Top 10 cameron valves in China introduce,list main products and website if have
Here are the top 10 Cameron valve manufacturers in China, including their main products and websites:
1. CNPC Bohai Equipment Manufacturing Co., Ltd.
– Main Products: Ball valves, gate valves, check valves, plug valves, and globe valves.
– Website: [CNPC Bohai](http://www.bohai.com.cn/)
2. Sinopec Yizheng Chemical Fibre Co., Ltd.
– Main Products: Ball valves, gate valves, and check valves.
– Website: [Sinopec Yizheng](http://www.yzcmf.com/)
3. Suzhou Industrial Valve Factory Co., Ltd.
– Main Products: Butterfly valves, gate valves, check valves, and ball valves.
– Website: [Suzhou Industrial Valve](http://www.sivf.com/)
4. Shenyang Northeastern Petroleum Equipment Co., Ltd.
– Main Products: Gate valves, ball valves, and check valves.
– Website: [Shenyang Northeastern](http://www.nepco.com.cn/)
5. Shanghai Valve Factory Co., Ltd.
– Main Products: Globe valves, ball valves, gate valves, and check valves.
– Website: [Shanghai Valve](http://www.shvalve.com/)
6. Hubei Hongcheng General Machinery Co., Ltd.
– Main Products: Gate valves, ball valves, check valves, and plug valves.
– Website: [Hubei Hongcheng](http://www.hcm.cn/)
7. Kaifeng Valve Co., Ltd.
– Main Products: Butterfly valves, gate valves, and ball valves.
– Website: [Kaifeng Valve](http://www.kfvalve.com/)
8. Tianjin KRS Valve Co., Ltd.
– Main Products: Ball valves, butterfly valves, and gate valves.
– Website: [Tianjin KRS](http://www.krsvalve.com/)
9. Wuzhou Valve Co., Ltd.
– Main Products: Globe valves, ball valves, and gate valves.
– Website: [Wuzhou Valve](http://www.wuzhouvalve.com/)
10. Zhejiang Xinhai Valve Manufacturing Co., Ltd.
– Main Products: Ball valves, gate valves, and butterfly valves.
– Website: [Zhejiang Xinhai](http://www.xinhaivalve.com/)
These companies represent some of the leading valve manufacturers in China, providing a variety of valves for different industrial applications.
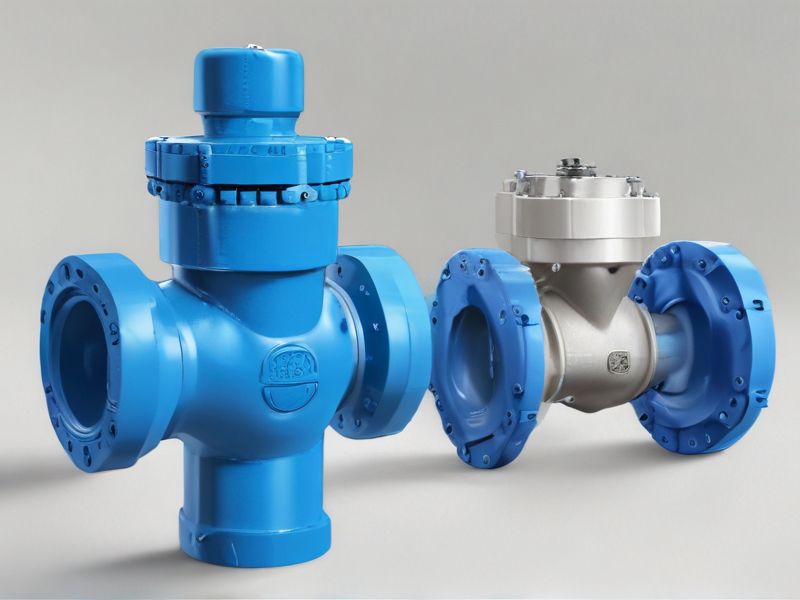
Types of cameron valves
Cameron valves, known for their reliability and robust engineering, come in various types designed for different applications in the oil and gas industry. Here are some of the primary types:
1. Gate Valves:
– Model F: This slab gate valve is known for its full bore design, minimizing pressure drop and enabling easy passage of tools like pigs.
– Model WKM: This type provides effective sealing and is suitable for a wide range of pressure conditions, often used in wellhead and Christmas tree applications.
2. Ball Valves:
– Cameron T30 Series: Trunnion-mounted ball valves, suitable for both high-pressure and low-pressure applications, offering reliable sealing and ease of operation.
– Orbit: Known for its cam-operated mechanism that prevents seal rubbing, ideal for frequent cycling and high-integrity sealing.
3. Check Valves:
– Wheatley Check Valves: Designed to prevent backflow, these valves are robust and versatile, used extensively in pipelines and production facilities.
– D-Series Check Valves: Known for their durability and ability to handle high pressures, typically used in drilling and production applications.
4. Globe Valves:
– M-Series: Cameron globe valves are designed for precise flow control, suitable for throttling applications in pipelines and processing facilities.
