Top 10 cnc milling operations in China introduce,list main products and website if have
Certainly! Here are ten prominent CNC milling operations in China, including their main products and websites:
1. Foxconn Technology Group
– Main Products: Consumer electronics, automotive components, precision tools.
– Website: [Foxconn](https://www.foxconn.com)
2. BYD Company Ltd.
– Main Products: Electric vehicles, rechargeable batteries, solar panels.
– Website: [BYD](http://www.byd.com)
3. Shenzhen SIBOASI Sports Goods Technology Co., Ltd.
– Main Products: Sports equipment, automated training machines, CNC machined parts.
– Website: [SIBOASI](http://www.siboasi.net)
4. Great Wall Motors
– Main Products: Automobiles, automotive parts, CNC machined components.
– Website: [Great Wall Motors](http://www.gwm-global.com)
5. Gree Electric Appliances Inc.
– Main Products: Air conditioners, home appliances, CNC machined parts for electronics.
– Website: [Gree](http://www.gree.com)
6. Wuhan Heavy Duty Machine Tool Group Corporation
– Main Products: Heavy machinery, CNC milling machines, industrial equipment.
– Website: [WHDM](http://www.whhdmt.com)
7. Tianjin HAAS Automation Co., Ltd.
– Main Products: CNC machining centers, lathes, milling machines.
– Website: [HAAS China](http://www.haas.com.cn)
8. Nanjing Auto Electric Co., Ltd.
– Main Products: Electric motors, automotive components, CNC machined parts.
– Website: [NAEC](http://www.njautoelectric.com)
9. Shanghai Automotive Industry Corporation (SAIC)
– Main Products: Automobiles, automotive parts, precision machined components.
– Website: [SAIC](http://www.saicmotor.com)
10. Shenyang Machine Tool Group
– Main Products: CNC milling machines, lathes, industrial machinery.
– Website: [SMTCL](http://www.smtcl.com)
These companies represent a cross-section of the industry, ranging from consumer electronics to heavy industrial machinery, highlighting China’s diverse capabilities in CNC milling and precision manufacturing.
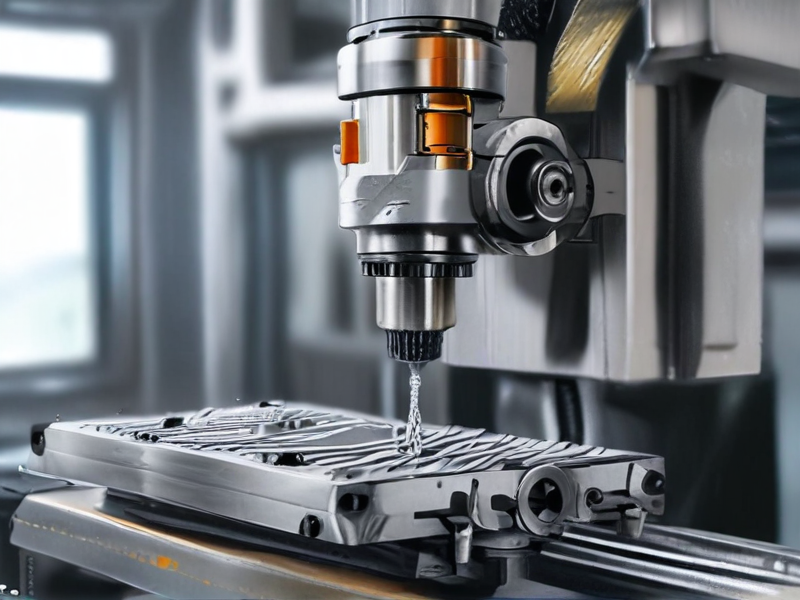
Types of cnc milling operations
CNC (Computer Numerical Control) milling operations are diverse, each tailored for specific machining tasks. Here are the main types:
1. Face Milling:
– Uses a cutter with teeth on the periphery and face.
– Creates flat surfaces perpendicular to the cutter’s axis.
– Ideal for shallow cuts.
2. Plain (or Slab) Milling:
– Employs a cylindrical cutter with teeth on the periphery.
– Cuts flat surfaces parallel to the cutter’s axis.
– Suitable for deeper cuts and larger surface areas.
3. Angular Milling:
– Uses a cutter at an angle to the workpiece.
– Produces angled features like grooves and chamfers.
– Often used for creating dovetail joints.
4. Form Milling:
– Involves a cutter with a specific profile.
– Creates complex shapes and contours.
– Used for machining gears, splines, and intricate profiles.
5. Profile Milling:
– Follows a defined path to shape the outer contour of a workpiece.
– Utilizes end mills or ball nose cutters.
– Suitable for 2D and 3D shapes.
6. Slot Milling:
– Uses a cylindrical cutter to create slots and keyways.
– Can be performed with straight or T-slot cutters.
– Essential for making grooves and channels.
7. Straddle Milling:
– Involves multiple cutters on the same arbor.
– Machines opposite sides of a workpiece simultaneously.
– Efficient for parallel cuts and uniform thickness.
8. Gang Milling:
– Utilizes multiple cutters of different shapes and sizes on a single arbor.
