Top 10 aluminium for cnc in China introduce,list main products and website if have
Here are the top 10 aluminum CNC machining manufacturers in China, along with their main products and websites:
1. Shenzhen Tuofa Technology Co., Ltd.
– Main Products: CNC milling, CNC turning, grinding, threading, and sandblasting.
– Website: [tuofa-cncmachining.com](https://www.tuofa-cncmachining.com)
2. RapidDirect
– Main Products: CNC machining, injection molding, sheet metal fabrication, 3D printing, and vacuum casting.
– Website: [rapiddirect.com](https://www.rapiddirect.com)
3. Gensun Precision Machining Co., Ltd.
– Main Products: CNC milling, CNC turning, rapid prototyping, and rapid tooling.
– Website: [china-machining.com](https://www.china-machining.com)
4. WayKen Rapid Manufacturing
– Main Products: CNC machining, rapid prototyping, 3D printing, vacuum casting, and rapid tooling.
– Website: [waykenrm.com](https://www.waykenrm.com)
5. Junying Metal Manufacturing Co., Ltd.
– Main Products: CNC turning, CNC milling, CNC drilling, injection molding, and custom machining parts.
– Website: [cnclathing.com](https://www.cnclathing.com)
6. 3ERP
– Main Products: CNC machining, rapid prototyping, vacuum casting, 3D printing, and sheet metal fabrication.
– Website: [3erp.com](https://www.3erp.com)
7. AT Precision Machining Ltd.
– Main Products: CNC milling, CNC turning, laser cutting, CNC bending, and anodizing services.
– Website: [at-machining.com](https://www.at-machining.com)
8. Klarm Machining Ltd.
– Main Products: CNC milling, CNC turning, CNC grinding, and CNC drilling.
– Website: [chinaimportal.com](https://www.chinaimportal.com)
9. Xometry China
– Main Products: 3D printing, injection molding, CNC milling, and CNC machining.
– Website: [xometry.com](https://www.xometry.com)
10. Sunrise Metal Technology Co., Ltd.
– Main Products: CNC machining, die casting, rapid prototyping, and injection molding.
– Website: [sunrise-metal.com](https://www.sunrise-metal.com)
These companies are renowned for their advanced manufacturing capabilities and precision in aluminum CNC machining, catering to various industries including automotive, aerospace, electronics, and medical devices. For more detailed information on their services, you can visit their respective websites.
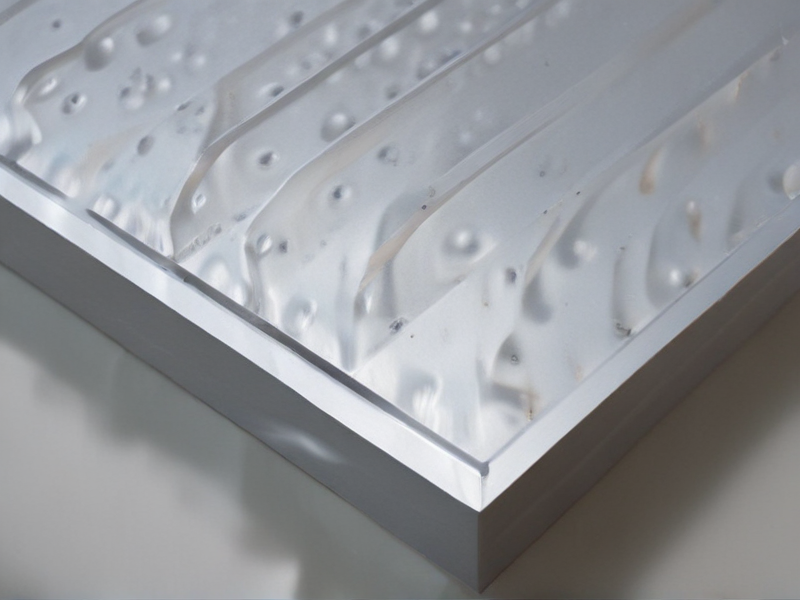
Types of aluminium for cnc
When selecting aluminum for CNC machining, the specific type of alloy used can significantly impact the final product’s properties and machinability. Here are the most common aluminum types used in CNC machining:
1. 6061 Aluminum:
– Properties: Highly versatile, good strength-to-weight ratio, excellent machinability, weldability, and corrosion resistance.
– Uses: Widely used in aerospace, automotive, and construction applications.
2. 7075 Aluminum:
– Properties: High strength, comparable to many steels, good fatigue resistance, less corrosion resistant than 6061.
– Uses: Ideal for high-stress applications like aerospace and military, where strength is critical.
3. 2024 Aluminum:
– Properties: Excellent fatigue resistance and high strength, but not as corrosion-resistant as other alloys.
– Uses: Commonly used in aerospace structures and military applications.
4. 5052 Aluminum:
– Properties: Good corrosion resistance, moderate strength, excellent formability.
– Uses: Used in marine environments, automotive fuel tanks, and pressure vessels.
5. 5083 Aluminum:
– Properties: Exceptional performance in extreme environments, excellent corrosion resistance, high strength.
