Top 10 brewery tanks in China introduce,list main products and website if have
Here are the top 10 brewery tank manufacturers in China, their main products, and websites:
1. NDL Craft
– Main Products: Brewhouses, fermentation tanks, brite tanks, keg cleaners, and fillers.
– Website: [ndlcraft.com](http://www.ndlcraft.com)
2. Micet Craft
– Main Products: Microbrewery setups, fermentation tanks, brite tanks, and complete brewing systems.
– Website: [micetcraft.com](http://www.micetcraft.com)
3. Lehui Craft
– Main Products: Brewhouses, fermentation tanks, brite tanks, kegging, casking, bottling, and canning equipment.
– Website: [lehuicraft.com](http://www.lehuicraft.com)
4. WeBrew
– Main Products: Brewhouses, unitanks, brite tanks, HLT/CLT, and keg washers.
– Website: [thewebrew.com](http://www.thewebrew.com)
5. GrainBrew
– Main Products: Nanobrewery systems, microbrewery equipment, commercial brewing systems, fermentation tanks, and brite tanks.
– Website: [grainbrew.com](http://www.grainbrew.com)
6. Zhejiang Dayu Light Industrial Machinery Co., Ltd.
– Main Products: Filling machines, capping machines, labeling machines, and packaging machines.
– Website: [dayumachinery.com](http://www.dayumachinery.com)
7. YoLong Brewtech
– Main Products: Brewhouses, fermentation tanks, bright beer tanks, CIP systems, and more.
– Website: [yolongbrewtech.com](http://www.yolongbrewtech.com)
8. Ningbo HGM Food Machinery Co., Ltd.
– Main Products: Food processing machinery, dough mixers, dough sheeters, bread slicers, and planetary mixers.
– Website: [hgmfoodmachinery.com](http://www.hgmfoodmachinery.com)
9. Jinan Shun Long Machinery Co., Ltd.
– Main Products: CNC routers, laser engraving machines, plasma cutting machines, and fiber laser marking machines.
– Website: [shunlongmachinery.com](http://www.shunlongmachinery.com)
10. Jinan China-Germany Brewing Co., Ltd.
– Main Products: Brewhouses, fermentation tanks, brite tanks, and packaging equipment.
– Website: [jinanchinagermanbrewing.com](http://www.jinanchinagermanbrewing.com)
These companies are well-regarded for their high-quality brewing equipment, catering to both small craft breweries and large-scale commercial operations.
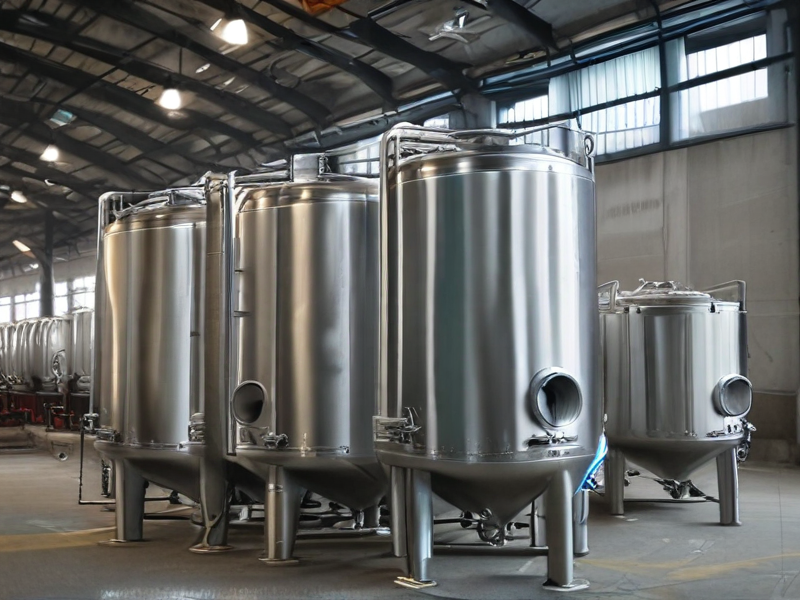
Types of brewery tanks
Brewery tanks are crucial in the brewing process, with specific types serving distinct functions:
1. Mash Tun: This insulated vessel mixes milled grains with hot water, converting starches to fermentable sugars through enzymatic action.
2. Lauter Tun: Used after mashing, this tank separates the liquid wort from the grain husks, often equipped with a false bottom for effective filtration.
3. Brew Kettle/Boil Kettle: Where wort is boiled and hops are added. The boiling process sterilizes the wort and extracts flavors and bitterness from hops.
4. Whirlpool Tank: Utilized post-boiling, this tank separates hop residues and trub (sediment) from the wort by creating a centrifugal motion.
5. Fermentation Tank: The primary fermentation vessel where yeast converts wort sugars into alcohol and CO₂. They can be cylindrical or conical to aid in yeast collection and beer clarity.
