Top 10 filling machine bottle in China introduce,list main products and website if have
Here are ten leading bottle filling machine manufacturers in China, their main products, and websites:
1. Newamstar
– Main Products: Water, beverage, and dairy filling machines; aseptic cold filling lines.
– Website: [newamstar.com](http://www.newamstar.com/)
2. Jimei Machinery
– Main Products: Dairy, juice, water, and carbonated drink filling machines.
– Website: [jimeimachinery.com](http://www.jimeimachinery.com/)
3. Zhangjiagang King Machine
– Main Products: Water, juice, carbonated drink filling machines; labeling and packaging machines.
– Website: [king-machine.com](http://www.king-machine.com/)
4. Tech-Long
– Main Products: Beverage filling machines; blow molding machines; water treatment systems.
– Website: [tech-long.com](http://www.tech-long.com/)
5. Shanghai Leadworld Machinery
– Main Products: Liquid, powder, and granule filling machines; capping and labeling machines.
– Website: [leadworldmachinery.com](http://www.leadworldmachinery.com/)
6. Fillex Machinery
– Main Products: Water, juice, carbonated drink filling machines; labeling and packaging equipment.
– Website: [fillex-packer.com](http://www.fillex-packer.com/)
7. Zhangjiagang Evertop Machinery
– Main Products: Water, juice, and carbonated drink filling machines; packaging systems.
– Website: [evertop-machine.com](http://www.evertop-machine.com/)
8. Reliable Machinery
– Main Products: Liquid, beverage, and dairy filling machines; capping and labeling equipment.
– Website: [reliable-machine.com](http://www.reliable-machine.com/)
9. Zhangjiagang Best Machinery
– Main Products: Water, juice, carbonated drink filling machines; packaging solutions.
– Website: [bestcarmachines.com](http://www.bestcarmachines.com/)
10. Sunswell Machinery
– Main Products: Water, juice, carbonated drink, and oil filling machines; blow molding and packaging machines.
– Website: [sunswell.com](http://www.sunswell.com/)
These companies are renowned for their high-quality filling machines and comprehensive packaging solutions.
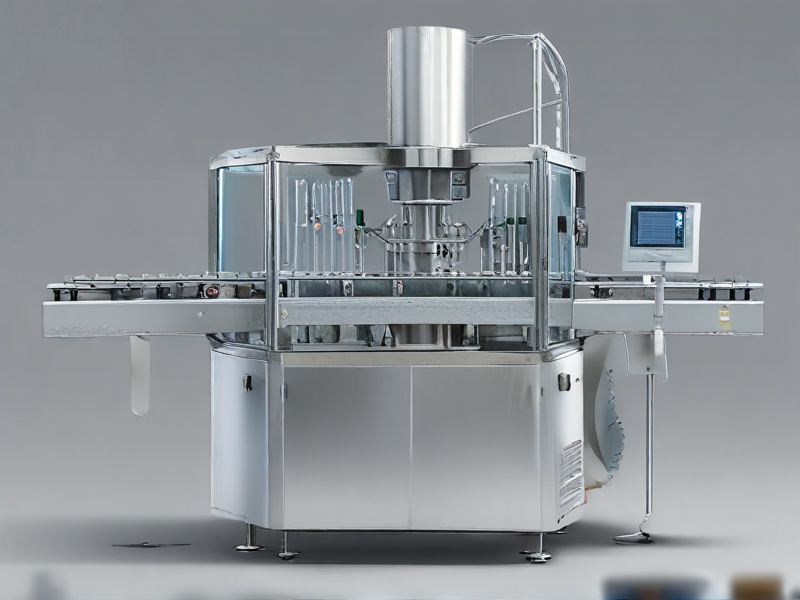
Types of filling machine bottle
Filling machines are essential in various industries for packaging liquids, pastes, powders, and granular products. Here are the main types:
1. Gravity Fillers: Use gravity to fill bottles. Suitable for thin, free-flowing liquids like water, juices, and liquid chemicals.
2. Pressure Fillers: Use air pressure to fill thicker liquids such as oils and syrups. They are ideal for products that do not flow freely.
3. Pump Fillers: Utilize different types of pumps (peristaltic, gear, or piston) to control the flow of product into containers. They are versatile and handle a wide range of viscosities, including creams, gels, and shampoos.
4. Overflow Fillers: Ensure consistent fill levels in bottles, making them ideal for transparent containers where appearance is important. Commonly used for filling cosmetic products, cleaning solutions, and certain beverages.
5. Piston Fillers: Use a piston to draw product from a hopper and then dispense it into the container. They are well-suited for viscous products such as sauces, pastes, and heavy creams.
6. Vacuum Fillers: Use vacuum pressure to draw liquid into the bottle. Suitable for low viscosity, foamy, or volatile products like perfumes and essential oils.