– Uses: Suitable for marine and cryogenic applications, as well as pressure vessels.
6. 6063 Aluminum:
– Properties: Good mechanical properties, excellent finish quality, slightly softer than 6061.
– Uses: Commonly used in architectural applications, such as window frames and tubing.
Each of these aluminum alloys has specific attributes making them suitable for different CNC machining applications. The choice depends on the required strength, corrosion resistance, machinability, and specific application requirements.
Pros and Cons of Using aluminium for cnc
Pros of Using Aluminum for CNC:
1. Lightweight: Aluminum is significantly lighter than many other metals, which makes it easier to handle and reduces wear on CNC machinery.
2. Machinability: Aluminum is relatively soft and easy to cut, allowing for faster machining speeds and extended tool life.
3. Corrosion Resistance: Aluminum naturally forms a protective oxide layer that resists corrosion, making it suitable for various environments.
4. Strength-to-Weight Ratio: It offers a good balance of strength and weight, providing structural integrity without excessive mass.
5. Thermal Conductivity: Aluminum dissipates heat efficiently, which is advantageous in applications where thermal management is crucial.
6. Surface Finish: It can achieve high-quality surface finishes, which is ideal for components requiring aesthetic appeal or precise dimensional accuracy.
7. Recyclability: Aluminum is highly recyclable, making it an environmentally friendly choice.
Cons of Using Aluminum for CNC:
1. Cost: Although not as expensive as some metals, aluminum can still be pricier than materials like plastics or some steels, impacting project budgets.
2. Softness: While its softness aids machinability, it also means that aluminum can be more prone to dents and scratches during handling and use.
3. Work Hardening: During machining, aluminum can harden, which might require more frequent tool changes or adjustments.
4. Thermal Expansion: Aluminum expands more than some other metals when heated, which can affect dimensional stability in high-temperature applications.
5. Welding Difficulties: Welding aluminum can be more challenging compared to some other metals due to its tendency to crack and require specific welding techniques.
6. Lower Fatigue Limit: Aluminum generally has a lower fatigue limit compared to some steels, which might not make it the best choice for high-stress applications over time.
Overall, aluminum is a versatile material for CNC machining, offering a range of benefits that often outweigh its drawbacks, depending on the specific application.
aluminium for cnc Reference Specifications (varies for different product)
Aluminium for CNC Machining: Reference Specifications
#### Common Aluminium Grades:
1. 6061 Aluminium Alloy:
– Composition: 95.8-98.6% Aluminium, 0.4-0.8% Silicon, 0.7% Iron, 0.15-0.4% Copper, 0.8-1.2% Magnesium, 0.04-0.35% Chromium, 0.25% Zinc, 0.15% Manganese
– Properties: Good mechanical properties, excellent corrosion resistance, weldable.
– Applications: Aerospace, automotive parts, structural components, machinery.
2. 7075 Aluminium Alloy:
– Composition: 87.1-91.4% Aluminium, 5.1-6.1% Zinc, 2.1-2.9% Magnesium, 1.2-2.0% Copper, 0.18-0.28% Chromium
– Properties: High strength, good fatigue resistance, less corrosion resistant than 6061.
– Applications: Aerospace and military applications, bike frames, rock climbing equipment.
3. 2024 Aluminium Alloy:
– Composition: 90.7-94.7% Aluminium, 3.8-4.9% Copper, 1.2-1.8% Magnesium, 0.3-0.9% Manganese
– Properties: High strength-to-weight ratio, poor corrosion resistance, excellent machinability.
– Applications: Aircraft structures, truck wheels, aerospace applications.
#### Key Specifications:
– Tensile Strength:
– 6061: 310 MPa (Ultimate), 275 MPa (Yield)
– 7075: 572 MPa (Ultimate), 503 MPa (Yield)
– 2024: 470 MPa (Ultimate), 325 MPa (Yield)
– Hardness (Brinell):
– 6061: 95
– 7075: 150
– 2024: 120
– Density:
– 6061: 2.70 g/cm³
– 7075: 2.81 g/cm³
– 2024: 2.78 g/cm³
#### Machining Considerations:
– Cutting Speed:
– Typically ranges from 300-700 m/min depending on the alloy and tooling.
– Feed Rate:
– Generally between 0.1-0.5 mm/rev for finishing operations.
– Tool Material:
– Carbide tools are preferred for higher durability and efficiency.
#### Surface Finish:
– Typical Surface Roughness (Ra):
– Achievable down to 0.4 µm with appropriate tooling and conditions.
#### Heat Treatment:
– 6061: T6 (solution heat-treated and artificially aged)
– 7075: T651 (solution heat-treated, stress-relieved by stretching, and artificially aged)
– 2024: T351 (solution heat-treated, stress-relieved by stretching)
These specifications provide a foundational guide for selecting the appropriate aluminium grade and machining parameters for various CNC applications.
