Top 10 cnc laser cutter in China introduce,list main products and website if have
Here are the top 10 CNC laser cutter companies in China, along with their main products and websites:
1. Han’s Laser
– Main Products: High-power fiber laser cutting machines, laser welding machines.
– Website: [hanslaser.net](http://www.hanslaser.net/)
2. Bodor Laser
– Main Products: Fiber laser cutting machines, metal cutting machines.
– Website: [bodor.com](http://www.bodor.com/)
3. HSG Laser
– Main Products: Laser cutting machines, laser welding machines, intelligent laser equipment.
– Website: [hsglaser.com](http://www.hsglaser.com/)
4. Penta Laser
– Main Products: High-power laser cutting equipment, laser welding equipment.
– Website: [pentalaser.com](http://www.pentalaser.com/)
5. Hymson Laser
– Main Products: Laser cutting machines, automation equipment for lithium batteries, and sheet metal industries.
– Website: [hymson.com](http://www.hymson.com/)
6. G.Weike
– Main Products: Laser cutting machines, laser engravers.
– Website: [wklaser.com](http://www.wklaser.com/)
7. Bystronic DNE
– Main Products: High-power and medium-power fiber laser cutting machines.
– Website: [dne.bz](http://www.dne.bz/)
8. Golden Laser
– Main Products: Laser cutting machines, laser welding machines, laser cleaning equipment.
– Website: [goldenlaser.cc](http://www.goldenlaser.cc/)
9. Shandong Leiming Laser
– Main Products: Fiber laser cutting machines, laser welding, and cleaning equipment.
– Website: [lmcnclaser.com](http://www.lmcnclaser.com/)
10. Yawei Laser
– Main Products: CNC turret punches, CNC bending machines, laser cutting machines.
– Website: [yawei.cc](http://www.yawei.cc/)
These companies are known for their advanced technology, extensive product ranges, and strong market presence both in China and internationally.
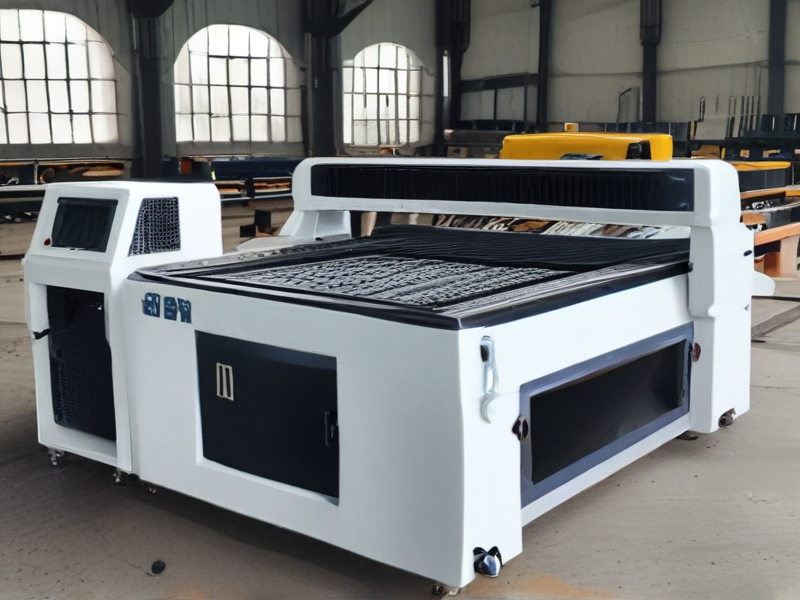
Types of cnc laser cutter
CNC laser cutters are classified based on their laser source and application capabilities. Here are the main types:
1. CO2 Laser Cutters:
– Laser Source: Carbon dioxide gas mixture.
– Applications: Suitable for non-metal materials like wood, acrylic, plastic, leather, and fabrics.
– Advantages: High cutting speed, smooth edges, cost-effective for non-metallic applications.
2. Fiber Laser Cutters:
– Laser Source: Fiber optics with rare-earth elements.
– Applications: Ideal for metals including steel, aluminum, brass, and copper.
– Advantages: High precision, energy-efficient, minimal maintenance, faster cutting speed for thin metals.
3. Nd:YAG (Neodymium-Doped Yttrium Aluminum Garnet) Laser Cutters:
– Laser Source: Solid-state crystal (Nd:YAG).
– Applications: Both metallic and non-metallic materials, used for cutting, engraving, and welding.
– Advantages: High power, suitable for deep engraving and drilling, used in medical and automotive industries.
4. Diode Laser Cutters:
– Laser Source: Semiconductor diodes.
– Applications: Typically used for engraving and marking on metals and non-metals.
– Advantages: Compact size, low cost, suitable for small-scale operations and DIY projects.
Each type of CNC laser cutter offers unique benefits and is chosen based on the specific needs of the material and the precision required for the project.
Pros and Cons of Using cnc laser cutter
Pros of Using CNC Laser Cutter
1. Precision and Accuracy: CNC laser cutters offer high precision and accuracy, allowing for intricate and detailed designs with minimal errors.