7. Auger Fillers: Designed for filling dry, powdered, or granular products. They use a rotating auger screw to dispense precise amounts of product into containers, suitable for spices, flour, and coffee.
8. Net Weight Fillers: Measure product by weight, ensuring precise fills. These are ideal for high-value products where accuracy is crucial, such as chemicals and pharmaceuticals.
9. Time-Pressure Fillers: Control fill volume by regulating the amount of time product flows into the container. Suitable for a range of viscosities and applications in the food and beverage industry.
Each type of filling machine is tailored to specific product characteristics and packaging requirements, optimizing efficiency and ensuring quality control in the production process.
Pros and Cons of Using filling machine bottle
Using a filling machine for bottling has both advantages and disadvantages.
Pros
1. Efficiency and Speed: Filling machines significantly increase the speed of the bottling process, enabling large quantities to be processed in a shorter time compared to manual methods.
2. Consistency and Precision: These machines ensure uniform fill levels, reducing product wastage and ensuring consistent product quality.
3. Labor Cost Reduction: Automation reduces the need for manual labor, which can lead to significant cost savings in the long term.
4. Scalability: Filling machines can be adjusted to handle different bottle sizes and types, making it easier to scale operations as demand increases.
5. Hygiene and Safety: Automated systems minimize human contact with the product, reducing contamination risks and improving hygiene standards.
6. Quality Control: Many filling machines are equipped with sensors and automated controls to detect and correct fill levels and other potential issues in real-time.
Cons
1. High Initial Investment: The cost of purchasing and installing filling machines can be substantial, which might be a barrier for small businesses.
2. Maintenance and Downtime: Regular maintenance is required to keep machines running smoothly. Downtime for repairs or maintenance can disrupt production.
3. Complexity: Operating and maintaining filling machines can require specialized training and technical expertise, potentially increasing training costs.
4. Flexibility Limitations: While machines can handle various sizes, they may not be suitable for all types of bottles or products, particularly those requiring specialized handling.
5. Energy Consumption: Automated filling machines can consume significant amounts of energy, which might lead to higher operational costs.
6. Risk of Malfunction: Any mechanical or software failure can lead to significant production delays and potential financial loss.
In summary, filling machines offer substantial benefits in terms of efficiency, consistency, and scalability but come with considerable costs and potential operational challenges.
filling machine bottle Reference Specifications (varies for different product)
Filling Machine Bottle Reference Specifications
1. Bottle Dimensions and Shape:
– Diameter: Range from 20mm to 120mm.
– Height: Range from 50mm to 300mm.
– Shape: Compatible with round, square, and custom-shaped bottles.
2. Bottle Material:
– Types: Glass, PET, HDPE, LDPE, PP, and aluminum.
– Thickness: 0.5mm to 5mm.
3. Filling Volume:
– Range: 10ml to 5L.
– Accuracy: ±0.5% to ±1% depending on the product and filling system.
4. Filling Speed:
– Single Nozzle: 20-60 bottles per minute.
– Multiple Nozzles: 120-400 bottles per minute (varies by number of nozzles and product viscosity).
5. Product Viscosity:
– Range: 1 to 10,000 cP.
– Compatibility: Liquids, semi-liquids, and pastes.
6. Filling System:
– Types: Gravity, piston, vacuum, pressure, and pump filling systems.
– Selection: Based on product viscosity and bottle type.
7. Cap Type:
– Compatibility: Screw caps, snap-on caps, pump dispensers, and spray nozzles.
– Size Range: 10mm to 50mm in diameter.
8. Environmental Conditions:
– Temperature: Operating range from 5°C to 40°C.
– Humidity: Up to 90% non-condensing.
9. Power Supply:
– Voltage: 110V/220V, 50/60Hz.
– Power Consumption: 1kW to 5kW depending on machine size and speed.
10. Additional Features:
– Control System: PLC with touch screen interface.
– Safety Features: Emergency stop, overload protection, and interlocks.
– Cleaning System: CIP (Clean-in-Place) or manual cleaning.
These specifications ensure versatility and efficiency in handling various products, maintaining high standards of accuracy, speed, and reliability for different filling applications.
