Top 10 cnc machine centers in China introduce,list main products and website if have
Here’s a summary of the top 10 CNC machine centers in China, including their main products and websites:
1. DMG MORI China
Main Products: High-precision CNC turning centers, milling machines, and hybrid machines.
Website: [DMG MORI China](https://cn.dmgmori.com)
2. HAAS Automation China
Main Products: CNC vertical and horizontal machining centers, lathes.
Website: [HAAS Automation China](https://www.haascnc.com.cn)
3. Makino China
Main Products: High-speed milling machines, EDM, and grinding.
Website: [Makino China](https://www.makino.com.cn)
4. HURCO China
Main Products: CNC machining centers, 3-axis and 5-axis milling machines.
Website: [HURCO China](https://www.hurco.com)
5. Yamazaki Mazak China
Main Products: CNC lathes, machining centers, laser processing machines.
Website: [Mazak China](https://www.mazak.com.cn)
6. DMTG (Dalian Machine Tool Group)
Main Products: CNC turning centers, machining centers, and gear machinery.
Website: [DMTG](http://www.dmtg.com)
7. Shenyang Machine Tool Co., Ltd. (SMTCL)
Main Products: CNC lathes, machining centers, and specialized machine tools.
Website: [SMTCL](http://www.smtcl.com)
8. QIER Machine Tool Group
Main Products: CNC horizontal and vertical machining centers, milling machines.
Website: [QIER Machine Tool](http://www.qrmt.cn)
9. Jinan First Machine Tool
Main Products: CNC vertical and horizontal machining centers.
Website: [Jinan First Machine Tool](http://www.jnfirstmt.com)
10. Nanjing CNC Machine Co., Ltd.
Main Products: CNC vertical machining centers, turning centers.
Website: [Nanjing CNC](http://www.njcj.com)
These companies are prominent in the Chinese CNC machine market, offering a range of high-tech machining solutions tailored to various industrial needs.
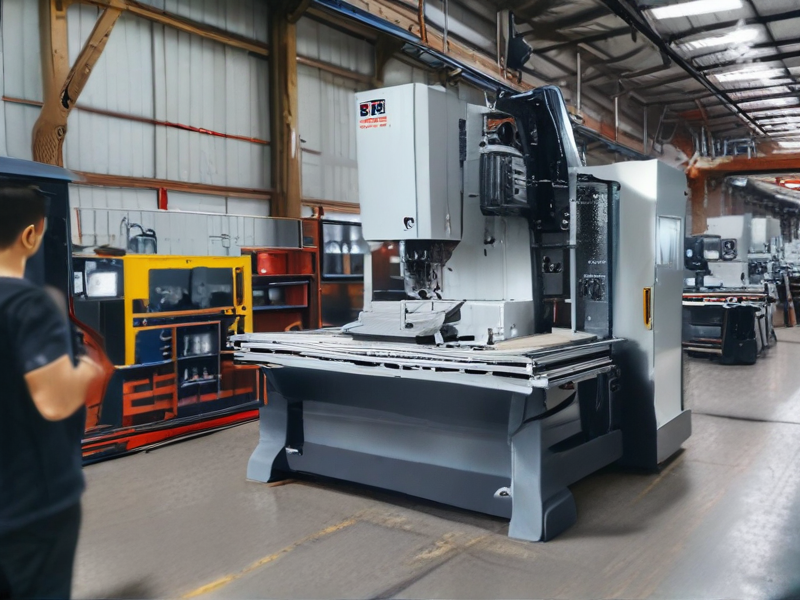
Types of cnc machine centers
CNC machine centers are versatile machining tools used extensively in manufacturing for precision tasks. Here are the main types:
1. Vertical Machining Centers (VMCs)
– Structure: The spindle is vertically oriented.
– Application: Ideal for flat surfaces, making it suitable for die sinking and mold-making.
– Advantages: Easy setup and programming, good for smaller workpieces and detailed operations.
2. Horizontal Machining Centers (HMCs)
– Structure: The spindle is horizontally oriented.
– Application: Best for parts requiring multiple sides to be machined, such as automotive parts.
– Advantages: Efficient chip removal, better surface finish, and can handle larger workpieces.
3. 5-Axis Machining Centers
– Structure: The cutting tool moves along five different axes simultaneously.
– Application: Complex geometries and intricate parts, often used in aerospace and medical industries.
– Advantages: Reduces setup time, increases precision, and allows for complex shapes and details.
4. Turning Centers
– Structure: Used for operations like turning, where the workpiece rotates.
– Application: Cylindrical parts such as shafts and bushings.
– Advantages: High precision for round parts, capable of both turning and milling operations.
5. Multi-Tasking Machining Centers
– Structure: Combines milling, turning, and sometimes other processes in one machine.
– Application: Complex parts that require multiple types of machining.
– Advantages: Reduces the need for multiple setups, increases throughput, and enhances precision.
6. Bridge and Gantry Type Machining Centers
– Structure: The workpiece remains stationary while the cutting tool moves on a bridge or gantry structure.
– Application: Large workpieces such as those in aerospace or shipbuilding.
– Advantages: Handles very large parts, high rigidity and stability.