– Executes several machining operations in one pass.
– Enhances productivity and accuracy.
9. Plunge Milling:
– Also known as Z-axis milling.
– The cutter plunges vertically into the workpiece.
– Effective for removing large amounts of material.
10. Pocket Milling:
– Removes material within a confined area (pocket).
– Uses end mills to machine cavities and recesses.
– Common in mold and die making.
Each operation is selected based on the desired geometry, material properties, and specific machining requirements.
Pros and Cons of Using cnc milling operations
Pros of CNC Milling Operations:
1. Precision and Accuracy: CNC milling machines offer high levels of precision and repeatability, ensuring consistent quality across multiple parts.
2. Efficiency: CNC milling can operate continuously 24/7, leading to high productivity and shorter production times.
3. Complex Geometry: These machines can create complex shapes and intricate details that would be difficult or impossible with manual machining.
4. Automation: Reduced need for manual intervention minimizes human error, enhancing safety and reliability.
5. Versatility: CNC mills can work with a variety of materials including metals, plastics, and wood, making them suitable for diverse applications.
6. Scalability: Ideal for both small and large production runs, allowing for flexible manufacturing processes.
Cons of CNC Milling Operations:
1. High Initial Cost: The purchase and setup of CNC milling machines require significant investment, which can be a barrier for small businesses.
2. Maintenance: Regular maintenance is necessary to keep the machines running smoothly, adding to operational costs.
3. Complexity: CNC milling requires skilled operators to program and manage the machines, which can involve a steep learning curve.
4. Limited by Size: CNC milling machines have size constraints, making them unsuitable for very large parts.
5. Material Waste: Although precise, the subtractive nature of milling generates waste material, which can be a concern for both cost and environmental impact.
6. Software Dependency: CNC milling relies heavily on software for design and operation, which can be susceptible to bugs, compatibility issues, and requires regular updates.
In summary, CNC milling operations provide high precision, efficiency, and versatility, making them valuable for a wide range of manufacturing needs. However, the high initial cost, maintenance requirements, and reliance on skilled labor and software are notable drawbacks.
cnc milling operations Reference Specifications (varies for different product)
CNC (Computer Numerical Control) milling operations are crucial for producing precise and complex parts in various industries. The specifications for CNC milling vary significantly depending on the product requirements, including material type, dimensional tolerances, surface finish, and geometric complexity. Below are some key reference specifications typically considered:
1. Material Type:
– Metals: Aluminum, steel, titanium, and brass.
– Plastics: ABS, nylon, polycarbonate.
– Composites: Carbon fiber, fiberglass.
2. Dimensional Tolerances:
– Standard Tolerances: ±0.005 inches (±0.127 mm) for most applications.
– High Precision: ±0.001 inches (±0.025 mm) for critical components.
3. Surface Finish:
– Roughing: Ra 125-250 micro-inches.
– Finishing: Ra 32-63 micro-inches.
– Ultra-fine Finish: Ra < 16 micro-inches for highly aesthetic or functional surfaces.
4. Geometric Complexity:
– 2.5D Milling: Primarily involves profiles and pockets with vertical side walls.
– 3D Milling: Includes complex contours, variable depth features, and sculpted surfaces.
– 4 and 5-axis Milling: Enables machining of intricate shapes and undercuts, reducing the need for multiple setups.
5. Tooling and Speeds:
– Tool Types: End mills, ball mills, face mills, and chamfer mills.
– Spindle Speeds: 2,000 to 20,000 RPM depending on material and tooling.
– Feed Rates: Vary from 20 to 200 inches per minute (IPM) based on the operation.
6. Machine Capabilities:
– Table Size: Determines the maximum part size that can be milled.
– Axis Travel: X, Y, and Z travel ranges, often 20-40 inches for medium-sized machines.
– Horsepower: 10-50 HP, affecting material removal rates and cutting efficiency.
7. Software:
– CAM Software: For generating toolpaths (e.g., Mastercam, Fusion 360).
– Simulation and Verification: Ensures accurate and collision-free operations.
8. Quality Control:
– Inspection Methods: CMM (Coordinate Measuring Machine), laser scanning, and manual gauges.
– Documentation: Inspection reports, material certificates, and traceability records.
These specifications help in planning and executing CNC milling operations to achieve the desired product quality and performance.