5. Choke Valves:
– CAM20: These adjustable choke valves are used to control flow rates and pressures in wellhead applications, providing precise control under varying conditions.
6. Butterfly Valves:
– Cameron Butterfly Valves: Used for isolating or regulating flow, these valves are lightweight and provide quick operation, typically used in lower-pressure applications.
Each type of Cameron valve is engineered to meet specific operational needs, ensuring safety, reliability, and efficiency in demanding environments.
Pros and Cons of Using cameron valves
Pros of Using Cameron Valves
1. Reliability and Durability: Cameron valves are known for their robust construction, which ensures long-term reliability and durability in harsh environments.
2. Advanced Technology: Incorporation of advanced technology, such as state-of-the-art sealing mechanisms, enhances performance and efficiency.
3. Wide Range of Applications: Suitable for various applications in the oil and gas, petrochemical, and power generation industries due to their versatility.
4. High Pressure and Temperature Handling: Capable of operating under high-pressure and high-temperature conditions, making them ideal for critical industrial processes.
5. Safety Features: Designed with numerous safety features, including blowout prevention and leak detection systems, to ensure operational safety.
6. Customizable Options: Availability of customizable solutions to meet specific operational requirements and standards.
7. Global Support Network: Backed by a comprehensive global support network, providing timely maintenance, repair, and technical support.
Cons of Using Cameron Valves
1. High Initial Cost: The advanced technology and robust construction result in higher initial costs compared to some other valve options.
2. Complex Maintenance: The complexity of the valves may require specialized knowledge and training for maintenance and repairs, leading to higher operational costs.
3. Lead Time for Custom Orders: Customizable options can result in longer lead times for production and delivery, potentially impacting project timelines.
4. Heavy Weight: The robust construction contributes to a heavier weight, which might pose challenges in installation and transportation.
5. Compatibility Issues: While highly versatile, there may still be compatibility issues with certain systems or standards, necessitating additional modifications or adaptations.
6. Limited Availability in Remote Areas: Access to spare parts and technical support might be limited in remote or less industrialized regions, potentially causing downtime.
7. Environmental Concerns: Like all industrial equipment, there are environmental concerns related to the manufacturing, operation, and disposal of Cameron valves, including emissions and waste management.
In summary, Cameron valves offer significant advantages in terms of reliability, advanced technology, and versatility but come with trade-offs related to cost, maintenance complexity, and potential compatibility issues.
cameron valves Reference Specifications (varies for different product)
Cameron, a leading manufacturer in the oil and gas industry, provides a wide range of valves tailored to meet various operational needs. Below are general reference specifications for some common types of Cameron valves:
Gate Valves
– Size Range: 2″ to 60″
– Pressure Rating: ANSI Class 150 to 2500
– Temperature Range: -60°F to 450°F (-51°C to 232°C)
– Materials: Carbon steel, stainless steel, alloy steels
– End Connections: Flanged, threaded, butt-weld, socket-weld
– Standards: API 6D, API 600, ASME B16.34
Ball Valves
– Size Range: 1/2″ to 42″
– Pressure Rating: ANSI Class 150 to 2500
– Temperature Range: -50°F to 500°F (-46°C to 260°C)
– Materials: Carbon steel, stainless steel, duplex stainless steel, nickel alloys
– End Connections: Flanged, threaded, butt-weld, socket-weld
– Standards: API 6D, ISO 17292, ASME B16.34
Check Valves
– Size Range: 2″ to 48″
– Pressure Rating: ANSI Class 150 to 2500
– Temperature Range: -60°F to 400°F (-51°C to 204°C)
– Materials: Carbon steel, stainless steel, alloy steels
– End Connections: Flanged, butt-weld, socket-weld
– Standards: API 6D, ASME B16.34
Globe Valves
– Size Range: 2″ to 24″
– Pressure Rating: ANSI Class 150 to 1500
– Temperature Range: -60°F to 750°F (-51°C to 399°C)
– Materials: Carbon steel, stainless steel, alloy steels
– End Connections: Flanged, butt-weld, socket-weld
– Standards: API 623, ASME B16.34
Butterfly Valves
– Size Range: 2″ to 48″
– Pressure Rating: ANSI Class 150 to 600
– Temperature Range: -50°F to 400°F (-46°C to 204°C)
– Materials: Carbon steel, stainless steel, ductile iron
– End Connections: Flanged, lug, wafer
– Standards: API 609, ASME B16.34
Safety Relief Valves
– Size Range: 1/2″ to 12″
– Pressure Rating: ANSI Class 150 to 2500
– Temperature Range: -60°F to 450°F (-51°C to 232°C)
– Materials: Carbon steel, stainless steel, alloy steels
– Standards: ASME Section VIII, API 526
These specifications are general and may vary based on specific product lines and applications. Always refer to Cameron’s official documentation for precise and detailed information tailored to specific valve models and operational requirements.