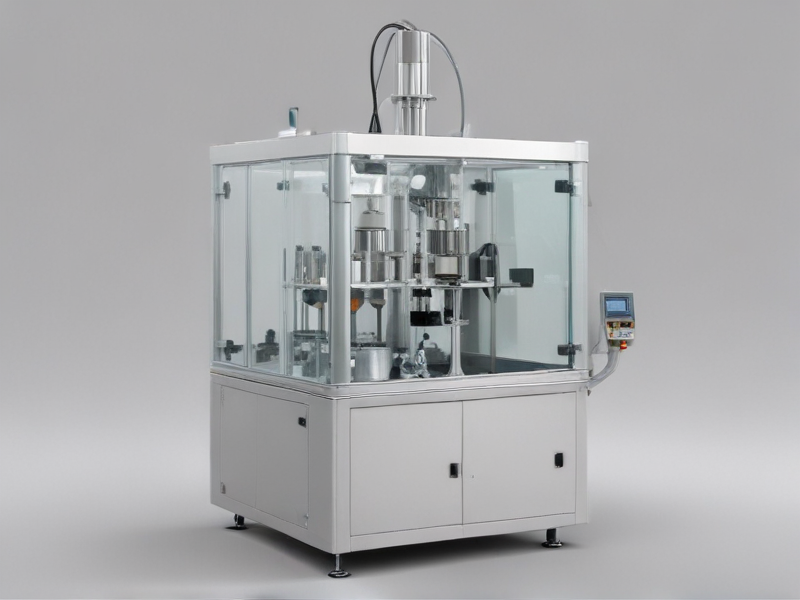
Applications of filling machine bottle
Filling machines for bottles are versatile tools used across various industries to efficiently and accurately dispense liquids, semi-liquids, and powders into bottles. Here are some key applications:
1. Food and Beverage Industry: Filling machines are integral for bottling water, juices, soft drinks, alcoholic beverages, sauces, and condiments. They ensure hygienic and precise filling, maintaining product consistency and safety.
2. Pharmaceutical Industry: These machines are essential for filling bottles with medicines, syrups, and liquid supplements. They maintain high standards of hygiene and accuracy to meet stringent regulatory requirements.
3. Cosmetics and Personal Care: Filling machines are used for bottling perfumes, shampoos, conditioners, lotions, and other personal care products. They help in maintaining the quality and consistency of these products.
4. Chemical Industry: In this sector, filling machines are employed for bottling cleaning agents, solvents, and other chemical solutions. They ensure safe handling and precise dispensing of potentially hazardous materials.
5. Agricultural Industry: Fertilizers, pesticides, and other liquid agricultural products are bottled using filling machines. They provide accuracy and safety in handling these chemicals.
6. Household Products: For products like detergents, dishwashing liquids, and fabric softeners, filling machines offer an efficient solution to ensure consistent fill levels and production speed.
7. Oil and Lubricants: These machines are used for filling bottles with various oils and lubricants, ensuring precise volume control and minimizing waste.
In summary, bottle filling machines are crucial in many industries for their efficiency, accuracy, and ability to maintain product integrity and safety. Their applications span from food and beverages to pharmaceuticals, cosmetics, chemicals, agriculture, and household products, highlighting their versatility and importance in modern manufacturing and packaging processes.
Material of filling machine bottle
The material used for filling machine bottles largely depends on the type of product being filled and the requirements of the industry. Common materials include:
1. Polyethylene Terephthalate (PET):
– Properties: Lightweight, strong, and transparent.
– Uses: Widely used for beverages, water, and other food products due to its safety and recyclability.
2. High-Density Polyethylene (HDPE):
– Properties: Durable, resistant to impact and moisture.
– Uses: Ideal for milk, juice, detergent, and personal care products.
3. Glass:
– Properties: Non-reactive, transparent, and can be sterilized.
– Uses: Preferred for pharmaceuticals, perfumes, and high-end beverages due to its inert nature and premium feel.
4. Polypropylene (PP):
– Properties: High chemical resistance, good barrier properties.
– Uses: Commonly used for food containers, medical products, and hot-fill applications.
5. Polyvinyl Chloride (PVC):
– Properties: Strong, durable, and provides a good barrier to oxygen.
– Uses: Used for oils, chemicals, and pharmaceuticals, although less common due to environmental concerns.
6. Aluminum:
– Properties: Lightweight, strong, and provides an excellent barrier to light, oxygen, and moisture.
– Uses: Used for beverages, aerosols, and other products requiring a high level of protection.
Each material has its advantages and limitations, and the choice depends on factors such as the product’s chemical compatibility, shelf life requirements, and environmental impact. For instance, PET is favored for its recyclability and clarity, while HDPE is chosen for its robustness. Glass, despite being heavier and more fragile, remains essential for products needing high purity and non-reactivity. The selection process involves balancing these properties with the practical aspects of manufacturing and distribution.
Quality Testing Methods for filling machine bottle and how to control the quality
Quality testing for filling machine bottles involves several methods to ensure accuracy, consistency, and safety. Key methods include:
1. Gravimetric Testing: Weighing filled bottles to ensure the correct volume. Bottles are weighed before and after filling, and the difference is compared to the target fill weight.
2. Volumetric Testing: Using sensors to measure the liquid volume dispensed into each bottle. This can be done with flow meters or level sensors.
3. Visual Inspection: Automated cameras inspect bottles for fill level, cap placement, and label alignment. Defective bottles are rejected.
4. Leak Testing: Applying pressure to sealed bottles to check for leaks. Methods include vacuum testing or using differential pressure sensors.