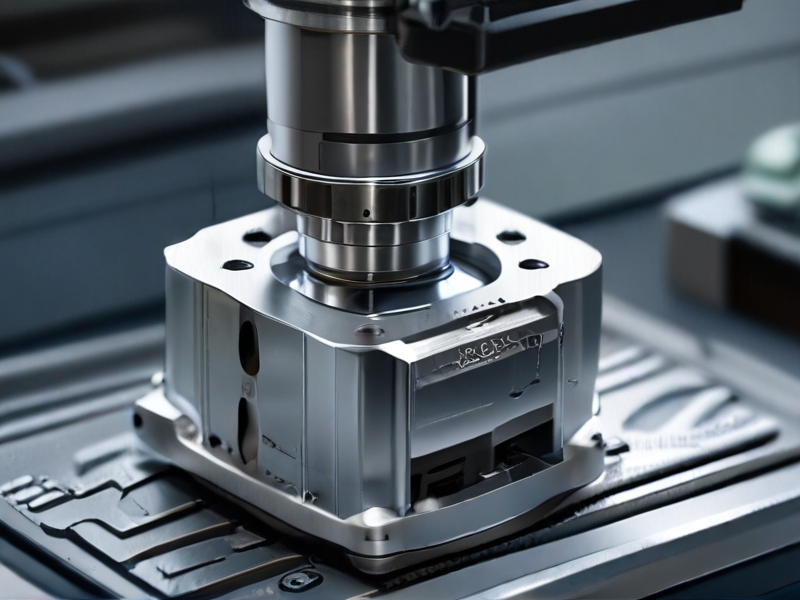
Applications of cnc milling operations
CNC (Computer Numerical Control) milling operations are widely utilized across various industries due to their precision, versatility, and efficiency. Here are some notable applications:
1. Aerospace: CNC milling is essential for manufacturing complex components such as turbine blades, engine parts, and structural components. The precision of CNC milling ensures the reliability and safety of aerospace parts.
2. Automotive: In the automotive industry, CNC milling is used to produce engine blocks, cylinder heads, transmission components, and custom car parts. It allows for high precision and consistency in mass production.
3. Medical Devices: CNC milling is critical in the production of surgical instruments, orthopedic implants, dental implants, and prosthetic devices. The ability to machine intricate details with high accuracy is crucial in this sector.
4. Electronics: CNC milling is employed to create enclosures, heat sinks, and components for various electronic devices. The precision machining ensures the proper fit and function of delicate electronic assemblies.
5. Tool and Die Making: CNC milling is used to create molds, dies, and tooling components for plastic injection molding, metal stamping, and forging. High precision and repeatability are key benefits in this application.
6. Prototyping: Rapid prototyping with CNC milling allows designers and engineers to quickly produce functional prototypes, test parts, and iterate designs before moving to full-scale production.
7. Construction: CNC milling is used to create architectural models, custom building components, and decorative elements. It enables the production of complex shapes and patterns that are difficult to achieve with traditional methods.
8. Jewelry: In jewelry making, CNC milling is used to craft detailed and intricate designs from metals and other materials. This allows for high precision and customization.
9. Energy Sector: CNC milling is used to produce components for wind turbines, solar panels, and oil and gas extraction equipment. The precision and durability of machined parts are essential for the reliability of energy systems.
Overall, CNC milling operations enhance productivity, reduce waste, and enable the manufacturing of complex and precise parts across a wide range of industries.
Material of cnc milling operations
CNC milling is a versatile machining process used to create precise components from a variety of materials. The choice of material depends on the application’s requirements, including strength, weight, corrosion resistance, and machinability. Here are some commonly used materials in CNC milling:
1. Metals:
– Aluminum: Known for its excellent machinability, strength-to-weight ratio, and corrosion resistance. Commonly used in aerospace, automotive, and consumer electronics.
– Steel: Available in various grades (carbon steel, alloy steel, stainless steel), steel offers high strength and durability. Stainless steel also provides excellent corrosion resistance, making it suitable for medical and food industry applications.
– Brass: Offers good machinability, corrosion resistance, and electrical conductivity. It is often used in fittings, valves, and electrical components.
– Titanium: Known for its high strength, light weight, and corrosion resistance, titanium is used in aerospace, medical implants, and high-performance automotive parts.
2. Plastics:
– ABS (Acrylonitrile Butadiene Styrene): Offers good machinability, impact resistance, and is widely used in prototyping and consumer products.
– Delrin (Polyoxymethylene or POM): Known for its high strength, rigidity, and low friction, Delrin is used in mechanical components like gears and bearings.
– Nylon: Offers good wear resistance, high tensile strength, and is often used in automotive and industrial applications.
– PTFE (Teflon): Provides excellent chemical resistance and low friction, making it ideal for seals, gaskets, and non-stick applications.
3. Composites:
– Carbon Fiber: Known for its high strength-to-weight ratio and rigidity. Used in aerospace, automotive, and sports equipment.
– Fiberglass: Offers good strength and electrical insulation properties. Commonly used in marine, automotive, and construction industries.
Selecting the appropriate material for CNC milling involves considering factors like the material’s mechanical properties, cost, and the specific requirements of the finished part.
Quality Testing Methods for cnc milling operations and how to control the quality
Quality testing in CNC milling operations involves several methods to ensure precision and adherence to specifications. Key methods include:
1. Dimensional Inspection:
– Calipers and Micrometers: Measure external and internal dimensions.
– Coordinate Measuring Machines (CMMs): Provide high accuracy in measuring complex geometries.
2. Surface Finish Inspection:
– Profilometers: Measure surface roughness.
– Visual and Tactile Inspection: Check for visible defects and surface texture.
3. Geometric Inspection:
– CMMs: Check for geometric tolerances like flatness, roundness, and perpendicularity.
– Optical Comparators: Project part profiles to measure and compare against design specifications.
