Top 10 casting steel in China introduce,list main products and website if have
Top 10 Casting Steel Companies in China
1. China Baowu Steel Group
– Main Products: High-strength steel, automotive steel, silicon steel, long steel, stainless steel.
– Website: [China Baowu Steel Group](http://www.baosteel.com/)
2. HBIS Group
– Main Products: Steel bars, steel plates, steel pipes, and steel coils.
– Website: [HBIS Group](http://www.hbisco.com/)
3. Ansteel Group
– Main Products: Hot and cold-rolled steel, galvanized steel, steel sections.
– Website: [Ansteel Group](http://www.ansteel.cn/)
4. Jiangsu Shagang Group
– Main Products: Steel billets, wire rods, steel bars, hot-rolled coils.
– Website: [Jiangsu Shagang Group](http://www.sha-steel.com/)
5. Shougang Group
– Main Products: Flat steel products, long steel products, special steel.
– Website: [Shougang Group](http://www.shougang.com.cn/)
6. Shandong Iron & Steel Group
– Main Products: Steel plates, steel bars, steel coils, H-beams.
– Website: [Shandong Iron & Steel Group](http://www.sdsteel.com/)
7. Wuhan Iron and Steel Corporation (WISCO)
– Main Products: Cold-rolled steel, hot-rolled steel, galvanized steel.
– Website: [WISCO](http://www.wisco.com.cn/)
8. Maanshan Iron and Steel Company (Masteel)
– Main Products: Hot-rolled plates, steel sections, special steel.
– Website: [Masteel](http://www.masteel.com.cn/)
9. Tianjin Iron and Steel Group (TISCO)
– Main Products: Stainless steel, carbon steel, high-strength steel.
– Website: [TISCO](http://www.tisco.com.cn/)
10. Benxi Steel Group
– Main Products: Steel plates, steel pipes, wire rods.
– Website: [Benxi Steel Group](http://www.bxsteel.com/)
These companies are the leading producers of various types of steel in China, catering to both domestic and international markets with a wide range of steel products.
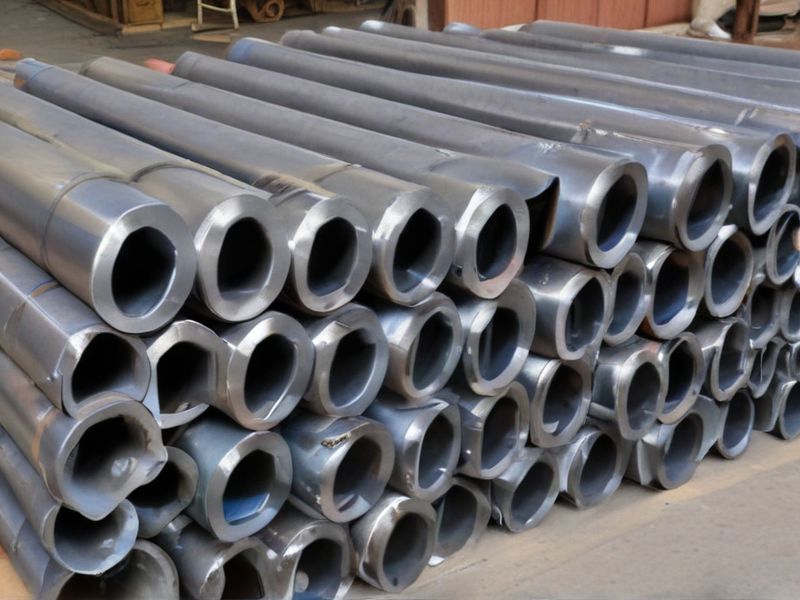
Types of casting steel
Casting steel involves various methods and types depending on the desired properties and applications. Here are the main types of casting steel:
1. Carbon Steel Castings:
– Low Carbon Steel (up to 0.3% carbon): Offers good ductility and toughness, used for parts requiring good machinability.
– Medium Carbon Steel (0.3-0.6% carbon): Balances strength and ductility, suitable for gears, axles, and rails.
– High Carbon Steel (0.6-1.4% carbon): High strength and hardness, used for tools, dies, and cutting instruments.
2. Alloy Steel Castings:
– Low-Alloy Steel: Contains small amounts of alloying elements (1-5%), enhancing properties like strength and toughness. Commonly used in automotive and construction.
– High-Alloy Steel: Contains higher percentages of alloying elements (above 5%). Examples include stainless steel, which contains chromium (usually above 10.5%) for corrosion resistance, used in medical devices and kitchenware.
3. Stainless Steel Castings:
– Austenitic: High chromium and nickel content, non-magnetic, excellent corrosion resistance, used in chemical and food industries.
– Ferritic: Lower nickel, magnetic, moderate corrosion resistance, used in automotive and industrial applications.
– Martensitic: Higher carbon, magnetic, can be hardened, used in cutlery and surgical instruments.
