upstream, midstream, and downstream processes, including extraction, transportation, and refining.
2. Water and Wastewater Management: In municipal and industrial water treatment plants, flanged valves regulate water flow, manage wastewater, and ensure the smooth operation of filtration systems. Their reliability is crucial for maintaining clean water supply and effective waste management.
3. Chemical Processing: Flanged valves are essential in chemical plants where precise control over fluid flow is necessary. They handle corrosive and hazardous chemicals, ensuring safety and efficiency in processes such as mixing, separation, and reaction control.
4. Power Generation: In power plants, flanged valves are used in cooling systems, boiler feed lines, and steam control applications. They help manage the flow of water, steam, and other fluids critical to power generation processes.
5. Pharmaceutical Industry: The pharmaceutical sector uses flanged valves in manufacturing processes where hygiene and precision are paramount. They control the flow of liquids and gases in processes such as mixing, filtration, and sterilization.
6. Food and Beverage Industry: In food processing plants, flanged valves control the flow of ingredients, manage temperature, and ensure sanitary conditions. They are crucial in processes like pasteurization, carbonation, and packaging.
7. HVAC Systems: Heating, ventilation, and air conditioning systems rely on flanged valves to regulate the flow of water and air, maintaining optimal temperature and air quality in commercial and residential buildings.
8. Marine Industry: Flanged valves are used in ships and offshore platforms to manage ballast systems, fuel supply, and cooling systems. Their durability and resistance to harsh marine environments make them ideal for such applications.
In summary, flanged valves are versatile and indispensable in various industries, providing reliable control over fluid flow in a wide range of applications.
Material of flanged valve
Flanged valves are crucial components in piping systems, used to control the flow of fluids. The material of a flanged valve is critical for its performance, durability, and suitability for specific applications. Here are some common materials used for flanged valves:
1. Cast Iron:
– Usage: General water, steam, and air services.
– Pros: Cost-effective, good machinability.
– Cons: Brittle, not suitable for high-pressure applications.
2. Ductile Iron:
– Usage: Water and sewage systems.
– Pros: Higher strength and flexibility than cast iron, resistant to corrosion.
– Cons: More expensive than cast iron.
3. Carbon Steel:
– Usage: Oil and gas, petrochemical industries.
– Pros: High strength, withstands high pressures and temperatures.
– Cons: Prone to corrosion, requires proper coating or treatment.
4. Stainless Steel:
– Usage: Food processing, pharmaceuticals, chemical industries.
– Pros: Excellent corrosion resistance, durability, hygiene.
– Cons: Expensive, requires special machining.
5. Bronze:
– Usage: Marine environments, water services.
– Pros: Good corrosion resistance, durability.
– Cons: Costly, not suitable for very high-pressure applications.
6. Brass:
– Usage: Plumbing, HVAC systems.
– Pros: Corrosion-resistant, easy to machine, cost-effective for low-pressure applications.
– Cons: Not suitable for high-pressure or high-temperature environments.
7. Plastic (PVC, CPVC, PTFE):
– Usage: Chemical handling, low-pressure water systems.
– Pros: Corrosion-resistant, lightweight, cost-effective.
– Cons: Limited pressure and temperature range, less durable than metals.
8. Alloy Steel:
– Usage: High-pressure steam, high-temperature services.
– Pros: High strength, temperature resistance.
– Cons: Expensive, requires specific machining techniques.
When selecting the material for a flanged valve, consider the specific requirements of the application, such as pressure, temperature, and the type of fluid being controlled. Proper material selection ensures longevity and reliability of the valve in its intended service.
Quality Testing Methods for flanged valve and how to control the quality
Quality testing of flanged valves involves several methods to ensure their reliability and performance. Key methods include:
1. Hydrostatic Testing: Valves are subjected to water pressure to check for leaks. This test ensures the valve body and sealing surfaces can withstand specified pressures without leaking.
2. Pneumatic Testing: Air or nitrogen is used instead of water, suitable for valves used in gas service. This test helps detect even small leaks due to the higher sensitivity of air.
