Top 10 cnc machine coolant in China introduce,list main products and website if have
Here are the top 10 CNC machine coolant manufacturers in China, their main products, and websites:
1. Blaser Swisslube China
– Main Products: Cutting oils, water-miscible coolants, grinding oils
– Website: [blaser.com](https://www.blaser.com)
2. FUCHS Lubricants China
– Main Products: Water-miscible coolants, neat oils, corrosion protection
– Website: [fuchs.com](https://www.fuchs.com/cn/zh/)
3. Yushiro Chemical Industry Co., Ltd.
– Main Products: Metalworking fluids, cutting and grinding fluids, rust preventatives
– Website: [yushiro.com](https://www.yushiro.com.cn/)
4. Total China
– Main Products: Cutting oils, soluble oils, synthetic and semi-synthetic coolants
– Website: [total.com](https://www.total.com.cn/)
5. MORESCO (Japan Moresco Co., Ltd. China)
– Main Products: Water-soluble coolants, neat cutting oils, grinding fluids
– Website: [moresco.com.cn](http://www.moresco.com.cn/)
6. Castrol China
– Main Products: Cutting fluids, grinding fluids, neat oils, synthetic coolants
– Website: [castrol.com](https://www.castrol.com/en_cn/china/home.html)
7. Quaker Houghton China
– Main Products: Cutting fluids, forming fluids, hydraulic fluids, cleaners
– Website: [quakerhoughton.com](https://www.quakerhoughton.com)
8. PetroChina Lubricant Company
– Main Products: Metalworking fluids, cutting oils, water-based coolants
– Website: [petrochina-lubes.com](http://www.petrochina-lubes.com)
9. Shell China
– Main Products: Metalworking fluids, neat oils, water-soluble coolants
– Website: [shell.com.cn](https://www.shell.com.cn/)
10. Sinopec Lubricant Co., Ltd.
– Main Products: Cutting oils, grinding fluids, synthetic and semi-synthetic coolants
– Website: [sinopec.com](http://www.sinopec.com)
These companies offer a wide range of CNC machine coolants designed to enhance machining efficiency, tool life, and surface finish quality.
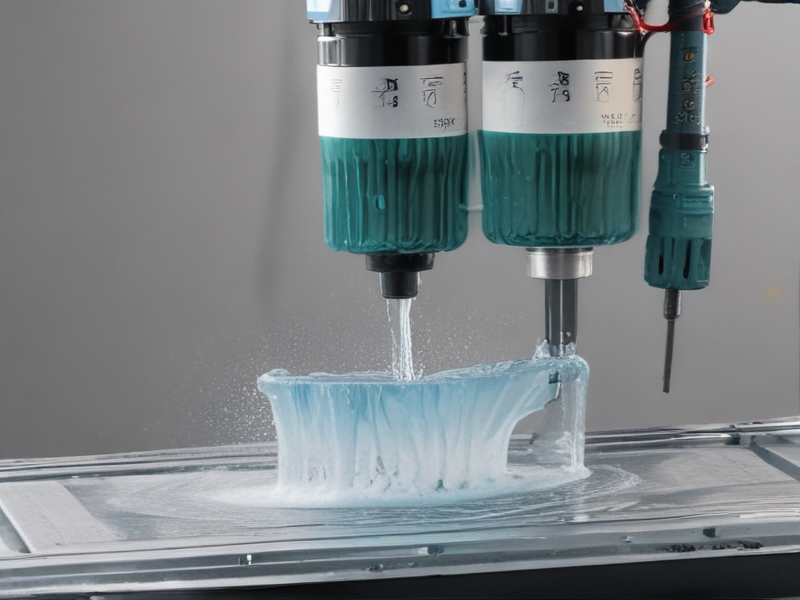
Types of cnc machine coolant
CNC machine coolants are essential for reducing heat, lubricating, and removing chips during machining processes. Here are the main types:
1. Soluble Oils:
– Description: A blend of oil and water, soluble oils are diluted to create an emulsion.
– Pros: Excellent cooling and lubricating properties, cost-effective.
– Cons: Can become rancid and develop bacteria without proper maintenance.
2. Synthetic Fluids:
– Description: Made entirely from chemical compounds, containing no petroleum oils.
– Pros: Superior cooling, longer lifespan, lower disposal costs, minimal bacterial growth.
– Cons: May provide less lubrication than soluble oils, higher initial cost.
3. Semi-Synthetic Fluids:
– Description: A hybrid of soluble oils and synthetic fluids, containing a small amount of oil.
– Pros: Balance of cooling and lubrication, better resistance to bacteria than soluble oils.
– Cons: More expensive than soluble oils, less effective than pure synthetics in extreme conditions.
4. Straight Oils:
– Description: Undiluted petroleum or mineral oils.
– Pros: Superior lubrication, great for heavy-duty machining.
– Cons: Poor cooling, higher viscosity, messy, and can be more costly.
5. Paste, Gel, and Solid Lubricants:
– Description: These are applied directly to the cutting tool.
– Pros: Targeted application, minimal waste, ideal for specific tasks.