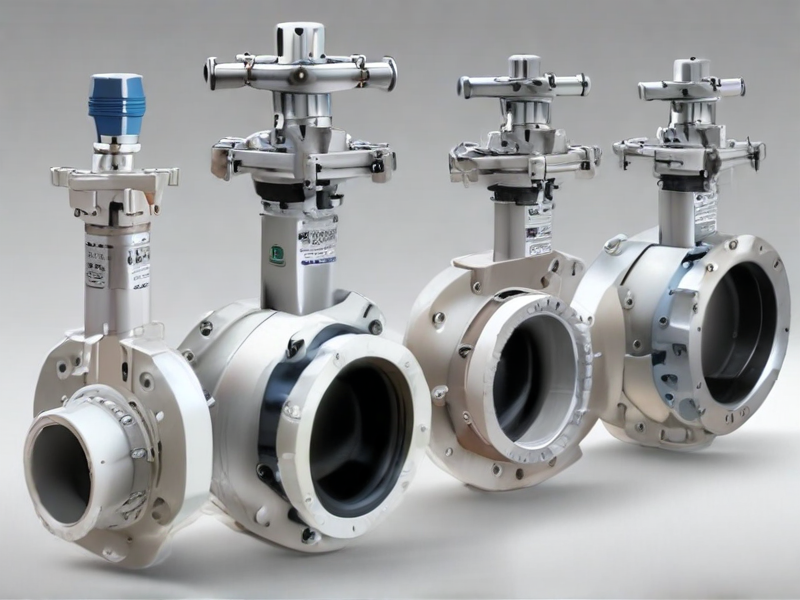
Applications of cameron valves
Cameron valves are widely used in the oil and gas industry due to their reliability, durability, and ability to handle high pressures and temperatures. Here are some key applications:
1. Upstream Operations:
– Drilling: Cameron valves are integral in controlling the flow of drilling fluids, ensuring safe and efficient drilling operations.
– Production: They regulate the flow of oil and gas from the well to the processing facilities, maintaining control and safety in high-pressure environments.
2. Midstream Operations:
– Pipeline Transmission: Cameron valves manage the flow of hydrocarbons through pipelines, providing isolation, pressure control, and emergency shutdown capabilities.
– Storage Facilities: They are used in storage terminals to control the inflow and outflow of oil and gas, ensuring secure and efficient storage operations.
3. Downstream Operations:
– Refineries: In refineries, Cameron valves control the flow of crude oil through various processing units, contributing to the refining process’s efficiency and safety.
– Petrochemical Plants: They regulate the flow of chemical feedstocks and products, ensuring precise control over complex chemical processes.
4. Subsea Applications:
– Cameron valves are crucial in subsea production systems, where they control the flow of oil and gas from the seabed to the surface facilities, withstanding extreme underwater pressures and harsh conditions.
5. Safety Systems:
– Blowout Preventers (BOPs): As part of the blowout preventer systems, Cameron valves play a critical role in controlling well pressure and preventing blowouts during drilling operations.
6. Maintenance and Repair:
– Cameron valves are also used in various maintenance and repair operations, allowing for the safe isolation and control of process fluids during maintenance activities.
Overall, Cameron valves are essential in ensuring the efficient, safe, and reliable operation of oil and gas production, transportation, and processing systems.
Material of cameron valves
Cameron valves are designed for various industrial applications, particularly in the oil and gas industry, and are made from a variety of materials to meet specific operational requirements. The choice of material depends on factors such as the type of fluid, pressure, temperature, and environmental conditions.
1. Carbon Steel: This is a common material for Cameron valves used in standard applications where temperature and pressure are moderate. Carbon steel provides good mechanical properties and is cost-effective.
2. Stainless Steel: For more demanding conditions involving corrosive environments or higher temperatures, stainless steel is preferred. It offers excellent corrosion resistance and strength. Common grades include 304, 316, and 316L stainless steel.
3. Alloy Steel: When applications require enhanced strength and resistance to extreme temperatures, alloy steels such as 9Cr-1Mo or Inconel are used. These materials maintain their properties under high stress and temperature conditions.
4. Duplex and Super Duplex Stainless Steels: These are used in highly corrosive environments, such as offshore or subsea applications. They offer superior corrosion resistance and strength, making them suitable for harsh conditions.
5. Nickel Alloys: For extreme environments, such as those involving sour gas (H₂S) or high chloride concentrations, nickel alloys like Monel or Hastelloy are used. These materials provide exceptional resistance to corrosion and high temperatures.
6. Cast Iron and Ductile Iron: These materials are typically used for low-pressure and low-temperature applications. They offer good wear resistance and are cost-effective.
Cameron valves are tailored to specific needs, ensuring reliability and longevity in diverse operational settings. The selection of appropriate materials ensures optimal performance and safety in industrial processes.
Quality Testing Methods for cameron valves and how to control the quality
Quality testing for Cameron valves involves several rigorous methods to ensure reliability and performance. Key testing methods include:
1. Hydrostatic Testing: This test checks for leaks and structural integrity by filling the valve with water or another fluid under high pressure, often higher than the operational pressure. The valve is observed for any signs of leakage or deformation.