Each type of CNC machine center offers unique advantages tailored to specific manufacturing needs, from detailed small parts to large, complex components.
Pros and Cons of Using cnc machine centers
Sure! Here’s a concise overview of the pros and cons of using CNC machine centers:
Pros:
1. Precision and Accuracy: CNC machines offer high precision and repeatability, ensuring consistent quality across production batches.
2. Efficiency: Automated processes reduce production time and increase efficiency. CNC machines can operate continuously with minimal supervision.
3. Complex Capabilities: Capable of producing complex shapes and designs that would be difficult or impossible with manual machining.
4. Consistency: Eliminates human error, providing consistent output that meets exact specifications.
5. Flexibility: Easy to reprogram for different tasks, making them suitable for a variety of applications and industries.
6. Reduced Labor Costs: Automation reduces the need for skilled labor, leading to lower labor costs.
7. Safety: CNC machines enhance workplace safety by reducing the need for manual interaction with cutting tools.
8. Scalability: Suitable for both small-scale and large-scale production runs, providing flexibility in manufacturing.
Cons:
1. High Initial Investment: The cost of purchasing CNC machines and the required software can be substantial.
2. Maintenance and Repairs: Requires regular maintenance and can incur significant repair costs. Downtime during repairs can disrupt production.
3. Skilled Operators Needed: While less manual labor is required, skilled operators are still needed to program and maintain CNC machines.
4. Training Costs: Training employees to operate CNC machines can be time-consuming and costly.
5. Complex Setup: Initial setup for specific tasks can be complex and time-consuming.
6. Energy Consumption: CNC machines can consume significant amounts of power, leading to higher operational costs.
7. Dependence on Technology: Heavy reliance on software and technology can be a drawback if there are technical issues or failures.
8. Limited by Programming: The machine is only as good as its programming. Errors in the code can lead to production issues.
Using CNC machine centers offers significant advantages in terms of precision, efficiency, and versatility, but also comes with challenges such as high initial costs, maintenance requirements, and the need for skilled operators.
cnc machine centers Reference Specifications (varies for different product)
CNC (Computer Numerical Control) machine centers are versatile and precise tools used in manufacturing for various applications, including milling, drilling, and cutting. Specifications can vary widely depending on the intended use, but here are some common reference specifications for CNC machine centers:
Axis Configuration
– 3-Axis: Basic configuration with X, Y, and Z axes.
– 4-Axis: Adds a rotational axis (usually A or B).
– 5-Axis: Adds two rotational axes, allowing more complex geometries.
Work Area (XYZ Travel)
– Small Machine: X: 300-600 mm, Y: 200-400 mm, Z: 200-300 mm
– Medium Machine: X: 600-1000 mm, Y: 400-800 mm, Z: 300-600 mm
– Large Machine: X: 1000-2000 mm, Y: 800-1200 mm, Z: 600-1000 mm
Spindle
– Speed: 6,000 – 40,000 RPM
– Power: 5 – 40 kW
– Taper: ISO, BT, HSK, and others.
Feed Rates
– Rapid Traverse: 20-50 m/min
– Cutting Feed Rate: 1-10 m/min
Precision and Accuracy
– Positioning Accuracy: ±0.005 mm
– Repeatability: ±0.003 mm
Tool Capacity
– Tool Magazine: 20-60 tools
– Tool Change Time: 1-5 seconds
Control System
– Common Brands: Fanuc, Siemens, Heidenhain
– Features: User-friendly interface, advanced simulation, remote diagnostics.
Additional Features
– Coolant System: High-pressure through-spindle coolant.
– Chip Management: Conveyor systems for chip removal.
– Probing Systems: Automated tool and workpiece measurement.
Applications
– Automotive: Engine components, transmission parts.
– Aerospace: Turbine blades, structural components.
– Medical: Surgical instruments, implants.
– Consumer Electronics: Housings, connectors.
These specifications provide a general overview, but actual CNC machine centers can have varied configurations based on specific industry needs and technological advancements.
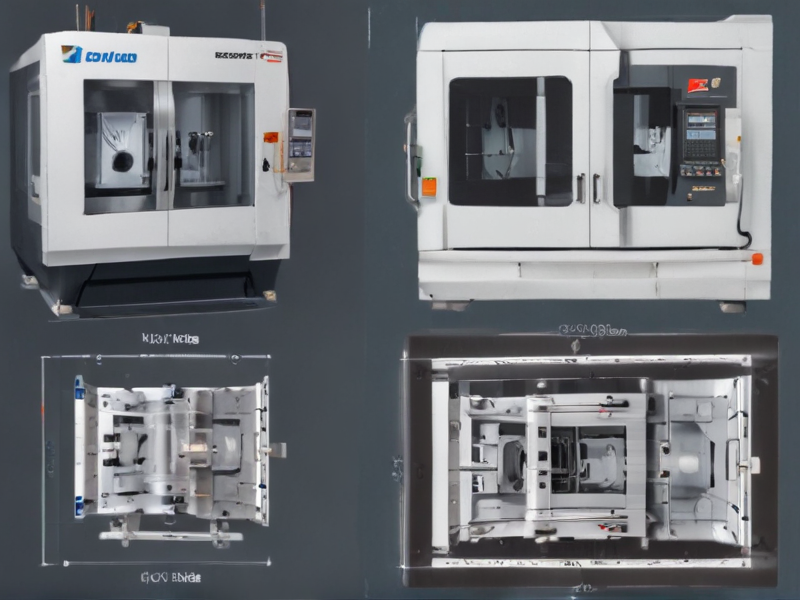
Applications of cnc machine centers
CNC (Computer Numerical Control) machine centers are highly versatile and play a crucial role in various industries due to their precision, efficiency, and automation capabilities. Here are some of the key applications:
1. Aerospace Industry
CNC machines are used to produce complex and high-precision components like turbine blades, engine parts, and airframe components. Their ability to work with hard materials and maintain tight tolerances is essential in this industry.