4. Tool Steel Castings:
– Designed for high wear resistance and durability, used in cutting, pressing, and stamping tools.
5. Manganese Steel Castings:
– High impact resistance, used in rock crushers, railway switches, and crossings.
6. Heat-Resistant Steel Castings:
– Can withstand high temperatures, used in furnace parts and gas turbines.
Each type of casting steel is tailored to specific applications by adjusting its composition and heat treatment to meet the desired mechanical properties and performance requirements.
Pros and Cons of Using casting steel
Pros of Using Casting Steel
1. High Strength and Durability: Casting steel offers superior strength and durability, making it suitable for heavy-duty applications in construction, mining, and automotive industries.
2. Versatility in Shape and Size: The casting process allows for the production of complex shapes and sizes that would be difficult or impossible to achieve with other manufacturing methods.
3. Cost-Effective for Large Productions: For large-scale productions, casting steel can be more cost-effective due to the economies of scale, reducing the cost per unit.
4. Excellent Mechanical Properties: Steel castings have excellent mechanical properties, such as high tensile strength, hardness, and resistance to wear and fatigue, which are essential for critical applications.
5. Customization: The casting process allows for a high degree of customization in alloy composition, enabling the production of parts with specific mechanical properties tailored to the needs of particular applications.
Cons of Using Casting Steel
1. High Initial Tooling Costs: The initial costs for creating molds and setting up the casting process can be high, making it less economical for small production runs.
2. Quality Control Challenges: Ensuring consistent quality in steel castings can be challenging due to potential defects such as porosity, shrinkage, and inclusions, which can compromise the integrity of the final product.
3. Longer Production Times: The casting process can be time-consuming, especially for large and complex parts, which may lead to longer lead times compared to other manufacturing methods like machining or forging.
4. Material Waste: The casting process can produce significant material waste due to the need for gating systems and risers, which can increase material costs and require additional processing.
5. Environmental Impact: The casting process involves high energy consumption and emissions, contributing to environmental concerns. Additionally, managing and disposing of waste materials and used molds can be challenging.
In summary, while casting steel provides significant advantages in terms of strength, versatility, and customization, it also presents challenges related to cost, quality control, production time, and environmental impact.
casting steel Reference Specifications (varies for different product)
Steel casting specifications are critical for ensuring the quality, performance, and suitability of steel products for their intended applications. These specifications can vary widely depending on the product type, application, and required properties. Here are key references and typical specifications for different steel casting products:
General Specifications
1. ASTM Standards: Widely used in the U.S., ASTM standards cover various steel grades and casting methods. For example, ASTM A27/A27M specifies carbon steel castings for general applications.
2. EN Standards: European norms such as EN 10293 specify steel castings for general engineering uses.
Product-Specific Specifications
1. Structural Steel Castings:
– ASTM A148/A148M: Specifies high-strength, low-alloy cast steel for structural purposes.
– EN 10340: Covers cast steel for structural uses, detailing mechanical properties and heat treatment requirements.
2. Corrosion-Resistant Castings:
– ASTM A743/A743M: Pertains to corrosion-resistant castings made of stainless steel.
– EN 10283: Specifies corrosion-resistant steel castings for general purposes.
3. Wear-Resistant Castings:
– ASTM A532/A532M: Details the specifications for wear-resistant high chromium cast iron.
4. Heat-Resistant Castings:
– ASTM A297/A297M: Specifies iron-chromium and iron-chromium-nickel castings for high-temperature service.
5. High Alloy Castings:
– ASTM A890/A890M: Covers duplex stainless steel castings known for high strength and resistance to corrosion.
– EN 12513: Specifies high alloy castings with specific chemical and mechanical properties.
Common Specifications
– Chemical Composition: Defines the necessary elements and their percentages (e.g., carbon, manganese, chromium).
– Mechanical Properties: Includes tensile strength, yield strength, elongation, and hardness.
– Heat Treatment: Describes the required thermal processes to achieve desired properties.
– Dimensional Tolerances: Ensures the castings meet precise size and shape requirements.
– Surface Finish: Specifies acceptable surface roughness and defect criteria.
– Non-Destructive Testing (NDT): Standards for inspections like ultrasonic or radiographic testing to detect internal flaws.
Conclusion
The specifications for steel castings are essential for meeting the functional, safety, and performance requirements of various applications. Adhering to recognized standards ensures consistency, reliability, and quality across different products and industries.