– Cons: Limited cooling properties, can be more labor-intensive to apply.
6. MQL (Minimum Quantity Lubrication):
– Description: Uses very small amounts of lubricant delivered directly to the cutting zone.
– Pros: Reduces fluid consumption and disposal costs, environmentally friendly.
– Cons: Limited cooling capability, may not be suitable for high-speed or heavy-duty machining.
Each coolant type has its specific advantages and disadvantages, making them suitable for different machining needs and materials.
Pros and Cons of Using cnc machine coolant
Using CNC machine coolant has its benefits and drawbacks. Here’s a concise overview:
Pros:
1. Cooling: Coolant helps dissipate heat generated during machining, which prevents thermal damage to both the workpiece and the cutting tool. This leads to better dimensional accuracy and surface finish.
2. Lubrication: It reduces friction between the cutting tool and the workpiece, which minimizes wear on the tool and prolongs its life.
3. Chip Removal: Coolant aids in flushing away chips and debris from the cutting zone, preventing them from causing damage or interfering with the cutting process.
4. Improved Cutting Speeds: With better cooling and lubrication, higher cutting speeds and feeds can be achieved, improving productivity.
5. Surface Finish: The use of coolant often results in smoother surface finishes on the machined parts.
Cons:
1. Cost: The purchase, maintenance, and disposal of coolant can be expensive. This includes the cost of coolant itself, as well as systems for filtering and recycling.
2. Health and Safety: Some coolants can cause skin irritation or respiratory issues for workers. Proper handling and protective equipment are essential.
3. Environmental Impact: Disposal of used coolant can be challenging and environmentally harmful if not done properly. Coolants can contaminate water sources if not disposed of correctly.
4. Maintenance: Coolant systems require regular monitoring and maintenance to ensure they are functioning correctly and to prevent bacterial growth and foul odors.
5. Compatibility Issues: Certain coolants may not be compatible with all materials or cutting tools, potentially limiting their use or requiring multiple types of coolant for different applications.
In conclusion, while CNC machine coolant significantly enhances machining performance and tool longevity, it also presents challenges related to cost, health, environmental impact, and maintenance. Balancing these factors is crucial for optimal use.
cnc machine coolant Reference Specifications (varies for different product)
Coolants for CNC machines are essential for maintaining the performance and longevity of the machinery. They serve to reduce friction, prevent overheating, and remove swarf from the cutting area. Below are some key specifications and considerations for CNC machine coolants:
Types of Coolants
1. Soluble Oils: Oil emulsions in water, offering good lubrication and cooling.
2. Synthetic Fluids: Water-based solutions with no oil content, providing excellent cooling and chip removal.
3. Semi-Synthetic Fluids: Combination of soluble oils and synthetic fluids, balancing lubrication and cooling.
4. Straight Oils: Non-water-miscible oils, offering superior lubrication but limited cooling.
Key Specifications
1. Concentration: Typically mixed with water in ratios ranging from 1:20 to 1:40. The exact concentration depends on the material being machined and the type of operation.
2. pH Level: Ideal pH levels range from 8.5 to 9.5 to prevent corrosion and maintain stability.
3. Lubricity: The coolant should provide sufficient lubrication to reduce tool wear and improve surface finish.
4. Cooling Efficiency: The coolant must dissipate heat effectively to prevent thermal deformation of the workpiece.
5. Biostability: Resistant to microbial growth to extend the coolant’s usable life and reduce maintenance.
6. Foaming Tendency: Low foaming properties to ensure clear visibility and consistent performance during high-speed operations.
7. Corrosion Inhibition: Should protect both the machine and workpieces from rust and corrosion.
Application Considerations
– Material Compatibility: Ensure the coolant is compatible with the materials being machined (e.g., aluminum, steel, titanium).
– Environmental and Health Safety: Choose coolants with low toxicity and minimal environmental impact.
– Maintenance: Regular monitoring of concentration, pH, and contamination levels is necessary to maintain effectiveness.
Example Products
1. Mobilcut Series: Offers a range of soluble, semi-synthetic, and synthetic coolants tailored for various machining operations.
2. Blaser Blasocut: Known for biostable formulations that extend coolant life and improve workplace safety.
3. Cimcool Cimstar: Provides high performance in both ferrous and non-ferrous metalworking applications.
By selecting the appropriate coolant and adhering to these specifications, CNC machine operators can ensure optimal performance, tool life, and workpiece quality.