4. Material Inspection:
– Hardness Testing: Ensure material properties are within desired range.
– Metallographic Analysis: Examine microstructure to verify material treatment processes.
5. Non-Destructive Testing (NDT):
– Ultrasonic Testing: Detect internal flaws.
– X-ray Inspection: Check for internal structural integrity.
Quality Control Strategies:
1. Statistical Process Control (SPC):
– Control Charts: Monitor process stability and detect variations.
– Process Capability Analysis: Ensure the process can produce within specified limits consistently.
2. In-Process Monitoring:
– Tool Wear Monitoring: Use sensors to detect tool wear and avoid defects.
– Real-Time Feedback Systems: Adjust parameters dynamically during the milling operation.
3. Preventive Maintenance:
– Regular Machine Calibration: Maintain accuracy and precision.
– Scheduled Maintenance: Prevent unexpected machine breakdowns.
4. Operator Training:
– Skilled Workforce: Train operators in inspection techniques and quality standards.
– Continuous Improvement Programs: Encourage operators to identify and solve quality issues.
5. Documentation and Traceability:
– Inspection Records: Maintain detailed logs of inspections.
– Traceability Systems: Track part history from raw material to finished product.
Implementing these methods and strategies ensures high-quality CNC milling operations, minimizes defects, and maintains consistent production standards.
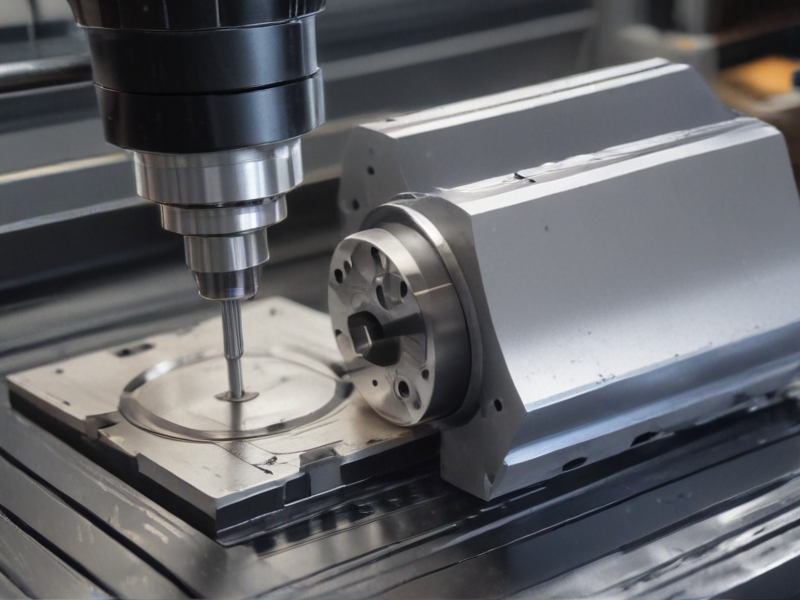
The Work Process and how to use cnc milling operations
CNC (Computer Numerical Control) milling is a precision machining process used to create complex parts and components. Here’s an overview of the work process and how to use CNC milling operations:
Work Process
1. Designing:
– CAD (Computer-Aided Design): Create a digital model of the part using CAD software.
2. Programming:
– CAM (Computer-Aided Manufacturing): Convert the CAD model into a CNC program using CAM software. This includes tool path generation, defining cutting tools, and setting machining parameters.
3. Setting Up:
– Machine Setup: Load the CNC program into the milling machine.
– Tooling: Install the appropriate cutting tools and secure the workpiece on the machine’s worktable.
– Zeroing: Set the machine’s zero point (datum) to establish the origin for the machining operations.
4. Machining:
– Operation Execution: Start the milling process. The CNC machine will follow the programmed instructions to remove material and shape the part. Common operations include:
– Face Milling: Creating a flat surface on the workpiece.
– Peripheral Milling: Cutting along the edges of the part.
– Slot Milling: Creating grooves or slots.
– Drilling: Creating holes.
5. Monitoring and Adjustments:
– Continuously monitor the machining process for any issues such as tool wear or material defects. Adjust feed rates, speeds, and other parameters as necessary.
6. Finishing:
– Deburring and Cleaning: Remove any burrs or sharp edges and clean the part.
– Inspection: Measure and inspect the finished part to ensure it meets the design specifications and tolerances.
Using CNC Milling Operations
1. Load Program: Import the CNC program into the machine’s controller.
2. Tool Setup: Insert the appropriate cutting tools and ensure they are properly calibrated.
3. Workpiece Setup: Secure the material on the machine table using clamps or vices.
4. Set Zero Point: Use the machine’s interface to set the datum point based on the workpiece position.
5. Run Simulation: Conduct a dry run or simulation to verify the tool paths and detect potential issues.
6. Start Machining: Execute the program to begin the milling operations. Monitor the process and make necessary adjustments.
7. Post-Processing: After machining, clean, deburr, and inspect the part.
By following these steps, CNC milling ensures precise, efficient, and repeatable manufacturing of parts.
cnc milling operations Importing questions including Cost,Supplier,Sample,Certification and Market
CNC milling is a versatile manufacturing process, and when considering importing CNC milling operations, several key factors need to be addressed:
1. Cost:
– Initial Cost: Includes the price of CNC milling machines, tooling, and setup. Consider shipping fees, import duties, and taxes.