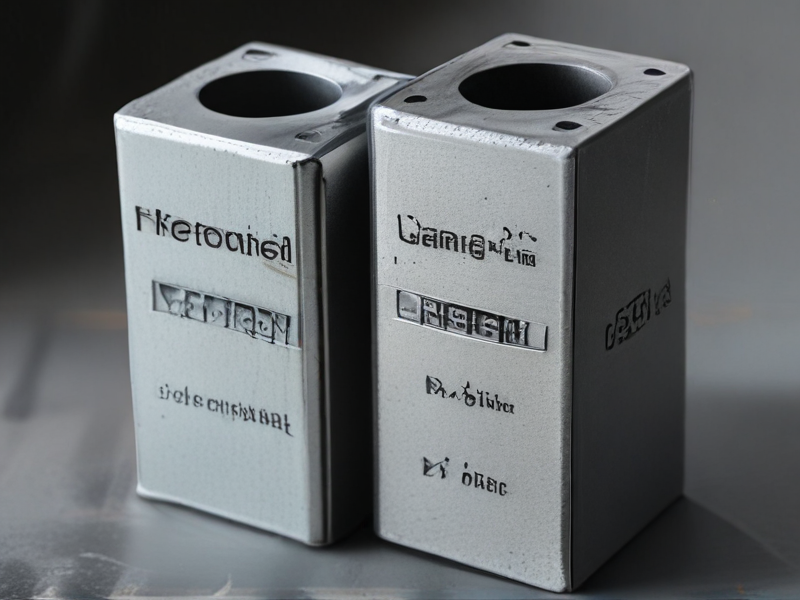
Applications of casting steel
Casting steel involves pouring molten steel into molds to create complex shapes that would be difficult or uneconomical to produce through other methods. This process is used in various industries due to its versatility, strength, and durability. Here are some key applications:
1. Automotive Industry: Steel castings are essential in manufacturing engine blocks, transmission cases, and various structural components due to their strength and ability to withstand high stress and temperatures.
2. Construction: Structural components like beams, columns, and joints are often cast from steel to provide the necessary support and durability for buildings, bridges, and other infrastructures.
3. Mining and Heavy Equipment: Steel castings are used for producing wear-resistant parts such as crusher parts, grinding mills, and excavator components. The toughness of cast steel makes it ideal for handling the harsh conditions in mining operations.
4. Railway: Critical components such as wheels, couplers, and brake parts are made from cast steel to ensure safety, reliability, and long service life in rail transport.
5. Power Generation: Turbine blades, housings, and other parts for power plants, especially those that operate under high pressure and temperature, are often made from cast steel for their high-temperature resistance and durability.
6. Marine: Propellers, rudders, and various other components of ships are made from cast steel due to its corrosion resistance and strength in marine environments.
7. Aerospace: While more limited due to the preference for lightweight materials, cast steel is used in aerospace for certain high-strength components where durability is critical.
8. Oil and Gas: Valves, pumps, and other drilling equipment components are cast from steel to endure high pressures and corrosive environments in oil and gas extraction and processing.
Steel casting’s ability to form complex shapes, combined with its mechanical properties, makes it indispensable across these and other industries.
Material of casting steel
Casting steel involves the process of pouring molten steel into a mold to form a desired shape. The materials used in casting steel include various types of steel alloys, each with specific properties tailored to different applications. Key components of casting steel are:
1. Iron (Fe): The primary element in steel, iron provides the base for the alloy. It is abundant and gives steel its fundamental properties of strength and durability.
2. Carbon (C): Carbon is the most crucial alloying element in steel, typically ranging from 0.02% to 2.14%. It enhances hardness and strength but can make the steel more brittle.
3. Manganese (Mn): Usually added in the range of 0.3% to 1%, manganese improves the steel’s hardness, strength, and wear resistance. It also helps in deoxidizing and desulfurizing the steel.
4. Silicon (Si): Present in small amounts (0.2% to 0.7%), silicon acts as a deoxidizer, improving the fluidity of molten steel and its castability.
5. Chromium (Cr): Added for its corrosion resistance and hardness, chromium is a key component in stainless steel and other high-strength alloys, usually in the range of 0.3% to 4%.
6. Nickel (Ni): Enhancing toughness and corrosion resistance, nickel is commonly found in amounts up to 8% in various steel grades.
7. Molybdenum (Mo): Used to increase strength, hardenability, and corrosion resistance, molybdenum is often included in amounts up to 0.25%.
8. Other Elements: Elements like vanadium (V), titanium (Ti), and aluminum (Al) are sometimes added in trace amounts to enhance specific properties such as grain refinement, strength, and toughness.
The casting process benefits from precise control of these elements to produce steel with the desired mechanical properties and performance characteristics.
Quality Testing Methods for casting steel and how to control the quality
Quality testing of casting steel involves several methods to ensure the material meets specified standards and performance requirements. Here are key testing methods and control measures:
1. Visual Inspection:
– Purpose: Identify surface defects like cracks, porosity, and inclusions.
– Method: Use magnifying glasses, microscopes, or visual aids.
– Control: Regular training of inspectors and standardizing inspection criteria.
2. Dimensional Inspection:
– Purpose: Ensure the cast part conforms to design specifications.
– Method: Use calipers, micrometers, and coordinate measuring machines (CMM).