2. Efficiency and Speed: They can cut materials quickly and efficiently, reducing production time significantly compared to traditional methods.
3. Versatility: CNC laser cutters can work with a wide range of materials, including metals, plastics, wood, and textiles.
4. Automated Process: The automation reduces the need for manual labor, leading to consistent quality and lower labor costs.
5. Minimal Waste: High precision leads to minimal material waste, making the process more cost-effective and environmentally friendly.
6. Flexibility in Design: Easy to switch between different designs and patterns without needing physical tool changes, allowing for greater flexibility in production.
Cons of Using CNC Laser Cutter
1. High Initial Cost: The upfront cost for purchasing CNC laser cutters can be significant, which might be prohibitive for small businesses.
2. Maintenance and Operating Costs: Regular maintenance and operating costs, including electricity and replacement parts, can add up over time.
3. Safety Concerns: CNC laser cutters can pose safety risks, including burns and eye damage from the laser beam, requiring strict safety protocols and protective equipment.
4. Skill Requirement: Operators need specialized training to handle the machines effectively, which can increase the cost and time investment for training staff.
5. Material Limitations: While versatile, there are some materials that CNC laser cutters cannot process effectively, such as certain types of glass and reflective metals.
6. Environmental Impact: The cutting process can produce fumes and emissions that may require proper ventilation and filtration systems to mitigate environmental impact.
In summary, CNC laser cutters offer high precision, efficiency, and versatility, making them valuable in modern manufacturing. However, they come with high initial costs, ongoing maintenance needs, and safety considerations that must be managed effectively.
cnc laser cutter Reference Specifications (varies for different product)
CNC Laser Cutter Reference Specifications
#### Laser Type
– Fiber Laser: Suitable for metals, providing high precision and efficiency.
– CO2 Laser: Ideal for non-metals like wood, acrylic, glass, and some metals.
– Diode Laser: Used for engraving and cutting softer materials like wood and plastic.
#### Power Output
– Low Power (20-50W): Suitable for thin materials and detailed engraving.
– Medium Power (50-150W): Versatile, handling a range of materials and thicknesses.
– High Power (150W and above): Designed for cutting thick metals and heavy-duty applications.
#### Cutting Area
– Small Format (300 x 200 mm): Best for detailed, small-scale work.
– Medium Format (600 x 400 mm): Suitable for mid-sized projects and more flexibility.
– Large Format (1300 x 900 mm and above): Used for industrial applications and large materials.
#### Cutting Speed
– Up to 1,000 mm/s: High-speed operation for quick cuts and increased productivity.
– Variable Speed Settings: Allows for adjustments based on material type and thickness.
#### Accuracy and Precision
– Positioning Accuracy: ±0.01 mm to ±0.03 mm.
– Repeatability: ±0.01 mm.
#### Control System
– CNC Control: Enables precise control of cutting paths and automation.
– Software Compatibility: Compatible with common design software like AutoCAD, CorelDRAW, and Illustrator.
#### Material Compatibility
– Metals: Steel, aluminum, brass, copper.
– Non-Metals: Wood, acrylic, plastics, textiles, leather, glass.
#### Cooling System
– Water Cooling: Common in high-power lasers for temperature management.
– Air Cooling: Suitable for low to medium power lasers.
#### Safety Features
– Enclosed Design: Protects users from laser exposure.
– Emergency Stop: Quickly halts operations in case of an issue.
– Laser Protective Glasses: Recommended for open design systems.
#### Additional Features
– Auto-Focus: Adjusts the focal length automatically for optimal cutting.
– Rotary Attachment: Allows for engraving cylindrical objects.
– Fume Extraction: Essential for removing harmful fumes generated during cutting.
These specifications provide a comprehensive overview, allowing for the selection of a CNC laser cutter tailored to specific needs and applications.
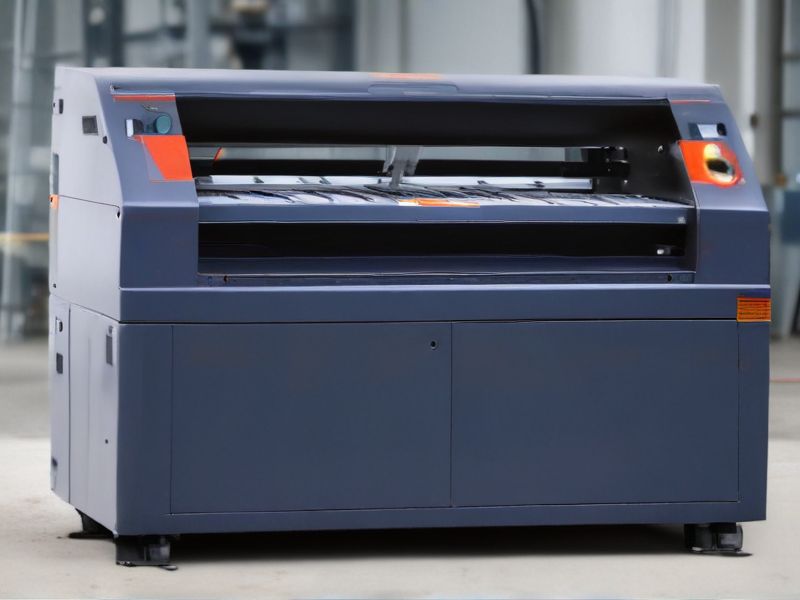
Applications of cnc laser cutter
A CNC (Computer Numerical Control) laser cutter is a versatile tool used in various industries due to its precision and efficiency. Here are some key applications:
1. Manufacturing and Prototyping: CNC laser cutters are widely used to produce precise parts and components. They can cut through metals, plastics, and composites, enabling the creation of intricate designs and rapid prototyping.