– Operational Cost: Factor in maintenance, power consumption, labor, and material costs.
– Total Cost of Ownership: Include long-term expenses like machine depreciation and software updates.
2. Supplier:
– Reputation and Reliability: Choose suppliers with a solid track record, verified by reviews and references.
– Quality Assurance: Ensure the supplier adheres to industry standards and provides consistent quality.
– Support and Service: Assess the availability of after-sales support, including maintenance services and spare parts.
3. Sample:
– Prototype Evaluation: Request samples to assess the machining quality, precision, and surface finish.
– Testing: Conduct stress and performance tests to ensure the product meets required specifications.
– Iterative Improvement: Work with suppliers to refine prototypes based on feedback.
4. Certification:
– Industry Standards: Ensure compliance with relevant certifications such as ISO 9001 for quality management and ISO 14001 for environmental management.
– Regulatory Compliance: Verify that machines and processes meet local and international regulatory requirements.
– Documentation: Obtain necessary documentation, including machine certification, material certificates, and safety compliance records.
5. Market:
– Demand Analysis: Study market trends to understand the demand for CNC machined products in your target market.
– Competitor Analysis: Evaluate the competitive landscape to position your offerings effectively.
– Distribution and Logistics: Plan the logistics for importing machinery and distributing products, considering lead times and transportation costs.
By carefully considering these factors, you can make informed decisions and ensure a successful CNC milling operation import.
How to find and select check reliable cnc milling operations manufacturers in China
To find and select reliable CNC milling operations manufacturers in China, follow these steps:
1. Research:
– Online Directories: Use platforms like Alibaba, Global Sources, and Made-in-China. These sites list numerous manufacturers and include reviews.
– Trade Shows: Look for events such as the China International Machine Tool Show (CIMT) to meet suppliers in person.
– Industry Associations: Check with organizations like the China Machine Tool & Tool Builders’ Association (CMTBA) for recommendations.
2. Verification:
– Business License: Ensure the manufacturer has a valid business license.
– Certifications: Verify ISO certifications (e.g., ISO 9001) to ensure quality standards.
– Factory Audits: Conduct on-site audits if possible, or hire third-party inspection agencies to do so.
3. Reputation:
– Customer Reviews: Read reviews and testimonials on online directories and forums.
– Case Studies: Request case studies or examples of previous work to assess their experience and capabilities.
– References: Ask for and contact references to get firsthand feedback.
4. Capabilities:
– Technical Expertise: Evaluate their technical capabilities, machinery, and software used.
– Quality Control: Inquire about their quality control processes and ask for quality inspection reports.
– Sample Production: Request samples to assess the quality firsthand.
5. Communication:
– Responsiveness: Gauge their communication efficiency and responsiveness.
– Language Proficiency: Ensure clear communication to avoid misunderstandings.
6. Cost and Terms:
– Pricing: Compare pricing with other manufacturers to ensure competitiveness.
– Payment Terms: Negotiate favorable payment terms and ensure they are flexible with payment options.
By combining these strategies, you can identify and select reliable CNC milling manufacturers in China that meet your quality and production requirements.
Background Research for cnc milling operations manufacturers Companies in China, use qcc.com archive.org importyeti.com
Researching CNC milling operations manufacturers in China yields a variety of companies that are leaders in the field. Here are a few noteworthy examples:
1. GSK CNC Equipment Co., Limited: Based in Guangzhou, this company is a major player in the CNC machinery industry. They specialize in the development and manufacturing of CNC systems and equipment, integrating advanced technology and innovation in their products. They are known for their comprehensive service and robust production capabilities【5†source】.
2. Dongguan Huayu Precision Technology Co., Ltd.: Located in Dongguan, this high-tech enterprise focuses on precision machining services. With a significant workforce, they are involved in scientific research and technological services, providing advanced CNC machining solutions to various industries【6†source】.
3. Changzhou Kuku CNC Technology Co., Ltd.: This small-scale company in Changzhou provides CNC equipment and related services. Despite its smaller size, it has carved out a niche in the local market, offering technical development, consulting, and sales of CNC equipment and accessories【7†source】.
4. Huagong Tech Co., Ltd.: Established in Wuhan, this company is part of a larger tech group. They specialize in manufacturing and technological innovation in the CNC machining sector, boasting a sizable team and substantial operational scale【8†source】.
5. Guangdong Guanghua Sci-Tech Co., Ltd.: Based in Shantou, this company has a long history and a significant presence in the manufacturing sector. They offer a variety of CNC machining services and have a strong focus on research and development to stay competitive【9†source】.
These companies highlight the diversity and strength of CNC milling operations in China, ranging from large enterprises with extensive capabilities to smaller firms with specialized expertise.