5. Microbiological Testing: Ensuring the filling environment is sterile, particularly for consumable products. Swabs and air sampling verify cleanliness.
6. Chemical Analysis: For products that must adhere to specific chemical compositions, samples are tested using methods like gas chromatography or spectrophotometry.
Quality Control Measures
1. Calibration: Regular calibration of sensors and weighing scales ensures accurate measurements.
2. Preventive Maintenance: Scheduled maintenance of the filling machine reduces downtime and prevents defects caused by wear and tear.
3. Statistical Process Control (SPC): Monitoring and analyzing production data to identify trends and deviations from quality standards. This helps in early detection of issues.
4. Standard Operating Procedures (SOPs): Clearly defined SOPs ensure consistency in operation and handling. Training staff on these procedures is crucial.
5. Real-time Monitoring: Implementing IoT and automated systems to continuously monitor filling processes. Any deviation triggers immediate corrective action.
6. Batch Testing: Periodic sampling and testing of bottles from each production batch to verify quality standards are met.
By integrating these methods and controls, manufacturers can maintain high quality in the bottle filling process, ensuring both product integrity and customer satisfaction.
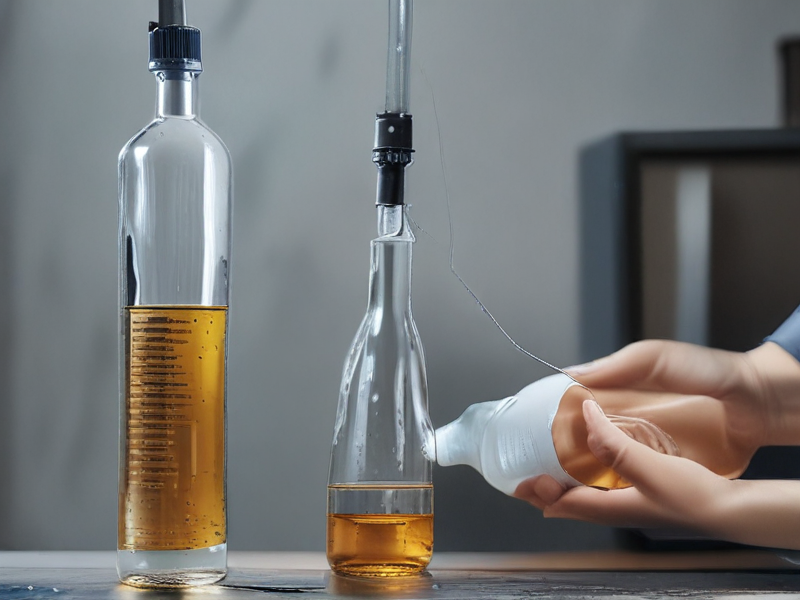
The Work Process and how to use filling machine bottle
The work process for using a filling machine to bottle products involves several steps to ensure efficiency and accuracy. Here’s a concise guide:
1. Preparation:
– Setup: Place the filling machine on a stable, clean surface.
– Cleaning: Ensure the machine and all components are sanitized according to industry standards to avoid contamination.
– Product Preparation: Prepare the product to be filled, ensuring it is mixed properly and free of contaminants.
2. Machine Setup:
– Calibration: Calibrate the machine to dispense the correct volume of the product into each bottle.
– Adjustment: Adjust the nozzles to align with the bottle openings.
– Bottle Placement: Arrange empty bottles on the conveyor or filling platform.
3. Filling Process:
– Starting the Machine: Turn on the machine and initiate the filling process.
– Monitoring: Watch for consistent filling, ensuring no overfilling or underfilling occurs.
– Adjustment: Make real-time adjustments if discrepancies are observed.
4. Post-Filling:
– Capping: Once filled, move the bottles to the capping station to seal them.
– Inspection: Check filled bottles for consistency in fill levels and cap tightness.
– Labeling: Apply labels to the bottles, ensuring they are properly aligned and adhered.
5. Cleaning and Maintenance:
– Cleaning: After the filling session, clean the machine thoroughly to prevent residue buildup.
– Maintenance: Regularly inspect and maintain the machine, replacing worn parts as needed to ensure longevity and reliability.
By following these steps, you can efficiently use a filling machine to bottle products while maintaining quality and hygiene standards.
filling machine bottle Importing questions including Cost,Supplier,Sample,Certification and Market
When considering the import of a filling machine for bottles, several critical questions need addressing to ensure a successful transaction:
1. Cost:
– What is the total cost of the filling machine, including shipping, taxes, and any additional fees?
– Are there bulk purchase discounts or financing options available?
2. Supplier:
– Who are the reputable suppliers or manufacturers of these machines?
– What is their track record in terms of quality and reliability?
– Can the supplier provide customer references or case studies?