3. Visual Inspection: This involves checking the valve for any visible defects such as cracks, deformations, or improper machining. It’s a preliminary step to identify obvious faults.
4. Dimensional Inspection: Using precise measuring tools, this inspection verifies that the valve dimensions adhere to specified tolerances, ensuring proper fit and function.
5. Non-Destructive Testing (NDT): Methods like ultrasonic testing, radiographic testing, and magnetic particle testing detect internal and surface defects without damaging the valve.
6. Operational Testing: Valves are operated through their full range to ensure smooth and proper functioning. This includes checking the torque required to operate the valve and verifying the operation of actuators.
7. Pressure Relief Testing: For safety valves, this test ensures they open at the correct set pressure and reseal properly after relieving pressure.
To control the quality:
1. Standardized Procedures: Implement and adhere to industry standards such as API, ASME, and ISO. Standard operating procedures should be documented and followed rigorously.
2. Quality Management Systems (QMS): Adopt QMS frameworks like ISO 9001 to maintain consistency in quality. Regular audits and continuous improvement practices help maintain high standards.
3. Supplier Quality Management: Ensure raw materials and components from suppliers meet specified standards through rigorous supplier evaluation and regular audits.
4. Training: Regular training programs for personnel on the latest testing techniques and quality standards ensure the workforce is competent and up-to-date.
5. Documentation and Traceability: Maintain detailed records of all tests and inspections. Traceability ensures that any defect can be traced back to its source, facilitating root cause analysis and corrective action.
By employing these testing methods and quality control practices, the reliability and performance of flanged valves can be assured.
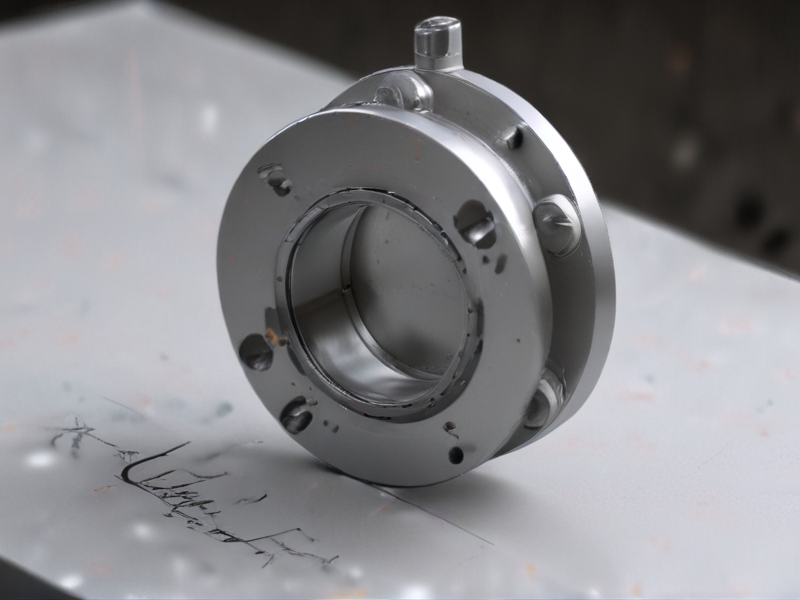
The Work Process and how to use flanged valve
Work Process of Using a Flanged Valve
1. Selection:
– Determine Requirements: Identify the type of fluid, pressure, temperature, and flow rate.
– Choose Material: Select valve material suitable for the fluid and operating conditions.
– Select Valve Type: Decide on the appropriate valve type (e.g., gate, ball, butterfly) based on the application.
2. Preparation:
– Inspection: Check the valve for any damage or defects.
– Clean Flanges: Ensure both the valve and pipe flanges are clean and free of debris.
– Gasket Preparation: Select appropriate gaskets and ensure they are in good condition.
3. Installation:
– Align Valve and Piping: Ensure proper alignment between the valve and the piping system.
– Insert Gaskets: Place gaskets between the flanges to ensure a tight seal.
– Bolt Tightening: Insert bolts and tighten them gradually in a crisscross pattern to ensure even pressure distribution and prevent leaks.
– Torque Specification: Follow manufacturer’s recommended torque specifications for the bolts.