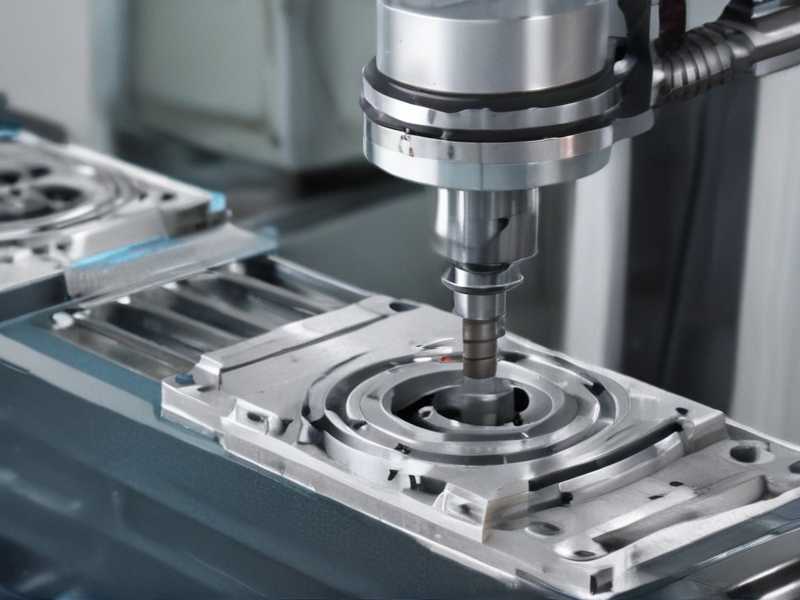
Price Cost Research for cnc milling operations manufacturers Companies in China, use temu.com and 1688.com
When researching CNC milling operations manufacturers in China, Temu.com and 1688.com offer various suppliers and products.
On Temu.com, the prices for CNC milling equipment and related products vary widely depending on the specifications and capabilities. For example, small desktop CNC milling machines are priced starting around $200, whereas larger, more industrial machines can range from $1,000 to $5,000 and above.
1688.com provides a more detailed view of CNC milling manufacturers. For instance, a variety of CNC engraving and milling machines are available, with prices for smaller units like the DIY small CNC engravers starting at approximately ¥104.5 (around $15) and going up to ¥1,710 (about $240) for more sophisticated laser engraving machines【9†source】【10†source】. High-precision milling equipment designed for industrial use is also available, with prices varying significantly based on complexity and production capacity.
Both platforms highlight a range of additional services, including bulk purchasing options, customization, and quick shipping, often within 48 hours. Manufacturers typically offer various models to cater to different industrial needs, from small-scale operations to large manufacturing plants.
For precise pricing and to ensure you get the best deal tailored to your specific requirements, it’s advisable to contact the suppliers directly through these platforms. This allows for negotiation on bulk orders and clarifications on machine specifications and capabilities.
Shipping Cost for cnc milling operations import from China
When importing CNC milling operations from China, shipping costs can vary widely based on several factors:
1. Shipping Method: The primary options are air freight and sea freight. Air freight is faster but more expensive, while sea freight is slower but more cost-effective for large shipments.
2. Weight and Volume: Shipping costs are calculated based on the greater of the actual weight or the volumetric weight. Bulky items can incur higher costs even if they are light.
3. Destination: Shipping costs depend on the distance between the port of origin in China and the destination port. Proximity to major ports can reduce costs.
4. Incoterms: These terms define the responsibilities of the buyer and seller regarding shipping costs. Common terms include FOB (Free on Board) and CIF (Cost, Insurance, and Freight).
5. Customs Duties and Taxes: Import duties, taxes, and customs clearance fees can significantly add to the total cost. These vary by country and product classification.
6. Additional Services: Services like insurance, warehousing, and handling fees at the port can increase the total cost.
Estimated Costs
For air freight, costs can range from $4 to $8 per kilogram. Sea freight costs are typically lower, averaging around $500 to $2,500 per 20-foot container, depending on the shipping route and current market conditions.
Practical Example
For a shipment weighing 500 kg:
– Air Freight: Approximately $2,000 to $4,000.
– Sea Freight: Approximately $500 to $1,500 for part of a container load.
Tips for Reducing Costs
– Consolidate Shipments: Combine multiple orders to reduce per-unit shipping costs.
– Flexible Timing: Opt for sea freight if time allows.
– Negotiate: Work with freight forwarders to get better rates.
In summary, careful planning and understanding of the various factors influencing shipping costs can help manage and reduce expenses when importing CNC milling operations from China.