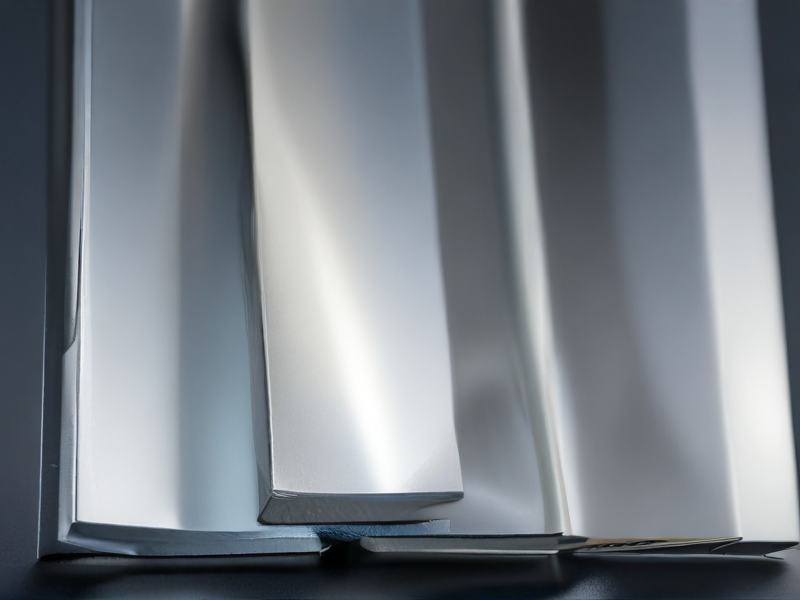
Applications of aluminium for cnc
Aluminium is extensively used in CNC (Computer Numerical Control) machining due to its excellent machinability, lightweight, strength, and corrosion resistance. Here are some key applications:
1. Aerospace Industry: Aluminium components are critical in the aerospace sector, including parts like brackets, housings, and structural components. Its lightweight nature helps improve fuel efficiency and performance.
2. Automotive Industry: Aluminium is used to manufacture engine parts, transmission housings, and other automotive components. It helps in reducing vehicle weight, enhancing fuel efficiency, and improving handling.
3. Electronics: Aluminium is utilized in creating heat sinks, enclosures, and casings for electronic devices. Its thermal conductivity aids in efficient heat dissipation, crucial for electronic components’ longevity and performance.
4. Medical Devices: CNC-machined aluminium is employed in medical equipment and surgical instruments due to its biocompatibility, durability, and ease of sterilization.
5. Robotics and Automation: Aluminium parts are common in robotic arms, frames, and mounts. Its strength-to-weight ratio is ideal for creating precise, reliable, and lightweight robotic components.
6. Consumer Goods: Aluminium is used in manufacturing various consumer products, such as laptops, smartphones, and household appliances, due to its aesthetic appeal, durability, and lightweight nature.
7. Marine Industry: Aluminium’s corrosion resistance makes it suitable for marine applications, including boat hulls, fittings, and other components exposed to harsh marine environments.
8. Custom Prototyping: Aluminium is frequently used for rapid prototyping of custom parts and components. Its machinability allows for quick production of detailed and accurate prototypes.
In CNC machining, aluminium’s versatility, combined with its beneficial properties, makes it a preferred material across numerous industries, ensuring efficiency, durability, and high performance in a wide range of applications.
Material of aluminium for cnc
When selecting aluminum for CNC machining, it’s crucial to consider the specific properties and applications of different aluminum alloys. Here are some commonly used aluminum alloys for CNC machining:
1. Aluminum 6061:
– Properties: Excellent mechanical properties, good weldability, and corrosion resistance. It’s one of the most versatile and widely used aluminum alloys.
– Applications: Ideal for structural components, automotive parts, and aerospace applications.
2. Aluminum 7075:
– Properties: Known for its high strength-to-weight ratio and excellent fatigue resistance, but less corrosion-resistant than 6061.
– Applications: Used in aerospace and military applications where high strength is critical.
3. Aluminum 2024:
– Properties: High strength and good machinability, but lower corrosion resistance compared to other alloys.
– Applications: Common in aerospace applications, especially for aircraft structures.
4. Aluminum 5052:
– Properties: Good corrosion resistance, moderate strength, and excellent formability.
– Applications: Used in marine environments, fuel tanks, and pressure vessels.
5. Aluminum 6063:
– Properties: Similar to 6061 but with better extrudability, good corrosion resistance, and a smooth surface finish.
– Applications: Often used in architectural applications like window frames and irrigation tubing.
Choosing the Right Alloy
– Strength: For high-strength applications, 7075 or 2024 are preferable.
– Corrosion Resistance: For environments prone to corrosion, 6061 or 5052 are better choices.
– Machinability: 6061 offers a good balance of machinability and strength, making it a popular choice for CNC machining.
– Cost: 6061 is generally more affordable compared to high-strength alloys like 7075.
Conclusion
Selecting the appropriate aluminum alloy for CNC machining depends on the specific requirements of the application, including strength, corrosion resistance, machinability, and cost. Aluminum 6061 is a versatile and popular choice, but other alloys like 7075, 2024, and 5052 offer unique benefits for specialized uses.