– Control: Calibration of measuring instruments and adherence to tolerance limits.
3. Non-Destructive Testing (NDT):
– Ultrasonic Testing (UT):
– Purpose: Detect internal flaws like cracks or voids.
– Method: High-frequency sound waves.
– Radiographic Testing (RT):
– Purpose: Identify internal and surface defects.
– Method: X-rays or gamma rays.
– Magnetic Particle Testing (MPT):
– Purpose: Surface and near-surface flaw detection.
– Method: Magnetic fields and iron particles.
– Control: Regular equipment calibration, qualified operators, and periodic audits.
4. Mechanical Testing:
– Tensile Testing:
– Purpose: Determine tensile strength, yield strength, and elongation.
– Method: Tensile test machines.
– Impact Testing:
– Purpose: Assess toughness and material behavior under sudden loads.
– Method: Charpy or Izod impact testers.
– Hardness Testing:
– Purpose: Measure material hardness.
– Method: Rockwell, Brinell, or Vickers hardness testers.
– Control: Standardized testing procedures and equipment calibration.
5. Chemical Analysis:
– Purpose: Verify the composition of the steel.
– Method: Spectroscopy or chemical analysis methods.
– Control: Regular calibration of analytical equipment and strict adherence to sampling procedures.
Quality Control Measures:
– Process Control: Monitor and control parameters such as temperature, alloy composition, and cooling rate during casting.
– Documentation: Maintain detailed records of inspections, tests, and corrective actions.
– Continuous Improvement: Implement feedback loops for process improvement and defect reduction.
– Training: Regular training programs for personnel involved in quality testing and control.
These methods and controls ensure the reliability and performance of cast steel products, minimizing defects and ensuring compliance with industry standards.
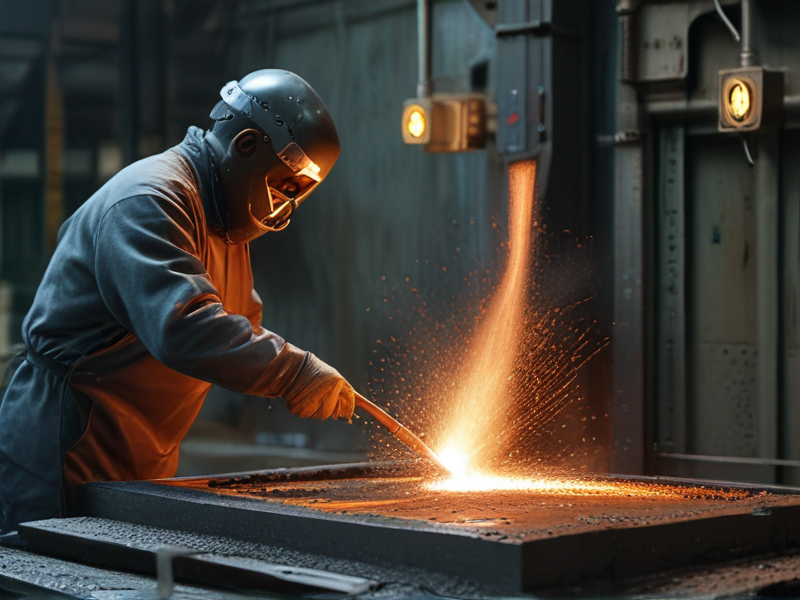
The Work Process and how to use casting steel
Casting steel is a process used to form complex shapes and high-performance components by pouring molten steel into a mold, where it solidifies. Here’s an overview of the work process and usage of casting steel:
Work Process:
1. Pattern Making:
– Create a pattern (model of the part) from wood, plastic, or metal.
– Patterns account for shrinkage and machining allowances.
2. Mold Making:
– Place the pattern in sand or another mold material to form a cavity.
– Use cores for hollow sections.
3. Melting:
– Heat steel in a furnace (electric arc, induction, or open-hearth) to reach its melting point (~1500°C).
– Add alloying elements for desired properties.
4. Pouring:
– Pour molten steel into the mold cavity.
– Ensure controlled flow to avoid defects like turbulence or air entrapment.
5. Cooling and Solidification:
– Allow the steel to cool and solidify within the mold.
– Cooling rate affects grain size and mechanical properties.
6. Removing the Casting:
– Break away the mold material (shakeout).
– Remove cores and clean the casting.
7. Heat Treatment:
– Heat treat (annealing, quenching, tempering) to enhance mechanical properties.
8. Finishing:
– Remove excess material (gating, risers) by cutting or grinding.
– Machine the casting to final dimensions if required.
– Inspect for defects and ensure quality standards.
Usage:
– Automotive: Engine blocks, gears, and suspension components due to high strength and wear resistance.
– Construction: Structural beams, columns, and machinery parts for robustness and durability.
– Aerospace: Turbine blades and airframe components for high strength-to-weight ratios.
