Top 10 flange valve in China introduce,list main products and website if have
Here are the top 10 flange valve manufacturers in China, along with their main products and websites:
1. Neway Valve (Suzhou) Co., Ltd.
– Main Products: Gate valves, globe valves, check valves, ball valves, butterfly valves, control valves, safety valves, and nuclear power valves.
– Website: [Neway Valve](https://www.newayvalve.com)
2. Xintai Valve Group Co., Ltd.
– Main Products: Gate valves, globe valves, check valves, ball valves, and butterfly valves.
– Website: [Xintai Valve](https://www.xintaivalves.com)
3. Shanghai Valve Factory Co., Ltd.
– Main Products: Gate valves, ball valves, and butterfly valves.
– Website: [Shanghai Valve Factory](http://www.shvalve.com)
4. CNNC Sufa Technology Industry Co., Ltd.
– Main Products: Nuclear valves, control valves, and safety valves.
– Website: [CNNC Sufa](http://www.sufa-cn.com)
5. Zhejiang Zhedong Valve Co., Ltd.
– Main Products: Gate valves, globe valves, and butterfly valves.
– Website: [Zhedong Valve](http://www.zdv.cn)
6. Jiangnan Valve Co., Ltd.
– Main Products: Butterfly valves and other industrial valves.
– Website: [Jiangnan Valve](http://www.jnvalve.com)
7. Beijing Valve General Factory
– Main Products: Various industrial valves including gate and globe valves.
– Website: Not available.
8. Huangshan Industrial Pump & Valve Co., Ltd.
– Main Products: Globe valves, check valves, and diaphragm valves.
– Website: [Huangshan Valve](http://www.huangshanvalve.com)
9. China Valve Technology Co., Ltd.
– Main Products: Ball valves, butterfly valves, and plug valves.
– Website: [China Valve Technology](http://www.chinavalve.com.cn)
10. Zhejiang Petrochemical Valve Co., Ltd.
– Main Products: Various valves for the petrochemical industry.
– Website: Not available.
These companies are recognized for their extensive product ranges, innovative designs, and adherence to international standards, making them key players in the global valve market.
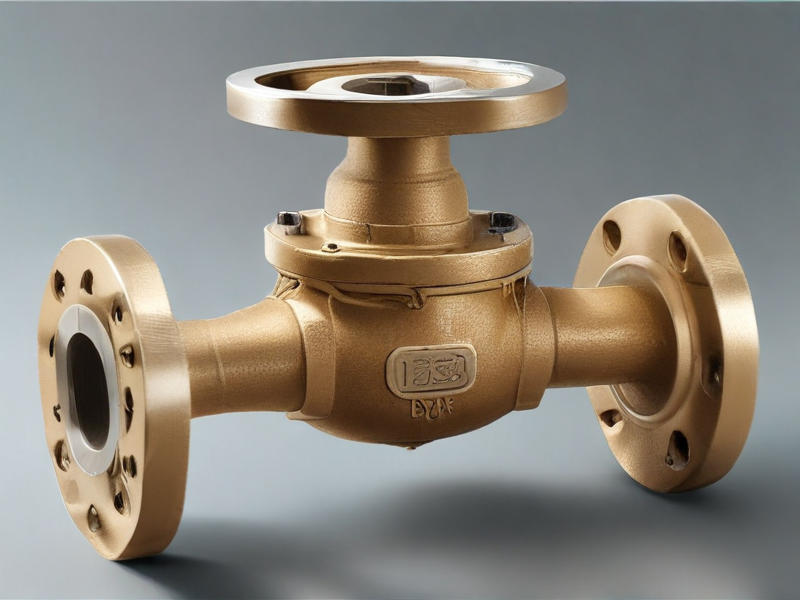
Types of flange valve
Flange valves, crucial in fluid control systems, come in various types, each tailored for specific applications:
1. Gate Valve: Known for their straight-through flow and minimal restriction, gate valves are ideal for on/off control. They operate by lifting a gate out of the path of the fluid.
2. Globe Valve: Designed for throttling and regulating flow, globe valves use a movable disk and a stationary ring seat in a spherical body. They offer precise control but create more flow resistance than gate valves.
3. Ball Valve: Featuring a spherical disc to control flow, ball valves provide reliable shutoff and can handle high pressures and temperatures. They offer quick quarter-turn operation.
4. Butterfly Valve: Lightweight and compact, butterfly valves use a rotating disc to regulate flow. They are suitable for large valve applications and offer quick operation with low pressure drops.
5. Check Valve: Check valves allow flow in one direction and prevent backflow. They are automatic and do not require any external control, making them essential for preventing reverse flow in pipelines.
6. Needle Valve: Used for precise flow control, needle valves have a small port and a threaded, needle-like plunger. They are ideal for metering applications.
7. Diaphragm Valve: Utilizing a flexible diaphragm that presses down onto a seat, diaphragm valves are suitable for handling corrosive and abrasive fluids. They provide excellent leak tightness.