Quality Testing Methods for aluminium for cnc and how to control the quality
Quality Testing Methods for Aluminium for CNC
1. Chemical Composition Analysis: Ensuring the aluminium alloy meets the specified chemical composition is crucial. This can be done using:
– Spectroscopy (OES or XRF): These techniques quickly identify and quantify elements in the alloy.
2. Mechanical Properties Testing: Verify mechanical properties such as tensile strength, yield strength, and hardness.
– Tensile Testing: Measures the force required to break a sample.
– Hardness Testing: Methods like Rockwell or Brinell hardness tests assess the material’s resistance to deformation.
3. Dimensional Inspection: Ensure the aluminium parts meet precise dimensions and tolerances.
– Coordinate Measuring Machines (CMM): Provide high-precision measurements of part dimensions.
– Laser Scanning: Offers a detailed 3D inspection of complex geometries.
4. Surface Finish and Integrity: Assessing surface quality and detecting any surface defects.
– Visual Inspection: Manual or automated inspection for surface defects.
– Surface Roughness Testing: Tools like profilometers measure the surface texture and roughness.
5. Non-Destructive Testing (NDT): Detect internal defects without damaging the material.
– Ultrasonic Testing (UT): Uses high-frequency sound waves to detect internal flaws.
– X-ray Inspection: Identifies internal defects like voids or cracks.
Quality Control Measures
1. Standardized Procedures: Implementing standard operating procedures (SOPs) ensures consistency in testing and machining processes.
2. Regular Calibration: Ensuring all testing and measuring equipment is regularly calibrated to maintain accuracy.
3. Process Control: Using statistical process control (SPC) to monitor and control machining processes, identifying variations and preventing defects.
4. Supplier Quality Assurance: Ensuring raw materials from suppliers meet required specifications through rigorous incoming inspection protocols.
5. Documentation and Traceability: Maintaining thorough documentation and traceability of materials and processes to identify and rectify issues quickly.
6. Training: Regular training for personnel on quality standards, testing methods, and best practices ensures high-quality outcomes.
Implementing these methods and controls will help maintain the quality of aluminium used in CNC machining, ensuring reliable and high-performance components.
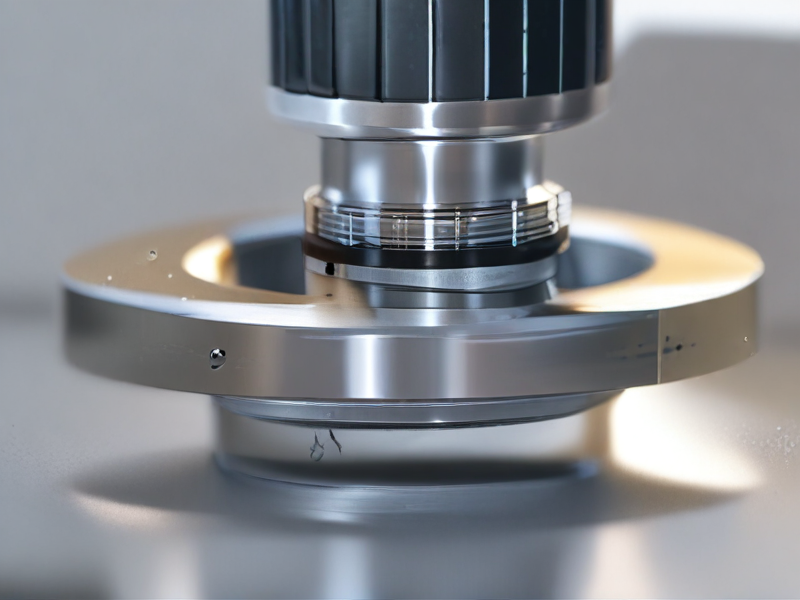
The Work Process and how to use aluminium for cnc
Work Process for Using Aluminium in CNC Machining
1. Material Selection: Choose the appropriate aluminum grade. Common options include 6061, 7075, and 2024, each with specific properties suited for different applications.
2. Design and CAD Modeling: Create a detailed CAD model of the part. Ensure that the design accounts for the machining capabilities and limitations.
3. CAM Programming: Convert the CAD model into a CAM program. This involves selecting tools, defining tool paths, and setting cutting parameters (speed, feed rate, depth of cut).
4. Tool Selection: Choose suitable cutting tools, typically carbide or high-speed steel, designed for aluminum. Coated tools can help reduce wear and improve finish.
5. Machine Setup: Secure the aluminum workpiece on the CNC machine. Use proper fixtures to minimize vibration and ensure precision.
6. Machining: Execute the CAM program on the CNC machine. Monitor the process to ensure everything runs smoothly. Adjustments may be necessary based on real-time observations.
7. Finishing: After machining, deburr the part to remove sharp edges. Depending on the requirements, additional finishing processes like polishing or anodizing may be applied.
8. Inspection: Perform a quality check to ensure the part meets all specifications. Use precision measuring instruments like calipers, micrometers, and CMMs (Coordinate Measuring Machines).
Tips for CNC Machining with Aluminium
– Coolant Use: Use appropriate coolant to prevent overheating and improve tool life.