2. Automotive Industry: These cutters are essential for manufacturing components such as gears, engine parts, and intricate interior details. The precision ensures high-quality parts with minimal waste.
3. Aerospace Industry: The aerospace sector relies on CNC laser cutting for the fabrication of complex components from lightweight materials, ensuring strength and precision critical for safety and performance.
4. Medical Device Manufacturing: CNC laser cutters produce precise and clean cuts needed for medical devices, surgical instruments, and implants. The accuracy is crucial for maintaining the integrity and safety of these products.
5. Jewelry and Fashion: In jewelry making, laser cutters enable the creation of intricate patterns and designs on metals and gemstones. In fashion, they cut fabrics and leather with precision, allowing for innovative designs and patterns.
6. Architecture and Construction: Laser cutters create detailed models and prototypes of architectural designs. They are also used for cutting materials like metal and glass for decorative elements in buildings.
7. Signage and Advertising: Laser cutting is used to produce signs, displays, and other advertising materials. The ability to cut detailed shapes and letters enhances the visual appeal of these products.
8. Arts and Crafts: Artists and hobbyists use CNC laser cutters for engraving and cutting materials like wood, acrylic, and paper, allowing for detailed artwork and personalized projects.
9. Electronics: In the electronics industry, laser cutters are used to manufacture circuit boards, enclosures, and components, providing the precision needed for small and complex parts.
These applications highlight the CNC laser cutter’s role in enhancing efficiency, precision, and innovation across diverse fields.
Material of cnc laser cutter
CNC laser cutters are versatile tools used in various industries for cutting, engraving, and marking materials with high precision. The materials commonly used with CNC laser cutters include:
1. Metals:
– Steel: Both carbon steel and stainless steel are frequently used due to their durability and strength.
– Aluminum: Popular for its lightweight and resistance to corrosion, making it suitable for aerospace and automotive applications.
– Brass and Copper: Utilized for their excellent thermal and electrical conductivity, often in electronics and decorative items.
2. Plastics:
– Acrylic (Plexiglas): Common for signage, displays, and artistic applications because of its clarity and ease of cutting.
– Polycarbonate: Known for its toughness and impact resistance, used in safety equipment and industrial applications.
– Polyethylene and Polypropylene: Used in packaging, containers, and mechanical parts due to their versatility and durability.
3. Wood:
– Plywood: Frequently used for its layered structure which offers strength and stability.
– MDF (Medium-Density Fiberboard): Popular in furniture making and cabinetry because of its smooth surface and uniform density.
– Hardwood and Softwood: Used for fine furniture, decorative items, and engraving purposes.
4. Composites:
– Carbon Fiber and Fiberglass: Used in high-performance applications such as automotive, aerospace, and sports equipment due to their strength-to-weight ratio.
– Laminate Composites: Used in various industries for their combined properties of strength, lightweight, and resistance to wear.
5. Others:
– Leather and Textiles: Utilized in fashion, accessories, and upholstery due to their flexibility and aesthetic appeal.
– Ceramics and Glass: While more challenging to cut, they are used in artistic and functional applications requiring precision engraving or etching.
These materials are chosen based on their specific properties, application requirements, and the capabilities of the CNC laser cutter.
Quality Testing Methods for cnc laser cutter and how to control the quality
Quality testing for CNC laser cutters involves several methods to ensure precision, reliability, and consistency. Here are key testing methods and quality control practices:
1. Dimensional Accuracy Testing:
– Calibration: Regularly calibrate the laser cutter using standard gauges to ensure dimensional accuracy.
– Test Cuts: Perform test cuts on materials to check for precision against design specifications. Measure the cuts with calipers or micrometers.
2. Cut Quality Inspection:
– Visual Inspection: Check for clean, smooth edges without burrs or roughness.
– Edge Burn Analysis: Inspect edges for signs of burning or melting, indicating incorrect power settings or speed.
3. Material Consistency Testing:
– Material Certification: Use certified materials and perform sample checks for consistency in thickness and composition.
– Traceability: Maintain records of material batches used for traceability and quality assurance.