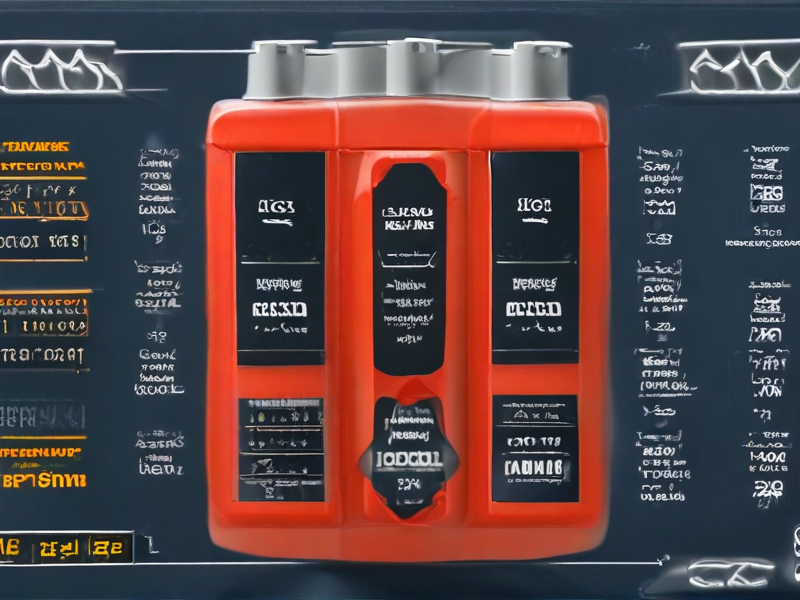
Applications of cnc machine coolant
CNC machine coolant serves several crucial functions in the machining process:
1. Temperature Control: Coolants help to dissipate the heat generated during machining. This prevents overheating, which can cause thermal distortion of both the workpiece and the cutting tool, ensuring dimensional accuracy and prolonging tool life.
2. Lubrication: By reducing friction between the cutting tool and the workpiece, coolants minimize wear on the tools and help achieve smoother finishes. This is particularly important in high-precision operations.
3. Chip Removal: Coolants assist in flushing away chips and debris from the cutting area. This not only maintains a clear work area but also prevents the re-cutting of chips, which can damage the tool and the workpiece.
4. Surface Finish Improvement: Coolants can enhance the surface finish of the machined parts by reducing tool wear and cooling the workpiece evenly. This is especially critical in industries where high-quality surface finishes are required, such as in aerospace and automotive applications.
5. Corrosion Prevention: Many coolants contain additives that prevent rust and corrosion on both the machine parts and the workpieces. This extends the life of the machinery and the finished products, particularly important in long-term storage or in humid environments.
6. Tool Life Extension: By providing adequate cooling and lubrication, coolants significantly extend the life of cutting tools, reducing the frequency of tool changes and downtime, thus improving overall productivity and reducing operational costs.
7. Environmental and Safety Considerations: Modern coolants are designed to be more environmentally friendly and safer for operators, with reduced toxicity and better biodegradability. This addresses health concerns and regulatory compliance in industrial settings.
In summary, CNC machine coolants are essential for maintaining optimal machining conditions, improving the quality of machined parts, and extending the lifespan of tools and equipment.
Material of cnc machine coolant
CNC machine coolant, essential for metalworking operations, primarily comprises water-based or oil-based fluids. The primary materials include:
1. Water-Soluble Oils: These coolants are emulsions of oil and water, providing good cooling and lubrication. They are effective for general-purpose machining and have high lubricity, which reduces tool wear.
2. Synthetic Fluids: Made from chemical compounds, these coolants contain no oil and offer excellent cooling properties. They are ideal for high-speed applications and do not leave a sticky residue, facilitating easier cleaning and better visibility of the workpiece.
3. Semi-Synthetic Fluids: These are a blend of synthetic and soluble oil fluids, offering a balance between cooling, lubrication, and rust prevention. They provide better lubrication than synthetics but are cleaner and more stable than soluble oils.
4. Straight Oils: These non-water-miscible oils offer superior lubrication and are used in low-speed operations where high lubricity is crucial, such as in heavy-duty machining. They help extend tool life but have less cooling capacity compared to water-based coolants.
5. Micro-emulsions: These are finely dispersed emulsions that combine the benefits of both soluble oils and synthetic coolants. They provide excellent cooling and lubrication properties and are effective in both high-speed and heavy-duty machining operations.
Additives such as biocides, corrosion inhibitors, anti-foaming agents, and lubricity enhancers are often included to improve the performance and longevity of the coolant.
The choice of coolant material depends on factors such as the type of machining operation, the material being machined, and the desired balance between cooling and lubrication. Proper maintenance and monitoring of coolant composition and concentration are crucial for optimal performance and longevity of both the coolant and the machinery.
Quality Testing Methods for cnc machine coolant and how to control the quality
Quality testing for CNC machine coolant involves several methods to ensure its effectiveness and longevity. Key tests include:
1. Concentration Testing: Using a refractometer or chemical titration to measure the concentration of the coolant mix. Maintaining proper concentration prevents corrosion and ensures lubrication.
2. pH Level Testing: Monitoring the pH with pH strips or meters to keep it within the optimal range (typically 8.5-9.5). A stable pH prevents bacterial growth and material corrosion.
3. Contamination Testing: Checking for contaminants like tramp oil, metal particles, and bacteria. Tramp oil can be identified through visual inspection or oil skimmers. Bacterial contamination is tested using dip slides or microbial test kits.
4. Water Hardness Testing: Measuring water hardness using titration or hardness test strips. Hard water can cause scaling and reduce coolant effectiveness.