– Industrial Equipment: Pumps, valves, and heavy-duty machinery for reliable performance under stress.
Casting steel allows for precise control over material properties and the creation of complex geometries, making it invaluable across various industries.
casting steel Importing questions including Cost,Supplier,Sample,Certification and Market
Casting Steel Importing Guide
1. Cost:
– Unit Price: Steel casting prices vary based on complexity, weight, and material. Typical costs range from $1 to $10 per kilogram.
– Shipping: Include freight costs, customs duties, and taxes. Use Incoterms (e.g., FOB, CIF) to clarify responsibilities.
– Total Cost: Consider both direct and indirect costs, including warehousing and potential tariffs.
2. Supplier:
– Selection: Choose reputable suppliers with proven track records. Websites like Alibaba, Made-in-China, and ThomasNet can be useful.
– Reputation: Check reviews, request references, and consider site visits if feasible.
– Capacity: Ensure the supplier can meet your volume requirements and deadlines.
3. Sample:
– Requesting Samples: Obtain samples to verify quality before placing bulk orders. Be prepared to cover sample and shipping costs.
– Evaluation: Assess samples for material composition, dimensional accuracy, and finishing. Use third-party testing if needed.
– Feedback Loop: Provide feedback and confirm any adjustments before finalizing the main order.
4. Certification:
– Quality Standards: Ensure the supplier complies with international standards like ISO 9001, ASTM, or ASME.
– Material Certifications: Obtain material test reports (MTRs) and certificates of compliance.
– Third-Party Audits: Consider independent audits to verify adherence to quality and safety standards.
5. Market:
– Demand: Analyze market demand for specific types of cast steel to avoid overstocking.
– Competition: Understand the competitive landscape and pricing strategies.
– Regulations: Be aware of import regulations and standards in your target market, including environmental and safety laws.
By thoroughly addressing these aspects, you can ensure a successful and cost-effective steel casting import process.
How to find and select check reliable casting steel manufacturers in China
To find and select reliable casting steel manufacturers in China, follow these steps:
1. Research and Compile a List:
– Use industry directories like Alibaba, Made-in-China, and Global Sources.
– Seek recommendations from industry associations or trade shows like China Foundry Expo.
2. Evaluate Manufacturer Credentials:
– Check certifications like ISO 9001, ISO 14001, or industry-specific standards.
– Review their portfolio to assess experience and expertise in casting steel.
3. Quality and Capacity Assessment:
– Request samples or visit the facility, if possible, to inspect production capabilities and quality control processes.
– Evaluate their technological capabilities, such as advanced casting methods and machinery.
4. Verify Reputation and Reliability:
– Read customer reviews and testimonials.
– Contact previous clients to get firsthand feedback on product quality, delivery reliability, and customer service.
5. Negotiate Terms and Agreements:
– Discuss and agree on terms regarding pricing, minimum order quantities, lead times, and payment conditions.
– Ensure there are clear terms for quality assurance and handling of defective products.
6. Conduct a Trial Order:
– Place a small initial order to evaluate the manufacturer’s performance under real conditions.
7. Long-term Considerations:
– Assess their ability to scale production to meet future demands.
– Establish a communication channel for ongoing support and collaboration.
By following these steps, you can identify and partner with reliable casting steel manufacturers in China.
Background Research for casting steel manufacturers Companies in China, use qcc.com archive.org importyeti.com
Here are some key casting steel manufacturers in China:
1. Deyang Wanzhou Electric Equipment Manufacturing Co., Ltd.
– Location: Deyang, Sichuan Province
– Established: 2006
– Scale: Employs over 500 workers
– Specialties: High-quality steel castings for electric equipment and industrial applications
– Capital: Registered capital of 100 million RMB
– Website: [Deyang Wanzhou on Qcc.com](https://www.qcc.com/firm/decc059427276fa2c327445e55d813d0.html)
2. Dalian Heavy Industry Co., Ltd.
– Location: Dalian, Liaoning Province
– Established: 1914 (restructured in recent years)
– Scale: Over 2,000 employees
– Specialties: Steel castings for heavy machinery and shipbuilding industries
– Capital: Registered capital of 500 million RMB
– Website: [Dalian Heavy Industry on Qcc.com](https://www.qcc.com/firm/02dd168ce0adc9e37877603cadafeef6.html)
3. Luoyang Sunrui Precision Casting Titanium Co., Ltd.
– Location: Luoyang, Henan Province
– Established: 2005
– Scale: 200-299 employees
– Specialties: Precision casting in titanium and steel for aerospace and marine industries
– Capital: Registered capital of 48.3 million RMB
– Website: [Luoyang Sunrui on Qcc.com](https://www.qcc.com/firm/8395b0f06705e900a89c839824610000.html)
4. Daye Special Steel Co., Ltd.
– Location: Huangshi, Hubei Province
– Established: 2007
– Scale: Employs over 5,000 workers
– Specialties: High-performance alloy steels for automotive and industrial applications
– Capital: Registered capital of 2.07 billion RMB
– Website: [Daye Special Steel on Qcc.com](https://www.qcc.com/firm/0d1830b116b7f2f8ceebfc30d7c6c860.html)
These companies represent a diverse range of capabilities and specializations within the steel casting industry in China. For more detailed information on these companies, you can visit Qcc.com.