6. Bright Tank: Used for conditioning, carbonating, and clarifying beer before packaging. It’s also where additional flavors can be infused.
7. Unitank: A versatile tank that combines fermentation and conditioning processes, allowing for a more compact brewing system.
8. Hot Liquor Tank: Stores hot water used throughout the brewing process, primarily for mashing and sparging (rinsing grains).
9. Cold Liquor Tank: Stores chilled water used to rapidly cool the wort after boiling, typically for use in heat exchangers.
Each tank plays a vital role in ensuring the efficiency and quality of beer production, contributing to the overall flavor, clarity, and stability of the final product.
Pros and Cons of Using brewery tanks
Pros and Cons of Using Brewery Tanks
#### Pros
1. Efficiency: Brewery tanks streamline the brewing process, allowing for large batches to be produced consistently and efficiently.
2. Quality Control: Tanks provide better control over fermentation conditions, such as temperature and pressure, ensuring a consistent product quality.
3. Scalability: Tanks enable brewers to scale up production easily to meet increased demand without compromising quality.
4. Hygiene: Modern brewery tanks are designed for easy cleaning and sterilization, reducing the risk of contamination.
5. Space Utilization: Vertical tanks optimize the use of floor space, allowing breweries to maximize their production capacity within limited areas.
6. Automation: Tanks often integrate with automated systems for monitoring and controlling the brewing process, enhancing precision and reducing manual labor.
#### Cons
1. Cost: High-quality brewery tanks require significant upfront investment, which can be a barrier for small or new breweries.
2. Maintenance: Regular maintenance is essential to ensure tanks function properly, which can be time-consuming and costly.
3. Complexity: The integration of advanced tanks requires technical expertise for operation and troubleshooting.
4. Flexibility: Large tanks may limit the ability to experiment with small batches or diverse recipes, potentially stifling creativity.
5. Energy Consumption: Tanks, especially those requiring precise temperature control, can consume substantial energy, impacting operational costs and environmental footprint.
6. Space Requirement: While vertical tanks save floor space, the overall facility must accommodate the height and weight of these tanks, which might necessitate structural modifications.
In summary, brewery tanks offer significant advantages in efficiency, quality control, and scalability, essential for commercial brewing success. However, the high costs, maintenance needs, and potential limitations on flexibility pose challenges that must be carefully managed.
brewery tanks Reference Specifications (varies for different product)
Brewery tanks, essential for beer production, come in various types and specifications depending on the production stage and specific requirements. Key types include fermentation tanks, brite tanks, and storage tanks. Below are reference specifications for each type:
Fermentation Tanks
– Capacity: Ranges from 1 BBL (31 gallons) to 300 BBL (9,300 gallons) or more.
– Material: Typically stainless steel (304 or 316 grade) for durability and sanitation.
– Pressure Rating: Usually designed for 1-2 bar pressure; some models can handle higher pressures for carbonation.
– Features:
– Conical bottom for yeast collection.
– Cooling jackets for temperature control.
– CIP (Clean-In-Place) systems for easy cleaning.
– Sampling ports, racking arms, and pressure relief valves.
Brite Tanks
– Capacity: Similar to fermentation tanks, ranging from 1 BBL to 300 BBL.
– Material: Stainless steel (304 or 316 grade).
– Pressure Rating: Typically rated for higher pressures up to 3 bar, suitable for carbonation.
– Features:
– Cooling jackets for maintaining optimal temperatures.
– Pressure gauge and relief valves.
– Sight glass and sample ports for monitoring clarity and quality.
– Sanitary design for easy cleaning and maintenance.
Storage Tanks
– Capacity: Varies widely from small batch storage of a few barrels to large-scale storage of hundreds of barrels.
– Material: Stainless steel is preferred, though food-grade plastic and other materials are used for smaller or less critical storage.
– Features:
– Often includes temperature control mechanisms.
– Valves and ports for easy transfer of beer.
– Insulation for temperature stability.
– CIP systems for sanitation.
General Considerations
– Dimensions: Vary significantly based on capacity; generally, larger tanks are taller to reduce the footprint.
– Finish: Interior polished to a sanitary finish (RA < 0.8 µm), exterior can be polished or brushed.
– Compliance: Should meet relevant industry standards (e.g., ASME, CE).
These specifications ensure the tanks are suitable for various stages of brewing, maintaining the quality and safety of the beer throughout the production process.