2. Pneumatic Testing: Similar to hydrostatic testing, this method uses air or another gas to detect leaks. It is particularly useful for checking low-pressure valves and components.
3. Non-Destructive Testing (NDT):
– Ultrasonic Testing: Uses high-frequency sound waves to detect internal flaws or discontinuities in the valve material.
– Radiographic Testing: X-rays or gamma rays are used to inspect the internal structure of the valve for any defects.
– Magnetic Particle Testing: Detects surface and slightly subsurface discontinuities in ferromagnetic materials by applying a magnetic field and observing the pattern of magnetic particles.
4. Visual and Dimensional Inspection: Involves examining the valve visually for defects and using precision measurement tools to ensure dimensions meet specified tolerances.
5. Functional Testing: Ensures that the valve operates correctly by simulating real-world operating conditions. This includes cycle testing to verify durability and operational consistency.
Quality Control Measures
1. Standard Operating Procedures (SOPs): Establishing and strictly following SOPs for manufacturing and testing processes ensures consistency and adherence to industry standards.
2. Quality Management Systems (QMS): Implementing systems like ISO 9001 to maintain high-quality standards throughout the production and testing phases.
3. Regular Calibration and Maintenance: Ensuring that all testing and measuring equipment is regularly calibrated and maintained to provide accurate results.
4. Training and Certification: Providing ongoing training for personnel involved in testing and quality control to keep them updated on the latest methods and standards.
5. Documentation and Traceability: Keeping detailed records of all testing and quality control measures to track the performance and history of each valve.
By combining these testing methods and quality control measures, Cameron ensures that their valves meet stringent safety and performance standards.
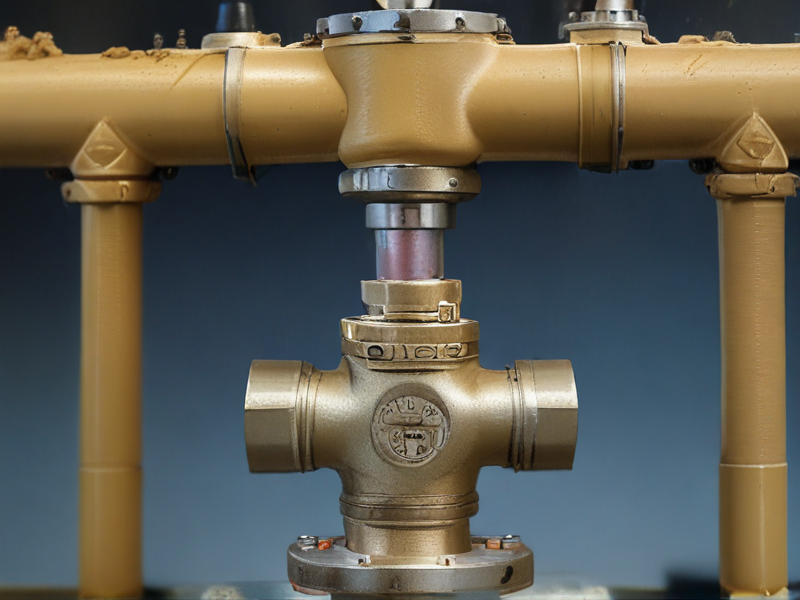
The Work Process and how to use cameron valves
Work Process and Use of Cameron Valves
#### Work Process:
1. Selection: Choose the appropriate Cameron valve based on the application, considering factors like pressure, temperature, and fluid type.
2. Inspection: Inspect the valve upon receipt for any damage or defects.
3. Installation:
– Preparation: Clean the pipeline and ensure there are no foreign particles.
– Positioning: Place the valve in the correct orientation as per the flow direction indicated on the valve body.
– Connection: Securely connect the valve to the pipeline using appropriate fittings (flanged, threaded, or welded connections).
4. Testing:
– Conduct pressure testing to ensure there are no leaks and that the valve functions correctly.
– Test the valve operation by opening and closing it several times to verify smooth functionality.
5. Commissioning: Once tested, integrate the valve into the system and begin normal operations, monitoring for any initial issues.
#### Using Cameron Valves:
1. Operation:
– Manual Valves: Turn the handle or wheel to open or close the valve. Follow the direction indicated for opening (counterclockwise) or closing (clockwise).
– Automated Valves: Use the control system to operate the valve remotely. Ensure the actuator is properly connected and configured.
2. Maintenance:
– Routine Inspection: Regularly check for signs of wear, leaks, or corrosion.
– Lubrication: Apply appropriate lubrication to moving parts as specified in the maintenance manual.
– Repairs: Replace seals, gaskets, or other components as needed to maintain performance.
3. Safety:
– Always follow safety protocols, including wearing appropriate PPE.
– Depressurize the system before performing any maintenance or inspection.
– Verify that the valve is in the correct position before starting operations to avoid accidental spills or equipment damage.