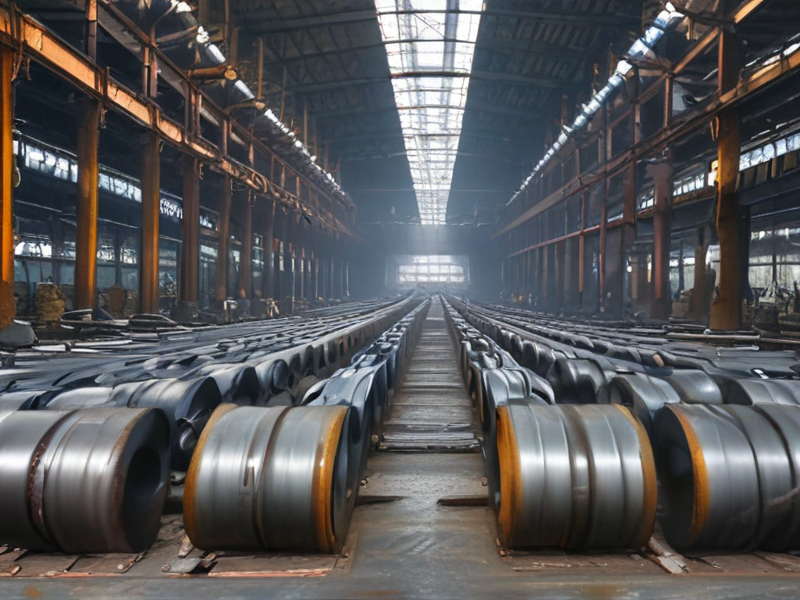
Price Cost Research for casting steel manufacturers Companies in China, use temu.com and 1688.com
On 1688.com, casting steel manufacturers offer a wide range of products, with prices varying based on specifications and order volume. For example, galvanized steel strands (GJ-35) are listed between ¥4.55 and ¥9300 per ton depending on the specific features and manufacturer. Brands like Hebei Anfeng and Hebei Zhongxu are notable suppliers. On Temu.com, similar products are available, but detailed price information is more variable and typically requires direct inquiry for specific quotes. Both platforms offer robust options for sourcing steel casting materials in China【7†source】.
Shipping Cost for casting steel import from China
When importing casting steel from China, shipping costs depend on several factors, including weight, dimensions, shipping method, and destination. Here’s a concise breakdown of what influences these costs and typical pricing:
1. Weight and Volume:
– Shipping costs are calculated based on either the actual weight or the volumetric weight (whichever is higher). Heavy and bulky items like casting steel will likely incur higher costs.
2. Shipping Method:
– Sea Freight: Ideal for large shipments, with costs averaging around $50-$100 per cubic meter (CBM). This method is economical for heavy items but has longer transit times (4-6 weeks).
– Air Freight: Suitable for smaller, urgent shipments, costing approximately $5-$10 per kilogram. Air freight is faster (1-2 weeks) but significantly more expensive.
3. Destination:
– Shipping costs vary based on the distance from China and local port fees. For example, shipping to the U.S. might range from $1,000 to $3,000 for a 20-foot container, while European destinations might cost slightly less or more depending on the specific location.
4. Additional Fees:
– Customs Duties and Taxes: Import duties, VAT/GST, and other taxes are applicable and vary by country.
– Port Handling Fees: Charges for loading and unloading at ports.
– Insurance: Optional but recommended for high-value shipments, usually a small percentage of the cargo value.
Example Calculation:
For a 20-foot container (around 28 cubic meters) of casting steel:
– Sea Freight: 28 CBM x $75 (average rate) = $2,100
– Air Freight: 5,000 kg x $7.50 (average rate) = $37,500
Conclusion:
For bulk shipments, sea freight is generally more cost-effective despite longer transit times. Accurate quotes should be obtained from freight forwarders considering specific shipment details and destinations.