To control the quality of CNC machine coolant:
1. Regular Monitoring: Implement a routine schedule for testing concentration, pH, and contamination. This allows for early detection of issues and timely corrective action.
2. Coolant Filtration: Use filtration systems to remove metal particles and other debris, maintaining coolant cleanliness and extending its life.
3. Tramp Oil Management: Employ oil skimmers or separators to remove tramp oil, which can degrade coolant and foster bacterial growth.
4. Proper Mixing: Ensure the coolant is mixed according to the manufacturer’s specifications to maintain the correct concentration and properties.
5. Coolant Replacement: Follow a periodic replacement schedule based on coolant condition and machine usage to prevent degradation and contamination buildup.
6. Water Quality Management: Use treated or softened water to mix coolant to prevent scaling and other issues associated with hard water.
Implementing these testing methods and control measures ensures the CNC machine coolant remains effective, thereby protecting machinery, enhancing performance, and reducing downtime.
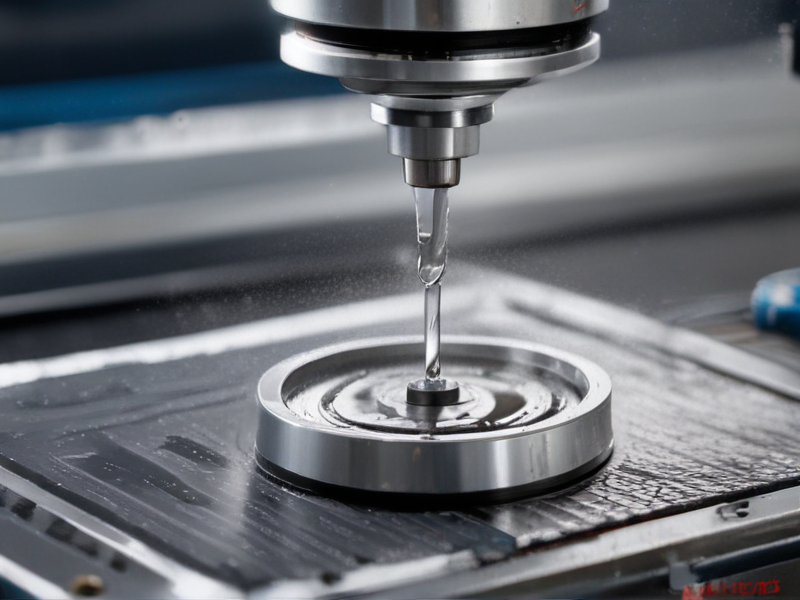
The Work Process and how to use cnc machine coolant
Work Process of Using CNC Machine Coolant
1. Preparation
– Selection: Choose the appropriate type of coolant (water-soluble, synthetic, semi-synthetic, or straight oils) based on the material and operation.
– Mixing: Dilute the coolant according to manufacturer guidelines. Use a refractometer to ensure proper concentration.
2. Setup
– Reservoir Check: Ensure the coolant reservoir is clean and free from contaminants.
– Filling: Fill the reservoir with the prepared coolant mix. Make sure it’s at the correct level.
– Filtration: Install any necessary filters to keep the coolant clean during operations.
3. Operation
– Flow Adjustment: Set the flow rate to ensure proper coverage and cooling of the tool and workpiece.
– Monitoring: Regularly check the coolant levels and concentration. Top up as needed.
– Performance Check: Observe the machining process to ensure the coolant is effectively reducing heat and removing chips.
4. Maintenance
– Regular Cleaning: Periodically clean the coolant system to prevent the buildup of bacteria, fungi, or sludge.
– Filter Replacement: Replace filters as needed to maintain coolant quality.
– Concentration Testing: Routinely test and adjust the coolant concentration.
Using CNC Machine Coolant
1. Prepare the coolant mix: Follow the manufacturer’s guidelines for the specific material and operation.
2. Fill the coolant system: Pour the mixed coolant into the machine’s reservoir.
3. Adjust the flow rate: Ensure the coolant covers the cutting area adequately.
4. Monitor and maintain: Keep an eye on coolant levels, concentration, and cleanliness, adjusting as necessary.
Tips
– Safety: Always wear protective gear and follow safety protocols.
– Documentation: Keep records of coolant usage, changes, and concentrations for optimal performance and troubleshooting.
– Environment: Dispose of used coolant responsibly according to local regulations.
This ensures efficient operation, tool longevity, and high-quality machined parts.
cnc machine coolant Importing questions including Cost,Supplier,Sample,Certification and Market
Importing CNC Machine Coolant: Key Considerations
#### Cost
The cost of importing CNC machine coolant depends on factors like volume, type (synthetic, semi-synthetic, or soluble oil), shipping method, and tariffs. Prices typically range from $3 to $10 per liter, excluding shipping and import duties. Bulk orders can reduce per-unit costs.
#### Supplier
Select reputable suppliers to ensure quality and compliance. Key suppliers include Blaser Swisslube, Castrol, and ExxonMobil. Verify suppliers through trade directories like Alibaba, Global Sources, or industry-specific expos. Check for customer reviews and testimonials to gauge reliability.