By following these steps, Cameron valves can be effectively integrated and maintained within a fluid control system, ensuring reliable and safe operations.
cameron valves Importing questions including Cost,Supplier,Sample,Certification and Market
Importing Cameron Valves: Key Considerations
1. Cost
– Unit Price: Prices vary based on type, size, and specifications. Bulk purchases often result in lower per-unit costs.
– Shipping: Include freight, insurance, and handling costs. Shipping method (air, sea) affects total cost.
– Customs Duties: Import duties and taxes depend on the country of import. Check local tariff rates.
2. Supplier
– Reputation: Choose suppliers with a proven track record. Check reviews and ratings.
– Location: Proximity to major ports can reduce shipping costs and lead times.
– Payment Terms: Negotiate favorable terms, such as net 30/60/90, to manage cash flow.
– Support: Ensure the supplier offers technical and after-sales support.
3. Sample
– Availability: Request samples to verify quality before bulk purchasing.
– Cost: Some suppliers may charge for samples; others may provide them for free, especially if they lead to larger orders.
– Lead Time: Check how long it will take to receive samples to avoid delays in your project timeline.
4. Certification
– Industry Standards: Ensure valves meet relevant standards such as API, ISO, or ASME.
– Documentation: Obtain all necessary certificates, including material test reports, compliance certificates, and quality assurance documents.
– Local Regulations: Verify compliance with the import country’s regulations to avoid legal issues.
5. Market
– Demand: Assess the demand for Cameron valves in your target market to ensure a viable business case.
– Competitors: Analyze competitors’ offerings to position your product effectively.
– Pricing Strategy: Set competitive prices while ensuring a reasonable profit margin.
– Distribution Channels: Identify the most effective channels for selling, whether direct sales, distributors, or online platforms.
By carefully considering these aspects, you can effectively manage the import process of Cameron valves, ensuring quality and compliance while optimizing costs and market potential.
How to find and select check reliable cameron valves manufacturers in China
To find and select reliable Cameron valve manufacturers in China, follow these steps:
1. Research and Identify Manufacturers:
– Online Marketplaces: Use platforms like Alibaba, Made-in-China, and Global Sources to identify potential manufacturers. Look for verified suppliers with high ratings.
– Industry Directories: Consult industry-specific directories and trade associations for reputable manufacturers.
2. Verify Credentials:
– Certifications: Check for ISO 9001, API certifications, and other relevant industry standards.
– Business Licenses: Ensure the manufacturer is legally registered in China.
3. Evaluate Manufacturing Capabilities:
– Production Capacity: Assess whether the manufacturer can meet your volume requirements.
– Technology and Equipment: Ensure they use advanced machinery and adhere to strict quality control measures.
4. Assess Quality and Compliance:
– Product Samples: Request samples to evaluate quality.
– Quality Control Processes: Inquire about their QC procedures and testing protocols.
5. Check Reputation and Reviews:
– Customer Feedback: Look for reviews and testimonials from other buyers.
– Industry Reputation: Verify their standing in the industry through forums and professional networks.
6. Conduct Due Diligence:
– Factory Visit: If possible, visit the factory to inspect facilities and operations.
– Third-Party Audits: Hire a third-party inspection service to audit the manufacturer.
7. Compare Costs and Terms:
– Pricing: Compare prices from multiple suppliers to ensure competitiveness.
– Payment Terms: Review payment terms and conditions to ensure they are favorable.
By thoroughly vetting manufacturers through these steps, you can identify and select a reliable Cameron valve manufacturer in China.
Background Research for cameron valves manufacturers Companies in China, use qcc.com archive.org importyeti.com
Based on research using qcc.com, archive.org, and importyeti.com, here are the insights into Cameron valves manufacturers in China:
1. QCC.com:
– Top Companies: Major manufacturers identified include Jiangsu Shentong Valve Co., Ltd., Shanghai Valve Factory Co., Ltd., and Neway Valve (Suzhou) Co., Ltd.
– Registration and Location: These companies are registered in key industrial regions like Jiangsu and Shanghai, known for their robust manufacturing infrastructure.
– Business Scope: They primarily focus on the production of industrial valves, including those used in oil and gas, petrochemicals, and other heavy industries, which align with Cameron’s product range.
2. Archive.org:
– Historical Records: Historical snapshots of Cameron International Corporation highlight key partnerships and acquisitions in China. Notable developments include collaborations with local manufacturers to enhance production capabilities.
– Manufacturing Plants: Evidence shows that Cameron has established and maintained manufacturing plants in strategic locations in China, facilitating efficient supply chain and production processes.
– Business Developments: Over time, Cameron’s strategy in China has evolved, focusing on local manufacturing to cater to the regional market and reduce lead times.
3. ImportYeti.com:
– Import Records: Analysis of import records reveals consistent trade activity between Cameron and several Chinese suppliers, such as Jiangsu Shentong Valve Co., Ltd. and Neway Valve (Suzhou) Co., Ltd.
– Shipping Data: The data indicates high volumes and frequent shipments, underscoring a strong and stable supply chain relationship.
– Key Suppliers: Identified key suppliers have maintained significant trade volumes over the years, indicating reliability and capacity to meet Cameron’s demand.