4. Operation:
– Open/Close Slowly: Operate the valve slowly to prevent water hammer and system shocks.
– Check for Leaks: Inspect the flanges and joints for any leaks once the valve is in operation.
– Adjust as Needed: Make any necessary adjustments to ensure the valve operates smoothly and seals correctly.
5. Maintenance:
– Regular Inspection: Periodically check the valve for wear, corrosion, and proper function.
– Lubrication: Apply appropriate lubrication to the valve stem and other moving parts as needed.
– Replace Gaskets/Bolts: Replace gaskets, bolts, and other components as they wear out to maintain the integrity of the valve.
Safety Tips:
– Wear Protective Gear: Use safety equipment like gloves, goggles, and hard hats.
– Follow Procedures: Adhere to standard operating procedures and safety guidelines.
– De-energize System: Ensure the system is depressurized and de-energized before working on the valve.
By following these steps, the installation and maintenance of a flanged valve can be performed efficiently and safely.
flanged valve Importing questions including Cost,Supplier,Sample,Certification and Market
Importing Flanged Valves: Key Considerations
1. Cost
– Unit Price: Varies based on material, size, and specifications.
– Shipping: Includes freight, duties, and insurance. Sea freight is cheaper but slower than air freight.
– Customs: Import duties and taxes can significantly affect total cost.
2. Supplier
– Selection: Evaluate manufacturers based on reputation, compliance, and quality.
– Verification: Conduct due diligence through reviews, audits, and compliance checks.
– Terms: Negotiate payment terms, warranties, and return policies.
3. Sample
– Requesting: Ask for samples to assess quality, specifications, and compatibility.
– Evaluation: Inspect for compliance with required standards and dimensions.
– Cost: Samples might be free but expect to pay for shipping.
4. Certification
– Standards: Ensure valves meet international standards (e.g., ISO, API).
– Documentation: Require certification for materials, pressure ratings, and testing.
– Compliance: Check for adherence to local regulations in the importing country.
5. Market
– Demand: Analyze market demand to determine the volume and types of valves needed.
– Competition: Understand competitors and pricing to position your product effectively.
– Regulations: Stay updated on regulatory changes that could affect market dynamics.
Thorough research and careful planning in these areas will ensure a smooth importing process for flanged valves.
How to find and select check reliable flanged valve manufacturers in China
To find and select reliable flanged valve manufacturers in China, follow these steps:
1. Research and List Potential Manufacturers: Use online platforms like Alibaba, Made-in-China, and Global Sources to find a list of manufacturers. Also, consider industry directories and trade shows like the Canton Fair.
2. Check Company Background: Look for companies with a long history and a solid reputation. Verify their business licenses, certifications (ISO, CE), and any industry awards. Websites like China’s National Enterprise Credit Information Publicity System can be useful.
3. Evaluate Product Quality: Request product catalogs and specifications. Ensure the manufacturer complies with international standards (ANSI, API, DIN). Ask for sample products to assess quality firsthand.
4. Verify Factory Capabilities: Check if the manufacturer owns advanced production facilities and has a capacity that meets your needs. Visiting the factory, if possible, is ideal. Alternatively, use third-party inspection services.
5. Review References and Customer Feedback: Ask for references from other international clients and read reviews. Online forums and business networks can provide additional insights into the manufacturer’s reputation.
6. Assess Communication and Responsiveness: Reliable manufacturers should have good communication skills and be responsive to your inquiries. This is crucial for ongoing support and resolving any issues that might arise.
7. Negotiate Terms and Conditions: Discuss and agree on terms of trade, including payment methods, delivery schedules, warranty, and after-sales service. Ensure these are clearly outlined in a contract.
8. Consider Third-Party Audits: Engage third-party audit services like SGS, Bureau Veritas, or TUV to perform factory audits and product inspections. This ensures compliance with your quality standards and requirements.
By following these steps, you can find and select reliable flanged valve manufacturers in China, ensuring a smooth and productive business relationship.