#### Sample
Request samples before placing large orders. Most suppliers provide samples either for free or at a nominal cost. Evaluate the sample for performance, compatibility with your CNC machines, and adherence to your requirements. Testing can prevent costly mistakes.
#### Certification
Ensure the coolant meets relevant certifications and standards. Common certifications include ISO 9001 for quality management and ISO 14001 for environmental management. Additionally, ensure compliance with local regulations such as REACH (Registration, Evaluation, Authorisation, and Restriction of Chemicals) in the EU or EPA (Environmental Protection Agency) standards in the US.
#### Market
The market for CNC machine coolant is expanding due to increased automation and manufacturing activities. Key markets include the US, Germany, China, and Japan. Staying updated with market trends and technological advancements can help in making informed purchasing decisions.
Summary
Importing CNC machine coolant involves understanding costs, choosing reliable suppliers, evaluating samples, ensuring certification compliance, and being aware of market trends. Proper research and due diligence are crucial for cost-effective and efficient importation.
How to find and select check reliable cnc machine coolant manufacturers in China
Finding and selecting reliable CNC machine coolant manufacturers in China involves several steps:
1. Research and Identification:
– Online Directories: Use platforms like Alibaba, Made-in-China, and Global Sources to identify potential manufacturers. These sites often provide company profiles, product listings, and customer reviews.
– Industry Associations: Check Chinese industry associations related to CNC machining and coolants for recommended manufacturers.
2. Evaluate Credentials:
– Certifications: Verify that manufacturers have relevant certifications such as ISO 9001 for quality management and ISO 14001 for environmental management.
– Compliance: Ensure they comply with international standards and have safety data sheets (SDS) for their products.
3. Assess Experience and Reputation:
– Company History: Look for manufacturers with a long history and substantial experience in producing CNC machine coolants.
– Reviews and Testimonials: Read customer reviews and testimonials to gauge the reliability and quality of their products.
4. Direct Communication:
– Inquiries: Contact the manufacturers directly to inquire about their products, production capacity, and quality control measures.
– Samples: Request product samples to test for quality and compatibility with your machines.
5. Factory Visits and Audits:
– On-Site Visits: If possible, visit the manufacturing facilities to inspect their production processes, quality control systems, and working conditions.
– Third-Party Audits: Hire a third-party inspection company to conduct a detailed audit of the factory.
6. Comparison and Selection:
– Quotes and Terms: Compare quotes, payment terms, and delivery timelines from different manufacturers.
– Service and Support: Consider the level of customer service and technical support offered.
By following these steps, you can identify and select reliable CNC machine coolant manufacturers in China, ensuring high-quality products and dependable supply chains.
Background Research for cnc machine coolant manufacturers Companies in China, use qcc.com archive.org importyeti.com
In China, several companies specialize in manufacturing CNC machine coolants. Some notable manufacturers include:
1. Changzhou KUKU CNC Technology Co., Ltd. Established in 2016, this company is based in Changzhou, Jiangsu Province. It focuses on producing and distributing CNC machine coolants and other related products【5†source】.
2. Shanghai Xuantian Intelligent Technology Co., Ltd. Founded in 2007 and located in Shanghai, this company manufactures industrial equipment and consumables, including CNC machine coolants. It is well-regarded in the field for its innovative technology and comprehensive product offerings【6†source】.
3. Hangzhou Hikrobot Technology Co., Ltd. This company, established in 2016, is based in Hangzhou and is a subsidiary of the China Electronics Technology Group. While primarily known for robotics and automation solutions, it also produces various industrial fluids, including CNC machine coolants【7†source】.
4. Chongqing Xinhui Material Technology Co., Ltd. A newer entrant in the market, founded in 2022 and based in Chongqing, it focuses on advanced material technologies, including coolants for CNC machinery【8†source】.
5. Shenzhen Yilian Technology Co., Ltd. Founded in 2011, this Shenzhen-based company produces a wide range of industrial products, including high-performance CNC machine coolants. It is known for its robust R&D capabilities and extensive distribution network【9†source】.
These companies leverage China’s strong manufacturing base and advanced technology to produce high-quality CNC machine coolants, catering to both domestic and international markets.