8. Plug Valve: Similar to ball valves but with a cylindrical or tapered plug, plug valves are used for quick shutoff and moderate throttling. They are durable and suitable for high-pressure applications.
9. Pinch Valve: Employing a pinching mechanism to control fluid flow, pinch valves are ideal for slurry and granular applications, offering full bore flow with no obstruction.
Each type of flange valve has distinct characteristics making it suitable for specific industrial applications, ensuring efficient and reliable fluid control.
Pros and Cons of Using flange valve
Pros and Cons of Using a Flange Valve
Pros:
1. Ease of Installation and Maintenance:
– Flange valves are easier to install and remove compared to other types, facilitating quicker maintenance and replacement.
2. Reliable Sealing:
– The bolted connections on flange valves provide a more reliable and tight seal, reducing the risk of leaks.
3. Versatility:
– Available in various materials, sizes, and pressure ratings, flange valves can be used in a wide range of applications, from water to high-pressure gas systems.
4. Strength and Durability:
– Flange valves are robust and can withstand higher pressures and temperatures, making them suitable for demanding environments.
5. Ease of Alignment:
– The flange connections allow for better alignment of the valve with the pipeline, improving the overall system integrity.
Cons:
1. Higher Cost:
– Flange valves are generally more expensive due to their design and the need for additional components like flanges and bolts.
2. Complex Installation:
– Although removal and maintenance are easier, the initial installation can be more complex and time-consuming due to the need for precise alignment and tightening of multiple bolts.
3. Space Requirements:
– Flange valves typically require more space for installation and operation compared to other valve types, which can be a limitation in compact systems.
4. Potential for Leaks:
– While the bolted connections offer a strong seal, improper installation or maintenance can lead to leaks at the flange connections.
5. Weight:
– Flange valves are generally heavier, which can be a drawback in applications where weight is a critical factor.
Overall, flange valves offer significant advantages in terms of durability, reliability, and ease of maintenance, but they come with higher costs and potential installation challenges. These factors need to be considered based on the specific requirements of the application.
flange valve Reference Specifications (varies for different product)
Flange Valve Reference Specifications
Materials:
– Body and Bonnet: Typically made from cast iron, carbon steel, stainless steel, or ductile iron.
– Seat and Disc: Materials can include stainless steel, bronze, or other corrosion-resistant alloys.
– Stem: Often made from stainless steel or high-strength alloy.
Design Standards:
– ASME B16.5: Standard for pipe flanges and flanged fittings.
– API 600: Standard for steel gate valves, flanged and butt-welding ends.
– ISO 5211: Mounting pad dimensions for part-turn actuators.
Pressure Ratings:
– Class 150, 300, 600, 900, 1500, 2500: Designated by ASME pressure class, defining maximum allowable pressure.
– PN10, PN16, PN25, PN40: Pressure ratings per European standards.
Temperature Ratings:
– Valves are rated for a wide temperature range, typically from -20°F to 1000°F (-29°C to 538°C), depending on materials used.
End Connections:
– Flanged: Raised Face (RF), Flat Face (FF), Ring Type Joint (RTJ) per ASME B16.5.
– Size Range: Typically from ½ inch to 24 inches (15mm to 600mm).
Operation:
– Manual: Handwheel or lever.
– Automated: Electric, pneumatic, or hydraulic actuators.
Types of Flange Valves:
– Gate Valves: Used for on/off control, not suitable for throttling.
– Globe Valves: Designed for throttling and frequent operation.
– Ball Valves: Provide quick on/off control with minimal pressure drop.
– Butterfly Valves: Suitable for large volume applications with low pressure drop.
– Check Valves: Prevent backflow, ensuring unidirectional flow.
Testing:
– Hydrostatic Testing: Performed to verify strength and leakage integrity.
– Pneumatic Testing: Used for low-pressure applications to check for leaks.
Coatings and Linings:
– Epoxy, PTFE, and rubber linings: For corrosion and abrasion resistance.
Certification:
– API, ISO, CE, and PED: Ensuring compliance with international standards.
Applications:
– Industries: Oil and gas, water and wastewater, chemical, power generation, and pharmaceuticals.
Flange valves are essential components in fluid control systems, offering reliable operation, durability, and compliance with industry standards.