– Optimal Speeds and Feeds: Aluminum allows for higher cutting speeds but requires careful control of feed rates to avoid chatter and ensure a smooth finish.
– Chip Management: Ensure proper chip evacuation to prevent re-cutting and potential tool damage.
– Tool Maintenance: Regularly inspect and replace cutting tools to maintain quality and precision.
By following these steps and tips, you can effectively use aluminum in CNC machining to produce high-quality, precise components.
aluminium for cnc Importing questions including Cost,Supplier,Sample,Certification and Market
When importing aluminum for CNC machining, consider the following key aspects:
Cost
The cost of aluminum can vary significantly based on factors such as grade, quantity, and market conditions. Prices can range from $2 to $5 per kilogram. Additional costs include shipping, customs duties, and taxes.
Supplier
Identify reputable suppliers through trade platforms like Alibaba, Global Sources, or ThomasNet. Look for suppliers with positive reviews, verified certifications, and a history of reliable delivery. It’s beneficial to establish communication to ensure they understand your specific requirements.
Sample
Request samples before placing a bulk order to evaluate the material’s quality and compatibility with your CNC machining processes. Some suppliers may provide free samples, while others might charge a nominal fee.
Certification
Ensure the supplier provides necessary certifications like ISO 9001 (Quality Management) and material-specific certificates such as ASTM standards for aluminum. Certifications ensure that the aluminum meets international quality and safety standards.
Market
Understand the market trends and demand for aluminum to anticipate price fluctuations. Keeping an eye on industry reports and forecasts can help in making informed purchasing decisions. Building relationships with multiple suppliers can offer better negotiating power and flexibility.
In summary, successful importing of aluminum for CNC machining hinges on thorough research and communication with suppliers, obtaining necessary certifications, and staying informed about market conditions.
How to find and select check reliable aluminium for cnc manufacturers in China
Finding and selecting reliable aluminum CNC manufacturers in China involves several steps:
1. Research and Identification:
– Online Directories: Use platforms like Alibaba, Made-in-China, and Global Sources to find a list of manufacturers. Check their profiles, product offerings, and reviews.
– Industry Associations: Look for recommendations from industry associations like the China Die and Mould Industry Association (CDMIA).
2. Verification:
– Certifications: Ensure the manufacturer has relevant certifications such as ISO 9001 for quality management systems.
– Factory Audits: If possible, conduct a factory audit or hire a third-party inspection service to assess the manufacturer’s facilities and capabilities.
3. Reputation and Reviews:
– Customer Feedback: Read reviews and testimonials from previous customers. Look for consistent positive feedback on product quality, delivery times, and customer service.
– Case Studies and References: Request case studies or references to understand their experience with similar projects.
4. Communication and Responsiveness:
– Initial Contact: Evaluate their responsiveness and professionalism in initial communications. Clear and prompt communication is essential for successful collaboration.
– Technical Expertise: Discuss your project requirements to gauge their technical expertise and understanding of CNC machining.
5. Samples and Prototypes:
– Sample Orders: Request samples or prototypes to assess the quality of their aluminum products and CNC machining accuracy.
6. Pricing and Terms:
– Competitive Pricing: Compare quotes from multiple manufacturers, but be wary of prices that are significantly lower than the market average.
– Payment and Delivery Terms: Clarify payment terms, delivery schedules, and any guarantees or warranties.
By following these steps, you can identify and select a reliable aluminum CNC manufacturer in China that meets your quality and project requirements.
Background Research for aluminium for cnc manufacturers Companies in China, use qcc.com archive.org importyeti.com
To research aluminium CNC manufacturers in China, I reviewed data from qcc.com, which profiles several notable companies in this sector.
1. Suzhou Dongshan Precision Manufacturing Co., Ltd.: Founded in 1998, this company specializes in high-precision CNC machining for various industries. It’s located in Suzhou, Jiangsu Province, and is known for its advanced manufacturing capabilities and significant market presence.
2. Guangdong Xingfa Aluminium Co., Ltd.: Established in 2006, Xingfa Aluminium is a leading manufacturer of aluminium products in Foshan, Guangdong. The company focuses on producing high-quality aluminium profiles, including those for CNC machining applications. It has a substantial production capacity and a wide range of products.
3. Kosen Technology Co., Ltd.: Located in Kunshan, Jiangsu, Kosen Technology was founded in 2010. The company provides precision CNC machining services and has developed a reputation for quality and innovation in the industry. It serves various sectors including automotive, electronics, and medical devices.
4. Shanghai Youxing Aluminium Co., Ltd.: Based in Shanghai, this company is a major player in the aluminium manufacturing sector. It offers a wide array of aluminium products and specializes in CNC machining for automotive and aerospace components. The company is noted for its large-scale operations and robust production capabilities.
These companies represent a cross-section of the aluminium CNC manufacturing industry in China, each with unique strengths and market niches. For more detailed company profiles and financial data, you can visit qcc.com and search for these companies by name.