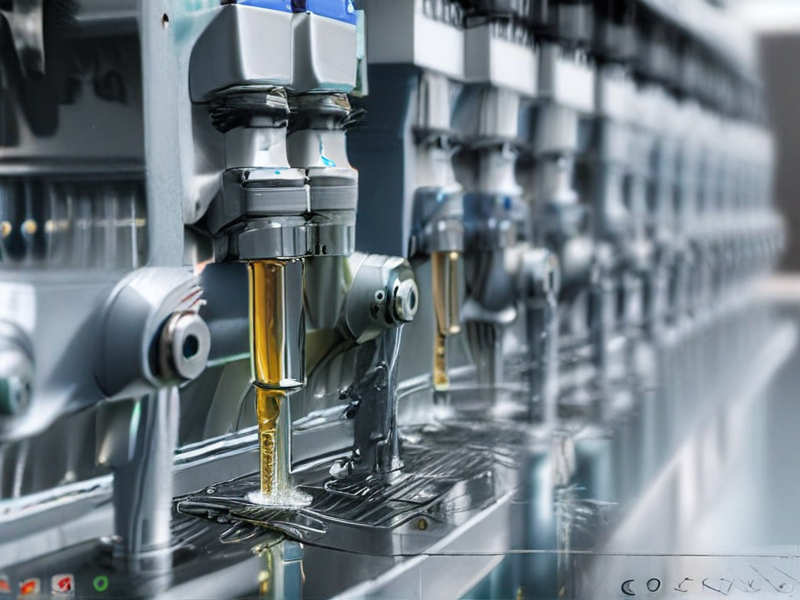
Price Cost Research for cnc machine coolant manufacturers Companies in China, use temu.com and 1688.com
When researching CNC machine coolant manufacturers in China, using platforms like Temu.com and 1688.com, several manufacturers and price ranges can be found.
On Temu.com, CNC machine coolant prices vary widely depending on the type and quantity. For example, coolant concentrates for CNC machines are listed with prices starting at approximately $10 per liter for smaller quantities. Bulk purchases can offer better rates, with discounts provided for larger orders. Temu.com offers a variety of coolants suitable for different machining needs, from basic coolants to more advanced formulations designed for high-performance applications.
On 1688.com, which is a part of the Alibaba group, prices also vary. Basic water-soluble coolants are available starting at around ¥40 (~$6) per liter. For specialized high-performance coolants, prices can go up to ¥100 (~$15) per liter or more, depending on the brand and specific properties required, such as anti-rust, lubrication, and cooling efficiency. Manufacturers such as Shenzhen Yidafeng Hardware Materials Co., Ltd., and others offer a wide range of products with detailed specifications and bulk purchase options【7†source】【8†source】【9†source】【10†source】.
In summary, both Temu.com and 1688.com provide a broad spectrum of CNC machine coolants with varying prices based on performance and quantity. Buyers can find basic coolants at lower prices, while high-performance variants are available at higher costs, often with discounts for bulk purchases.
Shipping Cost for cnc machine coolant import from China
To estimate the shipping cost for importing CNC machine coolant from China, consider the following factors:
1. Weight and Volume: Shipping costs are calculated based on the weight and volume of the shipment. CNC machine coolant is typically heavy, so weight will significantly impact the cost.
2. Shipping Method:
– Air Freight: Faster but more expensive, suitable for urgent or smaller shipments.
– Sea Freight: Cheaper for larger volumes but slower.
3. Distance: Costs vary depending on the distance between the Chinese port and the destination.
4. Customs and Duties: Import duties, taxes, and fees vary by country and must be considered in the total cost.
5. Freight Forwarder: Using a freight forwarder can streamline the process and might offer better rates due to their volume of shipments.
Example Calculation
For a typical 20-foot container (TEU) of CNC machine coolant:
– Sea Freight:
– Cost: Approximately $1,000 – $3,000 depending on the port of origin and destination.
– Transit Time: 20-30 days.
– Air Freight:
– Cost: Approximately $5 – $10 per kilogram.
– Transit Time: 3-7 days.
Additional Costs
– Insurance: Typically 0.3% – 0.5% of the cargo value.
– Handling Fees: Varies, often $100 – $500.
– Customs Duties: Varies by destination country (e.g., 2%-10% of the cargo value).
Example
For 1,000 kg of coolant shipped by air:
– Cost: 1,000 kg * $7/kg = $7,000.
– Customs Duties (e.g., 5%): $7,000 * 0.05 = $350.
– Total Cost: $7,350 plus any additional fees.
For a 20-foot container (approximately 20,000 kg) by sea:
– Cost: $2,000 (sea freight) + duties + additional fees.
– Customs Duties (e.g., 5%): (Cargo value estimate) $50,000 * 0.05 = $2,500.
– Total Cost: $4,500 + additional fees.
Conclusion
Sea freight is generally more cost-effective for large volumes, while air freight is suitable for smaller, urgent shipments. Always account for additional fees and customs duties in your total cost estimation.
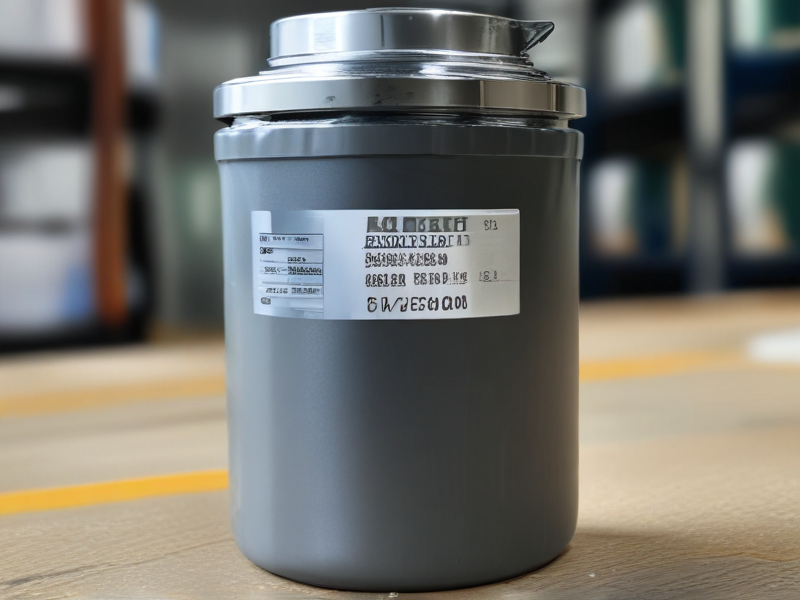
Compare China and Other cnc machine coolant Markets: Products Quality and Price,Visible and Hidden Costs
Comparing the CNC machine coolant markets in China with those in other regions involves examining product quality, pricing, and both visible and hidden costs.