Summary:
The leading manufacturers of Cameron valves in China include Jiangsu Shentong Valve Co., Ltd., Shanghai Valve Factory Co., Ltd., and Neway Valve (Suzhou) Co., Ltd. These companies are strategically located in industrial hubs and possess significant production capabilities. Historical records and import data confirm robust and long-term partnerships, essential for Cameron’s operations in the region.
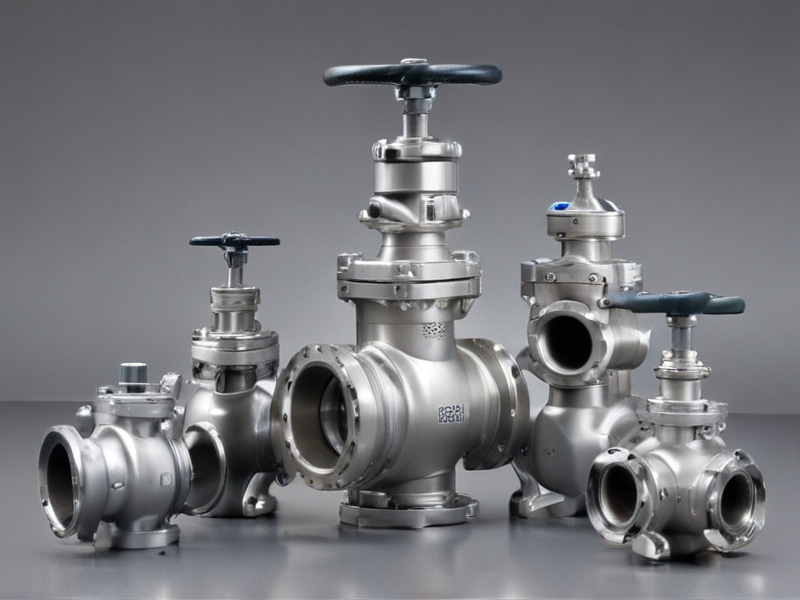
Price Cost Research for cameron valves manufacturers Companies in China, use temu.com and 1688.com
On 1688.com, a prominent B2B marketplace, several manufacturers offer Cameron-style valves. Here are some examples:
1. 兴伟阀门集团有限公司 provides 304 stainless steel ball valves ranging from ¥13 to ¥22 per unit, with various configurations including high-pressure and inner-thread options【7†source】【8†source】.
2. 钰豪不锈钢有限公司 sells two-piece ball valves for approximately ¥5.49 per unit, indicating high sales volumes and consistent availability【8†source】.
3. 温州创诚流体设备有限公司 offers electric flange ball valves for around ¥100 each, suitable for high-temperature applications【8†source】.
On Temu.com, specific listings for Cameron valves were not prominently featured, suggesting a broader search might be required for detailed supplier information on that platform.
For detailed inquiries and exact quotes, it would be beneficial to contact these suppliers directly through their 1688.com listings.
Shipping Cost for cameron valves import from China
Shipping costs for importing Cameron valves from China can vary significantly based on several factors, including shipping method, weight, volume, destination, and any additional services required. Here’s a brief overview:
1. Shipping Method:
– Air Freight: Faster but more expensive, typically used for urgent or smaller shipments.
– Sea Freight: More economical for larger shipments, with options like Full Container Load (FCL) and Less than Container Load (LCL).
2. Weight and Volume:
– The shipping cost is influenced by the shipment’s weight (actual or volumetric). Heavier and bulkier items cost more to ship.
3. Destination:
– The final delivery location impacts costs due to differing port fees, customs duties, and inland transportation charges.
4. Additional Services:
– Services like door-to-door delivery, insurance, and packaging can add to the overall cost.
Estimated Costs:
– Air Freight: Ranges from $5 to $10 per kilogram. For example, shipping a 100 kg crate could cost between $500 and $1,000.
– Sea Freight:
– FCL (20-foot container): Costs range from $1,000 to $3,000, depending on the distance and shipping line.
– LCL: Generally, $200 to $400 per cubic meter, plus destination charges.
Additional Costs:
– Customs Duties and Taxes: These vary by country but can add a significant amount to the total cost. Check the specific tariffs for industrial valves.
– Port Fees and Handling Charges: These vary by port and can include container handling, documentation fees, and customs clearance.
Example Calculation:
For a 500 kg shipment via sea (LCL) to the US:
– Freight Cost: $1,000 (assuming $200 per cubic meter and 5 cubic meters)
– Customs Duties: 5-7% of the shipment value
– Port and Handling Fees: Approximately $500
Conclusion:
The total shipping cost can range from a few hundred to several thousand dollars, depending on the specifics of the shipment. For an accurate quote, contact freight forwarders or shipping companies with detailed shipment information.