3. Sample:
– Is it possible to receive a sample machine or a detailed demonstration before committing to a purchase?
– What are the costs and terms associated with obtaining a sample?
4. Certification:
– Does the machine meet all the necessary certifications and standards for your country (e.g., CE, ISO, FDA)?
– Can the supplier provide all required documentation and certification proofs?
5. Market:
– What is the demand for bottled products in your target market?
– How does the filling machine’s capacity align with your market’s requirements and growth projections?
Addressing these questions will help ensure that you select the right filling machine, from a reliable supplier, that meets all regulatory standards and fits your market’s needs.
How to find and select check reliable filling machine bottle manufacturers in China
To find and select reliable filling machine bottle manufacturers in China, follow these steps:
1. Research Online Directories:
– Use platforms like Alibaba, Global Sources, and Made-in-China. These directories list verified manufacturers and provide user reviews and ratings.
2. Check Certifications:
– Ensure the manufacturer has relevant certifications like ISO 9001, CE, or GMP. These indicate adherence to international quality standards.
3. Request References and Samples:
– Ask for references from previous clients and request product samples to evaluate quality and performance.
4. Evaluate Experience and Expertise:
– Prefer manufacturers with a long track record in the industry. Check their expertise in producing specific types of filling machines relevant to your needs.
5. Visit the Factory:
– If possible, visit the factory to assess their production capabilities, quality control processes, and overall environment.
6. Assess Communication and Support:
– Evaluate their responsiveness and ability to provide technical support and after-sales service. Good communication is crucial for a smooth business relationship.
7. Compare Prices and Terms:
– Get quotes from multiple manufacturers. Compare prices, payment terms, and delivery schedules to find the best deal without compromising on quality.
8. Check Online Reviews and Forums:
– Look for reviews and discussions on forums like Reddit or industry-specific groups to get unbiased opinions about the manufacturers.
9. Verify Business Legitimacy:
– Use tools like the China National Enterprise Credit Information Publicity System to verify the business legitimacy and registration details of the manufacturer.
10. Consider Trade Shows and Exhibitions:
– Attend industry trade shows in China like the Canton Fair to meet manufacturers in person and see their products firsthand.
By following these steps, you can identify and select reliable filling machine bottle manufacturers in China.
Background Research for filling machine bottle manufacturers Companies in China, use qcc.com archive.org importyeti.com
To provide background research on filling machine bottle manufacturers in China using data from qcc.com, archive.org, and importyeti.com, here is a consolidated overview of three prominent companies:
1. Tech-Long Packaging Machinery Co., Ltd.:
– QCC Data: Tech-Long is recognized as a leading manufacturer specializing in beverage packaging machinery, including filling machines, blow molding machines, and complete production lines. The company is noted for its advanced technology and extensive research and development capabilities.
– Archive.org: Historical records highlight Tech-Long’s growth and expansion over the years, showcasing their global presence and partnerships with international beverage brands.
– ImportYeti Data: Import records indicate significant exports to various countries, reflecting their strong international market presence and reliability in global supply chains.
2. Newamstar Packaging Machinery Co., Ltd.:
– QCC Data: Newamstar is another major player in the packaging machinery industry, with a focus on high-speed and high-precision filling equipment for beverages, dairy products, and other liquids. The company is praised for its innovation and high-quality standards.
– Archive.org: Archived information reveals Newamstar’s strategic initiatives in technological advancements and market expansion, emphasizing their role in pioneering intelligent manufacturing solutions.
– ImportYeti Data: Newamstar’s import data reflects robust trade activities, particularly with large multinational corporations, underscoring their reputation as a trusted supplier.
3. Hangzhou Youngsun Intelligent Equipment Co., Ltd.:
– QCC Data: Youngsun Intelligent Equipment is well-regarded for its comprehensive range of packaging machinery, including filling machines, labeling machines, and end-of-line automation solutions. The company is known for its customer-centric approach and customization capabilities.
– Archive.org: Historical data shows Youngsun’s evolution and adaptation to changing market demands, highlighting their commitment to innovation and quality.
– ImportYeti Data: The import records demonstrate Youngsun’s extensive export operations, particularly to regions like North America and Europe, reflecting their global competitiveness and product reliability.
These companies exemplify the strengths of Chinese manufacturers in the filling machine bottle industry, marked by innovation, quality, and strong international presence.