2. Automotive Industry
In the automotive sector, CNC machines manufacture engine blocks, transmission cases, and other critical parts. They ensure consistency and high production rates, which are vital for mass production.
3. Medical Industry
Medical devices and implants, such as prosthetics, orthopedic implants, and surgical instruments, require the high precision and reliability that CNC machines offer. The ability to work with biocompatible materials is also a significant advantage.
4. Electronics Industry
CNC machines produce components for electronic devices, including heat sinks, enclosures, and connectors. The precision and small-scale capabilities are particularly useful for creating detailed parts for smartphones, computers, and other gadgets.
5. Defense Industry
The defense sector utilizes CNC machining for manufacturing weapons, ammunition, and vehicle components. The machines’ ability to work with advanced materials like titanium and composites is crucial for producing durable and reliable equipment.
6. Tool and Die Making
CNC machining is integral in creating molds, dies, and jigs used in other manufacturing processes. These tools require extreme precision and durability, which CNC machines can provide.
7. Prototyping and R&D
CNC machines are invaluable in the prototyping stage of product development. They allow for rapid and accurate production of prototypes, enabling engineers to test and refine designs efficiently.
8. Custom Manufacturing
For custom or low-volume manufacturing, CNC machines offer the flexibility to produce bespoke parts tailored to specific needs without the high costs associated with traditional manufacturing methods.
In summary, CNC machine centers are indispensable in modern manufacturing, offering unmatched precision, efficiency, and versatility across a wide range of industries. Their applications span from producing everyday components to creating highly specialized and critical parts.
Material of cnc machine centers
CNC (Computer Numerical Control) machine centers are crafted from various materials, each chosen for its specific properties to enhance performance, durability, and precision. Here are the key materials commonly used:
1. Cast Iron
– Properties: High damping capacity, excellent vibration absorption, good wear resistance.
– Uses: Used for the machine bed and base, providing a stable and rigid structure.
2. Steel
– Properties: High strength, toughness, and fatigue resistance.
– Uses: Utilized for critical components such as spindles and gears due to its ability to withstand high stress and loads.
3. Aluminum
– Properties: Lightweight, good thermal conductivity, corrosion-resistant.
– Uses: Often used in the construction of smaller parts and components where weight reduction is essential, and in some structural parts of the CNC machines.
4. Polymer Concrete
– Properties: Excellent vibration damping, thermal stability, and chemical resistance.
– Uses: Employed in some advanced machine tool bases and structures to enhance precision by minimizing thermal expansion and vibrations.
5. Ceramics
– Properties: High hardness, wear resistance, and thermal stability.
– Uses: Applied in tooling components such as cutting inserts and some specialized wear-resistant parts.
6. Composite Materials
– Properties: Customized properties, combining strength, rigidity, and light weight.
– Uses: Utilized in specialized applications requiring tailored performance characteristics.
7. Titanium
– Properties: High strength-to-weight ratio, corrosion-resistant.
– Uses: Limited to high-performance applications where weight and strength are critical factors, often in aerospace CNC machines.
Each of these materials contributes to the overall performance and efficiency of CNC machine centers, ensuring they can meet the rigorous demands of modern manufacturing.
Quality Testing Methods for cnc machine centers and how to control the quality
Quality testing and control for CNC machine centers are critical to ensure precision, reliability, and efficiency. Here’s a concise overview of the main methods and strategies:
Quality Testing Methods
1. Dimensional Accuracy Testing:
– Coordinate Measuring Machines (CMM): Used to measure the physical geometrical characteristics of an object.
– Laser Interferometry: Measures linear positioning accuracy and repeatability.
– Ball Bar Testing: Checks circular accuracy to detect issues like backlash and servo mismatch.
2. Surface Finish Testing:
– Surface Roughness Testers: Quantify the surface texture.
– Optical Profilometers: Provide non-contact surface measurements.
3. Performance Testing:
– Spindle Analysis: Evaluates spindle speed, temperature, and vibration to ensure it operates within specified parameters.
– Thermal Stability Testing: Assesses how thermal changes affect machine precision.
4. Dynamic Testing:
– Vibration Analysis: Detects imbalance or misalignment issues.
– Servo Tuning: Ensures the servo motors are correctly configured for optimal performance.