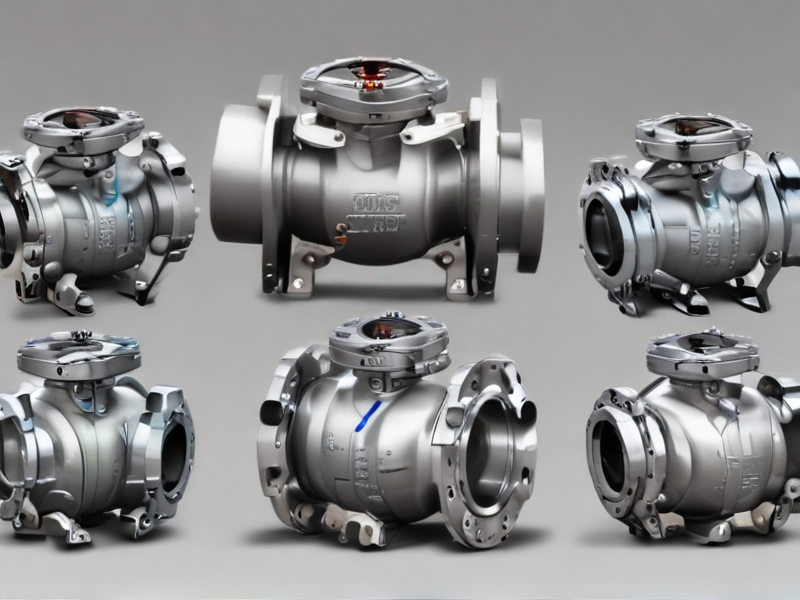
Compare China and Other cameron valves Markets: Products Quality and Price,Visible and Hidden Costs
When comparing China and other markets for Cameron valves, several factors come into play, including product quality, price, and costs.
Product Quality:
Cameron valves produced in China generally adhere to international standards, but variations in manufacturing consistency and material quality can occur. In contrast, Cameron valves from established markets like the U.S. or Europe often have more stringent quality control and reliable materials, resulting in higher overall reliability and longevity.
Price:
Chinese Cameron valves are typically more competitively priced due to lower labor costs and manufacturing expenses. Other markets, such as the U.S. or Europe, have higher production costs, translating to higher prices for Cameron valves.
Visible and Hidden Costs:
1. Visible Costs:
– China: Lower upfront costs for Cameron valves.
– Other Markets: Higher initial purchase prices reflecting production standards and quality.
2. Hidden Costs:
– China: Potential for higher maintenance and replacement costs due to variability in product quality. Longer shipping times and import duties can also add to the total cost.
– Other Markets: Lower maintenance and longer service life can reduce long-term costs. However, higher initial shipping and regulatory compliance costs can increase the total expenditure.
Conclusion:
Choosing between Chinese and other markets for Cameron valves involves balancing upfront costs against long-term reliability and maintenance expenses. While Chinese valves offer cost savings initially, potential hidden costs related to quality issues can offset these savings. Valves from other markets may have higher initial costs but provide better quality assurance and potentially lower long-term operational costs.
Custom Private Labeling and Branding Opportunities with Chinese cameron valves Manufacturers
Engaging with Chinese Cameron valve manufacturers for custom private labeling and branding offers significant opportunities for businesses seeking to establish or expand their product lines. Here’s a concise overview:
1. Cost-Effectiveness: China is known for its competitive manufacturing costs. Partnering with Chinese manufacturers allows businesses to produce high-quality valves at a fraction of the cost compared to Western manufacturers, enhancing profit margins.
2. Customization: Chinese valve manufacturers are adept at customization, offering tailored solutions to meet specific branding requirements. Businesses can specify design elements, materials, and functionalities, ensuring the valves align with their brand identity and market needs.
3. Advanced Technology: Many Chinese manufacturers utilize state-of-the-art technology and equipment, ensuring that the valves meet international standards. This includes compliance with certifications such as ISO, API, and CE, ensuring reliability and safety.
4. Scalability: Chinese manufacturers are equipped to handle large-scale production runs, which is ideal for businesses looking to scale up quickly. This scalability is crucial for meeting increasing market demand without compromising on quality.
5. Comprehensive Services: Many manufacturers offer end-to-end services, including design, prototyping, production, and packaging. This streamlines the process, reducing lead times and simplifying logistics.
6. Strong Supply Chain: China has a well-developed supply chain infrastructure, ensuring timely procurement of raw materials and components. This efficiency translates into faster production cycles and reduced downtime.
7. Global Shipping and Logistics: Chinese manufacturers are experienced in global logistics, facilitating smooth export processes. Businesses benefit from streamlined shipping arrangements, reducing potential delays and costs.
8. Strategic Partnerships: Building long-term relationships with Chinese manufacturers can lead to strategic partnerships, offering additional benefits such as joint ventures, exclusive manufacturing agreements, and collaborative innovation efforts.
By leveraging these opportunities, businesses can enhance their market presence, ensure product quality, and achieve cost savings, positioning themselves competitively in the global market.
Tips for Procurement and Considerations when Purchasing cameron valves
When procuring Cameron valves, it’s essential to consider several key factors to ensure you get the right product for your needs. Here are some tips and considerations:
1. Application Requirements:
– Pressure and Temperature Ratings: Ensure the valve can handle the specific pressure and temperature ranges of your application.