4. Machine Performance Monitoring:
– Regular Maintenance: Follow a scheduled maintenance routine to keep the machine in optimal condition.
– Laser Power and Focus Checks: Regularly test the laser power output and ensure the focus is correctly set to maintain cut quality.
5. Environmental Control:
– Temperature and Humidity Monitoring: Maintain a controlled environment to prevent variations in material behavior and machine performance.
– Dust and Debris Management: Keep the work area clean to avoid contamination that can affect cutting precision.
6. Software and Programming Verification:
– Simulation: Use software simulations to verify cutting paths and detect potential issues before actual cutting.
– Program Validation: Validate CNC programs to ensure they meet design requirements and machine capabilities.
7. Feedback and Continuous Improvement:
– Operator Training: Ensure operators are well-trained and aware of best practices.
– Customer Feedback: Collect and analyze customer feedback to identify areas for improvement.
By implementing these quality testing methods and control measures, the precision and reliability of CNC laser cutting processes can be maintained, ensuring high-quality outputs consistently.
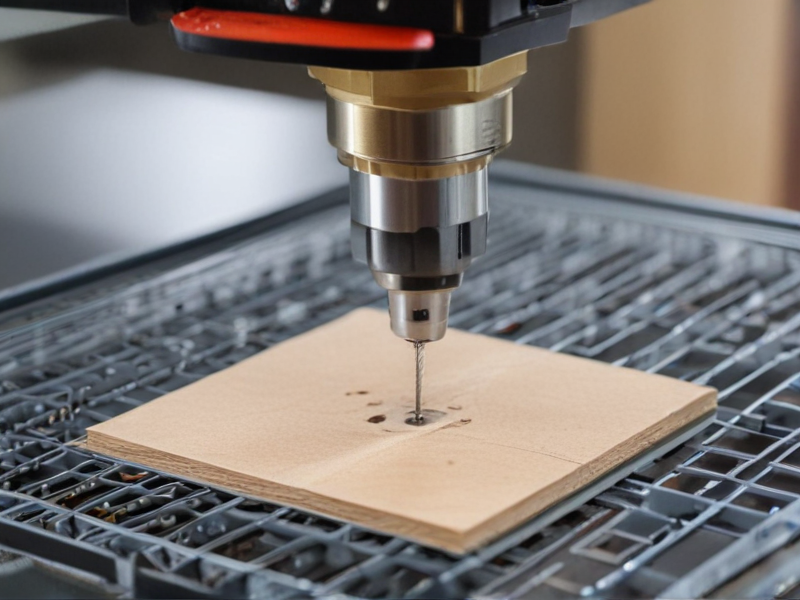
The Work Process and how to use cnc laser cutter
Using a CNC laser cutter involves a precise and structured process. Here’s a concise guide on the work process and how to use a CNC laser cutter:
Work Process:
1. Design Creation:
– Software: Use CAD software (like AutoCAD, SolidWorks) to create or import your design. Ensure the design is in vector format, typically using file types such as DXF, SVG, or AI.
– Parameters: Set design parameters, including dimensions and layers for different cuts or engravings.
2. File Preparation:
– Export: Save and export the design file in a format compatible with the CNC laser cutter’s software.
– Upload: Transfer the file to the laser cutter’s software, ensuring all settings (like scale and orientation) are correct.
3. Machine Setup:
– Material Preparation: Choose and prepare the material (e.g., wood, acrylic, metal). Secure it on the machine bed to prevent movement.
– Calibration: Calibrate the machine. This includes setting the focus of the laser, which ensures precise cutting or engraving.
4. Setting Parameters:
– Power and Speed: Adjust the laser’s power and speed settings based on the material and the desired outcome. Different materials require different settings for optimal results.
– Cutting Path: Define the cutting path and order. Ensure that inner cuts are performed before outer cuts to maintain material stability.
5. Execution:
– Start the Machine: Begin the cutting or engraving process. Monitor the machine to ensure there are no issues such as material shifting or laser misalignment.
– Safety: Always wear appropriate safety gear (e.g., safety glasses) and ensure proper ventilation to handle fumes or dust.
6. Finishing:
– Inspection: Once the process is complete, carefully remove the material and inspect the cut or engraving for accuracy and quality.
– Cleanup: Clean the machine and work area to maintain a safe and efficient workspace.
By following these steps, you can effectively use a CNC laser cutter to produce precise and intricate designs.
cnc laser cutter Importing questions including Cost,Supplier,Sample,Certification and Market
Importing CNC Laser Cutters: Key Considerations
1. Cost:
– Initial Investment: CNC laser cutters range from a few thousand to several hundred thousand dollars, depending on the model, power, and capabilities.
– Shipping and Duties: Include international shipping costs and import duties, which vary by country. Use Incoterms (e.g., FOB, CIF) to understand cost responsibilities.
2. Supplier:
– Reputation: Choose reputable suppliers with positive reviews and proven track records.
– Location: Suppliers from China, Germany, and the USA are common. Proximity can affect shipping costs and times.