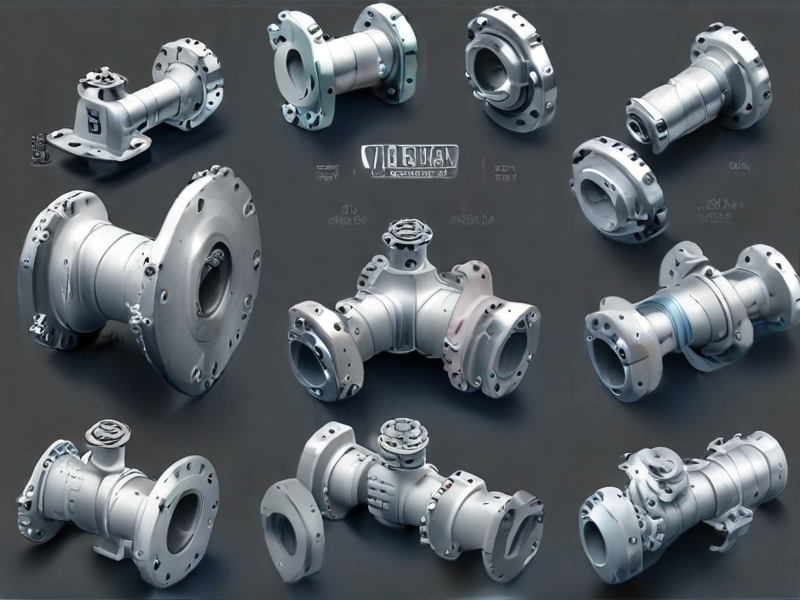
Applications of flange valve
Flange valves are widely used in various industries due to their robust design, easy installation, and secure sealing. Here are some key applications:
1. Oil and Gas Industry: Flange valves are critical in controlling the flow of crude oil and natural gas. They are used in pipelines, storage tanks, and processing facilities for their reliability under high pressure and temperature conditions.
2. Chemical Industry: In chemical plants, flange valves manage the flow of aggressive and corrosive fluids. Their design ensures safety and prevents leakage of hazardous materials, essential for maintaining operational safety standards.
3. Water Treatment Plants: These valves regulate water flow in treatment plants, ensuring efficient distribution and management of water resources. They are commonly used in pipelines, filtration systems, and reservoirs.
4. Power Generation: Flange valves are utilized in both conventional and nuclear power plants to control the flow of steam, water, and other fluids. Their ability to withstand extreme conditions makes them suitable for high-stress environments.
5. Pharmaceutical Industry: In pharmaceutical manufacturing, flange valves ensure precise control of fluids, contributing to maintaining hygiene and preventing contamination. Their easy-to-clean design is vital for maintaining strict sanitary standards.
6. HVAC Systems: Heating, ventilation, and air conditioning systems use flange valves to regulate air and fluid flow, enhancing the efficiency and reliability of climate control systems in residential, commercial, and industrial settings.
7. Food and Beverage Industry: These valves are used in processing plants to manage the flow of ingredients and cleaning fluids. Their sanitary design is crucial for complying with health and safety regulations.
In summary, flange valves are versatile components essential for various applications across industries, providing reliable, safe, and efficient flow control under diverse operational conditions.
Material of flange valve
Flange valves are crucial components in piping systems, used to control the flow of liquids and gases. The material selection for flange valves is critical to ensure they can withstand the operational conditions, including pressure, temperature, and the chemical nature of the fluid.
Common Materials for Flange Valves:
1. Cast Iron: Used for low-pressure and non-corrosive applications, cast iron offers good machinability and cost-effectiveness. It is suitable for water and steam applications but has limitations in terms of pressure and temperature.
2. Ductile Iron: An upgrade over cast iron, ductile iron provides better strength and toughness, making it suitable for higher pressure applications. It is commonly used in water supply and wastewater treatment systems.
3. Carbon Steel: This material is popular for its high strength and versatility, handling higher pressures and temperatures than cast iron. Carbon steel is often used in oil, gas, and petrochemical industries.
4. Stainless Steel: Known for its corrosion resistance, stainless steel is ideal for aggressive environments, including chemical processing, food and beverage industries, and pharmaceuticals. Common grades include 304 and 316 stainless steel, with 316 offering superior resistance to chloride environments.
5. Alloy Steels: These are used for high-temperature and high-pressure applications. Examples include chrome-molybdenum steels which provide excellent strength and resistance to thermal stress and oxidation.
6. Bronze: Known for its corrosion resistance and durability, bronze is often used in marine environments, desalination plants, and for handling water and non-corrosive fluids.
7. Plastic (PVC, CPVC, PVDF): These materials are used for their chemical resistance and cost-effectiveness in low-pressure and low-temperature applications. They are ideal for water treatment, chemical handling, and corrosive fluids.
Selection Criteria:
– Operational Pressure and Temperature: Ensures the material can handle the system’s demands.
– Corrosion Resistance: Essential for durability in aggressive chemical environments.
– Mechanical Strength: Needed for structural integrity and long-term performance.
– Cost: Balancing performance requirements with budget constraints.
Choosing the appropriate material for flange valves is essential for the reliability and efficiency of the piping system.
Quality Testing Methods for flange valve and how to control the quality
Quality Testing Methods for Flange Valve:
1. Visual Inspection: Check for surface defects, cracks, and proper markings. Ensure that the flange valve meets the specified standards and dimensions.