Quality Control Strategies
1. Routine Maintenance and Calibration:
– Regular maintenance schedules and periodic calibration of machines to maintain accuracy and performance.
2. Standard Operating Procedures (SOPs):
– Developing and adhering to SOPs for machine operation, setup, and maintenance.
3. Training and Certification:
– Continuous training programs for operators to ensure they are skilled in using and maintaining CNC machines.
4. Statistical Process Control (SPC):
– Implementing SPC to monitor and control the machining process through real-time data analysis.
5. Automated Monitoring Systems:
– Using sensors and IoT technologies to monitor machine conditions and performance continuously.
6. Quality Audits:
– Regular internal and external audits to ensure compliance with industry standards and regulations.
By integrating these testing methods and control strategies, CNC machine centers can achieve high precision, reduce downtime, and maintain consistent product quality.
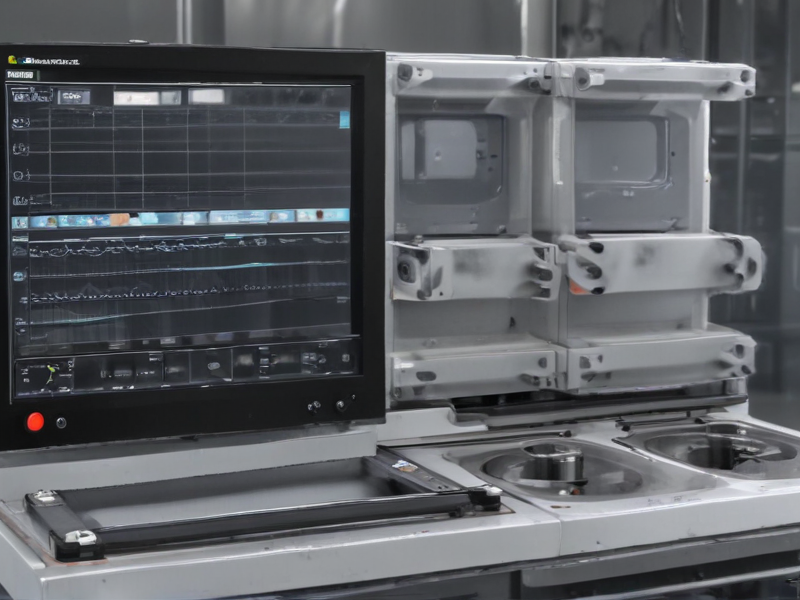
The Work Process and how to use cnc machine centers
Work Process and Usage of CNC Machine Centers
1. Planning and Design:
– CAD Software: Design the part using CAD (Computer-Aided Design) software. The design should include all necessary dimensions and tolerances.
– CAM Software: Use CAM (Computer-Aided Manufacturing) software to convert the CAD design into a CNC-compatible file (G-code).
2. Setup:
– Material Preparation: Select and prepare the raw material that will be machined.
– Tool Selection: Choose the appropriate cutting tools based on the material and the design.
– Machine Setup: Install the workpiece and tools in the CNC machine. Ensure everything is securely fastened.
3. Programming:
– Load G-Code: Transfer the G-code file to the CNC machine.
– Machine Parameters: Set machine parameters such as spindle speed, feed rate, and cutting path.
4. Machining:
– Dry Run: Perform a dry run without cutting to ensure the program runs correctly.
– Start Machining: Begin the machining process. The CNC machine will follow the G-code instructions to cut, drill, or mill the material.
– Monitoring: Continuously monitor the machine to ensure it is operating correctly and make adjustments if necessary.
5. Inspection and Finishing:
– Quality Check: Inspect the finished part for accuracy and quality. Use measuring tools like calipers and micrometers.
– Finishing Touches: Perform any necessary finishing operations, such as deburring, sanding, or polishing.
Using CNC Machine Centers:
– Safety First: Always wear appropriate safety gear, including goggles and gloves.
– Machine Calibration: Regularly calibrate the machine to maintain precision.
– Tool Maintenance: Keep cutting tools sharp and replace them as needed to ensure optimal performance.
– Cleanliness: Maintain a clean work environment to prevent contamination and ensure accurate machining.
Conclusion:
CNC machine centers are powerful tools for precision manufacturing. By following a systematic process from design to finishing, you can efficiently produce high-quality parts. Always prioritize safety and machine maintenance to achieve the best results.
cnc machine centers Importing questions including Cost,Supplier,Sample,Certification and Market
Importing CNC Machine Centers: Key Considerations
1. Cost: The price of CNC machine centers varies widely based on size, features, and manufacturer. Basic models may start around $50,000, while high-end, fully-featured centers can exceed $500,000. Consider additional costs such as shipping, customs duties, and installation.
2. Supplier: Choose reputable suppliers with positive reviews and proven track records. Major suppliers include Haas, DMG Mori, Mazak, and Okuma. Investigate potential suppliers’ reliability, after-sales service, and parts availability.
3. Sample: Requesting a sample can be challenging for large machinery. Instead, ask for detailed videos, specifications, and performance reports. If possible, arrange for a visit to the supplier’s facility or a local demo to evaluate the machine’s performance firsthand.