– Support: Ensure suppliers offer after-sales support, including training, maintenance, and spare parts.
3. Sample:
– Quality Verification: Request samples of laser-cut products to assess the machine’s precision and performance.
– Trial Period: Some suppliers may offer a trial period or demo units to evaluate before purchase.
4. Certification:
– Compliance: Ensure the machine complies with local and international standards (e.g., CE marking for Europe, FDA for the USA).
– Documentation: Obtain all necessary certifications and safety documentation to avoid legal issues and ensure workplace safety.
5. Market:
– Demand Analysis: Research the market demand for laser-cut products in your region.
– Competition: Understand the competitive landscape and identify potential niches or unique offerings.
– Trends: Stay updated on industry trends, such as advancements in laser technology and emerging applications, to maintain a competitive edge.
By considering these factors, you can make an informed decision when importing a CNC laser cutter, ensuring it meets your operational needs and market demands.
How to find and select check reliable cnc laser cutter manufacturers in China
Finding and selecting reliable CNC laser cutter manufacturers in China involves several steps:
1. Research and Identification:
– Online Directories: Use platforms like Alibaba, Made-in-China, and Global Sources to identify potential manufacturers. Look for suppliers with high ratings and positive reviews.
– Industry Trade Shows: Attend events like the China International Machine Tool Show (CIMT) or the China Import and Export Fair (Canton Fair) to meet manufacturers directly.
2. Verification and Evaluation:
– Company Background: Check the company’s registration details, business license, and years in operation. Platforms like Alibaba provide verification services.
– Certifications and Standards: Ensure the manufacturer has relevant certifications such as ISO 9001 for quality management and CE marking for safety standards.
– Product Range and Specifications: Compare the product specifications to ensure they meet your requirements. Look for manufacturers that offer a range of products with customizable options.
3. Quality Assurance:
– Sample Testing: Request samples to test the quality and performance of the CNC laser cutters.
– Factory Visits: If possible, visit the manufacturing facilities to inspect the production process, equipment, and quality control measures.
4. Customer Feedback:
– References and Reviews: Ask for references from previous clients and read customer reviews and testimonials to gauge satisfaction levels.
– Third-Party Reviews: Look for reviews and ratings from third-party sources to get an unbiased opinion about the manufacturer.
5. Communication and Support:
– Responsiveness: Evaluate the manufacturer’s responsiveness and willingness to provide detailed information.
– Technical Support and Warranty: Ensure the manufacturer offers good after-sales support, including technical assistance and warranty services.
By following these steps, you can find and select reliable CNC laser cutter manufacturers in China, ensuring high-quality products and trustworthy partnerships.
Background Research for cnc laser cutter manufacturers Companies in China, use qcc.com archive.org importyeti.com
CNC Laser Cutter Manufacturers in China
China is home to several prominent CNC laser cutter manufacturers, each offering a range of advanced products and solutions for various industries. Here are some key players:
1. Han’s Laser Technology Industry Group Co., Ltd.: Founded in 1996, Han’s Laser is one of the largest and most well-known laser equipment manufacturers in China. The company specializes in laser cutting, welding, marking, and engraving systems, with a strong emphasis on innovation and technological advancement.
2. Wuhan Raycus Fiber Laser Technologies Co., Ltd.: This company is a leading manufacturer of fiber lasers and has a strong focus on research and development. They offer a variety of laser sources for cutting, welding, and marking applications, catering to industries such as automotive, aerospace, and electronics.
3. Shenzhen DNE Laser Science and Technology Co., Ltd.: Known for its high-speed laser cutting machines, DNE Laser provides solutions for metal processing industries. The company has made significant investments in research and development to enhance the precision and efficiency of its machines.
4. Sunda Laser Technology Co., Ltd.: Based in Suzhou, Sunda Laser specializes in the development and manufacture of high-power fiber laser cutting machines. Their products are widely used in the construction, shipbuilding, and machinery industries.
5. Guangdong Hengye Energy Technology Co., Ltd.: A newer entrant in the market, established in 2018, Hengye Energy focuses on the integration of intelligent manufacturing with laser technology. Their products include laser cutting machines designed for efficiency and precision in various industrial applications.
These companies are recognized for their robust technological capabilities, extensive product lines, and strong market presence both domestically and internationally. They contribute significantly to the advancement of laser cutting technology, meeting diverse industrial needs with their innovative solutions.