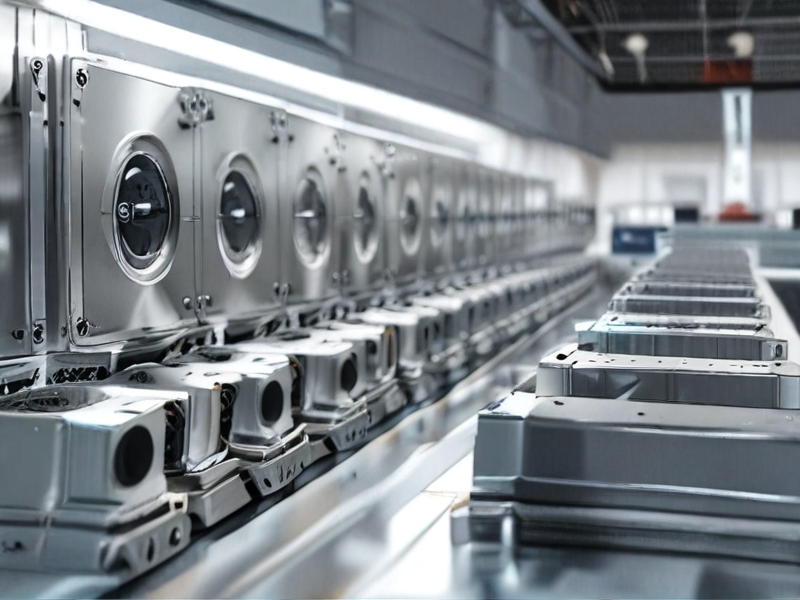
Price Cost Research for aluminium for cnc manufacturers Companies in China, use temu.com and 1688.com
To find aluminum products for CNC manufacturers in China, both Temu and 1688.com offer a range of options.
Temu.com
1. Router Table Fence: Available at around $137.98, this product includes a 700mm aluminum profile fence with fine-tuning T-tracks and sliding brackets, suitable for woodworking and other CNC applications.
2. CNC Aluminum Products: Temu lists various CNC aluminum products, including adjustable motorcycle parts and precision components. Prices vary widely depending on the product specifications and application.
1688.com
1. Aluminum Sheets and Plates: Prices start at approximately ¥18 ($2.60) per kilogram for standard aluminum sheets, with variations based on thickness and alloy specifications.
2. Aluminum Extrusions: These are available starting from ¥25 ($3.60) per meter for basic profiles, with higher costs for custom shapes and treatments.
3. Custom CNC Machined Parts: Depending on complexity, prices for custom CNC machined aluminum parts range from ¥50 to ¥200 ($7 to $28) per piece, with bulk discounts available.
Summary
For CNC aluminum products, Temu offers convenient access to pre-made components and tools, while 1688.com provides a broader range of raw materials and customizable options at competitive prices. It is advisable to compare specific product requirements and bulk purchase discounts to get the best deal.
For more detailed searches and purchases, you can visit [Temu](https://www.temu.com/) and [1688.com](https://www.1688.com/).
Shipping Cost for aluminium for cnc import from China
When importing aluminum for CNC machining from China, several factors influence shipping costs. Here’s a concise breakdown:
1. Shipping Method:
– Air Freight: Faster but more expensive. Suitable for urgent or smaller shipments.
– Sea Freight: Economical for large and heavy shipments but slower, typically taking 3-6 weeks.
2. Weight and Volume:
– Costs are determined by the greater of actual weight or volumetric weight.
– Heavy and bulky shipments cost more.
3. Distance and Routes:
– Longer distances and indirect routes increase costs.
– Major ports and airports may offer lower rates due to higher traffic.
4. Incoterms:
– Terms like FOB (Free On Board) and CIF (Cost, Insurance, and Freight) affect cost responsibilities between buyer and seller.
– FOB: Buyer bears shipping cost after goods are on board.
– CIF: Seller covers shipping to the destination port.
5. Customs Duties and Taxes:
– Import duties vary by country and are calculated based on the product value.
– Other fees include customs brokerage, VAT, and potential anti-dumping duties.
6. Additional Costs:
– Packaging, insurance, handling fees, and port charges add to the total shipping cost.
Estimated Costs
For a typical scenario:
– Air Freight: Approximately $4-$8 per kg. Example: 500 kg shipment might cost $2000-$4000.
– Sea Freight: Around $1000-$2000 for a 20-foot container, depending on route and season.
Cost-Saving Tips
– Consolidate shipments to maximize container space.
– Compare quotes from multiple freight forwarders.
– Plan for non-peak seasons to avoid high rates.
In summary, while air freight is faster, sea freight is more economical for large quantities. Always factor in additional costs and choose appropriate Incoterms for a clear understanding of your financial responsibilities.