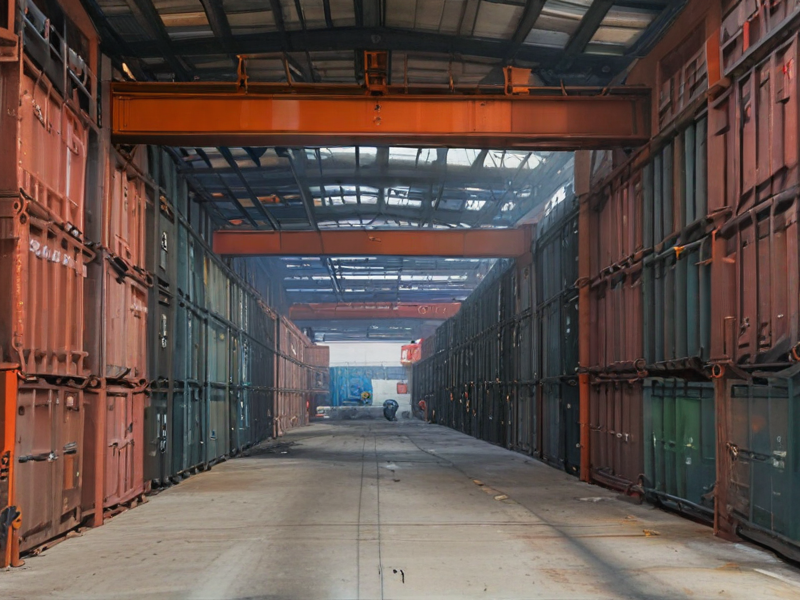
Compare China and Other casting steel Markets: Products Quality and Price,Visible and Hidden Costs
When comparing the casting steel markets of China and other regions (notably Europe and North America), several key factors emerge: product quality, price, and costs (both visible and hidden).
Product Quality:
Chinese casting steel quality has significantly improved over the years. However, it often varies depending on the manufacturer. Generally, European and North American steel castings are considered superior in consistency and compliance with stringent industry standards, ensuring higher reliability and longevity. These regions are known for advanced technology and strict quality control measures.
Price:
Chinese casting steel is typically lower-priced due to cheaper labor, lower raw material costs, and economies of scale. European and North American castings are more expensive, driven by higher labor costs, stringent environmental regulations, and higher operational costs. This price differential makes Chinese products attractive for budget-sensitive projects.
Visible and Hidden Costs:
Visible costs include the initial purchase price and shipping. Chinese steel castings have lower upfront costs and often lower shipping costs due to extensive global logistics networks.
Hidden costs, however, are critical in long-term assessments. These include:
– Quality Assurance: Higher defect rates in some Chinese castings may necessitate additional quality checks and potential rework, increasing operational costs.
– Lead Time: Longer lead times for Chinese imports can delay projects and increase inventory holding costs.
– Regulatory Compliance: Ensuring compliance with local regulations when using Chinese castings can incur additional costs.
– Supply Chain Risks: Political and economic instability can disrupt supply chains, causing delays and increased costs.
– Durability and Maintenance: Lower quality may lead to higher maintenance and shorter product lifespans, increasing total ownership costs.
In conclusion, while Chinese casting steel offers cost advantages, the overall value must consider potential hidden costs and quality differences. For critical applications requiring high reliability, European and North American steel castings may present better long-term value despite higher upfront costs.
Custom Private Labeling and Branding Opportunities with Chinese casting steel Manufacturers
Chinese casting steel manufacturers offer substantial opportunities for custom private labeling and branding due to their advanced production capabilities, cost efficiency, and flexible manufacturing processes. Here are key advantages and considerations:
1. Advanced Manufacturing Capabilities: Chinese manufacturers often employ cutting-edge technology in steel casting, allowing for high-quality and precise production. This enables businesses to create custom designs and specifications tailored to their brand needs.
2. Cost Efficiency: The lower labor and production costs in China can significantly reduce overall expenses, making it economically viable for companies to invest in private labeling. This cost advantage does not compromise quality, as many Chinese manufacturers adhere to international standards.
3. Flexibility in Production: These manufacturers can handle both small and large-scale orders, offering flexibility to businesses of various sizes. Whether you need a limited batch for a niche market or mass production for a global brand, Chinese suppliers can accommodate these demands.
4. Customization Options: With expertise in various casting techniques, manufacturers can offer extensive customization in terms of material grades, finishes, and designs. This allows brands to create unique products that stand out in the market.
5. Strong Supply Chain and Logistics: China’s well-developed infrastructure and logistics network ensure efficient shipping and handling of goods. This minimizes delays and ensures timely delivery of products to global markets.
6. Regulatory Compliance and Quality Assurance: Many Chinese manufacturers are compliant with international regulations and certifications such as ISO, ASTM, and CE, ensuring that the products meet global quality standards.
7. Collaborative Development: Engaging with Chinese manufacturers often involves collaborative product development, where businesses can work closely with engineers and designers to perfect their products.
In summary, Chinese casting steel manufacturers provide a robust platform for businesses seeking custom private labeling and branding opportunities, combining cost-effectiveness with high quality and flexible manufacturing solutions.
Tips for Procurement and Considerations when Purchasing casting steel
When procuring casting steel, careful planning and consideration are crucial to ensure quality, cost-effectiveness, and reliability. Here are some key tips and considerations:
Material Specification
1. Grade Selection: Choose the appropriate steel grade based on the application, such as carbon steel, alloy steel, or stainless steel. Consider factors like mechanical properties, corrosion resistance, and wear resistance.