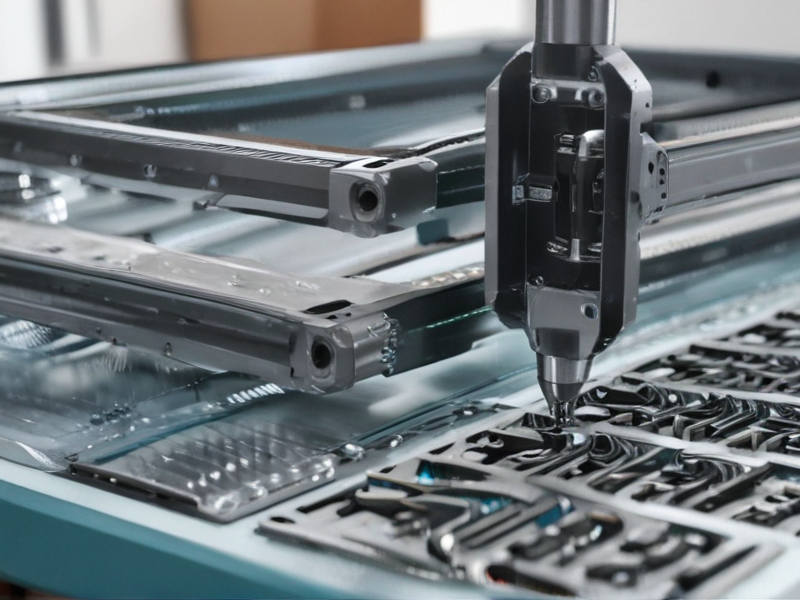
Price Cost Research for cnc laser cutter manufacturers Companies in China, use temu.com and 1688.com
CNC Laser Cutter Price Cost Research for Manufacturers in China
#### Temu.com:
1. Desktop CNC Laser Cutter: Price ranges from $1,200 to $2,000 depending on specifications such as power (30W-60W) and working area size.
2. Industrial CNC Laser Cutter: Prices start around $8,000 and can exceed $20,000 for high-power models (100W+) and larger working areas (up to 1500x3000mm).
#### 1688.com:
1. Mini CNC Laser Cutter: Prices range from ¥6,000 to ¥10,000 ($900 to $1,500), suitable for small businesses and hobbyists.
2. Medium to Large CNC Laser Cutters: Prices range from ¥50,000 to ¥150,000 ($7,500 to $22,500), designed for larger scale industrial applications. Specifications include power ranges from 80W to 150W and larger workspaces (e.g., 1300x2500mm).
#### Summary:
– Desktop Models: $1,200 – $2,000 (Temu), ¥6,000 – ¥10,000 ($900 – $1,500, 1688)
– Industrial Models: $8,000 – $20,000+ (Temu), ¥50,000 – ¥150,000 ($7,500 – $22,500, 1688)
These price ranges reflect the varying specifications and capabilities offered by different models from small, desktop units to large, industrial machines.
Shipping Cost for cnc laser cutter import from China
Importing a CNC laser cutter from China involves several cost components, including shipping, import duties, taxes, and potentially other fees. Here’s a breakdown of the typical costs:
1. Shipping Costs
Shipping costs vary based on the shipping method (air, sea, or rail) and the size and weight of the CNC laser cutter.
– Air Freight: Faster but more expensive. Costs range from $5 to $10 per kilogram. Ideal for smaller, high-value items.
– Sea Freight: More economical for large items. A 20-foot container can cost between $1,000 to $3,000, depending on the distance and current freight rates.
– Rail Freight: An alternative for regions connected by rail networks. Prices are generally lower than air but higher than sea freight.
2. Import Duties and Taxes
– Import Duties: Vary by country but typically range from 0% to 10% of the equipment’s value.
– VAT/GST: Most countries charge Value Added Tax or Goods and Services Tax on imports, usually around 5% to 20%.
3. Additional Fees
– Customs Clearance Fees: Costs for processing the import can range from $50 to $200.
– Insurance: Optional but recommended. It typically costs around 0.5% to 2% of the cargo’s value.
– Port Fees and Handling Charges: These can add another $100 to $500.
Example Calculation
For a CNC laser cutter weighing 500 kg and valued at $10,000, shipped by sea:
– Shipping: $1,500
– Import Duties (5%): $500
– VAT (15%): $1,500
– Customs and Other Fees: $300
Total Estimated Cost: $3,800 (excluding the cutter’s cost).
Conclusion
The total shipping cost can vary widely based on shipping method and local regulations. Always get quotes from multiple shipping companies and check local import regulations to get a precise estimate.
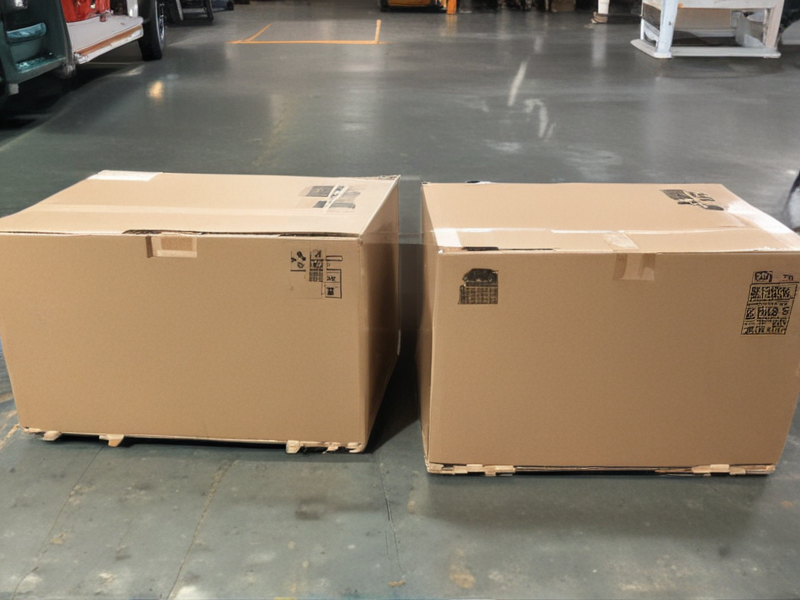
Compare China and Other cnc laser cutter Markets: Products Quality and Price,Visible and Hidden Costs
When comparing CNC laser cutters from China with those from other markets like Germany, Japan, and the USA, several key factors stand out: product quality, price, and costs.