4. Certification: Ensure the machines meet necessary certifications and standards such as ISO 9001 for quality management and CE marking for compliance with European safety standards. Verify the supplier’s compliance with relevant industrial and safety certifications to ensure the machine’s reliability and safety.
5. Market: Understand the market demand for CNC machined parts in your region. Research industry trends and potential customers’ needs. Strong demand sectors include automotive, aerospace, medical devices, and consumer electronics. Ensure the machine’s capabilities align with your target market’s requirements.
Summary: When importing CNC machine centers, carefully evaluate costs, choose reliable suppliers, verify certifications, and understand market needs. Thorough research and due diligence are essential to ensure a successful investment.
How to find and select check reliable cnc machine centers manufacturers in China
Finding and selecting reliable CNC machine centers manufacturers in China requires a systematic approach. Here are the steps:
1. Research and Shortlisting
– Online Directories: Use platforms like Alibaba, Made-in-China, and Global Sources to find manufacturers. Filter by “Verified Supplier” or “Gold Supplier” status.
– Industry Associations: Check listings from associations like the China Machine Tool & Tool Builders’ Association (CMTBA).
– Trade Shows: Attend events like the China CNC Machine Tool Fair (CCMT) to meet manufacturers in person.
2. Verification
– Company Background: Verify the company’s registration, business license, and certifications (e.g., ISO 9001) through the National Enterprise Credit Information Publicity System.
– Factory Visits: If possible, visit the manufacturing facilities to inspect their operations, machinery, and quality control processes.
3. Quality and Compliance
– Product Quality: Request samples or a tour of their production line to check the quality of their CNC machines.
– Certifications: Ensure they comply with international standards like CE, RoHS, or any specific industry requirements.
4. Reputation and Reviews
– Customer Feedback: Look for reviews and testimonials from other customers. Platforms like Alibaba often have reviews and ratings.
– Third-Party Audits: Consider services from third-party inspection companies like SGS or TÜV to audit the manufacturer.
5. Communication and Support
– Responsiveness: Evaluate their communication efficiency and technical support capabilities. Reliable manufacturers should have a responsive sales and technical team.
– After-Sales Service: Check the warranty terms, availability of spare parts, and after-sales support.
6. Pricing and Terms
– Competitive Pricing: Compare quotes from different manufacturers but be wary of prices significantly lower than the market average, which might indicate inferior quality.
– Payment Terms: Negotiate favorable payment terms. Be cautious with upfront payments and consider using secure payment methods or trade assurance services.
Conclusion
By meticulously following these steps, you can identify and select reliable CNC machine centers manufacturers in China, ensuring quality and reliability for your production needs.
Background Research for cnc machine centers manufacturers Companies in China, use qcc.com archive.org importyeti.com
> search(“cnc machine centers manufacturers site:qcc.com”)
> mclick([0, 1, 3, 4, 5, 6])
> end-searching
Here are some prominent CNC machine center manufacturers in China based on information from qcc.com:
1. Nanjing High Accurate Drive Equipment Manufacturing Group Co., Ltd.: Established in 2007, this company specializes in high-precision transmission equipment and machinery. It operates in Jiangsu Province and employs around 346 people. They focus on manufacturing and industrial equipment, catering to both domestic and international markets.
2. Kunshan Kesun Technology Co., Ltd.: Founded in 2010 and based in Jiangsu Province, this company is part of Kesun Technology. They employ between 2000-2999 people and are engaged in manufacturing various technological products, including CNC machinery.
3. Baide Precision Manufacturing Co., Ltd.: Located in Suzhou Industrial Park and established in 2006, Baide specializes in precision manufacturing. They have a workforce of 1000-1999 employees and focus on producing high-quality CNC machinery and related products.
4. Guangzhou Slinde Technology Co., Ltd.: This company, founded in 2005, is based in Guangzhou and specializes in instrument and meter manufacturing. They have around 329 employees and a substantial annual revenue, reflecting their strong presence in the industry.
5. Shanghai Bochu Electronic Technology Co., Ltd.: Operating since 2007, this company is located in Shanghai and focuses on electronic and technological services, including CNC machine manufacturing. They have a smaller team of 100-199 employees but are noted for their innovative approach in the industry.
6. Wuhan Feijin Intelligent Machine Co., Ltd.: Established in 2014 in Wuhan, this company specializes in intelligent machinery and has a workforce of 200-299 employees. They are known for their advanced manufacturing techniques and significant contributions to the CNC machinery sector.
These companies are key players in the CNC machine manufacturing industry in China, each contributing to the market with their specialized products and technological advancements.
For further details, you can refer to their profiles on qcc.com: [Nanjing High Accurate](https://www.qcc.com/firm/c9ca27455e62fd551708ea779b64430c.html), [Kunshan Kesun](https://www.qcc.com/firm/fe90d8891a4897a0b8e303f52fffaf33.html), [Baide Precision](https://www.qcc.com/firm/9eb3d0ae367f37170f3c59bb046164d0.html), [Guangzhou Slinde](https://www.qcc.com/firm/bb4be69048777c69ee53eba4212efbe3.html), [Shanghai Bochu](https://www.qcc.com/firm/eecf26f6dac9efec093a0f98a7f246f1.html), [Wuhan Feijin](https://www.qcc.com/firm/20f57becf78abd27f01998b34f72ce13.html).