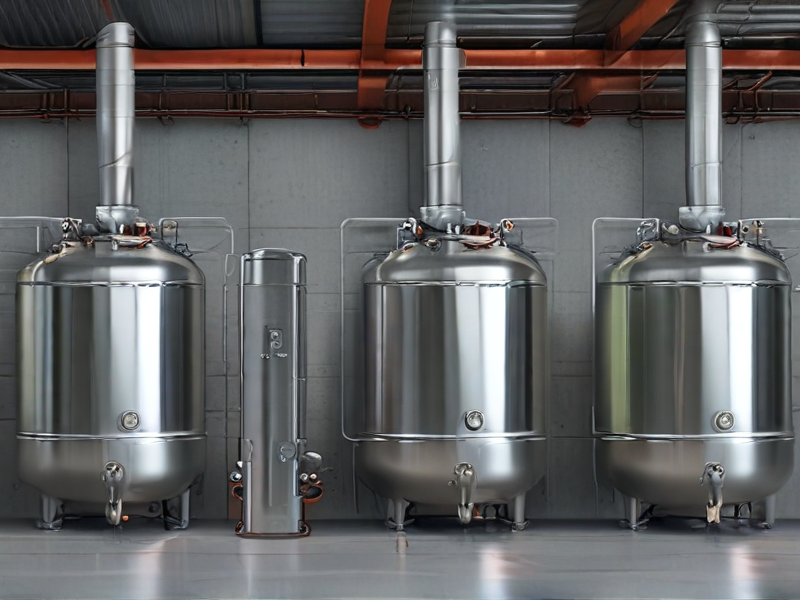
Applications of brewery tanks
Brewery tanks play a crucial role in the beer production process, serving various functions at different stages of brewing. Here are the primary applications of these tanks:
1. Mash Tun: The mash tun is used for mashing, where malted grains are mixed with hot water to convert starches into fermentable sugars. This tank must maintain specific temperatures and allow for efficient mixing and enzyme activity.
2. Lauter Tun: After mashing, the mixture is transferred to the lauter tun. Here, the wort (liquid) is separated from the grain husks. The design of this tank, with its slotted bottom and rakes, facilitates the efficient separation of liquid from solids.
3. Brew Kettle: The wort is then boiled in the brew kettle. This process sterilizes the wort, halts enzyme activity, and allows for the addition of hops, which provide bitterness and aroma. The kettle must handle high temperatures and be equipped with systems for steam or direct heating.
4. Whirlpool Tank: Post-boiling, the wort is transferred to the whirlpool tank. This tank uses centrifugal force to separate hop particles and other solids from the wort, ensuring a cleaner liquid for fermentation.
5. Fermentation Tank: The wort is cooled and transferred to fermentation tanks, where yeast is added to convert sugars into alcohol and carbon dioxide. These tanks are designed to control temperature and pressure, which are critical for consistent fermentation and beer quality.
6. Bright Beer Tank (BBT): After fermentation, the beer is conditioned in bright beer tanks. These tanks allow for maturation, carbonation, and the clarification of beer, ensuring it reaches the desired flavor, clarity, and carbonation levels before packaging.
7. Storage and Serving Tanks: For breweries that serve directly on-site, storage and serving tanks hold the finished beer. These tanks must maintain consistent temperatures and carbonation levels to preserve beer quality until it is served.
Each type of brewery tank is designed to optimize specific aspects of the brewing process, contributing to the production of high-quality beer.
Material of brewery tanks
Brewery tanks are primarily constructed from stainless steel, which is favored for its durability, ease of cleaning, and resistance to corrosion. The most common grades used are 304 and 316 stainless steel.
304 Stainless Steel: This is the standard material for brewery tanks. It offers excellent corrosion resistance and is cost-effective. It’s suitable for handling most brewing processes and cleaning agents used in the industry. Its surface finish can be polished to a high degree, making it easy to sanitize, which is crucial in brewing to prevent contamination.
316 Stainless Steel: This grade contains molybdenum, which increases its resistance to pitting and corrosion, especially against chlorides and acids. It is more expensive than 304 but is often used in brewing environments that involve more aggressive cleaning agents or processes that require higher purity standards.
Copper: Historically, copper was used for brewing vessels due to its excellent heat conductivity and antimicrobial properties. However, it has largely been replaced by stainless steel due to copper’s susceptibility to corrosion and its reactivity with certain brewing ingredients, which can affect the taste and quality of the beer.
Other Materials: In some smaller or specialized brewing operations, plastic or glass might be used for fermentation tanks. However, these materials are generally less durable and harder to clean, making them less suitable for larger or more professional setups.
The choice of material for brewery tanks is crucial as it affects the brewing process’s efficiency, hygiene, and overall quality. Stainless steel, with its blend of durability, resistance to corrosion, and ease of cleaning, remains the industry standard, ensuring consistent and high-quality beer production.
Quality Testing Methods for brewery tanks and how to control the quality
Quality testing for brewery tanks is essential to ensure the final product meets safety and quality standards. Here are the key methods and control measures:
Quality Testing Methods
1. Visual Inspection: Regularly check tanks for signs of wear, corrosion, or contamination. This includes inspecting welds and seals.
2. Pressure Testing: Conduct hydrostatic or pneumatic tests to ensure tanks can withstand operating pressures without leaking.