Product Quality
Chinese CNC laser cutters have improved significantly, offering decent performance for a lower price. However, they often fall short in precision, durability, and advanced features compared to German and Japanese machines, which are renowned for their high precision, reliability, and advanced technology.
Price
Chinese CNC laser cutters are typically much cheaper, often costing 30-50% less than their German or Japanese counterparts. This lower price is appealing for small businesses and hobbyists.
Visible Costs
– China: Lower upfront cost, but potential need for frequent replacements and upgrades.
– Other Markets: Higher initial investment with longer-lasting equipment and advanced features that can lead to better long-term value.
Hidden Costs
– China:
– Maintenance: Higher due to lower build quality.
– Downtime: Potentially higher due to less reliable components.
– Training and Support: Often limited or less comprehensive.
– Other Markets:
– Maintenance: Lower, with better durability and fewer breakdowns.
– Downtime: Lower, owing to better reliability and quicker support.
– Training and Support: More robust, often including comprehensive manuals, training programs, and prompt technical support.
In summary, Chinese CNC laser cutters offer an affordable entry point with decent quality but come with higher long-term hidden costs. In contrast, cutters from other markets, while more expensive initially, provide superior quality, reliability, and lower hidden costs, making them a better investment for larger-scale operations.
Custom Private Labeling and Branding Opportunities with Chinese cnc laser cutter Manufacturers
Custom private labeling and branding opportunities with Chinese CNC laser cutter manufacturers offer a cost-effective and efficient way for businesses to enter or expand in the market. Here’s how you can capitalize on these opportunities:
1. Diverse Product Range: Chinese manufacturers offer a wide range of CNC laser cutters, from entry-level models to high-precision industrial machines. This variety allows businesses to select products that best match their market needs and brand positioning.
2. Custom Design and Specifications: Many manufacturers provide customization options, including bespoke designs, specific technical specifications, and additional features. This ensures the product aligns with your brand’s unique selling points and customer requirements.
3. Branding and Packaging: Manufacturers can incorporate your branding elements directly onto the machines, such as logos, color schemes, and brand-specific designs. Additionally, they can provide customized packaging that enhances brand identity and appeal.
4. Cost-Effectiveness: China’s manufacturing sector benefits from economies of scale, reducing production costs without compromising quality. This cost advantage allows businesses to achieve higher profit margins while maintaining competitive pricing.
5. Quality Assurance: Leading Chinese CNC laser cutter manufacturers adhere to international quality standards (ISO, CE, FDA). They offer rigorous quality control processes, ensuring the final product meets your expectations and regulatory requirements.
6. Flexible MOQ: Many manufacturers offer flexible minimum order quantities (MOQ), making it feasible for both large enterprises and small businesses to engage in private labeling.
7. After-Sales Support and Warranties: Reputable manufacturers provide robust after-sales support, including technical assistance, maintenance services, and comprehensive warranties, enhancing customer satisfaction and loyalty.
8. Rapid Prototyping and Production: Chinese manufacturers excel in rapid prototyping and production, allowing quick turnaround times from design to delivery. This agility helps businesses respond swiftly to market demands and trends.
By leveraging these opportunities, businesses can effectively differentiate their products, enhance brand visibility, and expand their market presence with high-quality CNC laser cutters tailored to their specifications.
Tips for Procurement and Considerations when Purchasing cnc laser cutter
When procuring a CNC laser cutter, careful consideration of various factors is crucial to ensure optimal performance and return on investment. Here are some key tips and considerations:
1. Identify Needs:
– Determine the primary materials and thicknesses you will be cutting. This influences the type of laser (CO2, fiber, or crystal) and power requirements.
2. Laser Type:
– CO2 lasers are versatile for non-metallic materials and thin metals.
– Fiber lasers are excellent for metals and offer high efficiency.
– Crystal lasers (YAG) are suitable for thicker materials and specialized applications.
3. Power and Speed:
– Higher wattage lasers cut faster and thicker materials but are more expensive. Match power to your operational needs to balance cost and efficiency.
4. Cutting Bed Size:
– Ensure the bed size accommodates your largest workpieces. Consider future scaling needs to avoid frequent upgrades.