Background Research for flanged valve manufacturers Companies in China, use qcc.com archive.org importyeti.com
Several prominent manufacturers in China specialize in the production of flanged valves. Here’s an overview of some key companies:
1. Suzhou Neway Valve Co., Ltd.: Founded in 2002, Suzhou Neway Valve is a significant player in the valve manufacturing industry, located in Suzhou, Jiangsu Province. The company has a large workforce and is known for its comprehensive range of valve products, including flanged valves.
2. Jiangsu Jiulong Valve Manufacturing Co., Ltd.: Established in 2001, this company is situated in Yancheng, Jiangsu Province. It is notable for its robust manufacturing capabilities and a diverse range of valve products, including specialized flanged valves.
3. Wuxi Jingdeng Automatic Valve Co., Ltd.: Operating since 2006, this company is based in Wuxi, Jiangsu Province. Although it is a smaller entity in terms of employee size, it is recognized for its expertise in manufacturing various automatic valves.
4. Trimex Fluid Technology (Suzhou) Co., Ltd.: Founded in 2006, Trimex, previously known as Weir Group Energy Equipment (Suzhou) Co., Ltd., specializes in fluid technology and various types of industrial valves, including flanged valves. The company operates out of Suzhou, Jiangsu Province, and has a moderate-sized workforce.
5. YF Valve (Suzhou) Co., Ltd.: This company, established in 2006, is located in Suzhou, Jiangsu Province. It focuses on manufacturing a range of valve products and has a solid reputation for quality and innovation in the valve industry.
These companies are well-established in their respective regions and contribute significantly to the valve manufacturing industry in China, offering a wide variety of flanged valves to meet diverse industrial needs.
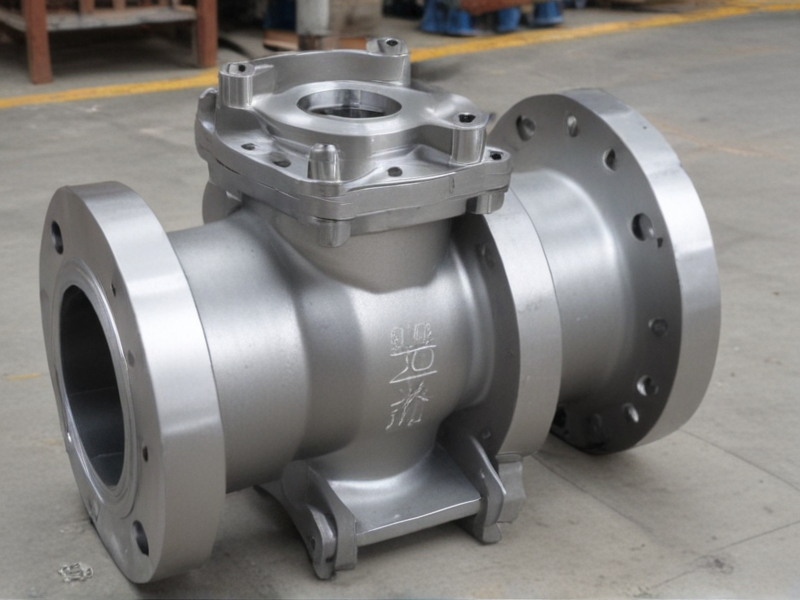
Price Cost Research for flanged valve manufacturers Companies in China, use temu.com and 1688.com
Here is a summary of the price and product details for flanged valve manufacturers in China from Temu and 1688:
Temu:
Temu lists a variety of flanged valves, with prices ranging based on specifications such as size, material, and pressure rating. For instance, a stainless steel flanged ball valve can range from $20 to $50 per unit, depending on the diameter and pressure class.
1688:
1688 provides detailed listings with numerous manufacturers offering flanged valves. Prices vary significantly:
– Hand-operated flanged butterfly valves: Prices range from approximately 300 RMB to 1000 RMB based on size (DN350 to DN1000).
– Flanged safety valves: Prices start around 150 RMB and can go up to 800 RMB depending on material (cast steel or brass) and size (DN50 to DN200).
For detailed product specifications and bulk purchase options, you can visit the respective platforms:
– [Temu](https://www.temu.com)
Shipping Cost for flanged valve import from China
When importing flanged valves from China, shipping costs depend on several factors, including the mode of transport (air, sea, or express), the weight and volume of the shipment, the shipping distance, and any additional fees or surcharges.