2. Dimensional Verification: Use calipers, micrometers, and gauges to measure dimensions and ensure they conform to design specifications.
3. Pressure Testing:
– Hydrostatic Test: Test the valve under water pressure to check for leaks and structural integrity.
– Pneumatic Test: Use air or gas pressure to detect leaks and verify the sealing performance.
4. Non-Destructive Testing (NDT):
– Ultrasonic Testing: Detect internal flaws and material integrity.
– Radiographic Testing (X-ray): Identify internal defects such as voids or cracks.
– Magnetic Particle Testing: Detect surface and near-surface discontinuities in ferromagnetic materials.
5. Functional Testing: Operate the valve to ensure it opens and closes correctly, and check the torque and operational smoothness.
6. Material Testing:
– Chemical Analysis: Verify the material composition to ensure it meets the specified alloy requirements.
– Mechanical Testing: Test the tensile strength, hardness, and impact resistance.
Quality Control Measures:
1. Quality Assurance Plan (QAP): Develop a comprehensive QAP outlining all inspection and testing procedures, acceptance criteria, and documentation requirements.
2. Standard Operating Procedures (SOPs): Implement SOPs for each testing method and ensure all technicians are trained to follow them.
3. Inspection and Test Records: Maintain detailed records of all inspections and tests to trace the history of each valve.
4. Third-Party Certification: Engage independent third-party inspectors to verify compliance with industry standards and specifications.
5. Statistical Process Control (SPC): Use SPC techniques to monitor manufacturing processes and identify variations that could affect quality.
6. Corrective and Preventive Actions (CAPA): Implement CAPA systems to address non-conformities and prevent recurrence.
7. Continuous Improvement: Regularly review and update quality control processes based on feedback and technological advancements.
By implementing these methods and controls, manufacturers can ensure that flange valves meet the highest quality standards and performance requirements.
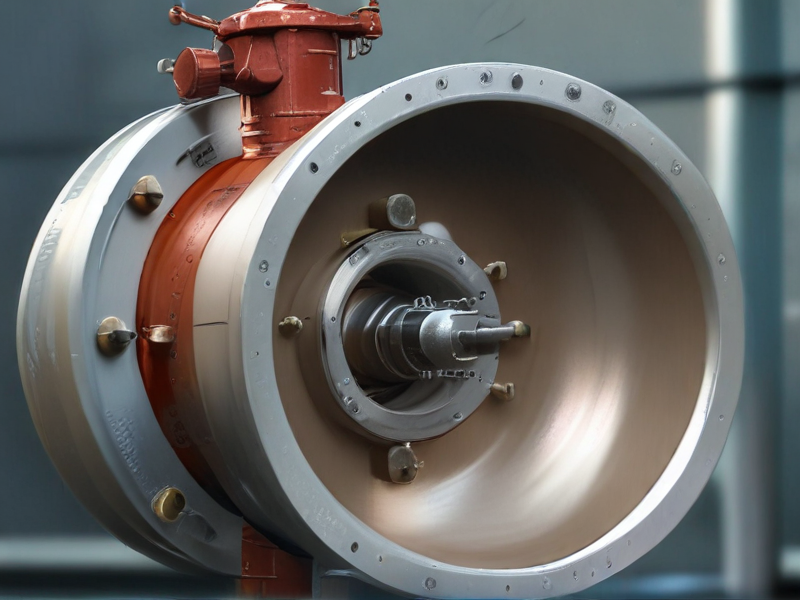
The Work Process and how to use flange valve
Work Process of Using a Flange Valve
1. Preparation
– Safety Gear: Wear appropriate personal protective equipment (PPE) including gloves, goggles, and protective clothing.
– Inspection: Check the flange valve for any visible damage or defects.
– Cleaning: Ensure the flanges and pipeline ends are clean and free of debris.
2. Alignment and Positioning
– Align Flanges: Position the valve flanges with the pipeline flanges ensuring proper alignment.
– Gasket Placement: Place a gasket between the flanges to ensure a proper seal.
3. Bolting
– Insert Bolts: Insert bolts through the aligned flange holes.
– Tighten Bolts: Hand-tighten bolts initially in a crisscross pattern to evenly distribute pressure.
– Torque Bolts: Use a torque wrench to tighten bolts to the manufacturer’s specified torque in the same crisscross pattern.
4. Operation Check
– Open/Close Test: Operate the valve by opening and closing it to ensure smooth functionality and no obstructions.
– Leak Test: Pressurize the system and check for leaks around the flanges and valve body.
5. Final Adjustments
– Adjust Bolts: Re-tighten bolts if necessary to stop any minor leaks.
– Secure Valve: Ensure the valve is securely fastened and operates without issues.
How to Use a Flange Valve
1. Opening the Valve
– Turn the valve handle or operate the actuator (if automated) counterclockwise to open the valve, allowing fluid to flow through the pipeline.