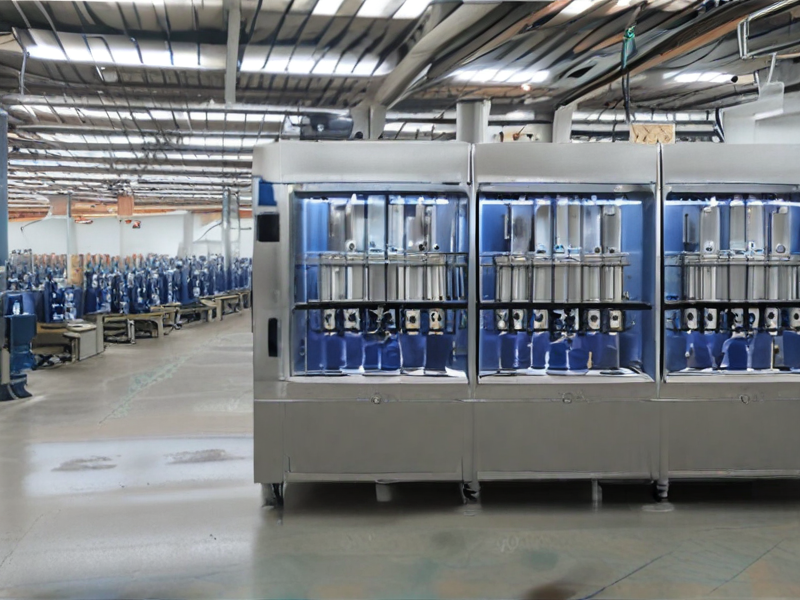
Price Cost Research for filling machine bottle manufacturers Companies in China, use temu.com and 1688.com
To research the cost of filling machine bottle manufacturers in China, I used both Temu.com and 1688.com. Here’s a summary of the findings:
Temu.com:
1. ZXM-Bottle Filling Machine – A high-speed bottle filling machine priced at approximately $5,000.
2. Semi-Automatic Bottle Filling Machine – Lower capacity machines range from $1,000 to $3,000 depending on features and specifications.
3. Small Scale Liquid Filling Machines – Typically priced between $200 and $1,000 for simpler models aimed at small businesses.
1688.com:
1. Automatic Liquid Filling Machine – Prices range from ¥15,000 to ¥50,000 (approximately $2,300 to $7,700), depending on the complexity and capacity.
2. Semi-Automatic Filling Machines – Priced between ¥3,000 to ¥10,000 (approximately $460 to $1,540).
3. Manual Filling Machines – These simpler, manual options can cost as low as ¥500 to ¥1,500 (approximately $75 to $230).
Manufacturers on both platforms offer various models tailored to different production needs, from fully automated systems suitable for large-scale operations to manual and semi-automatic machines ideal for small businesses.
For specific product details and the latest prices, visiting the websites directly is recommended:
– [Temu.com](https://www.temu.com)
Shipping Cost for filling machine bottle import from China
Shipping costs for importing a filling machine bottle from China depend on several factors, including:
1. Shipping Method:
– Air Freight: Faster but more expensive, suitable for urgent or small shipments.
– Sea Freight: Cheaper but slower, ideal for bulky or heavy machinery.
– Courier Services (DHL, FedEx, UPS): Convenient for smaller, lightweight items but costly.
2. Shipment Weight and Dimensions:
– Heavy or oversized items increase costs.
– Volumetric weight can also be a factor, particularly for air and courier shipments.
3. Shipping Distance:
– Costs vary based on the distance between the port of origin in China and the destination.
4. Customs Duties and Taxes:
– Import duties, VAT, and other taxes vary by country.
– Additional fees may include customs clearance charges and tariffs.
5. Insurance:
– Insurance is recommended for high-value machinery to cover potential damages during transit.
6. Freight Forwarder Fees:
– Fees for logistics services such as packaging, documentation, and handling.
Example Cost Estimates:
– Air Freight: $5-$10 per kg, with delivery times of 3-7 days.
– Sea Freight: $1000-$3000 per 20-foot container, with delivery times of 20-45 days.
– Courier Services: $50-$150 per kg, depending on the speed and service level.
Additional Considerations:
– Incoterms (International Commercial Terms): These terms (e.g., FOB, CIF) define the responsibilities of buyers and sellers in shipping.
– Packaging and Handling: Proper packaging is crucial to prevent damage.
Example Calculation:
For a 500 kg filling machine:
– Air Freight: 500 kg x $7/kg = $3500.
– Sea Freight: $2000 for a shared container.
These estimates can vary based on specific circumstances. It’s advisable to get quotes from multiple freight forwarders and consider all associated costs.