1. Mode of Transport
– Sea Freight: Cost-effective for large shipments, but slower (4-6 weeks). Average costs can range from $2 to $4 per kg.
– Air Freight: Faster (1-2 weeks) but more expensive, with costs typically ranging from $5 to $10 per kg.
– Express Shipping: The fastest option (3-7 days) but the most expensive, often exceeding $15 per kg.
2. Weight and Volume
– Shipping costs are calculated based on the greater of the actual weight or the volumetric weight. For heavy and bulky items like flanged valves, volumetric weight often plays a significant role.
3. Distance
– The distance between the origin port in China and the destination affects the cost. Longer distances or less frequented routes may incur higher costs.
4. Additional Fees
– Customs and Duties: Import duties vary by country and product classification.
– Handling Fees: Fees for loading, unloading, and handling at ports.
– Insurance: Optional but recommended to cover potential damages or losses during transit.
Example Calculation
For a 1000 kg shipment of flanged valves:
– Sea Freight: 1000 kg x $3/kg = $3000
– Air Freight: 1000 kg x $8/kg = $8000
– Express Shipping: 1000 kg x $18/kg = $18,000
Conclusion
Shipping costs for flanged valves from China vary significantly based on the transport mode and additional factors. Sea freight is cost-effective for large shipments, while air freight offers a balance between cost and speed. Express shipping, though fastest, is best suited for urgent and smaller shipments due to its high cost.
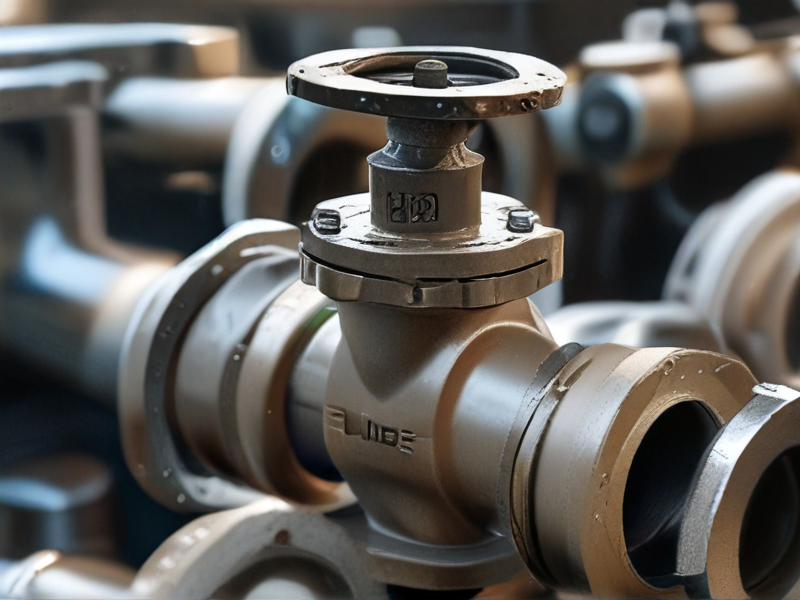
Compare China and Other flanged valve Markets: Products Quality and Price,Visible and Hidden Costs
China vs. Other Flanged Valve Markets:
1. Product Quality:
– China: Chinese flanged valves are often known for their cost-effectiveness but may vary in quality. Some manufacturers offer high-quality products comparable to international standards, while others may not meet the same rigor due to inconsistent manufacturing practices.
– Other Markets: Western and Japanese manufacturers generally maintain higher and more consistent quality standards, adhering to strict regulatory requirements and certifications (e.g., ISO, API). This results in more reliable and durable products.
2. Price:
– China: Chinese flanged valves are typically more affordable due to lower labor costs and economies of scale. However, the price range can be broad depending on the quality tier.
– Other Markets: Valves from Western and Japanese markets tend to be more expensive, reflecting higher production costs, advanced technology, and premium quality materials.