2. Closing the Valve
– Turn the valve handle or operate the actuator clockwise to close the valve, stopping the fluid flow.
3. Maintenance
– Periodically inspect the valve for leaks, wear, or damage.
– Clean and lubricate the valve as needed, following the manufacturer’s guidelines.
Using these steps ensures safe and effective use of flange valves in various industrial applications.
flange valve Importing questions including Cost,Supplier,Sample,Certification and Market
When importing flange valves, consider the following key factors:
1. Cost:
– Unit Price: Prices vary depending on the valve type, size, material, and manufacturer. Bulk orders often reduce unit costs.
– Shipping and Handling: Factor in international shipping rates, customs duties, and insurance.
– Hidden Costs: Be aware of costs related to compliance, documentation, and potential tariffs.
2. Supplier:
– Reputation: Research potential suppliers’ reputations, reviews, and references. Alibaba, Global Sources, and Made-in-China are good starting points.
– Location: Consider proximity to minimize shipping costs and time.
– Communication: Ensure the supplier is responsive and communicates clearly.
3. Sample:
– Requesting Samples: Before placing a large order, request samples to verify quality and specifications.
– Sample Costs: Some suppliers may charge for samples, while others may provide them for free or at a reduced cost.
4. Certification:
– Quality Standards: Ensure the valves meet international standards such as ISO, API, or ASME.
– Compliance: Verify that the supplier’s products comply with local regulations in your market.
– Documentation: Obtain all necessary certification documents to avoid customs issues.
5. Market:
– Demand: Research the demand for flange valves in your target market to ensure profitability.
– Competition: Analyze competitors to understand pricing strategies and market positioning.
– Trends: Stay informed about industry trends and innovations to meet market needs effectively.
By considering these factors, you can make informed decisions, mitigate risks, and optimize the import process for flange valves.
How to find and select check reliable flange valve manufacturers in China
Finding and selecting reliable flange valve manufacturers in China involves a few strategic steps:
1. Research and Compile a List: Start by researching online directories and trade websites such as Alibaba, Made-in-China, and Global Sources. Look for manufacturers specializing in flange valves and compile a list of potential suppliers.
2. Check Certifications: Verify that the manufacturers have relevant certifications such as ISO 9001, CE, and API, indicating their adherence to international quality standards.
3. Evaluate Experience: Look for manufacturers with extensive experience in producing flange valves. A company with a long history is more likely to have refined its production processes and quality control.
4. Assess Reputation: Read reviews and testimonials from other buyers. Check ratings on platforms like Alibaba, and look for any red flags or consistent complaints.
5. Request Samples: Ask for samples to evaluate the quality of their products firsthand. This will give you an idea of their manufacturing capabilities and product consistency.
6. Visit the Factory: If possible, arrange a visit to the factory to inspect their facilities, production processes, and quality control measures. This provides a more comprehensive understanding of their operations.
7. Review Communication and Support: Assess how responsive and supportive the manufacturer is during your inquiries. Good communication is crucial for addressing any issues that might arise during production or shipping.
8. Compare Pricing and MOQs: Compare prices and minimum order quantities (MOQs) from different manufacturers. Ensure the pricing aligns with your budget without compromising on quality.
9. Verify Legal Compliance: Ensure the manufacturer complies with local and international regulations. This includes environmental regulations and labor laws.
10. Seek References: Ask the manufacturer for references from other clients. Contact these clients to get feedback on their experiences.
By following these steps, you can systematically identify and select reliable flange valve manufacturers in China.
Background Research for flange valve manufacturers Companies in China, use qcc.com archive.org importyeti.com
Research on Flange Valve Manufacturers in China
Henan Gaoshan Valve Co., Ltd.
Henan Gaoshan Valve Co., Ltd., established in 2001, is located in Zhengzhou, Henan Province. The company specializes in the manufacturing and sale of valves, castings, and firefighting pumps. It is recognized for its robust production capabilities and significant market presence. The company’s registered capital is approximately 100.6 million RMB. It employs between 100 and 199 people, indicating a medium-scale operation. The firm is engaged in both domestic sales and international trade of its products and technologies.
Qingdao Bitron Electronic Co., Ltd.
Qingdao Bitron Electronic Co., Ltd., founded in 2012, operates in Qingdao, Shandong Province. Although primarily involved in manufacturing automotive components and home appliances, it also engages in the production of valves and related equipment. The company is a subsidiary of Bitron Industrie S.P.A., an Italian firm. With a registered capital of 16.07 million USD, it employs around 600 to 699 people. This indicates a significant scale of operations, with robust capabilities in both production and research and development.
Sinopec Valve Co., Ltd.
Sinopec Valve Co., Ltd., another notable player, focuses on the production of various types of industrial valves, including flange valves. The company benefits from its association with Sinopec, one of China’s largest state-owned enterprises, providing it with substantial financial backing and market reach. The company’s extensive experience and adherence to international standards make it a reliable supplier in both domestic and international markets.