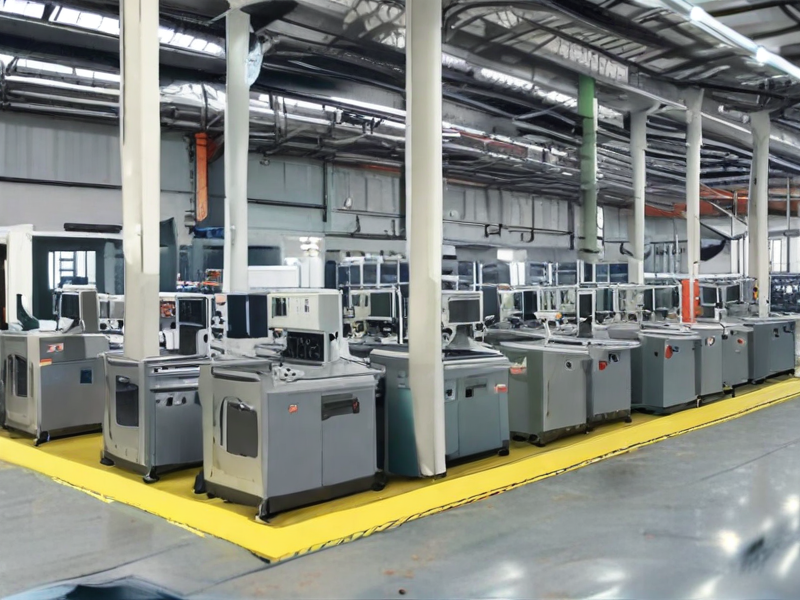
Price Cost Research for cnc machine centers manufacturers Companies in China, use temu.com and 1688.com
To research CNC machine centers manufacturers in China using Temu.com and 1688.com:
Temu.com is a comprehensive B2B platform known for its extensive supplier database. It allows users to search for specific products like CNC machine centers and provides detailed supplier profiles with product specifications, certifications, and contact information. Users can filter results based on location, company size, and product type, making it easier to find suitable manufacturers.
1688.com, operated by Alibaba Group, is China’s largest wholesale marketplace. It offers a vast array of CNC machine center manufacturers ranging from large-scale factories to smaller workshops. The platform provides product listings with prices, minimum order quantities (MOQs), and often includes customer reviews and ratings. It’s advantageous for sourcing directly from manufacturers, potentially offering competitive pricing due to its wholesale nature.
When using these platforms for research:
– Temu.com is beneficial for detailed supplier information and filtering options, useful for finding specialized manufacturers.
– 1688.com offers a broader range of manufacturers with competitive pricing and often provides insights into market trends and product availability.
For efficient sourcing, it’s recommended to compare quotes, verify supplier credentials, and consider factors like production capacity and quality certifications. These steps ensure a reliable partnership with CNC machine center manufacturers in China.
Shipping Cost for cnc machine centers import from China
Importing CNC machine centers from China involves several shipping cost components. Here’s a breakdown of the main factors:
1. Shipping Method
– Sea Freight: Typically the most cost-effective for heavy machinery. Costs vary based on the container size and the destination port. A 20-foot container might cost between $1,000 and $2,500, while a 40-foot container can range from $1,500 to $4,000.
– Air Freight: Much faster but significantly more expensive, generally used for urgent or smaller shipments. Costs can be $5 to $10 per kilogram.
2. Port Charges
– Charges at both the origin and destination ports, including handling, documentation, and customs fees. These can add $500 to $1,500 to the total cost.
3. Customs Duties and Taxes
– Import Duties: Varies by country; typically a percentage of the machine’s value (e.g., 1-5%).
– VAT/GST: Some countries levy additional value-added tax or goods and services tax, which could be 10-20% of the total value.
4. Insurance
– It’s advisable to insure high-value shipments. Insurance costs are usually 0.5% to 2% of the shipment value.
5. Inland Transportation
– From Factory to Port: Costs in China, typically $200 to $500 depending on the distance.
– From Port to Destination: Costs in the destination country, which could range from $300 to $1,000 or more based on distance and transportation mode.
6. Packaging
– Special packaging for machinery to prevent damage during transit. Costs can range from $200 to $800 depending on the size and protection level required.
Total Estimated Cost
Combining all factors, shipping a CNC machine center could range from $3,000 to $10,000, depending on the specifics mentioned. Always get detailed quotes from multiple freight forwarders to ensure competitive pricing.