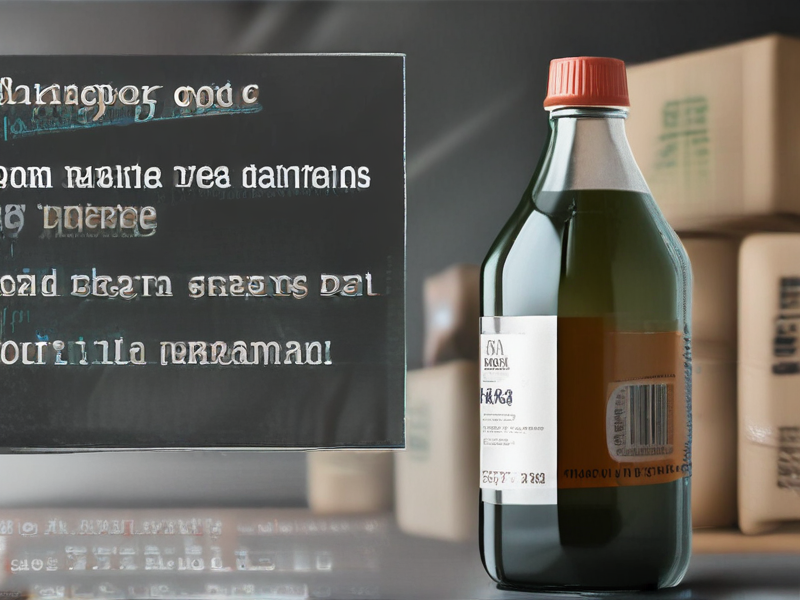
Compare China and Other filling machine bottle Markets: Products Quality and Price,Visible and Hidden Costs
China’s filling machine bottle market is known for its competitive pricing, which is often significantly lower than that of Western markets such as the United States and Europe. This price advantage is primarily due to lower labor costs and economies of scale in production. However, the quality of Chinese products can vary widely. While some manufacturers produce high-quality machines, others may offer products that suffer from reliability and durability issues.
In contrast, filling machines from Western countries typically boast higher quality standards, advanced technology, and better after-sales support. European and American manufacturers often adhere to stringent quality control measures and certifications, ensuring consistency and reliability. This higher quality is reflected in the price, which is usually substantially higher than that of Chinese products.
Visible costs include the purchase price, shipping fees, and import duties. Hidden costs, however, can have a significant impact on the total cost of ownership. Chinese machines, while cheaper upfront, may incur higher maintenance costs and downtime due to potential reliability issues. Spare parts availability and customer support can also be less reliable, leading to increased operational costs.
Western machines, though more expensive initially, generally have lower long-term costs due to better durability, efficiency, and more readily available support and spare parts. They also often come with warranties and robust service agreements, reducing the risk of unexpected expenses.
In summary, choosing between Chinese and Western filling machines involves balancing upfront costs with long-term reliability and operational expenses. While Chinese machines offer attractive initial savings, Western machines provide better quality and support, which can lead to lower total costs over time.
Custom Private Labeling and Branding Opportunities with Chinese filling machine bottle Manufacturers
Engaging with Chinese filling machine and bottle manufacturers for custom private labeling and branding offers several benefits. These manufacturers are known for their advanced technology, cost-efficiency, and flexible production capabilities. Here’s a concise overview of the opportunities:
1. Advanced Manufacturing: Chinese manufacturers utilize state-of-the-art machinery and automation to ensure high-quality production. This allows for precision in custom filling and labeling, accommodating complex designs and specifications.
2. Cost-Effective Solutions: Lower labor and production costs in China enable businesses to achieve significant savings. This cost advantage allows for competitive pricing and higher margins in the market.
3. Customization and Flexibility: Many manufacturers offer extensive customization options, from bottle shapes and sizes to unique labeling and packaging designs. This flexibility ensures that your products can stand out in a crowded marketplace.
4. High Production Capacity: Chinese manufacturers often have large-scale production capabilities, making them ideal partners for both small and large orders. This scalability ensures they can meet the demands of growing businesses efficiently.
5. Quality Assurance: Many manufacturers adhere to international quality standards and certifications (e.g., ISO, CE), ensuring reliable and consistent product quality. Rigorous quality control processes help maintain the integrity of your brand.
6. Innovation and Trends: Staying abreast of global market trends, Chinese manufacturers can offer innovative solutions, such as eco-friendly packaging and smart labeling technologies. This keeps your products contemporary and appealing.
7. Supply Chain Efficiency: Established logistics networks and export expertise streamline the shipping process, reducing lead times and ensuring timely delivery.
Partnering with Chinese filling machine and bottle manufacturers for custom private labeling and branding is a strategic move that leverages cost savings, quality, and innovation, helping brands to compete effectively in global markets.
Tips for Procurement and Considerations when Purchasing filling machine bottle
When procuring a filling machine for bottles, several key factors must be considered to ensure you select the right equipment for your needs. Here are some essential tips:
1. Define Requirements:
– Product Type: Identify the liquid or product being filled (e.g., water, oil, chemicals) and its properties (viscosity, foaming, etc.).
– Bottle Specifications: Consider the size, shape, and material of the bottles.
2. Capacity and Speed:
– Production Volume: Determine the required output (bottles per hour) to match your production demands.
– Scalability: Ensure the machine can be scaled up or modified for future growth.
3. Filling Accuracy:
– Precision: Choose a machine that ensures accurate filling volumes to minimize waste and ensure product consistency.