These companies highlight the diverse capabilities and scales of operations within the Chinese flange valve manufacturing sector, from medium-sized firms to subsidiaries of large multinational corporations.
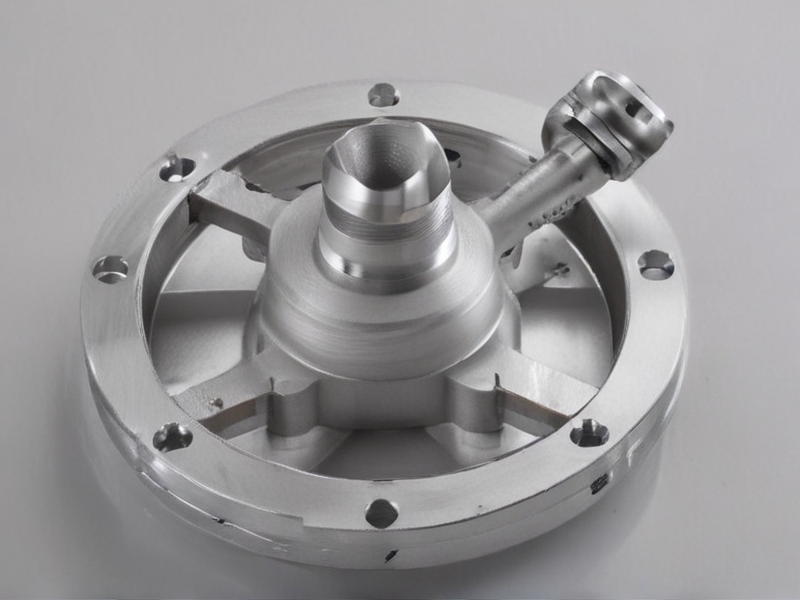
Price Cost Research for flange valve manufacturers Companies in China, use temu.com and 1688.com
When researching the prices and cost of flange valves from manufacturers in China on sites like Temu and 1688, here’s what I found:
Temu.com:
Temu offers a variety of industrial products, including flange valves. The prices vary widely depending on the specifications such as size, material, and pressure rating. For instance, basic models can start as low as $10, while more specialized or larger valves can go up to several hundred dollars. Temu focuses on providing wholesale prices which are competitive, often with additional discounts for bulk purchases and offers free standard shipping on most orders.
1688.com:
1688.com, being a part of the Alibaba Group, features numerous suppliers of flange valves. Prices here also depend heavily on the type and specifications. Simple, smaller valves can be found for as little as ¥20 (approximately $3), while larger or more specialized valves can range from ¥100 to ¥1000 (approximately $15 to $150). Many listings on 1688 also offer bulk discounts, which can significantly reduce the per-unit cost for large orders.
For detailed and specific pricing, visiting the respective product pages on these platforms will provide the most accurate and up-to-date information. The product range is vast, catering to different industrial needs and specifications.
Shipping Cost for flange valve import from China
Importing a flange valve from China involves several cost components: the product cost, shipping cost, customs duties, taxes, and any additional fees related to importation.
1. Product Cost: The price of a flange valve can vary depending on the type, size, and material. On average, it ranges from $50 to $200 per unit.
2. Shipping Cost: Shipping costs depend on the weight, dimensions, and shipping method (air or sea). For a flange valve, sea freight is generally more cost-effective than air freight due to the valve’s weight and size.
– Sea Freight: Costs approximately $500-$1,000 for a standard 20-foot container, but individual item shipping can be lower. For a small shipment, expect around $100-$200 per valve.
– Air Freight: More expensive, ranging from $5 to $10 per kilogram. This method is quicker but generally not recommended for heavy items unless urgency is a factor.
3. Customs Duties and Taxes: These vary by country. For the U.S., import duty on flange valves can be around 2-5%. Additionally, there may be a Value Added Tax (VAT) or Goods and Services Tax (GST), depending on the destination country. For instance, in the EU, VAT is about 20%.
4. Additional Fees: Includes port fees, handling charges, and possible insurance costs. Port fees and handling can add another $50-$200, depending on the shipment size and destination.
Example Calculation:
– Product Cost: $100 per valve
– Sea Freight: $150 per valve
– Customs Duties: 3% of product cost ($3)
– VAT: 20% of product cost + duties ($20.60)
– Additional Fees: $50
Total Cost per Valve: $100 (product) + $150 (shipping) + $3 (duties) + $20.60 (VAT) + $50 (fees) = $323.60 per valve
These estimates can vary, so it’s advisable to get quotes from suppliers and logistics companies for accurate figures.