3. Cleaning and Sanitization: Use CIP (Clean-In-Place) systems for thorough cleaning. Verify cleanliness through swab tests and ATP (adenosine triphosphate) testing.
4. Microbial Testing: Regularly test for microbial contamination using plate counts and PCR (polymerase chain reaction) methods to detect bacteria, yeast, and mold.
5. Material Verification: Ensure tanks are made from food-grade stainless steel. Perform surface integrity tests like dye penetrant inspection to check for cracks.
Quality Control Measures
1. Standard Operating Procedures (SOPs): Develop and follow SOPs for cleaning, sanitization, and maintenance of tanks.
2. Regular Maintenance: Schedule routine maintenance to replace worn parts and prevent contamination. Keep detailed logs of all maintenance activities.
3. Calibration: Regularly calibrate sensors and gauges to ensure accurate readings for temperature, pressure, and other critical parameters.
4. Training: Ensure staff are well-trained in hygiene practices and the correct operation and maintenance of brewery tanks.
5. Sampling and Monitoring: Implement a robust sampling plan to regularly test the beer at different stages of the brewing process. Use tools like pH meters, thermometers, and spectrophotometers for consistent monitoring.
6. Documentation: Maintain comprehensive records of all tests, inspections, and maintenance activities. This helps in tracing any issues and ensuring compliance with industry standards.
By combining these methods and controls, breweries can maintain high-quality standards, ensuring the safety and consistency of their products.
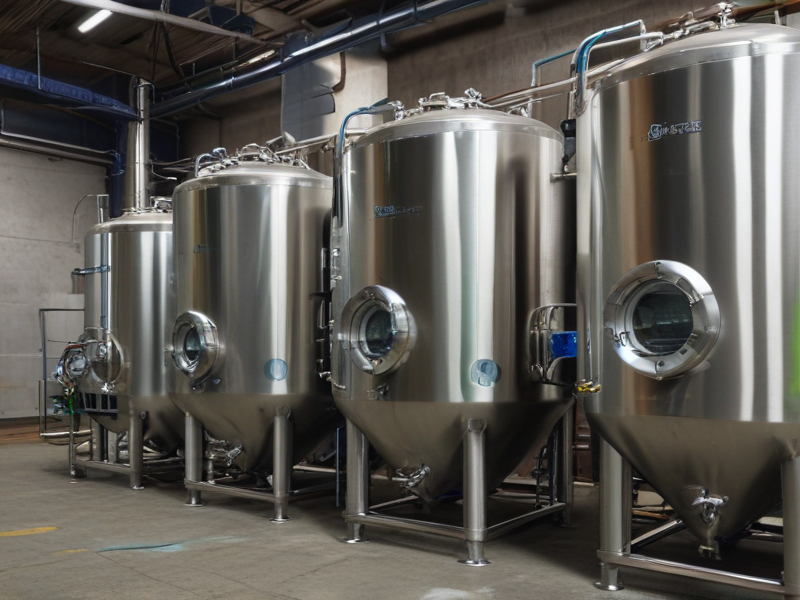
The Work Process and how to use brewery tanks
The brewing process involves several key steps, each utilizing specific brewery tanks to achieve the desired beer quality.
1. Milling: Malted barley is crushed in a mill to break the grain and expose the starches necessary for brewing.
2. Mashing: The crushed grains, now called grist, are mixed with hot water in a mash tun. This process converts the starches to fermentable sugars, creating a thick, sugary liquid called wort.
3. Lautering: The wort is separated from the grain husks in a lauter tun. This tank has a false bottom to filter out the solids.
4. Boiling: The wort is transferred to a brew kettle or boil kettle and boiled for an hour or more. Hops are added during this stage for bitterness, flavor, and aroma.
5. Whirlpooling: After boiling, the wort is moved to a whirlpool tank to separate hop particles and other solids through centrifugal force.
6. Cooling: The wort is rapidly cooled using a heat exchanger to prepare it for fermentation.
7. Fermentation: The cooled wort is transferred to a fermentation tank, where yeast is added. The yeast converts the sugars in the wort into alcohol and carbon dioxide, creating beer. This process can take several days to weeks.
8. Conditioning: After fermentation, the beer is conditioned in a bright tank or conditioning tank to mature and develop flavors. This stage can also include carbonation if needed.
9. Packaging: The finished beer is filtered and transferred to kegs, bottles, or cans for distribution.
Key Brewery Tanks:
– Mash Tun: Converts starches to sugars.
– Lauter Tun: Separates wort from grain husks.
– Brew Kettle: Boils the wort and adds hops.
– Whirlpool Tank: Removes solids post-boil.
– Fermentation Tank: Ferments wort into beer.
– Bright Tank: Conditions and matures the beer.