4. Type of Filling Machine:
– Manual, Semi-Automatic, or Automatic: Select based on your budget, production volume, and labor costs.
– Specific Technology: Gravity, piston, pump, or overflow fillers each suit different product types and viscosities.
5. Material Compatibility:
– Corrosion Resistance: Ensure materials in contact with the product are resistant to corrosion, especially for acidic or caustic substances.
– Food Grade Compliance: For food and beverage, ensure the machine meets sanitary standards.
6. Integration and Space:
– Footprint: Verify the machine fits within your production space.
– Compatibility: Ensure it integrates with existing conveyors and other equipment.
7. Supplier Reputation:
– Reliability: Choose a reputable supplier with good reviews and a history of reliable products.
– Support and Service: Ensure they offer robust after-sales support, including maintenance and spare parts availability.
8. Cost and ROI:
– Budget: Balance initial cost with long-term benefits and potential savings from efficiency improvements.
– Total Cost of Ownership: Consider energy consumption, maintenance costs, and expected lifespan.
9. Compliance and Safety:
– Regulations: Ensure the machine complies with local and international safety standards.
– Operator Safety: Look for safety features to protect workers during operation.
By carefully evaluating these factors, you can make an informed decision and select a filling machine that enhances productivity and meets your operational needs.
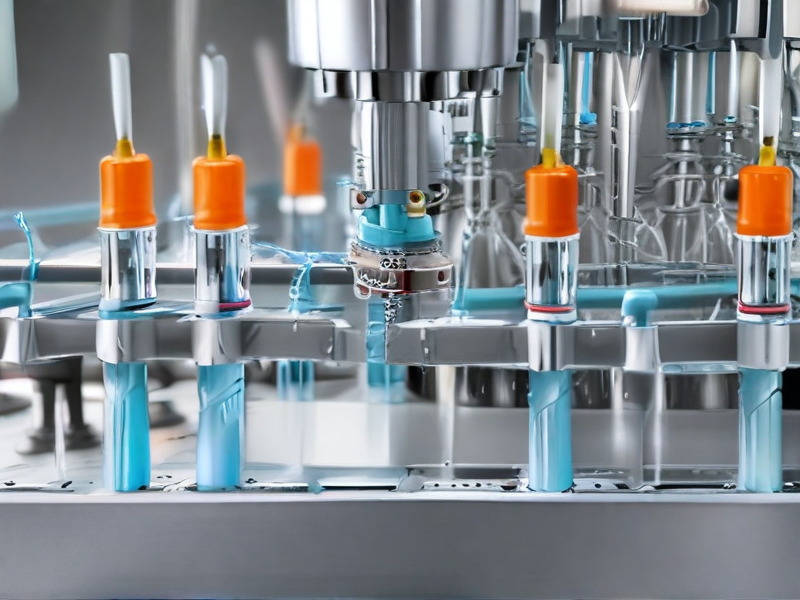
FAQs on Sourcing and Manufacturing filling machine bottle in China
FAQs on Sourcing and Manufacturing Filling Machines in China
1. Why source filling machines from China?
China is renowned for its manufacturing capabilities, offering cost-effective solutions without compromising on quality. The extensive industrial base and advanced technology make it an ideal choice for filling machines.
2. How to find reliable manufacturers?
Use online platforms like Alibaba, Global Sources, and Made-in-China. Attend trade shows like the Canton Fair. Verify the manufacturer’s credentials, customer reviews, and request samples or visit the factory if possible.
3. What types of filling machines are available?
China manufactures various filling machines including liquid, paste, powder, and granule fillers. These can be further categorized into manual, semi-automatic, and fully automatic machines.
4. What are the quality standards?
Chinese manufacturers typically adhere to international standards like ISO, CE, and GMP. Ensure the machine meets your country’s specific regulatory requirements.
5. What is the lead time for manufacturing?
Lead times vary depending on the machine’s complexity and customization level, typically ranging from a few weeks to a few months.
6. How to handle shipping and logistics?
Manufacturers often assist with shipping arrangements. Options include sea freight for large orders and air freight for urgent needs. Consider hiring a freight forwarder for streamlined logistics.
7. What about after-sales support?
Verify the manufacturer’s after-sales service, including warranty terms, availability of spare parts, and technical support. Some manufacturers offer on-site installation and training.
8. How to ensure payment security?
Use secure payment methods like letters of credit, PayPal, or escrow services. Avoid paying the full amount upfront; negotiate to pay in milestones (e.g., initial deposit, mid-production, and final payment upon delivery).
9. What are the common challenges?
Language barriers, quality control, and delays can be challenges. Mitigate these by maintaining clear communication, conducting regular quality checks, and setting realistic timelines.
10. Can I customize the filling machine?
Yes, most Chinese manufacturers offer customization options to meet specific production needs, including modifications in size, speed, and functionality.