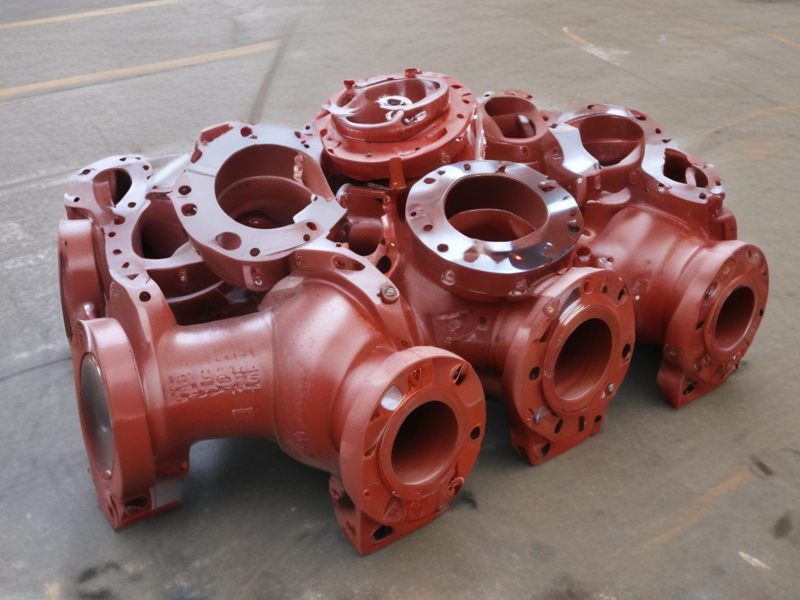
Compare China and Other flange valve Markets: Products Quality and Price,Visible and Hidden Costs
China and other flange valve markets, particularly from developed regions like Europe and the United States, exhibit distinct differences in product quality, price, and associated costs.
Product Quality:
Chinese flange valves have improved significantly, offering competitive performance, durability, and compliance with international standards. However, top-tier manufacturers in Europe and the U.S. are often perceived as superior in precision, material quality, and long-term reliability, supported by advanced engineering and stringent quality control.
Price:
Chinese flange valves are generally more cost-effective, benefiting from lower labor and production costs. European and U.S. valves, though higher in price, reflect the higher labor costs, advanced manufacturing processes, and extensive R&D investments.
Visible and Hidden Costs:
– Visible Costs: Initial purchase prices for Chinese valves are typically lower. European and U.S. valves command higher upfront costs due to better materials and technology.
– Hidden Costs:
– Chinese Valves: Potential hidden costs include shorter lifespans, more frequent maintenance, and potential issues with compatibility or compliance with local regulations. These factors can lead to higher long-term operational costs.
– European/U.S. Valves: While the initial price is higher, these valves often offer longer service life, reduced maintenance needs, and better overall performance, potentially lowering total cost of ownership over time. Additionally, these valves may come with comprehensive warranties and superior after-sales support.
Summary:
Choosing between Chinese and Western flange valves involves balancing initial costs against long-term performance and maintenance. Chinese valves provide cost efficiency and have steadily improved in quality, making them suitable for cost-sensitive projects. In contrast, valves from Europe and the U.S. offer higher reliability and durability, justifying their premium price through potentially lower long-term operational costs.
Custom Private Labeling and Branding Opportunities with Chinese flange valve Manufacturers
Custom private labeling and branding opportunities with Chinese flange valve manufacturers present significant benefits for businesses aiming to establish or enhance their market presence. Here’s an overview of these opportunities:
Cost-Effective Production
Chinese manufacturers are renowned for their cost-efficient production processes. They leverage economies of scale, advanced manufacturing technologies, and lower labor costs to offer competitive pricing without compromising quality.
Customization and Flexibility
Chinese flange valve manufacturers offer extensive customization options, including design modifications, material choices, and specific feature adjustments to meet unique customer requirements. This flexibility ensures that businesses can create products that align perfectly with their brand identity and technical specifications.
Advanced Manufacturing Capabilities
Many Chinese manufacturers are equipped with state-of-the-art machinery and employ rigorous quality control measures. They are capable of producing high-precision flange valves that adhere to international standards, ensuring reliability and performance.
Branding and Private Labeling Services
Chinese suppliers often provide comprehensive private labeling services, allowing businesses to have their logos, brand colors, and packaging designs on the products. This enhances brand recognition and loyalty among customers. They also assist with compliance documentation, certifications, and testing, facilitating smoother market entry.
Strategic Partnerships
Establishing long-term partnerships with Chinese manufacturers can lead to collaborative product development, innovation, and joint ventures. Such partnerships can result in unique product offerings and shared market insights, further strengthening a brand’s position in the market.
Market Expansion
Collaborating with Chinese manufacturers enables businesses to tap into new markets more effectively. With their extensive experience in global trade, these manufacturers can offer valuable logistical support, ensuring timely and efficient delivery of products worldwide.
In summary, partnering with Chinese flange valve manufacturers for custom private labeling and branding offers a cost-effective, flexible, and strategic approach to building and expanding a brand’s product portfolio and market presence.