3. Visible and Hidden Costs:
– China: While the upfront cost is lower, hidden costs can include higher failure rates, more frequent maintenance, and potential shipping delays. Quality control issues may also lead to increased replacement costs and downtime.
– Other Markets: Higher initial costs are offset by lower maintenance and replacement expenses, fewer operational disruptions, and better customer service. The durability and reliability of these valves can reduce the total cost of ownership over time.
In summary, choosing between Chinese and other flanged valve markets involves a trade-off between initial costs and long-term reliability. Chinese valves offer affordability but may come with quality variability and higher hidden costs. In contrast, valves from Western and Japanese manufacturers provide superior quality and reliability, often justifying their higher prices through lower total lifecycle costs.
Custom Private Labeling and Branding Opportunities with Chinese flanged valve Manufacturers
Engaging in custom private labeling and branding with Chinese flanged valve manufacturers offers significant advantages for businesses seeking to establish or expand their product lines. Here’s a concise overview of the opportunities:
1. Cost Efficiency: Chinese manufacturers are known for their competitive pricing due to lower labor costs and economies of scale. This enables businesses to procure high-quality flanged valves at a reduced cost, enhancing profit margins.
2. Customization: Many Chinese valve manufacturers offer extensive customization options. Businesses can work closely with these manufacturers to design valves that meet specific requirements, including size, material, pressure ratings, and finishes, ensuring that the products align perfectly with their brand’s identity and customer needs.
3. Quality Assurance: Reputable Chinese manufacturers adhere to international standards (e.g., ISO, API) and employ stringent quality control measures. This ensures that the custom-labeled valves meet global industry standards, providing reliability and durability.
4. Advanced Technology: China has made significant advancements in manufacturing technology. Modern facilities equipped with the latest machinery and processes enable the production of innovative and efficient valve designs, which can be leveraged for branding as cutting-edge products.
5. Speed to Market: Leveraging Chinese manufacturers’ capabilities can significantly reduce the time from design to market. The efficient production processes and logistics networks in China help in faster turnaround times, allowing businesses to quickly respond to market demands.
6. Branding Opportunities: Custom private labeling allows companies to establish a unique brand presence in the market. With personalized logos, packaging, and product specifications, businesses can differentiate themselves from competitors and build brand loyalty.
7. Global Reach: Partnering with Chinese manufacturers can open up access to their global distribution networks. This collaboration can facilitate easier entry into new markets and expand the reach of branded products.
In summary, collaborating with Chinese flanged valve manufacturers for custom private labeling and branding provides a strategic advantage through cost efficiency, high-quality products, customization, and rapid market entry, all of which contribute to enhanced brand presence and competitiveness.
Tips for Procurement and Considerations when Purchasing flanged valve
When procuring flanged valves, consider the following tips and key considerations to ensure a successful purchase:
Tips for Procurement
1. Identify Requirements: Clearly define the operational requirements, including pressure, temperature, and fluid type. This will help in selecting the appropriate valve material and design.
2. Supplier Research: Choose reputable suppliers with a track record of quality and reliability. Look for certifications like ISO or API to ensure product standards.
3. Budgeting: Understand the total cost of ownership, including purchase price, installation, maintenance, and potential downtime costs.
4. Compliance: Ensure the valve meets industry standards and regulatory requirements relevant to your application.
5. Lead Time: Consider the lead time for manufacturing and delivery. Plan procurement in advance to avoid project delays.
6. Technical Support: Prefer suppliers that offer strong technical support and after-sales service for troubleshooting and maintenance.
Considerations When Purchasing
1. Material Compatibility: Ensure the valve material is compatible with the process fluid to prevent corrosion and wear. Common materials include stainless steel, cast iron, and carbon steel.
2. Pressure and Temperature Ratings: Select a valve that can withstand the maximum operating pressure and temperature of your system.
3. Valve Type: Choose the appropriate type of flanged valve (e.g., gate, globe, ball, butterfly) based on the required control and isolation needs.
4. End Connections: Verify the flange type and size match your piping system standards (e.g., ANSI, DIN, JIS).
5. Actuation: Decide between manual, electric, pneumatic, or hydraulic actuation based on the automation level of your system.