2. Standards Compliance: Ensure the material meets industry standards (e.g., ASTM, AISI, ISO) to guarantee quality and consistency.
Supplier Selection
1. Reputation and Reliability: Choose suppliers with a strong track record and positive reviews. Reliability in delivery and consistency in quality are crucial.
2. Certification: Verify supplier certifications such as ISO 9001 to ensure adherence to quality management practices.
Quality Control
1. Testing and Inspection: Implement rigorous testing (e.g., non-destructive testing, tensile tests) and inspection protocols. Consider third-party inspections for unbiased verification.
2. Sample Analysis: Request samples and conduct thorough analysis to ensure the material meets required specifications before bulk purchasing.
Cost Management
1. Budgeting: Establish a clear budget considering not just the cost of materials but also transportation, storage, and potential wastage.
2. Negotiation: Negotiate terms with suppliers to secure competitive pricing, considering long-term contracts for better rates.
Logistics and Delivery
1. Lead Time: Factor in the lead time for production and delivery to avoid project delays.
2. Transport and Handling: Ensure proper handling and transport to prevent damage during transit. Evaluate shipping options for cost and reliability.
Sustainability and Compliance
1. Environmental Impact: Opt for suppliers with sustainable practices to minimize environmental footprint.
2. Regulatory Compliance: Ensure compliance with local and international regulations regarding materials and procurement practices.
By focusing on these aspects, you can make informed decisions and secure high-quality casting steel that meets your project requirements efficiently.
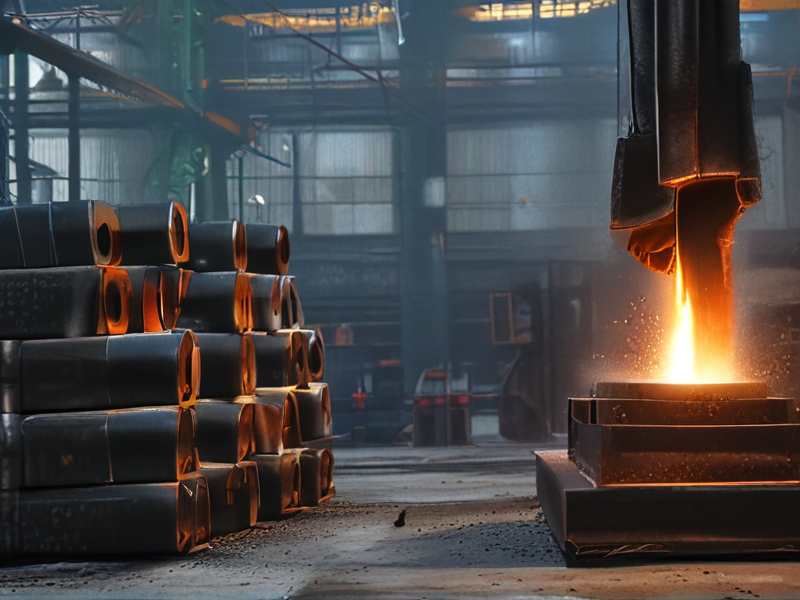
FAQs on Sourcing and Manufacturing casting steel in China
FAQs on Sourcing and Manufacturing Casting Steel in China
1. Why source casting steel from China?
China offers competitive pricing, high production capacity, and advanced technology in steel casting. This makes it a cost-effective option for various industries.
2. How to find reliable suppliers?
Use platforms like Alibaba, Made-in-China, and Global Sources. Verify suppliers’ credentials through certifications like ISO 9001 and customer reviews.
3. What are common challenges?
Quality control, communication barriers, and intellectual property risks are common. Regular inspections and clear contracts can mitigate these issues.
4. How to ensure quality?
Conduct factory audits and request material test reports. Hiring a third-party inspection service can help maintain standards.
5. What about lead times?
Lead times vary based on order size and complexity. Typically, expect 30-60 days. Discuss timelines upfront with suppliers.
6. Are there minimum order quantities (MOQ)?
Yes, most suppliers have MOQs, which can range from a few tons to larger quantities. Negotiation is possible for smaller orders.
7. How to handle logistics?
Use experienced freight forwarders for shipping and customs clearance. Consider insurance to cover potential shipping damages.
8. What payment terms are common?
Terms like 30% deposit and 70% upon shipment are standard. Letters of credit (L/C) are also widely used for secure transactions.
9. How to manage language barriers?
Hiring a local agent or using translation services can help. Clear and concise communication is crucial for successful transactions.
10. What about intellectual property protection?
Include confidentiality agreements and IP clauses in contracts. Register patents and trademarks in China to safeguard IP.
By addressing these key areas, businesses can effectively source and manufacture casting steel in China, leveraging its robust industrial capabilities.