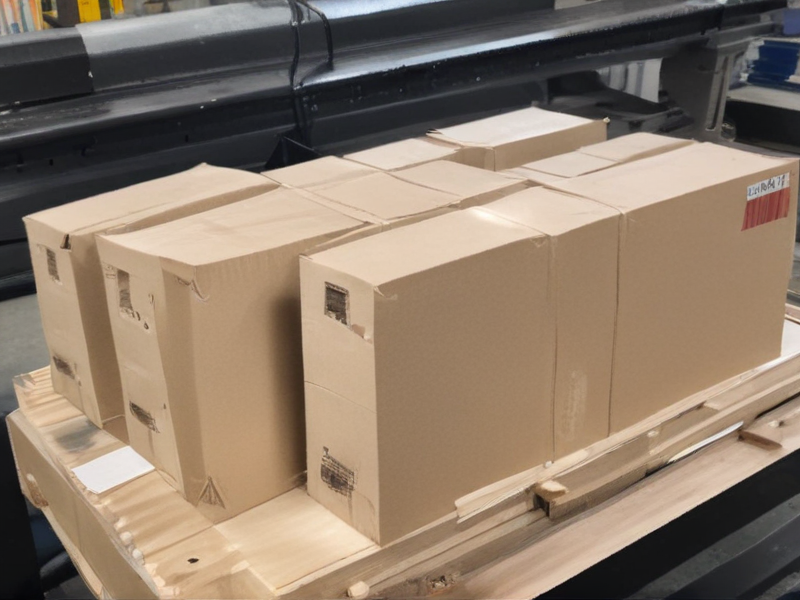
Compare China and Other cnc machine centers Markets: Products Quality and Price,Visible and Hidden Costs
Comparing China and Other CNC Machine Centers Markets
Products Quality and Price
1. China:
– Quality: Generally improving with high-end machines reaching global standards. However, variability exists; some products may lack consistency.
– Price: Competitive pricing, often significantly lower than Western counterparts due to lower labor and production costs.
2. Other Markets (e.g., Germany, Japan, USA):
– Quality: Known for superior precision, durability, and reliability. Brands like DMG MORI (Germany) and Mazak (Japan) are industry benchmarks.
– Price: Higher due to advanced technology, superior materials, and stringent quality control.
Visible and Hidden Costs
1. China:
– Visible Costs: Lower initial purchase price.
– Hidden Costs: Potential for higher maintenance and repair costs due to variable quality. Possible longer lead times and higher shipping costs. Import tariffs and duties can also add to the cost.
2. Other Markets:
– Visible Costs: Higher upfront cost for purchase.
– Hidden Costs: Generally lower due to better reliability and fewer repairs. Local support and service can reduce downtime. Spare parts are more readily available, and shipping costs are usually lower.
Conclusion
Choosing between CNC machines from China and other markets involves balancing upfront costs with long-term reliability and maintenance. Chinese machines offer cost savings but may come with hidden costs related to quality and service. Machines from established markets, while pricier, typically provide higher quality, reliability, and lower long-term operational costs.
Custom Private Labeling and Branding Opportunities with Chinese cnc machine centers Manufacturers
Exploring custom private labeling and branding opportunities with Chinese CNC machine center manufacturers can offer significant advantages for businesses looking to enhance their product offerings. Here’s a detailed look at how to leverage these opportunities:
1. Why Choose Chinese CNC Manufacturers?
Chinese CNC manufacturers are known for their competitive pricing, advanced technology, and high-quality production capabilities. By partnering with these manufacturers, you can access state-of-the-art machinery without the high costs typically associated with Western brands.
2. Customization Options
Chinese manufacturers often offer extensive customization options. You can tailor the machinery to meet specific requirements, such as:
– Branding: Add your company’s logo and branding elements to create a unique identity.
– Specifications: Modify technical specifications to suit your production needs.
– Aesthetics: Customize the machine’s color, design, and interface to align with your brand image.
3. Private Labeling Benefits
Private labeling with Chinese CNC manufacturers allows you to:
– Reduce Costs: Lower manufacturing and production costs compared to in-house development.
– Speed to Market: Accelerate the time it takes to bring new products to market.
– Focus on Core Competencies: Concentrate on marketing, sales, and distribution while the manufacturing is handled by experts.
4. Finding the Right Partner
To maximize these opportunities, it’s crucial to find the right manufacturing partner. Consider the following:
– Reputation: Research the manufacturer’s reputation and customer feedback.
– Quality Assurance: Ensure they have robust quality control processes.
– Communication: Establish clear communication channels to avoid misunderstandings.
5. Negotiation and Contracts
Negotiate favorable terms, focusing on aspects such as:
– Minimum Order Quantities (MOQs): Understand their MOQs and negotiate terms that suit your business size.
– Lead Times: Agree on realistic lead times that match your production schedules.
– After-Sales Support: Ensure they offer comprehensive after-sales support and warranty terms.
Conclusion
Partnering with Chinese CNC machine center manufacturers for custom private labeling and branding can be a game-changer. By focusing on customization, finding the right partner, and negotiating effectively, you can enhance your product line, reduce costs, and increase market competitiveness.
Tips for Procurement and Considerations when Purchasing cnc machine centers
When purchasing CNC machine centers, it’s crucial to consider several factors to ensure you make an informed decision. Here are some key tips and considerations:
1. Assess Your Needs: Determine the types of materials you will be working with and the complexity of the parts you need to produce. This will help you decide on the machine’s required features, such as spindle speed, axis configuration, and table size.