6. Maintenance: Consider ease of maintenance and availability of spare parts. Valves that are easy to service can reduce downtime.
7. Documentation: Ensure all technical documentation, including datasheets, installation manuals, and compliance certificates, are provided.
By carefully considering these tips and factors, you can make informed decisions that enhance the efficiency, reliability, and longevity of your flanged valve installations.
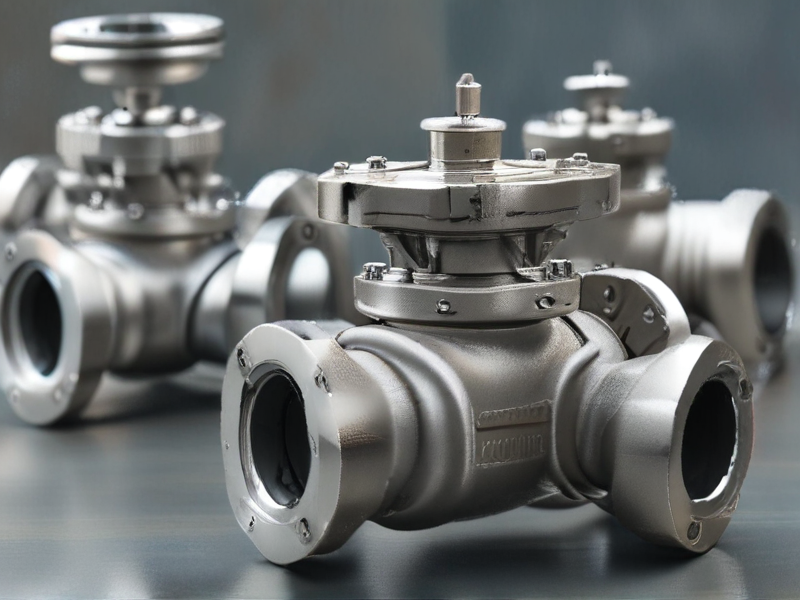
FAQs on Sourcing and Manufacturing flanged valve in China
FAQs on Sourcing and Manufacturing Flanged Valves in China
1. Why source flanged valves from China?
China is a leading global manufacturing hub known for competitive pricing, vast production capacity, and advancements in technology. Many Chinese manufacturers offer high-quality flanged valves that meet international standards.
2. How to find reliable manufacturers?
Utilize online directories like Alibaba, Made-in-China, and Global Sources. Attend trade shows such as the Canton Fair and valve-specific expos. Networking with industry contacts and conducting on-site visits also helps in verifying manufacturers’ credibility.
3. What are the common types of flanged valves available?
Flanged valves include gate valves, globe valves, ball valves, butterfly valves, and check valves. These come in various materials like stainless steel, cast iron, carbon steel, and more, catering to different industrial needs.
4. What standards do Chinese manufacturers follow?
Reputable manufacturers adhere to international standards such as ANSI, API, DIN, and JIS. It is crucial to confirm compliance with these standards to ensure product quality and compatibility.
5. How to ensure quality control?
Implement rigorous quality control measures such as third-party inspections, factory audits, and pre-shipment inspections. Request sample products for testing before placing bulk orders.
6. What is the typical lead time for production?
Lead times can vary but generally range from 30 to 60 days depending on the order size, complexity, and the manufacturer’s production schedule. Customizations may extend lead times.
7. How to handle logistics and shipping?
Manufacturers typically handle shipping arrangements. Ensure clear agreements on Incoterms (e.g., FOB, CIF). Partner with reliable freight forwarders and consider insurance for added security.
8. Are there any language barriers?
Many Chinese manufacturers have English-speaking sales representatives. However, clear communication, written agreements, and understanding cultural nuances are vital to avoid misunderstandings.
9. What about payment terms?
Common payment methods include T/T (Telegraphic Transfer), L/C (Letter of Credit), and sometimes Escrow services. Negotiate terms to balance security and cash flow management.
10. What are the risks and how to mitigate them?
Risks include quality issues, delays, and communication barriers. Mitigate them by working with established manufacturers, conducting thorough research, and maintaining consistent communication.