Each tank is crucial for specific steps, ensuring the beer’s quality and flavor. Proper use and maintenance of these tanks are essential for successful brewing.
brewery tanks Importing questions including Cost,Supplier,Sample,Certification and Market
Importing Brewery Tanks: Key Considerations
1. Cost:
– Initial Purchase: Brewery tanks vary in cost depending on size, material, and brand. Stainless steel tanks, preferred for their durability and cleanliness, can range from $1,000 to $50,000 or more.
– Shipping and Import Duties: Consider the costs of international shipping, import duties, and taxes. Shipping can add 10-20% to the purchase price.
2. Supplier:
– Reputation: Choose suppliers with a solid track record and positive reviews from other breweries.
– Location: Suppliers from countries known for quality manufacturing (e.g., Germany, China, USA) might offer better products. Proximity can also impact shipping costs and lead times.
– Support: Ensure the supplier provides good customer service, warranty, and after-sales support.
3. Sample:
– Requesting Samples: It’s beneficial to request samples or visit the supplier’s facility to inspect the tanks.
– Quality Check: Check for weld quality, material thickness, and overall craftsmanship. A sample can also help verify if the tank meets specific brewing requirements.
4. Certification:
– Compliance: Ensure tanks meet local and international standards, such as ISO 9001 for quality management.
– Safety Standards: Verify certifications like CE marking (Europe) or ASME certification (USA) to ensure the tanks adhere to safety and quality standards.
– Sanitation: Look for tanks certified for food and beverage use, ensuring they meet hygiene standards.
5. Market:
– Demand: Research the local demand for brewery tanks to ensure a viable market.
– Trends: Stay updated on industry trends, such as increasing demand for craft beer, which might influence tank size and type.
– Competitors: Analyze competitors’ equipment to gauge market standards and preferences.
By considering these factors, you can make informed decisions when importing brewery tanks, ensuring quality, compliance, and cost-effectiveness.
How to find and select check reliable brewery tanks manufacturers in China
Finding and selecting reliable brewery tank manufacturers in China involves several steps:
1. Research: Start with online research using business directories like Alibaba, Made-in-China, and Global Sources. These platforms list numerous manufacturers with detailed product descriptions and reviews.
2. Verification: Verify the legitimacy of the manufacturers by checking their business licenses, certifications (such as ISO, CE), and production capabilities. Look for companies with extensive experience and positive customer feedback.
3. Quality Assurance: Ensure the manufacturers adhere to international quality standards. Check if they have certifications like ISO 9001 or CE marking, which indicate compliance with quality management systems and safety standards.
4. References and Reviews: Read reviews and ask for references. Contact previous customers to gather feedback on product quality, reliability, and after-sales service.
5. Samples and Site Visits: Request samples to inspect the quality firsthand. If possible, visit the manufacturing site to assess their production facilities, equipment, and quality control processes.
6. Communication and Support: Evaluate the manufacturer’s responsiveness and willingness to provide support. Effective communication is crucial for addressing any issues that may arise during production or after delivery.
7. Pricing and Contracts: Compare pricing, but don’t compromise on quality for cost. Ensure all terms, including warranties, delivery timelines, and payment methods, are clearly defined in the contract.
By following these steps, you can identify reliable brewery tank manufacturers in China and ensure a successful partnership.
Background Research for brewery tanks manufacturers Companies in China, use qcc.com archive.org importyeti.com
Researching brewery tank manufacturers in China, several key sources provide valuable insights.
QCC.com: This platform is a comprehensive database of Chinese companies, offering detailed profiles that include business scope, financials, and certifications. It is an essential tool for identifying legitimate and reputable manufacturers in the brewery tank industry.
ImportYeti: This tool analyzes U.S. Customs sea shipment records to identify suppliers and manufacturers. For brewery tanks, ImportYeti can help pinpoint Chinese manufacturers exporting to the U.S., providing data on shipment volumes, product descriptions, and customer relationships. For instance, ImportYeti’s database includes extensive details on various manufacturers, helping to assess their export activities and reliability.
Archive.org: Utilizing the Wayback Machine on Archive.org can provide historical data on manufacturers’ websites, offering insights into their longevity, product evolution, and historical business practices. This can be particularly useful for verifying the consistency and reliability of potential suppliers.
Combining these resources offers a comprehensive view of the Chinese brewery tank manufacturing landscape, ensuring informed and reliable sourcing decisions.