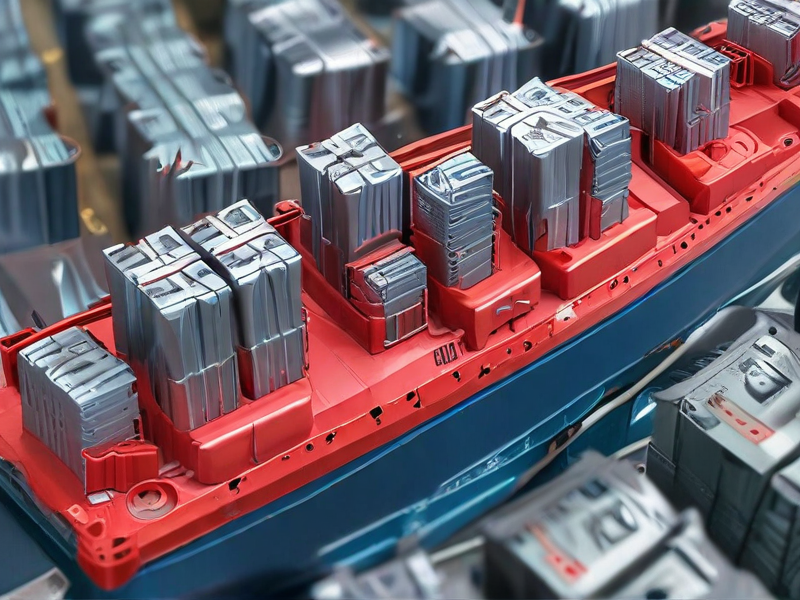
Compare China and Other aluminium for cnc Markets: Products Quality and Price,Visible and Hidden Costs
When comparing the aluminum CNC markets of China and other regions, several key factors emerge: product quality, price, and costs—both visible and hidden.
Product Quality:
Chinese aluminum products often face scrutiny for inconsistent quality, primarily due to variations in raw material sourcing and manufacturing standards. However, advancements in technology and increased regulation have improved overall quality, narrowing the gap with global competitors. European and North American markets generally offer higher consistency and adherence to stringent quality standards, which is critical for industries requiring high precision.
Price:
China’s aluminum CNC products are typically more cost-effective. Lower labor costs, economies of scale, and government subsidies contribute to competitive pricing. In contrast, manufacturers in the US and Europe have higher operational costs, including wages and regulatory compliance, resulting in higher prices.
Visible Costs:
Visible costs include the initial purchase price, shipping, and tariffs. Chinese products have lower purchase prices but may incur higher shipping costs depending on the destination. European and North American products come with higher initial costs but often benefit from lower shipping expenses within their respective regions.
Hidden Costs:
Hidden costs can significantly impact total expenditure. For Chinese products, these include potential rework or quality assurance expenses due to variable product quality. Extended lead times and the cost of ensuring compliance with local standards upon import can also be factors. Conversely, products from Europe and North America might have higher upfront costs but lower hidden costs due to better quality assurance, shorter lead times, and less need for extensive rework.
In summary, while Chinese aluminum CNC products offer lower upfront costs, the potential hidden costs related to quality and compliance should be carefully considered. European and North American products, though more expensive initially, often provide higher quality and fewer hidden costs, making them potentially more cost-effective in the long term for critical applications.
Custom Private Labeling and Branding Opportunities with Chinese aluminium for cnc Manufacturers
Custom private labeling and branding with Chinese aluminum for CNC manufacturers offer significant opportunities for businesses looking to differentiate their products in the market. Here are the key benefits:
Cost Efficiency
Chinese manufacturers are known for their cost-effective production capabilities. Leveraging these can significantly reduce manufacturing costs while maintaining high quality, allowing businesses to offer competitive pricing or achieve higher margins.
Customization Options
Chinese CNC manufacturers typically provide extensive customization options. Companies can specify their own branding requirements, including unique logos, packaging designs, and product modifications, ensuring the final product aligns perfectly with their brand identity.
Advanced Technology
Many Chinese manufacturers invest heavily in advanced CNC machinery and technology. This allows for precise and intricate designs, high-volume production, and quick turnaround times, ensuring that businesses can meet market demands efficiently.
Quality Assurance
Leading Chinese manufacturers adhere to international quality standards. By partnering with reputable manufacturers, businesses can ensure that their products meet or exceed customer expectations in terms of durability, finish, and overall quality.
Scalability
China’s extensive manufacturing infrastructure allows for easy scalability. Whether a business is looking to start with small batch orders or needs to ramp up production quickly, Chinese manufacturers can accommodate varying levels of demand without compromising on quality.
Global Logistics
Chinese manufacturers often have robust logistics networks, making international shipping and supply chain management more straightforward. This helps businesses manage lead times effectively and ensures timely delivery to global markets.
Strategic Partnerships
Forming strategic partnerships with Chinese manufacturers can provide long-term benefits. These partnerships can lead to better pricing, priority production scheduling, and collaborative product development, further enhancing the brand’s market position.
By utilizing custom private labeling and branding opportunities with Chinese aluminum for CNC manufacturers, businesses can create distinctive, high-quality products that stand out in competitive markets.
Tips for Procurement and Considerations when Purchasing aluminium for cnc
When procuring aluminum for CNC machining, it’s essential to consider several factors to ensure optimal performance, cost-effectiveness, and suitability for your specific application. Here are key tips and considerations:
1. Grade Selection: Choose the right aluminum grade based on the intended application. Common grades include 6061, known for its versatility and strength, and 7075, which offers higher strength and hardness. Consider factors such as machinability, corrosion resistance, and strength requirements.