5. Software Compatibility:
– Check if the machine’s software integrates well with your existing design tools and offers features like nesting, which optimizes material usage.
6. Precision and Tolerance:
– Evaluate the machine’s precision to ensure it meets your quality standards, especially for intricate designs.
7. Maintenance and Support:
– Choose a reliable supplier offering robust technical support and easy access to spare parts. Regular maintenance contracts can prevent downtime.
8. Operating Costs:
– Factor in electricity consumption, maintenance, and consumables (like lenses and nozzles) into the total cost of ownership.
9. Training and Safety:
– Ensure operators receive adequate training. Verify that the machine meets safety standards, including proper ventilation and protective enclosures.
10. Future-Proofing:
– Consider modular options or upgradable models to keep up with technological advancements without a complete replacement.
11. Budget and ROI:
– Balance upfront costs with potential productivity gains. Calculate the return on investment based on increased production capacity and reduced labor costs.
By addressing these considerations, you can make a well-informed decision that aligns with your production goals and budget constraints.
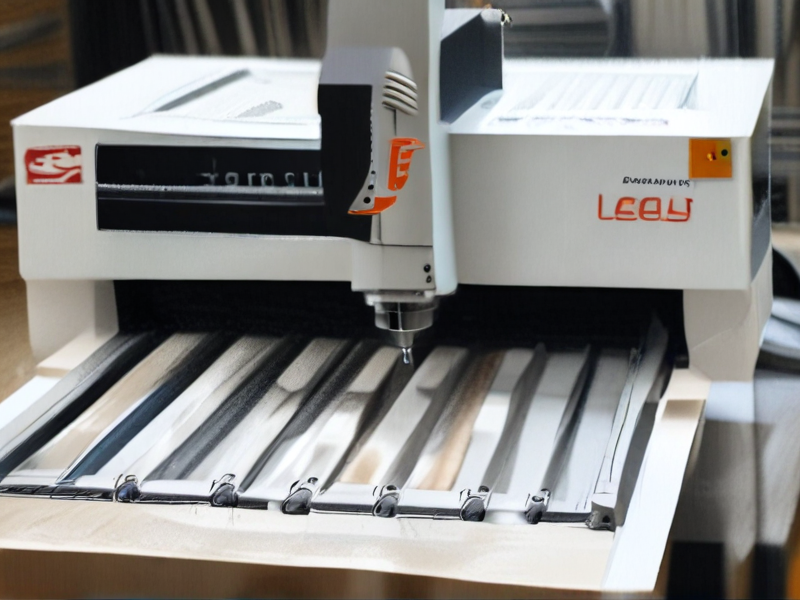
FAQs on Sourcing and Manufacturing cnc laser cutter in China
FAQs on Sourcing and Manufacturing CNC Laser Cutters in China
1. Why source CNC laser cutters from China?
China is a global leader in manufacturing CNC laser cutters due to its advanced technology, skilled labor, and cost-effectiveness. The country offers a wide range of options, from basic models to high-end, specialized machines, catering to various industrial needs.
2. How to find reliable manufacturers?
To find reliable manufacturers, research online directories like Alibaba and Made-in-China, attend trade shows, and request recommendations from industry peers. Checking certifications and reviewing customer feedback is also essential.
3. What are the key certifications to look for?
Look for ISO 9001 for quality management systems, CE marking for compliance with European standards, and FDA approval if the products are intended for the U.S. market. These certifications ensure that the manufacturer adheres to international quality and safety standards.
4. What factors should I consider when choosing a manufacturer?
Consider factors such as the manufacturer’s experience, production capacity, quality control processes, after-sales service, and customer support. It’s also beneficial to visit the factory to assess their facilities and capabilities.
5. How do I handle communication and language barriers?
Many Chinese manufacturers have English-speaking sales teams. Use clear, simple language and confirm all details in writing. Employing a sourcing agent can also help bridge communication gaps.
6. What are the payment terms and methods?
Common payment terms include a 30% deposit with the balance paid before shipment. Payment methods usually include bank transfers (T/T), Letters of Credit (L/C), and sometimes online payment systems. Always use secure and traceable payment methods.
7. How to ensure product quality before shipment?
Request product samples and third-party inspections before finalizing the order. Third-party inspection companies can verify that the products meet your specifications and quality standards before shipment.
8. What are the shipping options and costs?
Shipping options include air freight, sea freight, and courier services, depending on the urgency and volume of the order. Sea freight is the most cost-effective for large shipments. Be sure to account for customs duties and taxes in your budget.
9. How can I resolve disputes with manufacturers?
Include detailed terms and conditions in the contract. In case of disputes, start with negotiation and mediation. If unresolved, consider arbitration through recognized bodies like the China International Economic and Trade Arbitration Commission (CIETAC).
10. What after-sales support can I expect?
Reliable manufacturers offer after-sales support including installation guidance, technical training, spare parts supply, and maintenance services. Ensure these services are included in your agreement.