Tips for Procurement and Considerations when Purchasing flange valve
When procuring flange valves, several key factors ensure you get the right product for your needs:
1. Material Compatibility: Ensure the valve material is compatible with the fluid it will handle. Common materials include stainless steel, cast iron, and brass, each suited to different applications and fluid types.
2. Pressure and Temperature Ratings: Verify the valve’s pressure and temperature ratings match your system requirements. Exceeding these ratings can lead to valve failure.
3. Valve Type: Choose the appropriate type of flange valve (e.g., ball, gate, butterfly, or globe) based on the application’s flow control needs. Each type has specific advantages and limitations.
4. Flange Standards: Check that the flange standards (e.g., ANSI, DIN, JIS) match your existing piping system to ensure proper fit and compatibility.
5. Size and Flow Capacity: Select the correct valve size for your system. Oversized or undersized valves can affect flow rates and system efficiency.
6. Actuation Method: Decide on the actuation method (manual, electric, pneumatic, or hydraulic) based on operational requirements and accessibility.
7. Quality and Certifications: Look for valves that meet industry standards and certifications (e.g., ISO, API). Quality assurance ensures reliability and longevity.
8. Supplier Reputation: Choose reputable suppliers with good track records. Reliable suppliers provide better customer support, warranty services, and often offer higher-quality products.
9. Maintenance and Repair: Consider the ease of maintenance and availability of spare parts. Valves that are easier to maintain can reduce downtime and operating costs.
10. Cost: While cost is a significant factor, it shouldn’t compromise quality and reliability. Consider the total cost of ownership, including installation, maintenance, and potential downtime costs.
By focusing on these considerations, you can ensure a successful procurement process, leading to efficient and reliable valve operation in your system.
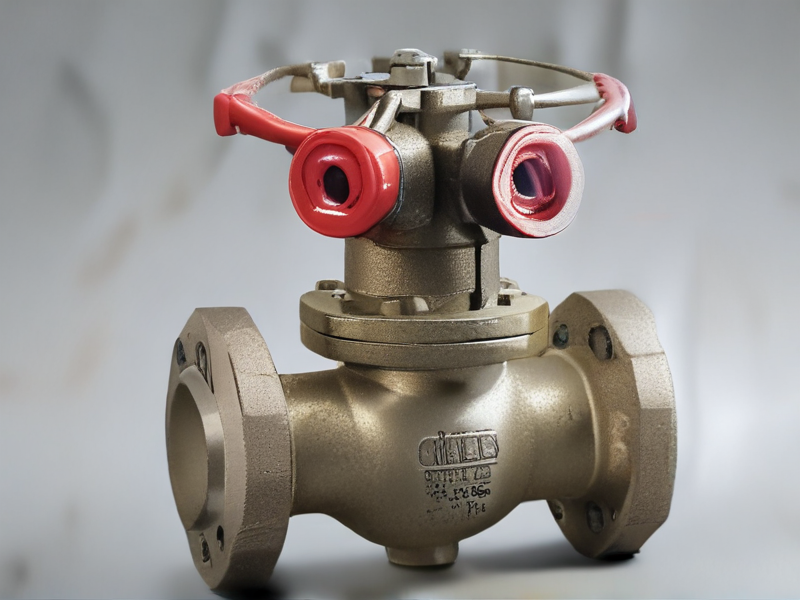
FAQs on Sourcing and Manufacturing flange valve in China
FAQs on Sourcing and Manufacturing Flange Valves in China
1. Why source flange valves from China?
China is a major manufacturing hub with cost-effective production, a wide range of suppliers, and advanced manufacturing technologies. This results in competitive pricing and high-quality products.
2. How to find reliable flange valve manufacturers in China?
Use online platforms like Alibaba and Made-in-China. Verify suppliers’ credentials through certifications like ISO 9001 and request references or visit trade shows for face-to-face interactions.
3. What are the key considerations when selecting a supplier?
Evaluate their manufacturing capabilities, quality control processes, lead times, and compliance with international standards. It’s crucial to ensure they have experience with the specific type of flange valve you need.
4. How to ensure product quality?
Request product samples and conduct third-party inspections. Implement stringent quality control agreements and periodically visit the factory to audit processes.
5. What are the typical lead times?
Lead times vary but typically range from 30 to 60 days. Custom orders may take longer, so it’s essential to communicate your timeline clearly with the supplier.
6. Are there any risks involved in sourcing from China?
Risks include potential language barriers, cultural differences, and quality inconsistencies. Mitigate these by establishing clear contracts, regular communication, and working with experienced freight forwarders for logistics.
7. What logistics considerations are important?
Choose between air or sea shipping based on cost and urgency. Work with reliable freight forwarders to handle customs clearance and ensure proper documentation to avoid delays.
8. How to handle intellectual property concerns?
Use non-disclosure agreements (NDAs) and register your patents in China to protect your designs and technology.
By addressing these key questions, you can effectively navigate the process of sourcing and manufacturing flange valves in China.