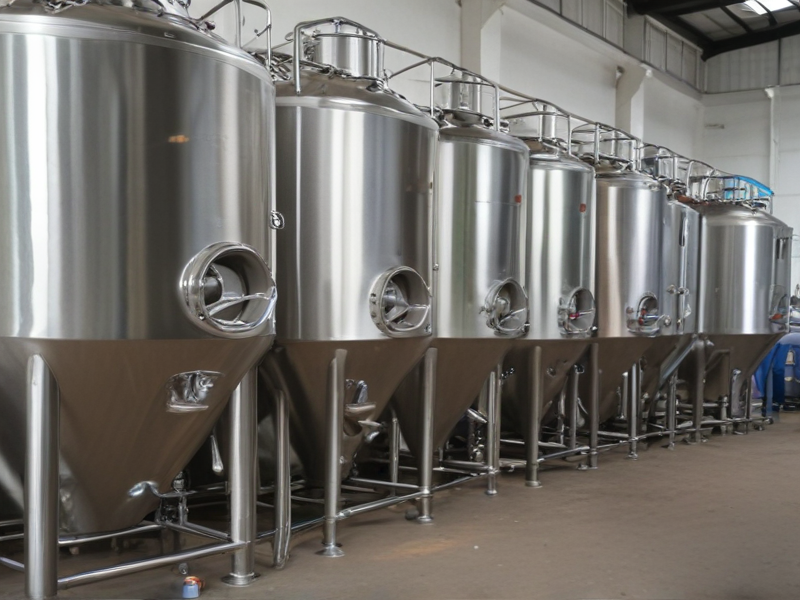
Price Cost Research for brewery tanks manufacturers Companies in China, use temu.com and 1688.com
When researching brewery tanks manufacturers in China, two useful platforms are Temu.com and 1688.com.
Temu.com: This platform offers a variety of industrial equipment including brewery tanks. Prices and suppliers vary, so it’s advisable to compare multiple listings to find the best deals. It’s also important to check the product specifications and supplier ratings to ensure quality and reliability.
1688.com: As a major B2B marketplace operated by Alibaba, 1688.com has a wide range of brewery tanks from different manufacturers. For instance:
– Qingdao Sanzhuji Equipment Co., Ltd. offers stainless steel brewery tanks at competitive prices, often ranging from ¥10,000 to ¥50,000 depending on the size and customization options.
– Jinan Cassman Machinery Co., Ltd. provides complete brewing systems with prices starting around ¥30,000 for small-scale equipment.
On 1688.com, you can find both standard and custom options, with suppliers offering different capacities and configurations to suit various brewing needs. It’s beneficial to review product details and negotiate with suppliers for bulk orders or specific requirements.
Both platforms provide robust search functions, allowing you to filter by price, supplier location, and product features to find the most suitable options for your needs. Ensure to communicate clearly with suppliers about your specifications and verify their credentials before making a purchase.
For more detailed information, you can visit [Temu.com](https://www.temu.com) and [1688.com](https://www.1688.com).
Shipping Cost for brewery tanks import from China
Shipping costs for importing brewery tanks from China depend on various factors, including the size and weight of the tanks, the shipping method, the destination, and current market conditions. Here’s a brief overview:
1. Shipping Methods:
– Sea Freight: Most cost-effective for large, heavy items like brewery tanks. Costs vary based on the container size (20ft or 40ft) and the shipping route. A 20ft container might cost between $1,000 and $3,000, while a 40ft container can range from $2,000 to $5,000.
– Air Freight: Faster but significantly more expensive. Suitable for urgent shipments or smaller tanks. Costs range from $5 to $10 per kilogram.
2. Factors Affecting Costs:
– Size and Weight: Larger and heavier tanks incur higher costs. Custom tanks may need special arrangements, increasing the price.
– Destination: Shipping to major ports is cheaper than inland locations. Additional costs for customs clearance, duties, and inland transportation should be considered.
– Market Conditions: Prices fluctuate based on demand, fuel prices, and global shipping disruptions.
3. Additional Costs:
– Insurance: Highly recommended for high-value items. Costs about 0.5% to 1% of the cargo value.
– Customs Duties and Taxes: Varies by country. Ensure compliance with local regulations to avoid delays and extra costs.
– Handling and Delivery: Fees for loading, unloading, and delivering to the final destination.
For accurate estimates, contact freight forwarders or shipping companies with specific details about the tanks and destination. Comparing multiple quotes can help find the best deal.