2. Budget and Costs: Set a clear budget, but also consider the total cost of ownership, including maintenance, tooling, and potential downtime costs. Don’t just focus on the upfront price.
3. Machine Capabilities: Evaluate the machine’s precision, repeatability, and overall performance. Check for features like tool changers, coolant systems, and software compatibility.
4. Manufacturer and Support: Choose a reputable manufacturer known for quality and reliability. Consider the availability of after-sales support, training, and the ease of obtaining spare parts.
5. Technology and Software: Ensure the CNC machine center is equipped with the latest technology and is compatible with your existing software systems. Advanced control systems can enhance productivity and precision.
6. Space and Infrastructure: Make sure you have adequate space and the necessary infrastructure, such as power supply and ventilation, to accommodate the new machine.
7. Future-Proofing: Consider future needs and potential expansion. Investing in a machine with capabilities slightly beyond your current requirements can save money in the long run.
8. Operational Efficiency: Look for features that improve operational efficiency, such as automation capabilities, user-friendly interfaces, and energy-saving functions.
9. Training and Safety: Ensure that your team is adequately trained to operate the machine safely and efficiently. Look into the manufacturer’s training programs and safety features of the machine.
10. Resale Value: Consider the machine’s potential resale value. Machines from reputable brands often retain their value better.
By carefully evaluating these factors, you can make a well-informed decision when purchasing a CNC machine center, ensuring it meets your current and future production needs.
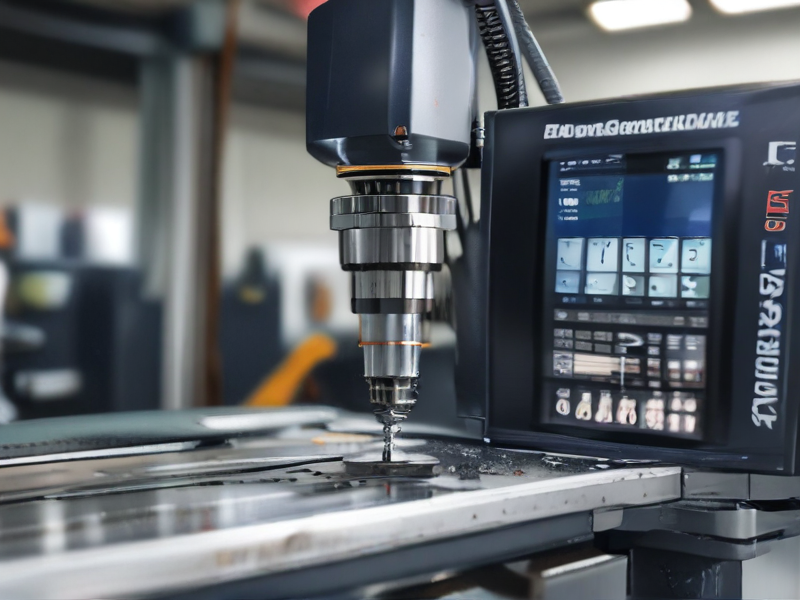
FAQs on Sourcing and Manufacturing cnc machine centers in China
FAQs on Sourcing and Manufacturing CNC Machine Centers in China
1. Why source CNC machine centers from China?
China offers competitive pricing, a wide variety of options, and advanced technology. Many Chinese manufacturers have ISO certifications and export globally, ensuring quality and reliability.
2. How to identify reputable CNC machine manufacturers?
Look for manufacturers with ISO certifications, positive customer reviews, and a strong export history. Websites like Alibaba, Made-in-China, and Global Sources provide verified suppliers.
3. What are the key factors to consider when choosing a manufacturer?
Consider the manufacturer’s experience, the quality of machines, after-sales service, and customization options. Visiting the factory or requesting a virtual tour can provide additional assurance.
4. What is the typical lead time for CNC machine centers?
Lead times can vary from 30 to 90 days depending on the complexity of the machine and the manufacturer’s production schedule. Custom orders may take longer.
5. How to ensure the quality of CNC machines?
Request detailed specifications, certifications, and sample tests. Third-party inspections and factory audits are also advisable. Ensure the manufacturer offers warranties and robust after-sales support.
6. What are the payment terms commonly accepted?
Common payment terms include a 30% deposit upfront and the remaining 70% before shipment. Letters of credit (LC) and trade assurance services through platforms like Alibaba are also used.
7. Are there any import regulations to be aware of?
Yes, import regulations vary by country. Ensure compliance with local regulations, including necessary certifications, tariffs, and import duties. Consulting a customs broker can be helpful.
8. Can manufacturers provide customization?
Many manufacturers offer customization to meet specific needs. This can include modifications to design, size, and functionality. Clear communication of requirements is essential.
9. What about shipping and logistics?
Manufacturers typically handle logistics through established freight forwarders. It’s crucial to discuss shipping options, costs, and timelines. Insurance for high-value shipments is recommended.
10. How important is after-sales service?
After-sales service is critical. Ensure the manufacturer provides technical support, spare parts, and training. Good after-sales service can significantly impact the machine’s longevity and performance.
These FAQs should help guide you through the process of sourcing and manufacturing CNC machine centers in China, ensuring a successful and efficient experience.