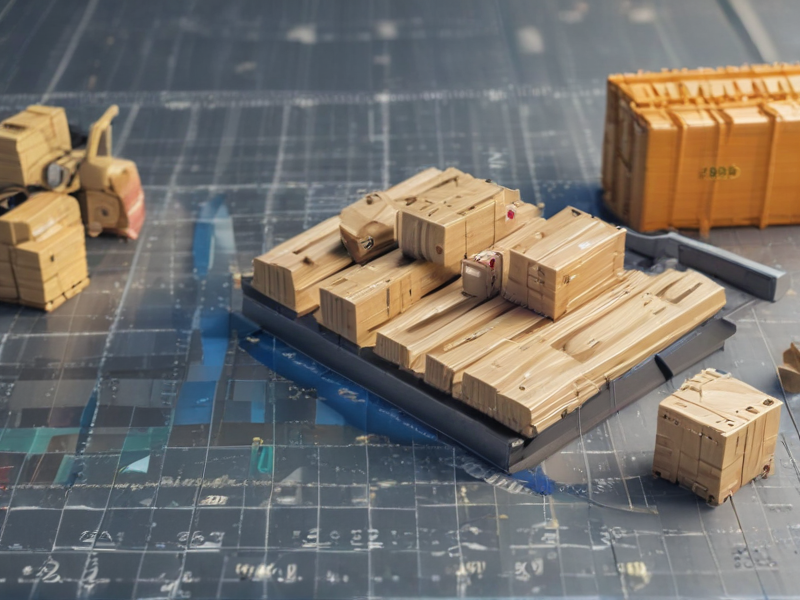
Compare China and Other cnc milling operations Markets: Products Quality and Price,Visible and Hidden Costs
China and other CNC milling operations markets differ notably in terms of product quality, price, and associated costs.
Product Quality:
Chinese CNC milling often emphasizes cost-efficiency, which can sometimes compromise quality. While many Chinese manufacturers produce high-quality parts, there are instances of variability in precision and material standards. In contrast, markets such as Germany, Japan, and the USA are renowned for their high-quality standards and consistent precision due to stringent manufacturing protocols and advanced technologies.
Price:
Chinese CNC milling services are typically cheaper due to lower labor costs and economies of scale. This makes them attractive for bulk orders and cost-sensitive projects. Conversely, CNC milling services in developed countries are generally more expensive due to higher labor costs, better working conditions, and more rigorous quality assurance processes.
Visible and Hidden Costs:
Visible costs, such as unit price per part, are lower in China. However, hidden costs can be significant. These include:
– Quality Control: More rigorous quality checks may be needed when sourcing from China, adding to the overall cost.
– Lead Time: Longer shipping times can delay projects, potentially increasing time-to-market.
– Communication and Coordination: Potential language barriers and different time zones can complicate project management.
– Customs and Tariffs: Import duties and taxes can add to the cost when sourcing from overseas.
– Rework and Returns: If quality issues arise, reworking parts or returns can be costly and time-consuming.
In contrast, while the upfront cost in countries like Germany or the USA is higher, hidden costs are often lower due to better quality control, faster lead times, more reliable communication, and fewer issues with rework.
In summary, while Chinese CNC milling offers cost advantages, the potential for hidden costs and quality variability necessitates careful consideration. Western markets, though pricier, provide higher and more consistent quality with fewer hidden costs, making them suitable for projects where precision and reliability are paramount.
Custom Private Labeling and Branding Opportunities with Chinese cnc milling operations Manufacturers
Chinese CNC milling operations manufacturers offer robust custom private labeling and branding opportunities, making them attractive for businesses aiming to establish or expand their own product lines.
1. Wide Range of Capabilities: Chinese manufacturers excel in producing complex and high-precision components using advanced CNC milling technology. They can cater to various industries, including automotive, aerospace, medical devices, and electronics, providing parts that meet stringent quality standards.
2. Customization: These manufacturers offer extensive customization options, allowing businesses to tailor products to specific needs. This includes adjustments in materials, dimensions, finishes, and tolerances. Custom branding can be integrated into the production process, such as engraving logos or part numbers directly onto the products.
3. Cost Efficiency: Due to lower labor and production costs, Chinese CNC milling operations can provide competitive pricing without compromising quality. This cost advantage is particularly beneficial for small and medium-sized enterprises looking to maximize their budget.
4. Scalability: Chinese manufacturers are equipped to handle both small and large-scale orders, providing flexibility as your business grows. This scalability ensures that you can start with smaller quantities and ramp up production as demand increases.
5. Advanced Technology: Many Chinese CNC milling manufacturers invest in state-of-the-art machinery and quality control systems, ensuring high precision and consistency in production. This technological edge helps maintain high standards and reliable delivery schedules.
6. Supply Chain Integration: Collaborating with Chinese manufacturers often comes with the added benefit of integrated supply chain solutions. Many manufacturers have established networks for sourcing raw materials, logistics, and export processes, simplifying the supply chain for your business.
7. Regulatory Compliance: Reputable Chinese CNC milling operations adhere to international standards such as ISO 9001, ensuring that products meet global quality and safety requirements.
By leveraging these opportunities, businesses can enhance their product offerings, maintain competitive pricing, and ensure high-quality output, ultimately strengthening their market position.
Tips for Procurement and Considerations when Purchasing cnc milling operations
When procuring CNC milling operations, careful consideration and strategic planning are essential for optimal performance and cost-efficiency. Here are some key tips and considerations:
1. Define Requirements:
– Material: Identify the materials you’ll be working with, as different materials require specific tools and machine capabilities.
– Precision and Tolerances: Determine the level of precision needed for your parts to ensure the machine meets these standards.
– Production Volume: Estimate the volume of production to choose a machine that can handle your workload efficiently.