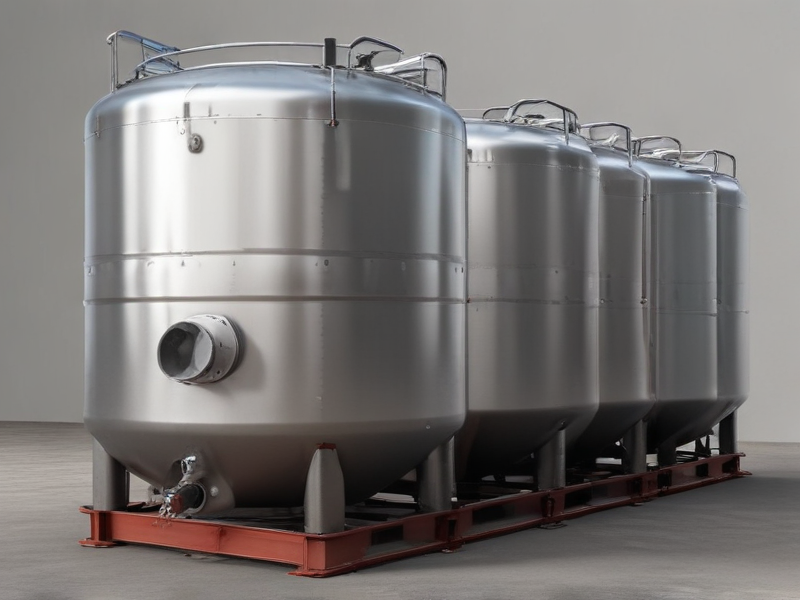
Compare China and Other brewery tanks Markets: Products Quality and Price,Visible and Hidden Costs
Comparison of Brewery Tanks Markets: China vs. Others
Product Quality and Price
Chinese brewery tanks are generally known for their competitive pricing. They offer cost-effective solutions due to lower labor and manufacturing costs. However, quality can vary widely. High-end manufacturers in China produce tanks that meet international standards, but lower-end products may suffer from quality control issues. In contrast, tanks from Europe and North America, such as those from Germany and the USA, are typically of higher quality, reflecting stringent manufacturing standards and advanced technology. These tanks, however, come at a higher price point, often significantly more expensive than Chinese alternatives.
Visible and Hidden Costs
Visible costs include the initial purchase price and shipping. Chinese tanks usually have lower visible costs, making them attractive upfront. European and North American tanks, while higher in purchase price, often have lower shipping costs within their regions. Hidden costs are crucial in this comparison. Chinese tanks may incur additional costs related to quality assurance, maintenance, and potential modifications to meet local standards. These can include replacement parts, frequent repairs, and higher downtime costs. On the other hand, tanks from established Western manufacturers often come with comprehensive warranties, better customer support, and longer lifespan, reducing hidden costs over time.
Overall Assessment
While Chinese brewery tanks offer a lower initial investment, potential hidden costs and variability in quality must be considered. Tanks from Europe and North America, despite their higher price, generally provide superior quality, reliability, and lower long-term costs due to fewer maintenance issues and better support.
This assessment highlights the importance of considering both visible and hidden costs and not just the initial purchase price when choosing brewery tanks.
Custom Private Labeling and Branding Opportunities with Chinese brewery tanks Manufacturers
Custom private labeling and branding opportunities with Chinese brewery tank manufacturers offer a significant advantage for breweries looking to establish or expand their brand presence. Chinese manufacturers are well-known for their ability to provide high-quality, cost-effective brewing equipment tailored to specific needs. Here are key opportunities:
1. Cost-Effective Solutions: Chinese manufacturers typically offer competitive pricing due to lower labor and production costs. This affordability allows breweries to invest more in branding and marketing.
2. Customization Options: Many Chinese manufacturers provide extensive customization options for brewing tanks, allowing breweries to tailor equipment to their specific brewing processes and brand aesthetics. This includes custom sizes, finishes, and features.
3. Quality Standards: Reputable Chinese manufacturers adhere to international quality standards, ensuring that their brewing tanks are reliable and durable. Many have certifications such as ISO, CE, and ASME, which attest to their quality and compliance.
4. Advanced Technology: Chinese manufacturers often employ advanced manufacturing technologies and techniques, offering state-of-the-art equipment. This can include automated systems, advanced welding technologies, and precise temperature controls.
5. Branding Opportunities: Custom private labeling allows breweries to feature their logos and branding on the equipment itself. This enhances brand visibility and professionalism, both in the brewery and during tours or promotional events.
6. Scalability: With the ability to produce equipment at scale, Chinese manufacturers can accommodate growing breweries that need to expand their production capacity quickly.
7. Supply Chain Efficiency: Chinese manufacturers often have robust supply chain networks, ensuring timely delivery and reduced downtime for breweries. This efficiency is crucial for maintaining consistent production schedules.
8. Partnership Potential: Establishing a partnership with a Chinese manufacturer can lead to long-term benefits, such as consistent supply, potential discounts, and continuous support for maintenance and upgrades.
In summary, partnering with Chinese brewery tank manufacturers for custom private labeling and branding offers breweries a blend of cost-efficiency, quality, and customization, enhancing their market presence and operational capabilities.
Tips for Procurement and Considerations when Purchasing brewery tanks
When purchasing brewery tanks, careful planning and informed decision-making are essential. Here are key tips and considerations:
1. Determine Requirements:
– Capacity Needs: Assess your production volume and growth projections to determine tank size and quantity.
– Space Constraints: Measure your available space to ensure the tanks fit properly without impeding workflow.
2. Material and Quality:
– Stainless Steel: Opt for high-quality stainless steel for durability, ease of cleaning, and resistance to corrosion.
– Insulation: Ensure tanks have proper insulation to maintain temperature control, crucial for fermentation.
3. Features and Specifications:
– Cooling Jackets: Consider tanks with cooling jackets for precise temperature regulation.