Product Quality:
– China: Chinese CNC machine coolants often offer adequate performance for standard applications. However, there can be variability in quality due to differing manufacturing standards and regulations. Advanced and specialty coolants may lag behind in innovation and performance compared to those from more established markets.
– Other Markets (e.g., USA, Germany, Japan): These regions typically provide high-quality CNC coolants with consistent performance and compliance with stringent industry standards. They often lead in innovation, offering specialized coolants for high-precision or high-speed machining.
Pricing:
– China: CNC machine coolants from China are generally more affordable, making them attractive for cost-sensitive operations. The lower price is primarily due to cheaper raw materials, labor costs, and less stringent regulatory frameworks.
– Other Markets: Coolants from the USA, Germany, and Japan are usually more expensive. The higher costs reflect superior quality control, advanced research and development, and compliance with strict environmental and safety standards.
Visible and Hidden Costs:
– China:
– Visible Costs: Lower upfront costs for purchasing coolants.
– Hidden Costs: Potential hidden costs include shorter lifespan of the coolant, increased machine wear and tear due to inconsistent coolant quality, and possible higher maintenance costs. Additionally, there may be environmental compliance issues leading to potential fines or additional treatment costs.
– Other Markets:
– Visible Costs: Higher initial purchase costs.
– Hidden Costs: These coolants generally incur fewer hidden costs. Their superior quality can lead to longer coolant life, better machine performance, reduced maintenance, and less frequent replacements. Compliance with environmental standards is typically built-in, reducing the risk of fines or extra processing costs.
In summary, while Chinese CNC machine coolants are cost-effective upfront, the potential for higher hidden costs and variable quality can offset initial savings. Coolants from more established markets, though pricier, tend to offer better overall value due to their reliability, longer lifespan, and adherence to stringent standards.
Custom Private Labeling and Branding Opportunities with Chinese cnc machine coolant Manufacturers
Partnering with Chinese CNC machine coolant manufacturers for custom private labeling and branding offers several significant advantages. These manufacturers are renowned for their cost-effective production capabilities and flexibility in meeting specific customer requirements, making them ideal partners for businesses looking to establish or expand their branded product lines.
1. Cost Efficiency: Chinese manufacturers often provide competitive pricing due to lower production costs. This can translate into higher margins for your private label products.
2. Customization: Many manufacturers offer extensive customization options, allowing you to tailor formulations, packaging, and labeling to meet your brand’s specifications. This includes options for eco-friendly coolants, various viscosity levels, and specific chemical compositions.
3. Quality and Compliance: Reputable Chinese manufacturers adhere to international quality standards such as ISO certifications. Ensuring that your products meet regulatory requirements for different markets is crucial, and many manufacturers can provide necessary compliance documentation.
4. MOQ Flexibility: Minimum order quantities (MOQs) can be more flexible, enabling smaller businesses to enter the market without the need for large initial investments.
5. Innovation and R&D: Many Chinese manufacturers invest in research and development, allowing them to offer the latest advancements in coolant technology. This can help your brand stay competitive by offering cutting-edge products.
6. Logistics and Lead Time: Efficient logistics and shorter lead times due to proximity to major shipping hubs ensure timely delivery of your products, facilitating smoother supply chain management.
7. Partnership and Support: Building a strong relationship with your manufacturer can provide additional benefits such as technical support, marketing materials, and after-sales service, helping your brand to grow sustainably.
In conclusion, leveraging the capabilities of Chinese CNC machine coolant manufacturers for private labeling can provide substantial benefits in terms of cost, quality, customization, and market readiness, making it a viable strategy for businesses looking to enhance their brand presence in the industrial sector.
Tips for Procurement and Considerations when Purchasing cnc machine coolant
When procuring CNC machine coolant, it’s essential to consider the following tips and factors:
1. Coolant Type:
– Soluble Oils: Offer excellent lubrication and cooling but can be prone to bacterial growth.
– Synthetic Fluids: Provide good cooling and are resistant to bacterial growth, but may offer less lubrication.
– Semi-synthetic Fluids: A balance between soluble oils and synthetic fluids, offering good cooling and lubrication.