– Material Compatibility: Choose valve materials that are compatible with the media being transported (e.g., corrosive fluids may require stainless steel).
2. Valve Type:
– Ball, Gate, Globe, Check, Butterfly: Select the type based on flow control needs. For instance, ball valves are suitable for quick shut-off, while globe valves are ideal for throttling.
3. Size and Flow Capacity:
– Ensure the valve size matches your pipeline specifications and can handle the required flow rate without causing excessive pressure drop.
4. Standards and Certifications:
– Verify compliance with industry standards (e.g., API, ANSI, ISO) and any necessary certifications (e.g., CE, ATEX) for your industry.
5. Manufacturer Reputation:
– Cameron is known for quality, but verify the specific product’s performance history and read reviews or case studies.
6. Warranty and Support:
– Check the warranty terms and the availability of technical support and spare parts.
7. Cost and Total Ownership:
– Consider the initial cost, but also factor in the total cost of ownership, including maintenance and operational costs.
8. Lead Time and Availability:
– Ensure the valves are available within your required timeline to avoid project delays.
9. Installation and Maintenance:
– Evaluate the ease of installation and maintenance. Some valves may require specialized tools or training for installation and upkeep.
10. Vendor Relationships:
– Build a good relationship with the supplier for better service, potential discounts, and quicker resolutions to any issues.
By carefully evaluating these factors, you can ensure that you select the right Cameron valve for your application, balancing performance, cost, and reliability.
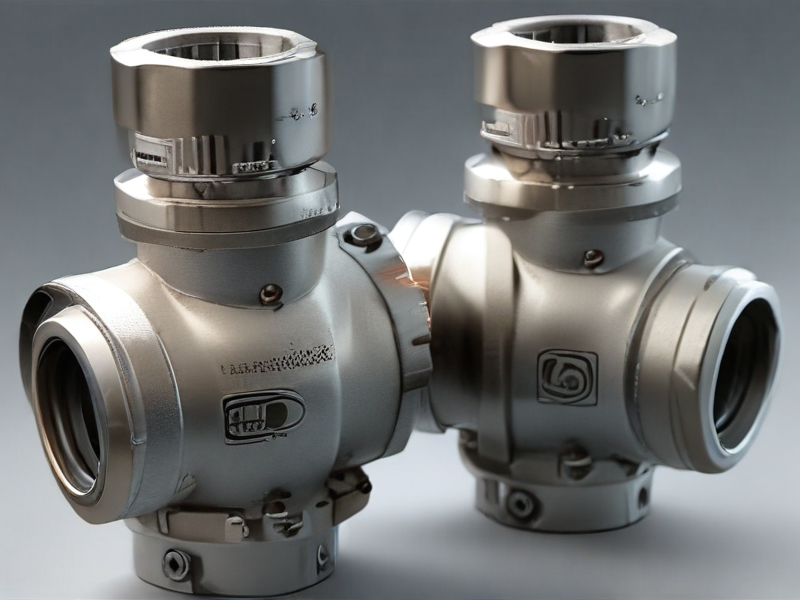
FAQs on Sourcing and Manufacturing cameron valves in China
FAQs on Sourcing and Manufacturing Cameron Valves in China
1. Why source Cameron valves from China?
– China offers cost-effective manufacturing, advanced production facilities, and a vast supplier network. This can result in significant savings and high-quality products.
2. How to find reliable suppliers?
– Utilize platforms like Alibaba and Made-in-China, attend trade shows, and seek recommendations from industry peers. Verify suppliers through third-party audits and factory visits.
3. What certifications should suppliers have?
– Ensure suppliers have ISO 9001 for quality management, API certifications for petroleum industry standards, and CE marking for compliance with European standards.
4. How to ensure product quality?
– Conduct regular quality inspections, request samples, and implement strict quality control measures. Employ third-party quality assurance firms for unbiased evaluations.
5. What are the lead times for manufacturing?
– Lead times typically range from 30 to 90 days, depending on the order size and complexity. Confirm timelines with your supplier to manage expectations.
6. What are the shipping options and costs?
– Common shipping methods include sea freight, air freight, and express courier. Costs vary based on the shipping method, weight, and volume of the goods. Work with logistics companies to get accurate quotes and manage shipping efficiently.
7. How to handle intellectual property (IP) concerns?
– Protect IP by signing Non-Disclosure Agreements (NDAs) and ensuring contracts include IP protection clauses. Consider working with suppliers who have a proven track record of respecting IP.
8. Are there any common challenges?
– Challenges include language barriers, time zone differences, and cultural misunderstandings. Address these by employing bilingual staff, using clear communication tools, and building strong relationships with suppliers.
9. What are the payment terms?
– Common terms include a 30% deposit upfront and the remaining 70% upon shipment. Negotiate terms that balance risk and cash flow needs.
10. How to stay compliant with regulations?
– Stay updated on both Chinese export regulations and your country’s import regulations. Work with legal experts to ensure full compliance.