– Manways and Ports: Check for adequate manways, ports, and valves for easy access, cleaning, and sampling.
– Agitation: Some tanks may require mixers or agitators, especially for certain brewing processes.
4. Compliance and Standards:
– Certifications: Ensure tanks meet industry standards and local regulatory requirements (e.g., ASME, PED).
– Documentation: Verify that manufacturers provide detailed specifications and compliance certificates.
5. Supplier Evaluation:
– Reputation and Experience: Choose reputable suppliers with experience in the brewing industry.
– Customization Options: Look for suppliers offering customization to match your specific needs.
– Support and Service: Ensure they provide robust after-sales support and service.
6. Budget and Financing:
– Cost vs. Quality: Balance between cost and quality; cheaper tanks may lead to higher maintenance costs.
– Financing Options: Explore leasing or financing options to manage upfront costs.
7. Installation and Maintenance:
– Professional Installation: Ensure professional installation for proper setup and to avoid operational issues.
– Maintenance Plans: Set up regular maintenance schedules to prolong the lifespan and efficiency of the tanks.
By considering these factors, you can make a well-informed decision, ensuring your brewery tanks meet your operational needs and contribute to the overall efficiency and success of your brewing process.
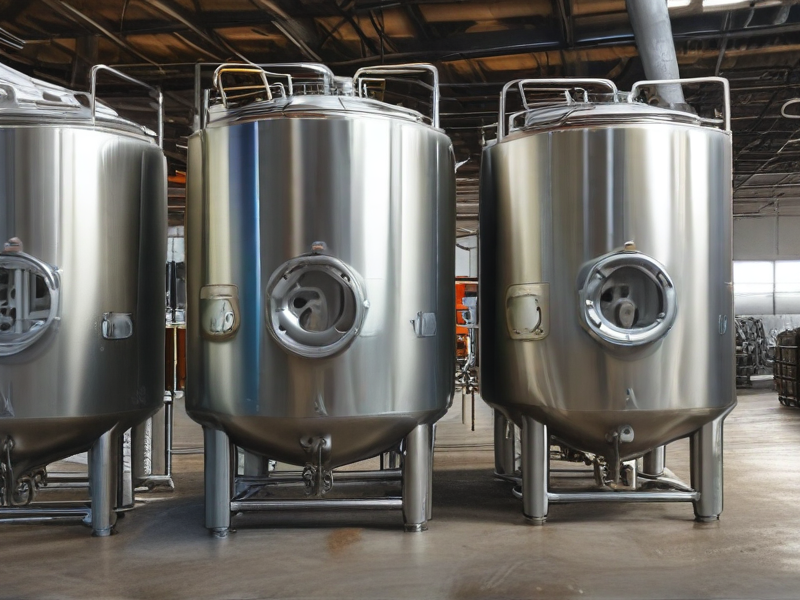
FAQs on Sourcing and Manufacturing brewery tanks in China
FAQs on Sourcing and Manufacturing Brewery Tanks in China
1. Why source brewery tanks from China?
China offers competitive pricing, advanced manufacturing capabilities, and a wide variety of options for customization, making it a preferred destination for sourcing brewery tanks.
2. How to find reliable manufacturers?
Use online platforms like Alibaba, Made-in-China, and Global Sources. Attend trade shows such as the China Brew & Beverage (CBB) Exhibition. Verify manufacturers by checking certifications (ISO, CE), customer reviews, and requesting samples.
3. What are the key certifications to look for?
Ensure manufacturers have ISO 9001 for quality management and CE certification for compliance with European standards. Additional certifications like ASME (for pressure vessels) can also be beneficial.
4. How to ensure product quality?
Conduct factory audits, request detailed product specifications, and inspect production processes. Engage third-party inspection services to verify quality before shipment.
5. What is the typical lead time for production?
Lead times vary depending on order complexity and volume but typically range from 30 to 90 days. Custom orders may require additional time.
6. What are the shipping options and costs?
Shipping options include sea freight, air freight, and rail. Sea freight is the most cost-effective for large orders. Costs depend on the shipment’s size, weight, and destination.
7. How to handle payment and reduce risks?
Use secure payment methods like Letters of Credit (L/C) or Trade Assurance services offered by platforms like Alibaba. Negotiate payment terms such as a deposit (30%) and balance upon delivery or inspection.
8. Are there any import duties or taxes?
Import duties and taxes vary by country. Consult with a customs broker to understand applicable fees and ensure compliance with local regulations.
9. Can manufacturers assist with installation and maintenance?
Many manufacturers offer installation services, training, and maintenance support. Confirm these services during the negotiation phase.
10. What should be included in the contract?
Specify product details, quality standards, payment terms, delivery schedules, warranty terms, and after-sales support. Clearly outline penalties for non-compliance.
These guidelines can help streamline the process of sourcing and manufacturing brewery tanks in China.