2. Material Compatibility: Ensure the coolant is suitable for the materials you are machining, such as aluminum, steel, or titanium, to prevent chemical reactions that could damage the workpiece.
3. Machine Compatibility: Verify that the coolant is compatible with your CNC machine’s components, including seals and pumps, to prevent corrosion or degradation.
4. Concentration and Dilution: Check the recommended concentration levels and dilution ratios for optimal performance and cost-effectiveness.
5. Health and Safety: Evaluate the coolant for potential health hazards. Look for coolants with low toxicity and minimal fumes to ensure a safer working environment.
6. Environmental Impact: Consider the environmental regulations and disposal requirements. Opt for biodegradable coolants to minimize environmental impact.
7. Cost and Efficiency: Balance the initial cost with the long-term performance. A higher upfront cost might be justified if the coolant has a longer lifespan and better efficiency.
8. Maintenance Requirements: Understand the maintenance needs, including filtration, monitoring concentration, and bacterial control, to ensure consistent performance and longevity.
9. Supplier Reliability: Choose reputable suppliers with good customer service, technical support, and consistent supply to avoid downtime.
10. Performance Reviews: Check reviews and get feedback from other users to gauge the coolant’s real-world performance.
By considering these factors, you can ensure the procurement of a CNC machine coolant that optimizes machining performance, prolongs tool life, and maintains a safe working environment.
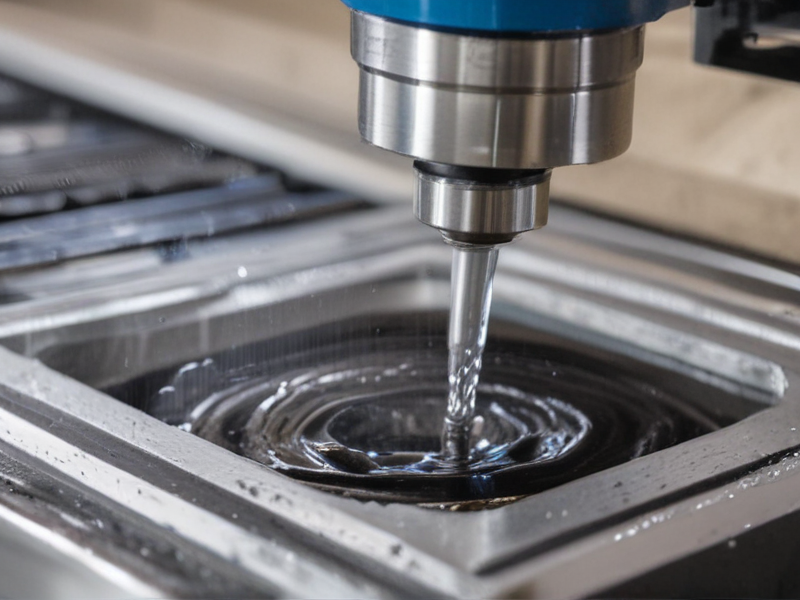
FAQs on Sourcing and Manufacturing cnc machine coolant in China
FAQs on Sourcing and Manufacturing CNC Machine Coolant in China
#### 1. Why source CNC machine coolant from China?
China is a global leader in manufacturing, offering competitive prices, advanced technology, and a vast supplier network. This makes it a cost-effective and efficient option for sourcing CNC machine coolant.
#### 2. What are the main types of CNC machine coolants available?
– Water-Soluble Coolants: Offer good cooling and lubrication.
– Semi-Synthetic Coolants: Blend of synthetic and soluble coolants, balancing cost and performance.
– Synthetic Coolants: Provide excellent lubrication and are suitable for high-speed machining.
#### 3. How do I find reliable suppliers?
Utilize platforms like Alibaba, Made-in-China, and Global Sources. Additionally, attending trade shows like the China International Machine Tool Show (CIMT) can help in networking with reputable suppliers.
#### 4. What are the key factors to consider when selecting a supplier?
– Quality Certifications: Ensure the supplier has ISO certifications and adheres to international standards.
– Production Capacity: Confirm the supplier can meet your volume requirements.
– R&D Capabilities: A supplier with strong R&D can offer customized solutions.
– Customer Reviews and References: Check reviews and request references to gauge reliability and service quality.
#### 5. What is the typical lead time for production and delivery?
Lead times can vary based on order size and customization but generally range from 4 to 8 weeks. Factor in additional time for shipping and customs clearance.
#### 6. What are the common payment terms?
Typical payment terms include a 30% deposit upfront and 70% upon shipment. Letters of credit and other secure payment methods are also used to mitigate risk.
#### 7. How can I ensure the quality of the coolant?
– Sample Testing: Request samples for testing before placing a bulk order.
– Third-Party Inspection: Employ inspection services to verify quality and compliance with specifications.
#### 8. What are the shipping and import considerations?
– Shipping Costs: Consider the mode of transport (air or sea) and associated costs.
– Customs Duties and Regulations: Be aware of import duties and ensure compliance with your country’s regulations regarding chemical imports.
By addressing these key areas, you can effectively source high-quality CNC machine coolant from China while managing risks and ensuring smooth operations.