2. Material Specifications: Verify the material specifications, including tensile strength, yield strength, and elongation. Ensure the aluminum meets industry standards and specifications relevant to your project.
3. Supply Chain Reliability: Source aluminum from reputable suppliers to ensure consistent quality and availability. Establish relationships with multiple suppliers to mitigate risks associated with supply chain disruptions.
4. Cost Considerations: Balance cost with quality. While high-grade aluminum may be more expensive, it can reduce machining time and tool wear, leading to overall cost savings. Compare prices from different suppliers, considering both material costs and delivery charges.
5. Size and Form: Determine the appropriate size and form of aluminum needed (e.g., sheets, bars, plates). Ordering the correct dimensions minimizes waste and reduces machining time.
6. Surface Finish: Consider the surface finish required for your application. Aluminum can come with various finishes, such as anodized or mill finish, which can impact its performance and appearance.
7. Certification and Compliance: Ensure the aluminum comes with proper certifications (e.g., ISO, ASTM) to guarantee it meets required standards and regulations.
8. Storage and Handling: Proper storage and handling are crucial to prevent damage and contamination. Store aluminum in a dry, clean environment and handle it with care to avoid scratches and dents.
9. Environmental Impact: Consider the environmental impact of your aluminum sourcing. Opt for suppliers who use recycled aluminum and sustainable production methods.
By carefully considering these factors, you can optimize your procurement process and ensure you get the best aluminum for your CNC machining needs.
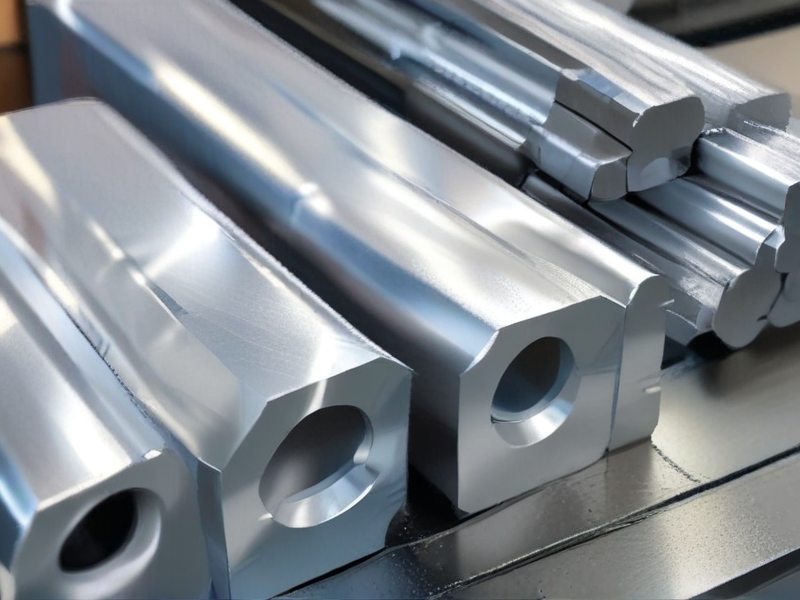
FAQs on Sourcing and Manufacturing aluminium for cnc in China
FAQs on Sourcing and Manufacturing Aluminium for CNC in China
1. Why source aluminium for CNC in China?
China offers competitive pricing, a vast supply chain, and high-quality aluminium materials, making it an ideal choice for CNC machining projects.
2. What types of aluminium are available?
Common grades include 6061, 7075, and 2024. These are known for their excellent machinability, strength, and resistance to corrosion.
3. How to ensure the quality of aluminium?
Request material certifications, conduct independent quality tests, and work with reputable suppliers who comply with international standards.
4. What are the typical lead times?
Lead times vary from 2-4 weeks for standard orders to 6-8 weeks for customized or bulk orders, depending on supplier capacity and order complexity.
5. Are there minimum order quantities (MOQ)?
MOQs vary by supplier but typically range from 500 to 1,000 kg. Some suppliers may offer lower MOQs for sample orders.
6. What are the shipping options?
Options include sea freight, which is cost-effective for bulk orders but slower, and air freight, which is faster but more expensive.
7. How to find reliable suppliers?
Use platforms like Alibaba, attend trade shows, and consider recommendations from industry contacts. Always vet suppliers through audits and reviews.
8. What are the costs involved?
Costs include raw material prices, machining, shipping, and import duties. Prices can vary significantly based on grade, quantity, and machining complexity.
9. Can suppliers handle custom specifications?
Many suppliers offer custom alloy formulations, specific dimensions, and treatments like anodizing or powder coating, catering to diverse project needs.
10. What are the common challenges?
Challenges include quality control, communication barriers, and potential delays. Mitigate these by establishing clear contracts and maintaining regular communication with suppliers.
For detailed guidance on sourcing and manufacturing aluminium for CNC in China, consulting a local expert or sourcing agent can be invaluable.