2. Machine Specifications:
– Spindle Speed and Power: Ensure the machine’s spindle speed and power are suitable for the materials and type of milling operations you intend to perform.
– Axis Configuration: Consider the number of axes (e.g., 3-axis, 5-axis) based on the complexity of parts you need to produce.
– Work Envelope: Verify the machine’s work envelope (the maximum size of the part that can be machined) matches your requirements.
3. Software and Compatibility:
– CNC Software: Choose a machine compatible with your preferred CAD/CAM software for seamless integration and workflow.
– Updates and Support: Check for software updates and technical support availability from the manufacturer.
4. Cost Analysis:
– Initial Investment vs. Long-term Costs: Evaluate the total cost of ownership, including maintenance, operation, and potential downtime.
– Financing Options: Explore financing options or leasing if the initial investment is substantial.
5. Supplier Evaluation:
– Reputation and Reliability: Research suppliers’ reputations and customer reviews to ensure reliability.
– After-Sales Support: Consider the availability of after-sales services, spare parts, and technical support.
– Training and Installation: Ensure the supplier provides training for your staff and installation services.
6. Quality Assurance:
– Inspection and Testing: Check if the machine comes with quality assurance certifications and test it under working conditions before finalizing the purchase.
– Warranty: Ensure the machine has a comprehensive warranty covering key components.
By meticulously evaluating these factors, you can make informed decisions that enhance productivity, maintain high quality, and optimize costs in your CNC milling operations.
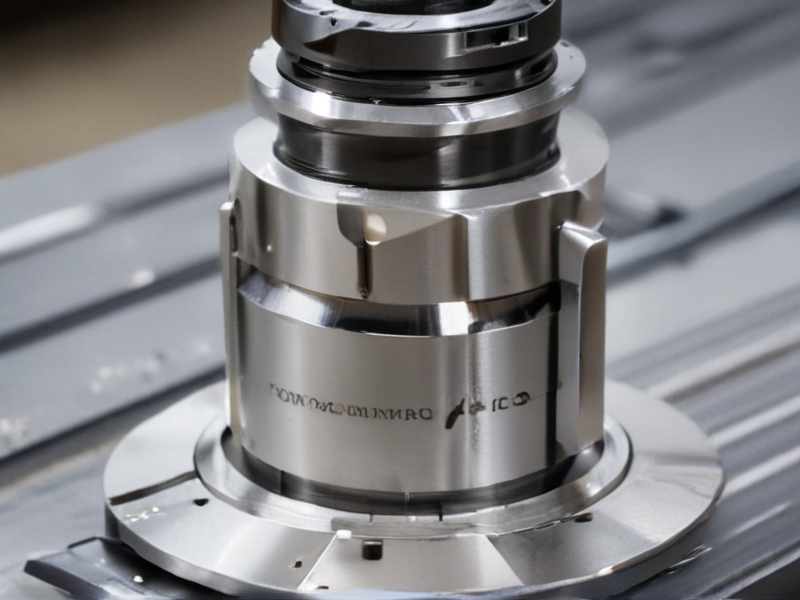
FAQs on Sourcing and Manufacturing cnc milling operations in China
FAQs on Sourcing and Manufacturing CNC Milling Operations in China
#### Why choose China for CNC milling operations?
China is a leading hub for CNC milling due to its advanced manufacturing capabilities, cost efficiency, and extensive supplier network. The country offers competitive pricing without compromising on quality, making it an attractive option for businesses globally.
#### What should I consider when selecting a CNC milling supplier in China?
Key factors include the supplier’s technical capabilities, quality control processes, certifications (e.g., ISO 9001), production capacity, and experience with similar projects. Additionally, check for clear communication channels and responsiveness.
#### How can I ensure the quality of CNC milled parts from China?
Quality assurance involves several steps:
1. Supplier Audits: Conduct on-site visits or virtual audits to evaluate facilities and processes.
2. Prototyping: Request prototypes to verify the quality before mass production.
3. Third-Party Inspections: Hire independent inspection agencies to perform quality checks.
4. Certificates and Standards: Ensure compliance with international standards like ISO, RoHS, and CE.
#### What are common challenges in CNC milling operations in China?
Challenges include language barriers, cultural differences, shipping delays, and potential quality issues. Mitigating these requires clear communication, well-defined specifications, regular quality checks, and reliable logistics partners.
#### How can intellectual property be protected when manufacturing in China?
To safeguard intellectual property (IP):
1. NDAs and Contracts: Sign Non-Disclosure Agreements (NDAs) and robust contracts outlining IP rights.
2. Patents and Trademarks: Register patents and trademarks in China.
3. Supplier Vetting: Choose reputable suppliers with a history of respecting IP.
#### What are the lead times for CNC milling projects in China?
Lead times vary based on project complexity, order size, and supplier workload. Generally, prototyping takes 1-3 weeks, while full production can range from 4-12 weeks. Discuss timelines upfront and include them in contracts to avoid delays.
#### How is pricing structured for CNC milling in China?
Pricing depends on factors such as material type, part complexity, volume, and surface finishing requirements. Obtain detailed quotes from multiple suppliers to compare costs and ensure transparency.